Tie-backs and seafloor pumping improve economics in deepwater developments
During periods of elevated oil prices, many options are examined to optimize production from deepwater discoveries. These include waterflooding, miscible gas injection and other EOR/IOR methods. While showing improved recoveries in some cases, these options are capital-intensive and carry significant technical risk. Lower commodity prices have provided clarity. Project development teams, which are actively working through the various options, are slowly concluding that tie-back developments are the key, remaining development method to meet today’s stringent economic criteria.
Tie-backs present an attractive lower-cost alternative for deepwater developments. Current commodity prices make it difficult to justify the large host developments that entail building a new FPSO, spar or TLP. These large capital investments are justified only for mega-discoveries, in areas where there is no available infrastructure. For most discoveries, the strategies now focus on reduction of development costs and making the best use of existing assets. Despite the difficult business environment for new greenfield developments, leases have fixed expiration terms, and some level of exploration drilling continues.
A tie-back option utilizing a multi-phase pump, termed a multi-phase pump tie-back (MPTB), is particularly attractive in terms of reduced capital costs and improved rates/recovery. One way to look at MPTB is that it represents an alternative to a host development in many ways. An MPTB is able to create the low wellhead pressures, similar to a local host, but at a much lower cost. Rather than a host alternative, instead, multi-phase pumping is often viewed as an upside to a no energy-added, bare pipe tie-back development. In fact, MPTB’s are an intermediate step between a host and a bare pipe tie-back.
Tie-backs that utilize multi-phase pumping are attractive for sustaining flowrates and adding reserves. Some of the recent seafloor pumps installed in the GOM are single-phase pumps. However, tie-backs are more likely to need multi-phase pumps, due to the higher reservoir GOR’s and bubble point pressures encountered. In addition, a lower wellhead pressure is desired to lower BHP and increase flowrates/recovery. Multi-phase pumping also helps in flowline sizing, as a smaller pipeline is possible, improving stability and slugging characteristics versus a larger-diameter flowline that would be considered to reduce early-life backpressure on the wells.
MULTI-PHASE PUMPING
Subsea pumping has evolved to be a reliable, widely used, artificial lift method for offshore production. Currently deployed systems extend from single-phase to multi-phase and cover a wide power range (1 MW–6.4 MW). A good review of multi-phase pumping technologies is available in published literature.1,2 Although a detailed discussion of multi-phase pumping is beyond the scope of this article, it is important to highlight the three primary types of subsea pumps: 1) rotodynamic; 2) twin-screw; and 3) the electrical submersible pump (ESP) form of rotodynamic pumps. Multi-stage rotodynamic pumps have been installed most widely in subsea applications, and will be the focus of much of the discussion regarding new and emerging cost-reduction capabilities for tie-back developments. As will be shown, subsea pumps have been applied over a wide range of applications, from single-well pumping systems to multi-phase well caisson-ESP systems to large, dual-pump stations used in association with hub developments.
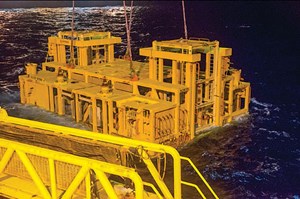
Rotodynamic pump systems. Helicoaxial, centrigual and hybrid rotodynamic pumps represent the clear majority of the installed subsea boosting systems. While much can be said related to multi-phase pumping for subsea applications, this discussion will focus on important new capabilities relevant to tie-back developments. These include new HPHT-rated seafloor pumps and high-boost pumps. Pump burst casing pressures of 15,000 psi are now available, and the pump/motor/seal system has been qualified to 350°F. This opens new areas of the GOM to MPTBs, as many recent deepwater discoveries have been in HPHT reservoirs. The Barracuda project, operated by Petrobras, represents the deployment of a new generation of high-boost multi-phase pumps3 which, on the test stand, demonstrated a boost of 2,350 psi at GVF of 60%. There are several vendors providing multi-phase pumping options that are deployable or being qualified.
Over the past year, several key, hub-based, seafloor pumping systems have been deployed. In the GOM, Exxon Mobil deployed two single-phase pumps from OneSubsea for the Julia field, Fig. 1. Chevron also deployed three similar pump stations for the Jack/St. Malo (JSM) project, Fig. 2. The Julia development is a 15-mi tie-back to the Chevron JSM semisubmersible host FPU. In December 2016, Subsea Integration Alliance announced the longest deepwater MPTB project, which will be developed by Murphy E&P for its Dalmatian field, in the GOM. This will be a 22-mi tie-back to Chevron’s Petronius compliant tower platform. It is anticipated that these types of tie-back developments will dominate the GOM for the upcoming decade. Emerging cost-reduction methods will open a path to development for even smaller discoveries.
