Coiled Tubing Technology
Tapered coiled tubing reaches extreme depths
New coiled tubing string development and pipe handling equipment increased operating well depth ranges by 55%.
Hampton Fowler and Perry Courville, Halliburton
A developing coiled tubing service incorporates tapered outside diameter (OD) tubing that enables coiled-tubing (CT) intervention at depths that were previously unachievable.
The system is capable of operating 55% deeper than conventional CT equipment. This ultra-deep capability was initially developed to provide deepwater intervention through as much as 9,000 ft of ocean riser pipe to total well depth of 36,000 ft. The added reach is made possible by joining sections of varying outside diameters, using specially designed transition segments, Fig. 1. The resulting string features a smaller OD on the bottom and progressively larger OD and wall thickness near the surface, optimizing the workstring’s weight and service rating.
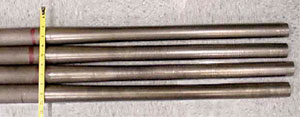 |
Fig. 1. Tapered transition section mates coiled tubing of different diameters.
|
|
The transition connector that furnishes the taper between CT sections of different diameter has a complex, geometrical profile designed to enable maximum CT contact with the injector’s gripper section. Special V-shaped gripper blocks and flexible inner beams help maintain consistent gripper contact with the transition connector as it passes through the injector to provide uniform and controlled loading on the CT. A customized hydraulic circuit accommodates both large- and small-OD tubing and maintains a constant gripping force on the tubing as it passes through the injector.
A special added safety feature of the overall CT system is the hydraulic circuit’s capability to default to a fail-safe condition. In the event of failure in the primary hydraulic pressure supply, an automated safety system stops the injector, sets the brakes and increases gripping force to a pre-selected value – without operator intervention – to enhance safety for personnel, the well and equipment.
Technology development. Use of continuous lengths of coiled steel tubing has been an intervention option for oil and gas operators since 1962. Ranging to 25,000 ft in length and outer diameter (OD) sizes from 1.00 in. to 2.875 in., these continuous pipe strings are uncoiled into live wells to perform milling, drilling, logging, perforating, fracturing and completion operations; or maintenance tasks such as cleaning and chemicals placement.
In the years since its first use, coiled tubing technical advancements include use of newer materials and larger pipe sizes with increased minimum yield-strength steel, improved manufacturing processes, variable wall thickness tubing, and increased knowledge of pipe behavior in the well and how fatigue and pipe failures occur.
Fig. 2 shows the evolution of industry efforts to achieve more reach with CT by varying wall thickness. Current CT technology, featuring tubing sections of different OD and ID mated together by tapered sections, enables use of CT at depths 55% greater than is possible with conventional CT. This method of extending CT reach provides larger ID, which results in less pumping friction pressure and greater flowrates. The stronger, thick-walled section at the surface supports the greater suspended tubing weight associated with extreme-depth CT interventions.
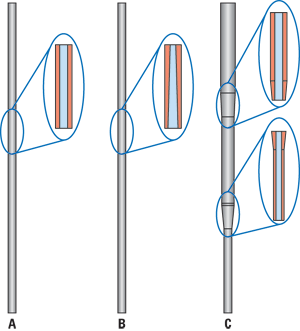 |
Fig. 2. Development of tapered-OD coiled tubing. A is conventional CT. B is CT with uniform OD and tapered ID; this method extended CT range to 25,000 ft. C is tapered-OD CT, which extended CT reach to 36,000 ft vertical depth.
|
|
For shallower applications, the relatively lighter weight of tapered CT offers advantages in velocity string or production string applications, and helps optimize pumping operations conducted through CT. These applications may involve facilities with limited crane capacities and deck load restrictions, making the lighter weight an important factor.
Tapered CT was developed to enable CT intervention to extreme depths, through very deep water. However, the service can be used with land-based operations where extended reach and improved flow characteristics within the CT string are needed. Tapered CT can be used for essentially all applications where CT is applicable.
Other key technologies. To accommodate the diameter variation, modifications to the injector head were necessary, Fig. 3. The modified injector head hydraulic system maintains a constant pressure on the injector gripper beam loading cylinders during all phases of passing the transition joint through the injector. Flexible inner beams in the injector incorporate elastomeric elements to enhance even gripping force distribution.
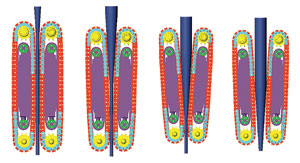 |
Fig. 3. Special injector modifications help prevent crushing or slippage of tubing in transition from one OD to another.
|
|
Maintaining constant pressure on the transition joint is crucial when moving the joint in either direction. During a transition from larger to smaller OD (pulling out of the hole), cylinder pressure could potentially drop due to the fluid volume increase as the injector beams (gripping system) close further on the smaller OD tubing. If the pressure drops too much, then tubing slippage will occur when tension load exceeds the friction force imposed by the injector gripper chains.
