Efficiencies and capabilities designed for the bottom line
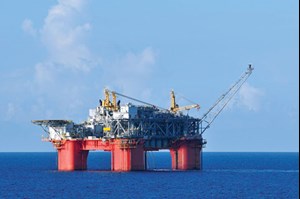
There’s almost always room for improvement. The offshore industry has proven that many times over the years as it has adapted, evolved, and reinvented itself. Whether it’s a better process, a new tool, or a whole new concept, advances focused on safety, reliability, cost and capability are a bedrock fundamental of the business. In the following summaries, NOV, Baker Hughes, Varel, AFGlobal, and Weatherford present some of the offshore advances they are focused on, and in doing so provide insights on where the industry is headed.
DATA DOES IT BETTER
Today the industry relies on pressure and dynamics measurements near the bit, and uses torque and drag, and hydraulic models, to estimate downhole conditions along the string. The future of drilling, however, will be built using high speed, real-time data to optimize drilling performance, says NOV.
NOV’s eVolve Optimization Service equips existing rigs and crews with an advanced toolkit that enables informed decision-making and provides real-time analytics capability. The premier tier of the service, AUTOMATE, uses the world’s first application of closed-loop, downhole data to drive improvements in efficiency, wellbore quality and safety.
An example of the eVolve service, is the improved efficiency achieved in developing a challenging field, using IntelliServ wired drill pipe and along-string sensor technology. The field consisted of an oil reservoir and several deeper, structurally complex, high-pressure gas and condensate reservoirs. Three oil wells were drilled; one water injection well and two gas wells. Annular pressure and vibration measurements along the string were used to monitor hole cleaning and assess the impact of parameter changes, including string rotation, rate of penetration (ROP), and fluid properties.
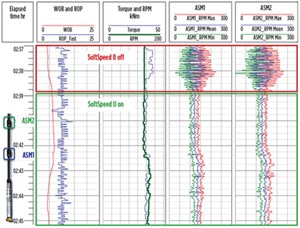
The measurements obtained by the along-string tools were used to continuously build knowledge and optimize well geometry, while the extended dataset obtained from the tools allowed the client to increase reservoir exposure. As a result of using the eVolve service, the total number of wells necessary to reach the planned production level was reduced from 11 to 10.
Mitigating vibration issues. The NOV SoftSpeed II stick-slip prevention service also was used to mitigate torsional vibrations on this project, Fig. 1. The service uses automated vibration dampening to reduce stick-slip vibration during drilling operations. By stabilizing drill string torque, the SoftSpeed II service helps maximize the drilling envelope of extended-reach wells. Its use helped to improve drilling efficiency and reduce nonproductive time.
Measurable improvements. Using real-time measurements along the drillstring makes it possible to efficiently monitor and manage borehole conditions, and extend reservoir sections in a safe manner, Fig. 2. The resulting performance optimization achieved with the eVolve service eliminated drilling an entire well, saving approximately 70 days of rig time. Moving forward, these types of significant increases in performance and efficiency will drive much-needed change in the industry.
RECIPES FOR SUBSEA EXTREMES
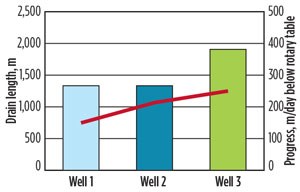
Producing from deepwater wells brings new extremes to the familiar challenges of mitigating corrosion, scale, hydrate, paraffin and asphaltene. Stability, deliverability and system compatibility are critical factors for treatment in subsea umbilical systems, where plugging and failure can lead to unacceptable HSE and operational risks, unnecessary delays and downtime, costly repair and replacement expenses, and deferred production. In these subsea applications, chemical deliverability has become as important as chemical performance.
The challenge is complex and has resulted in industry-wide studies, API standards, and new ways of qualifying production chemicals for subsea extremes. Baker Hughes has developed FATHOM XT deepwater subsea-certified production chemicals to provide the reliable performance required for flow assurance production challenges in subsea tie-backs.
JIP produces new standards. Key to this subsea performance is a rigorous design, testing and certification process to confirm chemical performance, cleanliness and system compatibility. Testing is based on standards recommended by the findings of the Blockage Avoidance in Subsea Injection and Control Systems (BASICS) Joint Industry Project (JIP) and published in API specification 17A TR6. Baker Hughes partnered with several operators, chemical and fluid vendors, and industry trade groups in the JIP that produced the standard.
The testing process is extensive and takes a broad scope of variables into account. Stability testing is focused on preventing conditions, including sedimentation, phase separation, and haze development in the chemical. It investigates stability in various temperature and pressure conditions in the umbilical, at the seabed and in the injection system. In addition, capillary tests evaluate injection in capillary tubing strings at high temperatures and pressures to avoid the risk of blockage or damage. Temperature cycling tests examine thermal degradation caused by temperature extremes. Shelf life is also a stability consideration. Tests study thermal aging of the chemicals that can result from storage and transportation conditions.