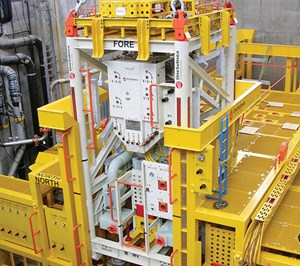
ESP-based subsea pumping systems. Seafloor boosting options that utilize wellbore-type ESP systems have been applied in several ways for subsea pumping. ESPs have been skid-mounted and installed in short caissons. Skid-mounted ESPs have been installed by Petrobras in Brazil and in Cascade-Chinook field in the GOM. A skid-mounted ESP provides lower intervention costs than ESPs installed in subsea caissons, but so far, the skids have been quite large. Caisson-installed ESPs have been utilized in Brazil and the GOM.4 A large-diameter caisson, in the 200-to-300-ft depth range, is installed to house a high-horsepower ESP string. The volume provided by the caisson provides an advantage in terms of separation/surge capability, when the caisson is operated as a gas-liquid separator. The caisson also can be operated in unseparated mode, with all flow pumped by the ESP. In this case, the caisson provides an advantage in conditioning the flow before the pump and slug damping. The downside to the currently deployed caisson-ESP system is the large intervention cost (rig intervention), low ESP reliability and poor separator efficiency under some conditions.
In recent years, ESP systems have advanced in their ability to handle gas, moving them into the realm of multi-phase pumps for subsea applications. As demonstrated by large-scale testing,5,6 gas-handling ESP stages, placed at the inlet of the ESP pump, can prevent gas lock-up to GVFs of 60%, and effectively pump a multi-phase mixture in the 0–40% GVF range. ESP systems provide a key advantage for tie-back developments by minimizing topside modification. ESPs do not require a barrier oil system and hold the potential for lower costs. However, the reliability of these systems continues to be in the 1-to-3-year MTBF range, which is far less than for rotodynamic seafloor pumping systems.
Twin-screw pumps. In some cases, a twin-screw pump (TSP) has been deployed. TSPs have an advantage when pumping heavy oil, and are widely used onshore, due to their ability to handle high gas volume fractions (GVF). In a recent study, TSPs were shown to effectively pump at GVF’s of 95%, when a small amount of liquid is cooled and re-circulated.7
SPECIAL CONSIDERATIONS FOR TIE-BACKS
Tie-back developments differ from new hub-based developments in two important ways. First, a tie-back is, by definition, bringing production onto an existing structure, such as a platform, spar, TLP, FPSO or FPU. This requires modification to an existing and, most often, producing asset. The multi-phase pumping approaches that minimize the impact on the host structure are most likely to succeed, as they are easier to fit into the host work schedule, are generally less complex, and do not require costly modifications and coordination. Secondly, a tie-back typically will utilize a longer flowline than a hub-based development. The greater length increases the importance of lower-cost umbilical options, because the umbilical cost begins to dominate project economics. There are two new methods to address these important differences.
During periods of high oil prices, seafloor pumps fell victim to the same cost run-ups as other parts of the industry. For seafloor pumps, “over-specification” became common, as deepwater producers focused on added features and “like-to-have” options, rather than the minimum technical specifications to deliver production safely and efficiently. Every seafloor pump deployed has been custom-designed in some way.
Today, deepwater producers are beginning to look at the specifications they are providing to subsea pump suppliers, and options for standardization and cooperation. Also, single-pump systems are preferred, due to decreased upfront capital costs, and producers are more willing to tolerate short-term production loss (days) versus paying for redundancy. Another area that yields 30% or more cost-savings is the reconfigurations of subsea hardware for pumping. In this case, using alternative pump structures (PLET/PLEM/trees), and rationalizing redundancy and valves, is yielding immediate cost-savings.
Emerging cost-cutting measures. One of the limiting factors for brownfield and tie-back deployment of seafloor pumps is the modifications required topside. Utilities required to support a subsea multi-phase pump include power, pump speed control, valve control system, and the barrier oil system to support the mechanical shaft seals in the pump. In some cases, the magnitude of these topside modifications has eliminated MPTBs or pushed deployment beyond a five-year window. Recently, the concept of a “topsideless” MPTB has been proposed. The idea is to minimize the topside impact in two key areas: 1) barrier oil system; and 2) speed control. Power for the seafloor pump will either be available on the hub structure or will need to be installed; the topside less approaches discussed below will not address power.
Umbilical costs. The greater lengths of tie-back developments push umbilical costs to the forefront. Simplification of the umbilical used for the multi-phase pump may be possible, using new topside-less approaches that alter or eliminate the need for a barrier oil system. Running commercial power cables from other offshore industries is attractive from a cost viewpoint, as other industries, such as offshore power generation, would appear to offer a path to a lower-cost commodity cable.
