Technology developments in wellhead systems bring greater efficiency and safety to drilling applications
Much has been written about the shale boom that began more than a decade ago in the U.S. A combination of favorable oil prices, technological innovations and a growing global demand for energy helped the E&P industry turn shale into an economically favorable source of vast volumes of oil and gas production.
The traditional drilling techniques since the early 19th century—such as drilling vertical wells into conventional oil-rich reservoirs across the U.S.—often left large volumes of recoverable oil and gas in the formation, due to limited connectivity. Additionally, the depletion of these conventional reservoirs over the decades raised the industry demand for greater technology innovations—a demand that was met with the development of horizontal drilling technology, hydraulic fracturing completions and multi-well pad drilling for unconventional reservoirs. As they explored and tested these advancements in their shale wells, operators began to push their well construction operations to new limits. The drilling of longer laterals became the norm, bringing with it vastly improved recovery rates and the ability to drill and produce a single zone more effectively.
At the same time, the industry faced greater well control requirements and operators’ needs to manage and reduce time and total well costs, while simultaneously cutting worker safety risks. This call was answered through the development of an industry-leading wellhead system that takes full advantage of the efficiency gains in drilling rig technology and shale drilling methods in recent years. Combining seven field-proven and proprietary technologies, the Baker Hughes Riser Speed Head (RSH) wellhead system offers many options to deliver maximum efficiency, safety and well control for almost any well design and requirement in shale plays today, Fig 1.
This article begins with an historical review of the industry’s well control technologies and techniques during drilling. It then reviews one of the field applications of the RSH wellhead system and the safety, cost and time savings that the operator achieved.
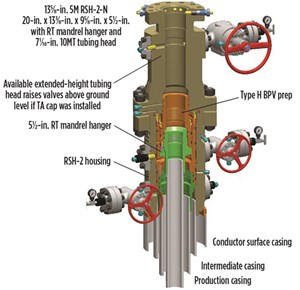
History has shown that drilling for oil and gas can be a hazardous operation. The blowout preventer (BOP) is the industry’s standard equipment for well control during drilling. BOPs are critical for safe drilling operations, and they are connected to wellhead equipment as casing is installed.
For many decades, traditional wellhead systems followed proven, conventional set-ups. Wells with surface and production casing traditionally used a conventional SOW casing head, followed by a tubing head sealed over the production casing.
On deeper wells with intermediate casing, a typical system consisted of a conventional slip-on-weld (SOW) casing head, an additional casing spool sealed over the intermediate casing, and a tubing head sealed over the production casing. Early industry development of stacked, two-piece multi-bowl wellhead systems was aimed at these deeper wells, to save rig time and keep the BOP in place by running intermediate strings with mandrel casing hangers and pack-offs through the BOP. This allowed the BOP to remain in place, instead of being removed, while setting slips, cutting casing and installing a casing spool before the BOP was nippled up again.
Demand for efficiency drives improvements. More recently, operators requested greater efficiency in BOP operations. This drove the market to find ways to reduce the time to connect the BOP with wellhead equipment. Baker Hughes engineers designed the RSH system family to include both single-bowl and, for wells with intermediate casing strings, multi-bowl units. This feature eliminates a BOP nippling down and nippling up connection for further time-savings and better well control for the operator.
In addition, the market demand for further efficiencies has led some operators to use riser systems during drilling operations. The RSH wellhead system family of tools includes riser connectors that are quickly installed and removed from the conductor without welding. The system housing’s threaded flange lets the housing be installed with a running tool through the riser, which allows for the cementing of surface casing with the housing running tool. Once the riser operations are complete, the housing tool is removed, and the API flange is threaded onto the housing. An optional USC-1 Speed Clamp Connector drilling adapter also may be used.
