Within your typical industrial circle, a common refrain holds that “what you can’t measure, you can’t manage.” That aphorism is particularly applicable to the multi-phase flow regime of an active drilling fluid system, where operators, all too often, have had little choice but to make critical decisions based on less-than-precise flow measurements.
Today’s ever-increasing pressures, economic and otherwise, have brought to the forefront the glaring limitations of conventional differential pressure meters, particularly their inability to deliver sustainable and constant measurements during the reiterative transitions between turbulent and laminar flow. So says Dave Bell, chief technology officer of namesake Bell Technologies, LLC, of Houston. He has quietly modified a differential pressure flow measurement device used in the downstream, mid-stream and non-oilfield sectors, which, he believes, addresses the shortcomings.
Owing largely to its geometric configurations, Bell says the so-called TORUSWEDGE has longer service life, with significantly less pressure drop than the ubiquitous orifice plates. Unlike the now-standard Coriolis meter, it delivers consistent measurements in the multi-phase flow, intrinsic of muds. With no moving parts, and rated for pressures from vacuum to 15,000 psi, Bell says the circumferential differential pressure flow element, with calibration, is within 0.5% accuracy.
“Someone once said that an orifice plate is designed to die and go away the minute flow starts,” Bell said. “The sharp edge of an orifice plate erodes during flow, and when that happens the differential [pressure flow] starts to disappear. You get a lot of throughout volume, but have no idea how much volume you’re actually getting.”
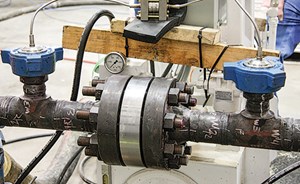
As for the commonly used Coriolis meter, Bell says that along with high sourcing and installation costs, the device is unable to deliver continuous and precise measurements in the often-abrasive and ever-changing flow regimes of the mud stream—a liability that, he said, was demonstrated in a November 2015 comparative flow test.
Technology transfer. The original iteration of the differential pressure flow measurement device was patented in 2008 and, until recently, was used primarily to measure gas and fluids in the chemical processing, refining and pipeline industries. One of the units is even in operation at the primary gas meter station of the Kremlin in Moscow. “We basically were in everything but the drilling market,” said Bell, whose small company bills itself as “a global leader in process measurement.”
He said the durability of the device, and its applicability to severe service applications, was borne out with a year-and-a-half run in a coal-fired power plant, where it was used to measure the limestone slurry, which was pumped to absorbers to help clean the coal as it was being burned. “We put the device in a 4-in. flowline for pulverized limestone, and found it did not wear at all,” Bell said.
It was a natural evolution to the drilling fluids side, where the first step was evaluating the then-primary measurement devices. “We took work-ups of the Venturi [tube], orifice plate, a standard wedge meter and a flow nozzle,” he said. “We like to say we took the best features of these technologies, put them in a bag, shook them up, and the TORUSWEDGE is what came out.”
The next step was to independently compare the device with a Coriolis meter in a simulated, multi-phase mud flow regime.
11,000 data points. The head-to-head, multi-phase flow analysis was conducted on a water-based mud at the Compatible Components Corp. flow lab in Houston. To ensure an unbiased test, Bell said, independent process instruments and industry standards personnel conducted both the set-up and execution of the test, in which a TORUSWEDGE and a vibrating multi-tube Coriolis meter were comparatively evaluated in identical flow regimes. The test protocol began with pure water, to establish a homogeneous flow baseline, and went on to simulate real-world mud flow, with subsequent injections of xanthan gum to increase viscosity and barite to elevate density. As of this writing, a similar test was underway in oil-based mud.
Bell said data were electronically collected every second during the 4-hr flow test, resulting in the gathering of nearly 11,000 data points, which, in December 2015, were grafted into 18 operating windows. The results, he said, documented that the TORUSWEDGE analog signals remained consistent throughout the multi-phase flow regime, including the transitional periods when air, water and solids particulates were introduced. Bell said the Coriolis meter “went blind” and was unable to deliver volume flow output during multi-phase flow, which amounted to an estimated 25% of the 4-hr test.
These intermittent nap times, he says, can lead to decisions being made, based on assumptions. “It is not a continuation of signals, but rather what we classify as a mathematical calculation of inferred data. By continually measuring, even during multi-phasing, we’re giving you information you can use to control your well.”
Consistent differential pressure flow measurements, he said, could also aid in early kick detection, raising opportunities in applications, such as managed pressure drilling. “You’d be able to sense a movement of flow on the outlet of a pressure-balanced well,” he said.
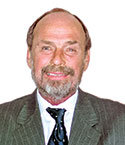
- Coiled tubing drilling’s role in the energy transition (March 2024)
- Digital tool kit enhances real-time decision-making to improve drilling efficiency and performance (February 2024)
- E&P outside the U.S. maintains a disciplined pace (February 2024)
- U.S. operators reduce activity as crude prices plunge (February 2024)
- Drilling advances (January 2024)
- Driving MPD adoption with performance-enhancing technologies (January 2024)
- Applying ultra-deep LWD resistivity technology successfully in a SAGD operation (May 2019)
- Adoption of wireless intelligent completions advances (May 2019)
- Majors double down as takeaway crunch eases (April 2019)
- What’s new in well logging and formation evaluation (April 2019)
- Qualification of a 20,000-psi subsea BOP: A collaborative approach (February 2019)
- ConocoPhillips’ Greg Leveille sees rapid trajectory of technical advancement continuing (February 2019)