Operators and service firms collaborate through ground-breaking subsea technology
Collaboration is the driving force of the global oil and gas industry, as it faces mounting pressure to increase efficiencies, maximize production and streamline processes, both offshore and onshore. In turn, these moves hopefully will reduce costs and boost profits.
However, a fresh mindset is essential, if the industry is to overcome some of the challenges that it faces. Accordingly, a recent shift in culture, which is centered on a more open-minded approach toward technological advances and innovations, is gaining noticeable traction. This is particularly true in the subsea sector.
This tangible change in attitudes is the key to unlocking efficiencies throughout the entire global supply chain, as we work to maximize the remaining value from what is—certainly in terms of the UK Continental Shelf (UKCS)—an aging basin. According to a recent report by Oil & Gas UK, the Oil and Gas Technology Centre (OGTC)—which co-invested £37 million in a variety of projects—already has played a part in 72 technology solutions, demonstrating the sector’s desire to embrace innovation and prolong the life of the UKCS.
The report stated that the UK oil and gas services sector has faced some of its toughest times in recent years, as revenues fell by more than £10 billion from 2014 to 2016. However, the study also highlighted that EBITDA (Earnings Before Interest, Taxation, Depreciation and Amortization) fell by £1.7 billion, on average, over the same period. In this sense, innovations in digital transformation and technology, among other activities, have been vital in helping supply chain companies sustain their businesses in what has been a more demanding climate.
GLOBAL TECHNOLOGY
The investment in, and subsequent progression of, innovative technologies, particularly within the subsea sector, is critical to sustaining production into the next decade.
We already know that technical advances have been a driving force behind the increase in total production and improved well placement in recent years, providing solutions to complex offshore challenges, which often require cutting-edge techniques. Many companies also have been prioritizing methods of maximizing ROI from existing wells and infrastructure, which could include well interventions and workovers, according to Oil & Gas UK.
The industry’s attention also will soon turn to developing and pinpointing solutions to extract oil and gas from high-pressure regions, which are moving higher up boardroom agendas, as the oil price increases. The biggest start-up next year is expected to be the Culzean HPHT gas field in the central North Sea.
This also has a global focus, as some of the world’s most challenging deepwater basins exist in international waters. Examples include the Gulf of Mexico’s ultra-deepwater Paleogene, Egypt’s West Nile Delta, and offshore Azerbaijan, where reservoir pressures and temperatures exceed the industry’s current technical capacity.
In 2012, BP announced the launch of “Project 20K,” an R&D program designed to create bespoke technologies that are able to drill, complete, produce and intervene in deepwater reservoirs that have pressures of 20,000 psi at the mud line. However, investment in deepwater technology has taken a back seat in recent years, as a result of the industry downturn.
Nonetheless, as the oil price strengthens, and with high pressure at the seabed in these locations, a critical item becomes subsea connectors that can operate safely and reliably at these elevated pressures. They are necessary—particularly at extreme depths—to maintain the highest productivity levels.
Subsea Technologies Ltd. (STL) is designing and developing products that challenge the norm, customizing connectors specifically for deepwater developments, where the demand is expected to become more evident, as the market improves.
As the oil price reaches a viable level, operators are exploring deepwater areas further, with specific areas of interest in the Gulf of Mexico. The key is to complement and enhance a range of innovations to fit customers’ requirements. Instead of selling solely from a “shopping list,” the company tailors its approach to offering products that are entirely client-led, and which can configure seamlessly into existing offshore systems.
In this respect, the company is seeing a growing demand to develop technology for highly complex and critical applications, which has put pressure on the sector. Nevertheless, STL has succeeded in launching a number of industry firsts with quantifiable benefits. The introduction of the Xtreme Release (XR) Connector and the multi-functional Stackable Lightweight Intervention Connector (SLIC) are just two examples.
COMING OF AGE
As one of the world’s first purpose-built, well intervention technologies, the XR Connector has paved the way for further subsea technical advancements. Providing a safety-critical solution to the ingrained industry issue of maximum riser disconnect angle, it gives operators the confidence to disconnect a riser in an emergency, while offering improvements in efficiency, productivity and costs.
The connector’s face-to-face technology differs fundamentally from all other subsea connectors, which offer a conventional male-into-female arrangement. In an emergency scenario, it allows operators to stay connected to a subsea well for longer periods of time in adverse weather, and it minimizes pre-emptive disconnects when bad weather strikes.
It also reduces the risk of damage to subsea infrastructure, if the vessel has a position-keeping failure, while lowering the risk of damage to a vessel, failure of the riser pipe, and damage to the wellhead and/or loss of well containment. Accordingly, the connector guards against environmental, as well as reputational damage.
The high-angle connector enables vessels to continue operating, while protecting personnel, assets and the environment, and defending against the consequences of dynamic positioning failure. It essentially solves the challenge of safely and reliably disconnecting a riser under a high-bending moment and without damage—which can occur in any water depth, as a result of a vessel drift or drive-off.
