Condition-based maintenance drives efficiency and profitability improvements
These are challenging times for the oil and gas industry. The drop in oil prices has reduced margins for operators, drilling contractors, equipment manufacturers and related service providers. Many have reduced staffing and operations; some have shut down altogether.
However, some are seeing a silver lining. A slow market can be a good time to upgrade equipment and train employees. Global Drilling Support, or GDS International (GDS), for one, is utilizing the slowdown to develop product and process improvements.
A recent McKinsey & Company report says that more money isn’t required to improve operations. According to the report, best-in-class players do not incur higher costs to improve production efficiency, and high performance is not linked to a specific asset type or the maturity of assets. Instead, companies with high production efficiency are often similar in the quality of operations, approach to eliminating equipment defects, equipment choices, and planning and execution of shutdowns.
Oil and gas companies are optimizing maintenance schedules to improve efficiency and profitability by reducing equipment downtime. For both drilling contractors and equipment manufacturers, finding the “sweet spot” for equipment maintenance is critical. Conducting maintenance when it’s not needed presents the risk of wasting money, by taking the equipment out of service too soon. Meanwhile, waiting too long to perform maintenance can put employees, the environment, reputations and profits at risk.
To operate more efficiently, oil and gas companies can benefit from engaging partners, like GE, that bring both industry expertise and Big Data solutions to the table. GE works with some of the largest oil and gas companies in the world. Through solutions like Equipment Insight, GE combines industry experience with its leadership of the Industrial Internet—the convergence of the global industrial system with the power of advanced computing, analytics, low-cost sensing and new levels of connectivity—to help original equipment manufacturers (OEMs), and their customers reduce equipment downtime, while still maintaining the security of their operations.
MAINTENANCE REQUIREMENTS
Maintenance is a significant investment of time and money for drilling operations. Traditionally, rig maintenance guidelines have been set by the American Petroleum Institute (API), based on OEM recommendations, produced by hypothetical design calculations and known failure rates. On a set schedule, equipment is removed from service and maintenance is performed—whether it’s needed or not.
However, no maintenance schedule is perfect; it can result in too much maintenance or too little—neither of which is ideal. Over-maintaining equipment could mean taking it out of service while it can still operate safely, and unnecessary maintenance can pose the risk of introducing a failure that wouldn’t otherwise occur. On the other hand, being wedded to a schedule that does not take into account operations, which may dictate earlier or more frequent maintenance, can lead to unplanned outages.
Calendar-based maintenance can waste both time and money. For example, as markets recover, and equipment goes back online, a rig that has been idled for months may have to undergo prescribed maintenance based on the calendar, not the equipment condition, before it can go back into service. This can result in an equipment owner spending hundreds of thousands of dollars to overhaul rig equipment that has not been operated and, therefore, doesn’t require scheduled service. Premature scheduled maintenance also results in lost productivity. Weeks without production can be devastating to operations already working on thin margins.
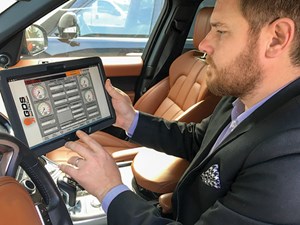
Calendars are intended to mark the passing of time, not to determine if a dynamic oil rig needs to be inspected or overhauled. There literally can be hundreds of factors involved in determining the maintenance needs (some correlating in ways that have yet to be discovered) of a rig. Examples include weight on bit, oil temperature, reactive torque, rotations per minute—the list goes on. A maintenance schedule can only determine how much time has passed and how similar machines have performed.
Scheduled maintenance looks to the past and doesn’t account for technological improvements that can make an operation safer, or increase the interval between maintenance. Every drill hole, each piece of equipment, and the operating conditions of a specific rig are unique. How, then, can time be the judge of when to perform maintenance? That is why it is important to track conditions and relationships. By analyzing how a rig has actually performed—how much weight has actually been applied to it, how many rotations it has performed—operators can better estimate when equipment needs to be inspected, disassembled and serviced. This is where condition-based maintenance can provide a competitive and financial advantage.
CONDITION-BASED MAINTENANCE
Condition-based maintenance is based on the specific performance and operation of a particular asset, not broad historical guidelines. By capturing and leveraging actual data about a particular asset, operators can help prevent failure, optimize maintenance schedules and save money by increasing operational uptime. By leveraging actual machine data, maintenance can be anticipated and scheduled, and, when a problem is detected, a downtime plan can be developed to have the right people and parts on-site to fix, or even prevent, the problem, thereby reducing the impact of maintenance, Fig. 1.