For decades, traditional wellhead equipment would require welding the wellhead to the surface casing. Historical incidents, many of which came with a high price to operators, were the result of poor-quality welding jobs. In addition, the welding of the housing is a time-consuming and hazardous operation, as it requires flammable equipment near the well. In an effort to improve productivity and drive safer operations, operators have required wellhead equipment that can eliminate hot work and increase the speed of operations. RSH wellhead systems answered this call through a propriety design that eliminates field welding and wait-on-cement time. The system’s single- or multi-bowl housing functions as a casing hanger, essentially eliminating the wait-on-cement time and removing the hazardous operations that come with welding near an active well.
Maintaining well control with pressure-containing equipment during drilling operations has seen a tremendous shift in safety and efficiency over the decades. Twenty plus years ago, flanged connections were simply made up with hammer wrenches, without fully knowing the torque applied to the connection and relying only on pressure tests as a sign of proper makeup. This rudimentary operation evolved into the use of hydraulic torque wrenches that provided the torque value and ensured overall safer operations. Though safer, the use of hydraulic torque wrenches for flanged connections can be a time-consuming process.
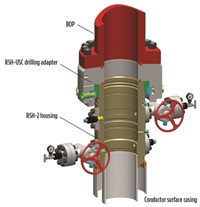
Quick connectors. Now, quick connectors are replacing traditional flanged connections in the more recent industry trend to bring cost-effectiveness for operators. To meet this market demand, Baker Hughes has engineered a proprietary quick connector, called the USC-1 drilling adapter, as part of the RSH wellhead system family. This adapter provides time-saving features and options for operators, which can be especially valuable during batch drilling as intermediate casing is set across wells. The USC-1 quick connect allows operational efficiency with the make and break of the BOP. It reduces BOP nipple-up time by up to 75%, with fewer workers in the well cellar. This feature is twice as valuable when intermediate strings are batch-set across a pad, Fig 2.
Once drilling operations are complete, the RSH system’s housing converts to completions mode, with a standard API flanged top connection for frac and production operations.
As multi-well pad drilling grew to become the industry standard in the past decade, the number of wells per pad evolved from one well per pad to multiple wells per pad. Multi-well pad drilling has improved efficiency drastically and reduced the cost of drilling operations. Consequently, operators moved to batch-setting certain casing strings to further increase efficiency and time-savings in their drilling curves.
This gave rise to walking drilling rigs and further requirements on wellhead systems overall. Operators requested more compact wellhead housings to minimize cellar depth and low-profile temporary abandonment caps, as walking rigs needed to walk from well to well during multi-well pad drilling. The RSH system’s family of tools includes temporary abandonment caps that provide high-pressure intervention access at the minimum possible height. In addition, the RSH wellhead housings include low-profile designs that can meet the market demand for multi-well pad drilling operations.
Stringent well control requirements for wellhead systems were once exclusive to super-majors, but they are being adopted by a growing cross-section of U.S. operators. For decades, slip-and-seal hangers were widely used to set production casing. This simple technology is economical and functional, but it has inherent well control risks, safety issues and non-productive time associated with cutting off casing, with the BOP removed and the annular seal not yet tested. All-purpose RSH systems offer operators the choice of fluted mandrel casing hangers and separate pack-off assemblies, to allow testing annular seals around production casing before BOP nipple-down and setting a back-pressure valve (BPV) when maximum two-barrier well control is required.
Top drive requirements. The industry’s push to longer laterals and more fractured zones per well led to the advent of rigs with top drive technology. Top drives that could push and rotate a drill bit farther out in a horizontal wellbore essentially became a standard for drilling rigs working in shale developments. Horizontal lateral sections of wells became so long that production casing strings would become stuck while making up new connections, and they had to be rotated to sufficiently reduce friction in the lateral, such that the casing could be run all the way out to the toe of the wellbore.
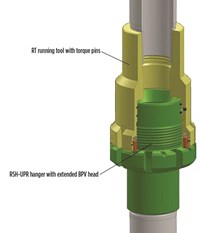
The RSH wellhead system incorporates a patented, right-hand torque (RT) mandrel casing hanger that allows high-torque rotation of production casing strings for running in today’s extended lateral wellbores, including string rotation during cementing, Fig 3. Casing Running Tools (CRTs) also have added time efficiency to operators, as the casing handling system makes for faster makeup of the casing.