The connector was designed and developed about a decade ago, and is believed to be the only connector that is able to disconnect a riser at 100% of its rated bending capacity. Its success has led to further variations in the connector family.
FORWARD-THINKING APPROACH
The XR Connector was introduced to offshore operations following the first coiled tubing intervention using a rigid riser, which was deployed for an oil major in the North Sea. This was carried out from a mono-hull vessel and, although the downhole objectives of the project were achieved, an entirely bespoke system was ultimately required for this to become a regular operation.
Following this realization, the support of STL was enlisted to deliver a purpose-built, coiled tubing riser system to overcome many of the challenges previously identified. As part of this, the company completed a Front-End Engineering Design (FEED) study to develop a detailed conceptual design.
During the global analysis work on the riser, it was discovered that, to get the system operating safely in North Sea water depths, no existing connector would be able to ensure the release of the riser from the subsea christmas tree with absolute assurance that it would not get stuck. Thus, the XR Connector was the answer.
STL proposed the technology and ultimately secured its first launch customer. The first XR Connector (a 10-ksi, 73/8-in. bore version) was delivered in 2009, following extensive qualification testing. The launch customer had designed their intervention system to operate as a hybrid riser/riserless configuration, which meant that, in the riserless configuration, the XR Connector remained in the stack, but its functionality was not required.
Although the client successfully completed its first riserless intervention in 2009, it was months before the company deployed the coiled tubing riser system on a test well, to prove the operation of the system. This was the first time that the connector was disconnected subsea. Initially, it was just with vertical tension on the riser. It subsequently included a bending load, by intentionally moving the vessel off center from the test well, restricted to approximately 5° from the vertical.
Since completing offshore trials on the test well, the customer has successfully completed a number of riser well intervention operations, with more contracted for the coming years. STL also built an XR Connector for a Houston-based operator, which has the potential to be deployed in the coming months.
In a further example, the 10-ksi, 73/8-in. version of the XR Connector was licensed in 2011 to a multi-national client, which standardized on this item in its completion/workover riser (CWOR) systems. At the request of the customer, the XR Connector was re-engineered to optimize the design and manufacture of the product and meet its precise requirements, building a prototype of the modified connector for re-qualification.
DEEPWATER/SUBSEA SOLUTIONS
Along with the XR Connector, STL’s engineers have designed a number of other products that cope with the demanding requirements of both constant operation in harsh conditions and maximum operational uptime, allowing for minimum maintenance downtime.
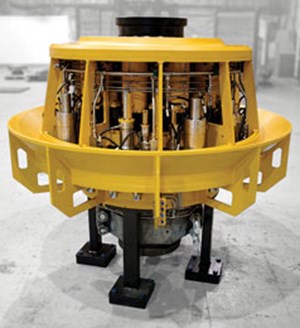
The XR Connector’s unique design ensures that no damage is done, even after repeated release, offering the ability to rapidly disconnect from the wellhead in an emergency situation, Fig. 1. It also allows the vessel’s crew enough time to respond to challenging scenarios, without the risk of getting stuck to the wellhead or damaging the connector or riser, if the crew does not react quickly enough. This is a risk presented by all other connectors on the market.
Without the benefits of this technology (Fig. 2), the resulting damage could cause a significant financial burden, as well as a reputational crisis for the operator—particularly if the damage results in a spill or a well control incident. Nearly a decade after the connector’s launch, the company has responded to the more recent industry demands for high-performance products at lower price points by reworking the XR Connector design to achieve a new derivative—the HB Connector.
By incorporating the key benefits of the XR Connector, the company is now developing the HB Connector, which was designed following a customer request for a lower-cost version of the XR for use in deepwater applications. It will have almost all of the benefits offered by the XR, except that it is not recommended for use in water depths less than 300 m and will cost between 50% and 65% of the price of the XR, depending on the configuration selected by the client. STL already has secured a launch client, with a firm order for two HB Connectors to be qualified, manufactured and delivered before the end of 2018.
Just like the XR Connector, the HB Connector allows the vessel’s crew enough time to respond to challenging scenarios, without the risk of getting stuck to the wellhead, ultimately improving productivity levels.
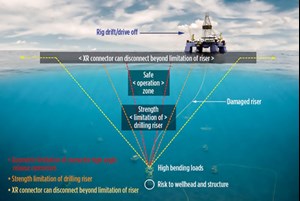
The SLIC technology (Stackable Lightweight Intervention Connector) is a further product that makes up STL’s portfolio, and it features “plug-and-play” configurability.
The SLIC is a latch-style connector for Riserless Subsea Well Intervention (RLWI), Fig. 3. It improves safety, offers increased reliability, ease of maintenance and redundancy. Its design takes into account the complexities of the entire physical, operational and contractual environment in which it operates, which minimizes downtime, not only for the operator but the end user, and subsequently benefiting the entire industry.