Alternatively, during a transition from smaller to larger OD (running into the hole), a pressure increase with fluid volume decrease could result in the transition joint or larger OD tubing being crushed. The hydraulic circuit modifications to the injector head help prevent these occurrences at the maximum recommended tripping speed when passing the transition joint.
Fig. 4 shows a transition (or connecting) joint passing through the injector during testing. The white-appearing covering on the CT is tactile pressure-indicating film, placed on the transition joint to help design engineers arrive at the connecting joint’s optimum shape. The connector profile is the product of extensive design and testing. The resulting shape is not simply a linear taper; rather, it is a complex, geometrical form developed to maintain optimum contact between pipe and the injector gripper surfaces to help ensure gripping capability throughout the insertion/ retrieval process.
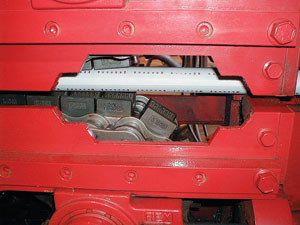 |
Fig. 4. Tapered CT transition section going through injector pull-off test at 60,000 lb. White-appearing coating on CT is tactile pressure-indicating film used to guide design engineers developing tapered section shape.
|
|
The pressure-control stack for the tapered CT must meet a variety of design standards to seal at pressures up to 15,000 psi on all sections of the tubing. Meeting these standards involved clearing several technical hurdles during development. Most CT pressure-control stacks are built to accommodate a single specific CT size. For tapered CT service, the stack required variable bore components that not only function over the range of straight OD tubing within the string, but also over the tapered transition joint. The pressure control stack that was developed for service includes: 1) variable OD pipe rams; 2) variable OD slip rams; and 3) variable OD stripper.
Testing. Tapered CT service equipment and procedures have been tested extensively under lab, full-scale test well and field conditions, as noted below. The development of different diameters and use of base-metal yields are also to be tested to a similar degree. Test areas and conditions included:
- Laboratory: Established testing requirements for transition-connector sections
- Laboratory: Well control aspects lab-tested were gripper packs, slips and rams
- Full-scale test well: Transition connectors were tested for tubing fatigue-life and joint fatigue-life characteristics.
- Field testing at 12,000 ft in a temporarily abandoned well served as a proof of concept. Field trials focused on the fatigue analysis of the transition joint between 2 in. OD and 1.75 in. OD sections of the CT string, and performance of the joint as it spooled on the reel and passed through injector chains and stripper packer. (The slip and tubing inserts were designed and built to handle both 2-in. OD and 1.75-in. OD sections of coiled tubing.)
Other tests conducted during the trials included:
- Fatigue analysis model validation
- Testing of the stripper element to view the effect of multiple OD sections
- Slip tests on both 2-in. OD and 1.75-in. OD sections of CT
- Reverse circulation, and
- Step-up flowrate test to validate flow characteristics through the CT.
After testing was completed, an examination of all materials and equipment involved showed suitability for introduction into commercial applications, which are expected to begin in the first quarter of 2005. 
BIBLIOGRAPHY
M. Kalman, B. Dorman, R. Rosine, R. Stephens, M. Chambans, J. Martin, D. McWhorter, “Tapered OD coiled tubing system,” Paper SPE 89335, SPE/ ICoTA Coiled Tubing Conference and Exhibition, Houston, Texas, March 23 – 24, 2004.
THE AUTHORS
|
 |
Hampton Fowler, global operations manager for Well Intervention Services for Halliburton, is based in Houston. His responsibility extends to hydraulic workover as well as CT operations. He received a BS degree in engineering in 1981 from Texas A&M University and joined Halliburton as a field engineer for Otis in New Iberia, Louisiana. He has held various operational, technical and managerial roles in the US and North Sea area related to the company’s coiled tubing product service line. Mr. Fowler holds several foreign and US patents and has published numerous technical papers and magazine articles related to CT operations.
|
 |
Perry Courville, Halliburton’s product manager for coiled tubing and hydraulic workover products, based in Houston, holds a BS degree in mechanical engineering from McNeese State University, and has been employed by Halliburton for 25 years. His work during that time has been exclusively in well intervention, where he has held engineering, operations and business development positions. Mr. Courville has authored or co-authored more than 25 technical papers and journal articles.
|
|
|
|