Product deliverability studies are aimed at achieving a sufficient injection rate in long, small-bore umbilical tubes. They examine physical and chemical properties, including density, pour point, viscosity, and susceptibility to forming a hydrate plug, if production gasses bypass subsea check valves. System compatibility analysis ensures production chemical compatibility with standard metals and soft goods used in construction of the chemical injection and delivery system, and with the canning and spacer fluids often used for storage, pre-commissioning and commissioning of umbilicals.
Solving the asphaltene issue. Operations in the deepwater Gulf of Mexico (GOM) illustrate the challenge and the Baker Hughes solution. An operator managing a large subsea project in the GOM experienced a failure with its methanol umbilical to a subsea well. A line was jumped from another well to the first well, to treat it with methanol, causing the second well to shut in, due to pressure. The only solution to get the second well back online was to commingle with a third higher-pressure well, but the high asphaltene content of the third well was incompatible with the condensate from the gas well.
The only solution that would not cause a loss of production was to chemically inhibit the asphaltenes from precipitation, which is why the company’s subsea-certified asphaltene inhibitor was selected. The certified inhibitor proved highly effective at preventing the asphaltene precipitation, and full production was restored to the well that had been shut in because of the umbilical failure.
BIG ON EFFICIENCY
Drilling efficiency in large diameter surface and conductor holes is not solely a bigger-bit-is-better solution. Even in these shallow applications, demands on the bit vary considerably and require a lot of fine-tuning. Size is only part of the answer; the rest relies on bit design options and how efficiently they can be applied.
Large borehole applications. Large-hole drilling programs for deep wells in the Arabian Gulf, and splitter wellheads in the North Sea, make significantly different demands on the bit. As objectives and challenges change, so must the bit. Achieving this versatility in a cost-effective way is a challenge. Varel Oil & Gas Drill Bits is working the equation from several directions with its Everest roller cone bit series.
The series owes a lot to advances in modeling and materials science, which provided the means to engineer a flexible design for a better-balanced bit across a variety of configurations and performance metrics, such as hole conformance and total footage. The tungsten carbide insert and steel tooth series begins with a 14 3/4-in. product and concludes with a 45-in. 5,100-lb behemoth that Varel says is the industry’s largest commercial bit.
There are three models in the series, distinguished by size and configuration. They aim to provide an integrated solution for large-diameter pilot, surface and intermediate hole sections. This versatility in the different hole sections is meant to simplify procurement, reduce costs, improve logistics, enable management of bit programs and avoid the cost of overbuilding to ensure performance.
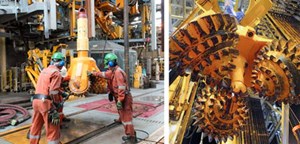
Model selection is guided by durability demands that range from tough carbonates in intermediate hole sections to low-abrasion conditions in pilot holes. Each model builds toughness in steps with features that range from shirt tail protection and high-energy tumble processed inserts to diamond enhancement.
Offshore Middle East. Everest bits have been used in some very different large-hole applications. Deep wells in the Arabian Gulf typically have large surface sections drilled with a pilot hole, followed by second run with a hole opening assembly. Drilling the top-hole section of these wells in a single run offered a significant efficiency gain. In an attempt to do so, a 44-in. milled tooth bit was manufactured with a design emphasis on minimizing tooth wear and cutter tracking. The bit successfully drilled the entire section and was dull-graded in good condition, Fig. 3. Cost reductions included one less trip, elimination of time to change bits and BHAs, and time to enlarge the hole.
Danish North Sea. The large-hole task in the Danish North Sea involved construction of splitter wellhead systems in which dual strings were run through a 40-in. conductor pipe. The need to land the conductor in a clay band to facilitate cementing eliminated driving the conductor pipe. Instead, the installation was drilled using a specially made 45-in., hybrid, milled tooth/roller cone bit with a three-bladed PDC core breaker in the center. Run on a 12¾-in. mud motor, the bit successfully drilled 88 m at 10.6 m/hr and was dull-graded in good condition.
MODULARITY IN THE MIDDLE
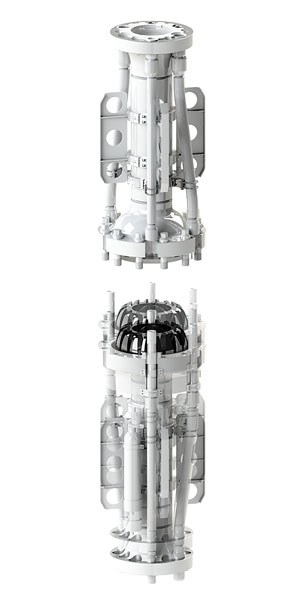
Between deepwater rigs and managed pressure drilling (MPD) stands a fundamental change. The rig must be ready to provide a closed-loop circulation system instead of a traditional open-to-the-atmosphere system. The transition is complicated by the need to integrate a multitude of rig designs with a broad range of proprietary MPD systems.