It is typically used at the top of a subsea lubricator assembly as the interface for subsea wireline pressure control heads and other riserless subsea intervention system components. However, it is, at times, used at the bottom of the lubricator, to enable rapid connection and disconnection of the lubricator from the well control package, either at surface or subsea.
Operators have commented on the “rugged” and “robust” nature of the connector and its ease of use. One major operator, who has a SLIC at the bottom of its lubricator assembly, was able to deliver a highly successful project to a client that would not have been possible without it.
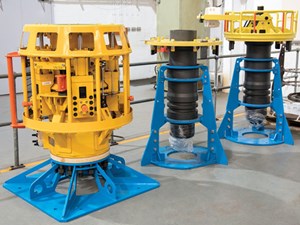
In that instance, the wells required high-rate injection of stimulation fluid (much greater than would have been possible through other access routes) so, after pulling the crown plugs out of the christmas tree, the lubricator was recovered, and a modified SLIC mandrel, with an adapter to two 3-in. hoses, was installed. Using the two large-bore hoses, a stimulation vessel was then able to connect and pump very high-rate stimulation fluids—resulting in productivity improvements of over 50% on the project.
The SLIC essentially is a multi-functional access point, enabling a wide variety of tools to connect to it, creating a highly flexible and adaptable element of an intervention system. This adaptability and configuration benefits not only operators but the whole supply chain.
The technology also provides the option to extend the lubricator of a riserless intervention system and, as a result, creates the ability to recover a dropped wireline toolstring using the same RLWI system.
A CUSTOMIZED PORTFOLIO
In 2015, STL was approached by China’s BOMCo, regarding subsea hydraulic stab plate couplers. The profiles of the intended couplers were already machined into their equipment, but the couplers they had intended to use had become unavailable. Consequently, there was a need to develop couplers that would fit into the existing profiles to avoid scrapping the high-value machined components.
The company’s initial coupler development strategy had been to enter the subsea stab plate coupler market by developing elastomeric sealing couplers for temporary equipment, but the client required much more challenging metal-to-metal sealing couplers for permanent installation. STL developed five different coupler configurations and sizes, each with its own set of design complexities. They required extremely small components that would work under very high pressures, while minimizing the restriction of fluid flow, using several different exotic alloys for both corrosion resistance and strength.
While major suppliers of hydraulic stab plate couplers produce permanently installed couplers, which use a metal-to-metal seal when engaged, they use elastomeric or polymer seals to seal the poppet when they are disengaged. The company created a metal-to-metal sealing poppet, enabling the couplers to seal with metal seals, whether engaged or disengaged. This means the male coupler—typically left permanently subsea—has only metallic components that will not degrade over its lifespan.
The company’s project ultimately allowed it to run a series of internal process improvement programs, focused on more efficient management of orders for small, standardized products. New stab plate coupler variants are now in development, with orders having been secured from customers for elastomeric sealing variants. The first ¼-in., 10-ksi stab plate couplers have just been delivered to the customer, with 3/8-in., ½-in. and ¾-in. variations now in development.
After significant effort, STL offers a growing hydraulic coupler portfolio in a lead time of 12 weeks or less. This allows clients to become increasingly responsive and supportive of their own customers’ needs, while reducing project delays.
FUTURE INNOVATION
According to Oil & Gas UK, if a supply chain company can provide a solution that improves efficiency and reduces costs, it typically has been able to protect or grow market share. The timely progression and development of technology and innovation that is driving supply chain efficiency is essential to help and sustain production for the future, which ultimately has global implications for the offshore/subsea sector.
The deployment of new technology has been beneficial to more recently drilled development wells, which have experienced increased efficiencies as a direct result. As an industry, we will need to be even bolder and braver in terms of how we introduce and incorporate the latest cutting-edge solutions into the subsea sector, and beyond, to recover the remaining oil reserves.
This growing urgency and drive for innovation in the subsea sector has seen the development of some of the world’s first purpose-built, well intervention technologies. Acceptance of new technology in the subsea industry is always challenging, yet, with signs that the industry is beginning to recover, operators and service companies are taking a different approach to component selection. We are having conversations that are more open to technological advancements, providing invaluable performance benefits.
- Advancing offshore decarbonization through electrification of FPSOs (March 2024)
- Subsea technology- Corrosion monitoring: From failure to success (February 2024)
- Driving MPD adoption with performance-enhancing technologies (January 2024)
- Digital transformation: A breakthrough year for digitalization in the offshore sector (January 2024)
- Offshore technology: Platform design: Is the next generation of offshore platforms changing offshore energy? (December 2023)
- 2024: A policy crossroads for American offshore energy (December 2023)
- Applying ultra-deep LWD resistivity technology successfully in a SAGD operation (May 2019)
- Adoption of wireless intelligent completions advances (May 2019)
- Majors double down as takeaway crunch eases (April 2019)
- What’s new in well logging and formation evaluation (April 2019)
- Qualification of a 20,000-psi subsea BOP: A collaborative approach (February 2019)
- ConocoPhillips’ Greg Leveille sees rapid trajectory of technical advancement continuing (February 2019)