Condition-based maintenance also can help operators determine whether they can keep an asset running safely. Estimates vary depending on the asset, but moving from calendar-based maintenance to condition-based maintenance can result in a 10–25% reduction in maintenance costs.
Traditionally, condition-based maintenance has relied on the visual inspections of rig components. More recently, however, GE has deployed condition-based maintenance solutions that utilize on-rig, non-destructive testing inspections. In some applications, by implementing ultrasound technologies developed by its healthcare business unit, GE is able to use its inspection technology to create 3D comparisons of BOP parts. This process enables rig site inspection of BOPs, which allows repair requirements to be quickly identified without the need to perform a teardown.
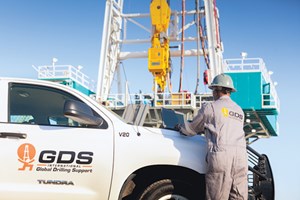
Leveraging the power of machine data is the next evolution in condition-based maintenance. Rig equipment produces hundreds of data points. GDS’s top drive, a smart machine, specifically tracks over 140 data points, Fig. 2. That data can provide important insights for condition-based maintenance, which relies on getting the right information to the right people so that they can act on it. However, capturing, storing, transmitting and analyzing rig data is easier said than done, and it can be beyond the expertise of operators, drilling contractors and equipment manufacturers.
This is where solutions like GE’s Equipment Insight come in. Equipment Insight is a cloud-based, industrial Internet remote monitoring and diagnostics (RM&D) solution that enables asset performance management. Powered by Predix, Equipment Insight gives fleet operators, owners and OEMs a cost-effective solution to help monitor the health of distributed assets, reduce costs, increase reliability and optimize equipment performance.
EQUIPMENT INSIGHT
Equipment Insight collects and manages long-term fleet performance data and alarms, and it administers user access. Based on this historical data, the Equipment Insight solution performs trend analysis of a single machine or an entire fleet. It then delivers role-specific key performance indicators (KPIs), alarms and trends to either the end user or OEM personnel, via mobile device applications or a web browser.
Because Equipment Insight is a universal solution, it can be layered on top of any intelligent control device. The data are buffered to protect against network outages, encrypted, and then transmitted to the OEM or operator. An optional 3G interface provides access where end-user networks or public infrastructure aren’t available.
Equipment Insight is ideal for cost-constrained businesses. It is deployed through a “Software as a Service” (SaaS) model and can be installed on a subscription basis, thereby negating the need for a large upfront capital expenditure. Because it is a horizontal, out-of-the-box solution, Equipment Insight customers get not only a very simple-to-implement platform, but also a powerful solution. Installation is fast—the solution is typically up and transmitting data in a few days. Based on their domain expertise, OEMs and operators set up specific machine parameters—such as pressures or temperatures—to track and analyze. Customers can add their own KPIs, alarms, reports, notifications, tasks and workflows to fit their specific operations and requirements.
CASE STUDY
GDS develops and provides drilling equipment and services that drive innovation and automation technology in the oil and gas industry. Its state-of-the-art line of top drives, The Global Drilling Machine (GDM), solves many of the problems that reduce performance and reliability of conventional top drive models.
GDS got its start by repairing and servicing top drives to API requirements, and then began offering inspection services and spare parts before designing its own top drives in 2010. The company put a programmable logic controller on its top drive system, so that it can monitor the health of the top drive and perform onboard condition-based maintenance.
GDS wanted to go beyond offering control with proprietary condition-based maintenance software by creating a smart top drive. The company realized that by leveraging the constant stream of data produced by its unique top drive sensors, it could help customers improve the functionality of their equipment and revenue stream. By improving data collection, analytics and management, the company aimed to increase uptime, reduce costs and meet maintenance requirements, while still protecting employees, the environment and assets.
Servicing top drives, based on actual usage instead of the API standard of five years for a major CAT IV inspection, could save hundreds of thousands of dollars in overhaul costs and help avoid weeks of production lost during inspection and overhaul. However, the company faced a common challenge—data necessary for condition-based maintenance was stranded on the machine at the rig or not available at all for the OEM to help its customer safely make that determination. The company sought to put that data into the pipeline for its customers.