Integrating MPD and the riser. The middle ground, where this integration takes place, must accommodate the needs of both parties. AFGlobal is occupying that position with a modular technology that integrates with the riser, creating a closed-loop-ready configuration that facilitates riser gas handling (RGH) and MPD, Fig. 4. The technology has been deployed successfully in the GOM, Brazil and offshore West Africa.
Its modularity is key to accommodation. The RGH system is modified readily to accommodate current and future design nuances presented by various rig designs and MPD services. It also expedites component service, maintenance and upgrades.
Case in point is a recent upgrade of the RGH system’s drillstring isolation tool (DSIT). The DSIT Gen II tool is a riser joint component that helps eliminate surging and swabbing in the wellbore while installing or removing the bearing/seal in the rotating control device (RCD), a key MPD component. The tool also enables flow diversion for RGH during RCD sealing element changes, and as a backup if the RCD does not hold sufficient pressure.
The system’s modular design enables fast component maintenance and upgrades aboard the rig to significantly reduce downtime. Maintenance is done with auxiliary lines in place, and the DSIT remains in position when a MPD system’s RCD is added to the RGH system.
The RGH system is an enabling technology that integrates with the marine riser and rig systems in retrofits and new dynamically positioned and moored rigs. The system components consist of a top and bottom riser interface, drillstring isolation tool, and a valve system to distribute flow to a dedicated manifold and integrated control system.
The system enables either conventional or closed loop operations. Flow distribution for RGH is controlled without the rotating control device (RCD) needed for MPD. As a fully MPD-scalable technology, the RGH system enables the addition of an RCD using a specialized adapter to integrate the equipment with the riser. The RGH system works with all known MPD service providers’ equipment.
RAISING THE COMPLETION BAR
The continued advance of offshore completion technologies is playing a critical role in reducing offshore operational risks, securing wellbore integrity, minimizing completion costs, and optimizing life-of-well production. Applied to core technologies, such as safety valves and gravel packs, innovative engineering can significantly raise the bar for standards of operational and economic performance.
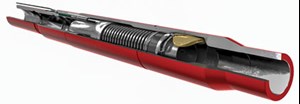
Study sets higher safety valve standards. The safety of rig personnel, assets, and the environment can come down to a subsea safety valve. Weatherford studied historical points of failure in valve designs to improve this key barrier against catastrophic loss of well control. The resulting Optimax safety valve tested beyond API 14A standards for subsurface valve equipment, Fig 5. It has proven to be a highly reliable device with zero failures in more than 7,000 deployments, worldwide, that account for over 20,000 years of cumulative service life.
Super-slim and deep-set tools. The Optimax portfolio includes super-slim and deep-set valves. Compared to curved-flapper safety valves of an equivalent size, the super-slim flappers have a reduced outside diameter. As a result, smaller casing strings can be used to reduce completion costs and still allow space for bypass lines. Deep-set valves provide fail-safe closure at depths greater than 12,000 ft (3,658 m) without being affected by tubing pressure or relying on the long-term storage of nitrogen.
Integration cuts gravel pack time. To cut days of rig time from openhole gravel pack operations, Weatherford has combined its WFXO gravel pack system with its TerraForm deep-set, open-hole packer system. Described as the first fully integrated, V0-rated (ISO’s highest, special gas-tight seal standard) gravel-pack system, the WFXO system includes the packer, quick connect and gravel-pack sliding sleeve. It is designed to run with the TerraForm open-hole packer system, shunt-tube screens, and the V1-rated OptiBarrier ball valve. This WFX0 configuration eliminates the need for a dedicated deep-set barrier run with an additional packer and ball valve, which can save two to three days of rig time by enabling single-trip gravel packing across multiple zones.
Inclusion of the TerraForm packer in the WFX0 system enables cased-hole functionality in openhole environments to save costs and time of cementing or perforating the lower wellbore. The packer uses proprietary cup-seal technology to conform to non-uniform wellbores and provide life-of-well zonal isolation. The cup seals are tension-set, which enables them to maintain form throughout thermal cycles. A unique clutch mechanism eliminates the possibility of the packer harming the reservoir or creating micro fractures. The Rokankor anchoring system, available on certain models of the TerraForm packer, prevents movement of the completion string while distributing forces evenly into the formation to prevent damage.
- Coiled tubing drilling’s role in the energy transition (March 2024)
- Advancing offshore decarbonization through electrification of FPSOs (March 2024)
- What's new in production (February 2024)
- Subsea technology- Corrosion monitoring: From failure to success (February 2024)
- Using data to create new completion efficiencies (February 2024)
- Digital tool kit enhances real-time decision-making to improve drilling efficiency and performance (February 2024)
- Applying ultra-deep LWD resistivity technology successfully in a SAGD operation (May 2019)
- Adoption of wireless intelligent completions advances (May 2019)
- Majors double down as takeaway crunch eases (April 2019)
- What’s new in well logging and formation evaluation (April 2019)
- Qualification of a 20,000-psi subsea BOP: A collaborative approach (February 2019)
- ConocoPhillips’ Greg Leveille sees rapid trajectory of technical advancement continuing (February 2019)