BARRIER OIL SYSTEM ALTERNATIVES
The pumps currently in subsea installations have a barrier oil system to provide a positive pressure in the motor and generate flow across the mechanical shaft seal, from the motor side to the pump/process side. This adds complexity to the seafloor pump, necessitates installation of a hydraulic unit topside, and requires hydraulic lines to be added to the seafloor pump power umbilical. New concepts are emerging to mitigate, or eliminate, the barrier oil system, as well as the added cost and complexity.
Use of alternative barrier oil fluids. Subsea pump manufacturers are investigating and testing alternative barrier oil fluids that can be utilized subsea, without the need for extensive topside modifications. Topsides furnish MEG and control line oil to subsea trees and manifolds, and it may be possible to use these fluids as the multi-phase pump barrier oil. Compatibility of these fluids with the motor and seals is being investigated, as well as whether these can be adapted to use in support of a multi-phase pump. If an existing hydraulic line can be accessed subsea, this would enable running a bare electric power line, greatly reducing umbilical costs, in addition to eliminating the need for topside modifications to install a new hydraulic system.
Use of ESP-based seafloor pumping systems. ESPs are designed to equalize pressure across the mechanical shaft seal and do not require a barrier oil system. This has been an advantage for ESP-based systems, as topside modification for a barrier oil system is not required, and umbilical costs can be less, due to elimination of the need for hydraulic lines to support a barrier oil system. One limitation for ESP-based systems has been motor and seal failures that have typically limited run-lives to the 2-to-3-year range, significantly less than the run-life experience for seafloor pumps. A frequent failure mode for ESPs has been produced fluid entering the motor/seal, causing motor or pothead/motor connector failure. A recent advancement for ESPs that has the potential of extending ESP life is a local seal pressurization system.
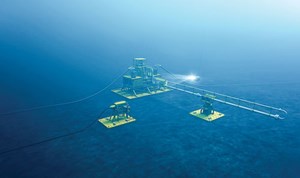
EagleBurgmann has introduced a pressure intensifier/accumulator, named ESPro, to maintain a ~30-psi positive pressure in the ESP motor, preventing fluid ingress and stabilizing the seal.8 The system contains a multi-year supply of oil, so a barrier oil system from the topside is not required. It has the potential to replace the traditional ESP seal system, which uses elastomeric bags or metal bellows and check valves to equalize pressure across redundant mechanical shaft seals.
Aker Solutions/Baker Hughes, has introduced POWERJump, through their subsea production alliance, which uses gas-handling ESP stages and an 880 series motor to pump fluid in the 15,000-to-30,000-bpd range. The system is best-suited for one- or two-well tie-backs. The ESP geometry has been optimized to be retrieved like a standard jumper, to allow lower installation costs and lower upfront capital costs, Fig. 3. Improvements also have been made in the seal section, with TRL4 qualification of the entire system expected in the first quarter of 2017.
Canned motor. The canned motor is utilized in nuclear applications, where extreme reliability is required. In these applications, a 30-plus-year run-life has been well-documented. The first canned motor/pump (CMP) was installed subsea with a TSP multi-phase application by Petrobras.
The company has also installed CMPs topside. A canned motor hermetically seals the stator and rotor inside separate metal cans, protecting them from produced fluids, Fig. 4. A canned motor does not require a mechanical shaft seal, thereby eliminating the need for a shaft seal and barrier oil system for rotodynamic pumps; an enormous benefit for MPTBs. Produced fluid flows through the canned motor, and its bearings are product-lubricated, introducing some risks in the multi-phase cooling of the motor and lubrication of the bearing by produced fluids.
A JIP has been proposed by the author to study multi-phase bearing lubrication, to quantify this risk and develop mitigation methods. Today, CMP systems are rated to 5,000 psi, as the canned motor is filled with one-atmosphere gas, and the shell must withstand the pressure of the produced fluids. Work is underway to extend the canned differential pressure rating to 10,000 and 15,000 psi, using pressure compensation, and is expected to be commercially available in one to two years. Note that a CMP can be configured in either a traditional seafloor skid or in a caisson vertical ESP form.
SPEED CONTROL
For seafloor applications, pump speed is typically controlled by a variable frequency drive (VFD) installed topside. Some level of recirculation is utilized during pump start-up, but the VFD is the primary speed control device. The need for topside installation of the VFD necessitates considerable engineering and construction time, and takes precious space/weight on the production structure (FPSO, TLP or spar). There are two approaches for topside less speed control discussed below:
Subsea VFD. The notion of a subsea VFD is attractive for tie-back applications but, thus far, subsea VFDs have been qualified only for high-power subsea compressors over 6 MW. Today, lower-power VFDs, in the 1–4 MW range, are being developed, to be suitable for MPTB applications.
Several approaches are being pursued that place existing VFD technology in an atmospheric chamber. While there is general concern regarding VFD reliability based on topside experience, it is expected that two or more products will be available commercially in two years, as a result of shared developments between the VFD supplier, subsea equipment packagers and deepwater operators.