In addition, the RSH system’s family of installation tools includes running tools that allow quick, safe and torqueable casing running for intermediate and production casing strings. These tools interface with CRTs for production casing strings. RT torqueable hangers can be provided for intermediate casing strings upon request.
Speed, economics and safety are the key drivers for operators. The case study below demonstrates the time savings per well, increased safety operations, and net drilling cost reductions that the wellhead system can bring.
MEETING NEW WELL CONTROL DEMANDS
Challenge. An operator in the Delaware basin (Permian basin) of West Texas was using Baker Hughes’ 135/8-in. 5M one-piece Land Speedhead (LSH) multi-bowl system—a more economical one-piece alternative to first-generation, two-piece multi-bowl systems with lockdown screws. The operator’s casing program for its wells was as follows: 20-in. conductor, 133/8-in. surface casing, 95/8-in. intermediate casing and 51/2-in. production casing.
The LSH system offered reduced installation time and increased safety, compared to conventional stack-up wellheads. The primary time and safety advantages of the LSH system were based on its ability to set the intermediate casing and drill to total depth (TD) without removing the BOP.
However, a new internal well control requirement—pressure-testing of annular seals on the production casing before removing the BOP—forced the operator to consider an alternative to the LSH system. The operator investigated other wellhead systems and technologies that could meet the new requirement. Such a system also would have to reduce total well costs by slashing wellhead installation time during drilling and simultaneously cutting worker safety risks.
Solution. Baker Hughes’ one-piece RSH-2-N multi-bowl wellhead system offered the design features and capabilities needed to achieve the operator’s time and cost reduction goals while meeting the new well control requirements.
By comparing the rig times for the wellhead-related tasks associated with the installation of the previous LSH system (Table 1) to time estimates associated with RSH system installation (Table 2), the decision to implement the RSH-2-N system was clear.
Results. The RSH-2-N wellhead system was designed to have features that would reduce the installation time for each job. A 10-well pilot program was planned and executed to evaluate system performance. To determine total savings, the operator recorded and compared the actual installation times for the RSH-2-N system to the installation times of the previous LSH system (Table 2).
Total time savings per well ranged from 9.5 to 13.25 hr, an 84% reduction in wellhead installation time. It also resulted in an approximately $220,000 net drilling cost reduction over the 10-well program, Fig. 4.
Future plans include batch-setting the 95/8-in. intermediate casing, as well as adopting the RSH-USC-1 drilling adapter. Once implemented, these actions are anticipated to save an additional 2.5 to 3.5 hr per well.
BUILDING ON PROVEN PERFORMANCE
The case study presented here is the latest example of how the RSH wellhead system is delivering value to shale operators across the U.S. Since its introduction in 2016, more than 5,000 RSH systems have been installed and implemented during shale well drilling in the U.S. This growing level of acceptance and adoption is a strong testament to the safety, reliability and cost effectiveness of the RSH system.
The successes realized in the U.S. are gaining the attention of operators in other parts of the world. The RSH system is now being made available to international markets, where operators are looking for similar safe, cost-effective and efficient well control solutions for their challenging well drilling operations.


- Evolving technology strategy enhances drilling efficiency across the Permian basin (July 2025)
- Drilling advances: Is hot coffee the secret to geothermal energy? (July 2025)
- Smarter well interventions accelerate productivity (July 2025)
- Breaking the status quo in the Permian (July 2025)
- From guesswork to ground truth: The rise of geomechanics in the Permian basin (July 2025)
- Modernizing rod-lift automation for deviated wells (June 2025)
- Subsea technology- Corrosion monitoring: From failure to success (February 2024)
- Applying ultra-deep LWD resistivity technology successfully in a SAGD operation (May 2019)
- Adoption of wireless intelligent completions advances (May 2019)
- Majors double down as takeaway crunch eases (April 2019)
- What’s new in well logging and formation evaluation (April 2019)
- Qualification of a 20,000-psi subsea BOP: A collaborative approach (February 2019)