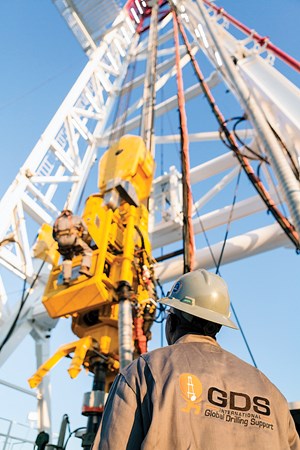
To better monitor the health of its top drives, and to optimize operation and maintain rig uptime, the company deployed GE’s Equipment Insight solution for a six-month pilot program with Orion Drilling Company. The pilot program included the installation of two field agents on GDS’s top drives on rigs operating in the Marcellus and Utica shales. With the cloud-based solution, GDS monitored various data points—including load, RPMs, flow, pressures, temperatures and torque. These critical data provided valuable insight into the operating performance of the top drive. The information was transferred by Equipment Insight, via a cellular connection. From there, GDS analyzed the data and communicated real-time operating conditions and alarms to Orion. The contractor then used the data to push out condition-based maintenance routines, Fig. 3. The data also were used to remotely log-in to troubleshoot and modify perimeters, without the cost and time typically associated with sending out a specialized technician.
With GE’s Equipment Insight solution, GDS is able to provide advanced remote monitoring and diagnostics to its customers. It can provide these services without having to make a large upfront investment in expensive software or data centers to manage the data, and without replacing existing hardware technology. In addition, GE provided GDS with a customer success manager, who helped ensure technical satisfaction. This manager supports OEMs in their efforts to franchise their solutions to expand aftermarket service capabilities and revenues. GDS can outfit additional drilling equipment with sensors to link them into Equipment Insight, creating a truly smart rig.
SUCCESSFUL PARTNERSHIP
All three companies involved in the pilot have termed it a success. For GDS, using Equipment Insight has improved equipment reliability and optimized performance. By helping customers increase the time between planned service intervals, the company is able to reduce the operating cost of their equipment.
Backed by the continuous flow of data from its top drives, GDS can quantify this reduced total cost of ownership, providing a tangible, desirable differentiator for its top drives. It also broadens the company’s portfolio, allowing it to expand its services business and revenue.
Gathering and analyzing data from top drives is just the beginning for GDS. GE’s Equipment Insight can be layered on top of almost any intelligent industrial device, making it a universal solution for data management. This capability enables companies to expand their monitoring capabilities to other oilfield equipment—such as draw works, mud pumps, catwalks and generators—by engineering specific sensors or integrating existing sensors.
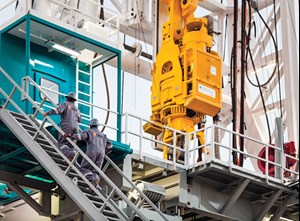
For Orion, the Equipment Insight trial resulted in greater uptime and reduced maintenance intervals. This saved the company money by keeping equipment operating and reducing maintenance costs. Equipment Insight also provided the company operational insights. Armed with an analysis of equipment data, the company can now predict operational events, allowing it to improve operations and grow revenues .
For GE, the partnership with GDS and Orion provided another example of how Industrial Internet solutions, such as Equipment Insight, reduce risk, improve service and increase uptime for fleets of distributed assets. It also broadened and deepened GE’s oil and gas domain expertise.
CONCLUSION
In today’s industrial Internet economy, data are critical for oil and gas companies, Fig. 4. Much like the natural resources that these operations tap, equipment data are most beneficial when they can be captured, transported and processed. As the industry continues to weather market uncertainty, leveraging the Industrial Internet to maximize performance and asset value can make an important difference in the success of oil and gas operations. Looking ahead, those that seek to optimize their operations now can hope to be rewarded with a distinct head start, as they prepare for the future.
ACKNOWLEDGMENTS
The author would like to thank Steve Pavlosky, senior product manager in GE’s Automation & Controls business, for contributing to this article.
- Coiled tubing drilling’s role in the energy transition (March 2024)
- Digital tool kit enhances real-time decision-making to improve drilling efficiency and performance (February 2024)
- E&P outside the U.S. maintains a disciplined pace (February 2024)
- Prices and governmental policies combine to stymie Canadian upstream growth (February 2024)
- U.S. operators reduce activity as crude prices plunge (February 2024)
- U.S. producing gas wells increase despite low prices (February 2024)
- Applying ultra-deep LWD resistivity technology successfully in a SAGD operation (May 2019)
- Adoption of wireless intelligent completions advances (May 2019)
- Majors double down as takeaway crunch eases (April 2019)
- What’s new in well logging and formation evaluation (April 2019)
- Qualification of a 20,000-psi subsea BOP: A collaborative approach (February 2019)
- ConocoPhillips’ Greg Leveille sees rapid trajectory of technical advancement continuing (February 2019)