Torque converter. Hydraulic speed control is an alternative to the VFD that has not been used widely in the subsea industry. A torque converter (TC) is a hydraulic coupling between the motor and the pump that uses adjustable guide vanes to transfer varying amounts of energy to the pump.9 The TC has been coupled with both TSPs and rotodynamic pumps. The TC sits subsea between the pump and motor, thus eliminating the need for VFD installation at the surface. A TC provides several important advantages, in addition to moving the pump speed control to the seafloor. The TC allows for the “no-load” start of the motor and up to two times multiplication of the motor’s speed.
In addition, the TC allows the motor to work at a constant speed and absorbs load fluctuations produced by changing GVFs at the pump inlet during operation. For tie-back applications, only one additional hydraulic or electric line is required subsea to control the pump speed. Methods to provide a soft-start for the subsea motor are being pursued, so that any associated topside soft-start unit can be eliminated or minimized.
CONCLUSION
The multi-phase pump tie-back (MPTB) is emerging as the most affordable development method for deep water. The MPTB approach provides improved recoveries and rates, when compared with a no-energy added, bare pipeline tie-back. New methods also are being developed to dramatically cut the cost and complexity of seafloor boosting. These include topside-less approaches that minimize topside modifications and reconfiguration of subsea hardware, resulting in a total cost savings of approximately 30% to 50%.
REFERENCES
- Martin, A. M. and S. L. Scott, “Modeling reservoir/tubing/pump interaction identifies best candidates for multi-phase pumping,” SPE paper 77500 presented at the SPE Annual Technical Conference and Exhibition, San Antonio, Texas, Sept. 29–Oct. 2, 2002.
- Shippen, M. E. and S. L. Scott, “Multi-phase pumping as an alternative to conventional separation, pumping and compression,” PSIG paper 0210, presented at the 34th Annual Pipeline Simulation Interest Group meeting, Portland, Oregon, Oct. 25, 2002.
- Huguenin, R., “Subsea high-boost multi-phase pump system: Development and application in Barracuda field, Brazil,” presentation given at the Multi-phase Pump User Roundtable, Houston, Texas, May 8, 2014.
- Gilyard, D. T. and E. B. Brookbank, “The development of subsea boosting capabilities for deepwater Perdido and BC 10 assets,” SPE paper 134393, presented at the SPE Annual Technical Conference and Exhibition, Florence, Italy, Sept. 19–22, 2010.
- Barrios, L., C. Deuel, D. Knowles, S. Patni, S. L. Scott, and K. Sheth, “Large-scale experimental investigation of ESP performance with high viscosity fluids and gas,” paper presented at the SPE 2011 ESP Workshop, The Woodlands, Texas, April 25–29, 2011.
- Barrios, L., S. L. Scott, R. Rivera and K. Sheth, “ESP technology maturation: Subsea boosting system with high GOR and viscous fluid,” SPE paper 159186, presented at the SPE Annual Technical Conference and Exhibition, San Antonio, Texas, Oct. 8–10, 2012.
- Morrison, G. L., R. Kroupa, A. Patil, J. Xu, S. L. Scott, and S. Olsen, “Experimental investigation of wellhead twin-screw pump for gas well deliquification,” SPE Oil and Gas Facilities Journal, Vol. 3, Issue 2, April 2014, pp 73–80.
- EagleBurgmann website https://www.eagleburgmann.com/en/products/seal-supply-systems/supply-system-for-esp/espro-supply-system-for-br-electrical-submersible-pumps
- Scott, S. L., J. Xu and C. Lenz, “Subsea multi-phase pressure boosting and a new approach for speed control using a hydrodynamic variable speed drive,” SPE paper 103323, presented at the SPE Annual Technical Conference and Exhibition, San Antonio, Texas, Sept. 24–27, 2006.
- Advancing offshore decarbonization through electrification of FPSOs (March 2024)
- Subsea technology- Corrosion monitoring: From failure to success (February 2024)
- X80 heavy wall pipe solutions for deep/ultra-deepwater field developments in mild sour environment (November 2023)
- FluiDeep: An innovative subsea storage and injection solution for chemicals management (November 2023)
- What's new in production (October 2023)
- Wellbore seal control and monitoring enhance deepwater MPD operations (October 2023)
- Applying ultra-deep LWD resistivity technology successfully in a SAGD operation (May 2019)
- Adoption of wireless intelligent completions advances (May 2019)
- Majors double down as takeaway crunch eases (April 2019)
- What’s new in well logging and formation evaluation (April 2019)
- Qualification of a 20,000-psi subsea BOP: A collaborative approach (February 2019)
- ConocoPhillips’ Greg Leveille sees rapid trajectory of technical advancement continuing (February 2019)