Treating water in heavy oil emulsions with microemulsion fluids
The “heavy” nature of crude oil is due primarily to a relatively large proportion of complex, high molecular weight, aromatic and naphthenic compounds, and a relatively small proportion of low carbon number hydrocarbons. Heavy crude oils include asphaltenes, resins, naphthenates, mercaptans and polar compounds, such as carboxylates, that exhibit high interfacial activity and promote interaction between the oil and the water phase, enabling formation of water-in-oil (W/O) emulsions. The emulsified water in the crude oil could be produced water, completion brine, drilling fluids, injection water or a combination of some or all of these.
Emulsions of water- or brine-in-crude oil can form in the reservoir, near the wellbore or in downhole and surface facilities during wellbore construction or production. In addition to the natural components with interfacial activity that are present in crude oil, additives used in drilling, completion and hydraulic frac fluids, such as emulsifiers, friction reducers, ROP enhancers and corrosion inhibitors, also could produce emulsions when they come in contact with crude oil. Emulsion problems also can result if high-rate acid treatments are pumped into a reservoir without the appropriate additives to prevent emulsion formation. In this case, the mechanical energy and low pH of the acid-based fluid creates an ideal environment for generating unwanted viscous emulsions.
THERMAL EOR PROMOTES W/O EMULSIONS
Thermally enhanced oil recovery processes, such as in-situ combustion and steam injection, also contribute to emulsion problems by the addition of thermal energy that disperses W/O. These emulsions are stable and cause severe production problems. In all cases, mechanical and/or thermal energy is required to generate small emulsified water droplets in systems composed of two immiscible fluids (water and crude oil) and surface active molecules that are present, either in the crude oil or in fluids pumped into the producing formation.
Depending on the amount of energy and the strength of the added chemicals or natural surfactants in the crude oil, the emulsion stability can be either strong or weak. When a crude oil/water mixture encounters high shear conditions in pumps, production tubing, safety valves, or other process equipment, a stable emulsion can form. For crude oil/water systems that do not have naturally-occurring molecules acting as emulsifiers, a dispersion of one liquid phase into the other phase is generated, but the dispersed droplets will coalesce and separate relatively easily after the shear condition ceases.
Heavy oil with stable emulsions creates flow assurance issues, and they also increase surface treatment costs for pipelines, separation facilities and processing plants. The disposal of the water, salt and residual oil separated from the crude before the refining process can be costly and affect the value of the operator’s asset. To select an efficient treatment for crude oil emulsions, it is important to understand where, and how, they are produced, their composition and the properties of the W/O oil emulsions.
EMULSION BREAKING
There is no standard method to estimate emulsion stability. It depends on the conditions under which the emulsion is handled. A good macroscopic indicator of emulsion stability is the time required for a given amount of emulsion to separate.
Emulsion stability depends on many factors related to adsorbed molecules with surface activity. The two important breakdown processes for crude oil emulsions are flocculation and coalescence. Flocculation refers to aggregation of droplets, without any change in the primary droplet size. Coalescence occurs when two or more droplets come into contact. Thinning of the liquid film can result in a rupture that allows the droplets to coalesce. In some emulsions, dispersed droplets can closely approach, but do not coalesce, due to electrostatic repulsion or steric stabilization of the interfacial film surrounding each droplet.
The principle of emulsion breaking can be explained using the concept of optimum formulation at zero hydrophilic-lipophilic difference (HLD). The optimum formulation at zero HLD signifies no difference between the hydrophilic and lipophilic interaction energies of the surface active molecules in the emulsion system. This formulation condition exhibits low interfacial tension and minimal emulsion stability, the desired situation for emulsion breaking. Figure 1 shows the variation of emulsion stability with HLD. Water-in-crude oil emulsions are found in the region of HLD>0.
Emulsion stability decreases when the optimum formulation is approached from either side, facilitating the drop-breaking process. When the formulation approaches the optimum formulation, the coalescence rate of the droplets increases considerably, which is the desirable condition for eliminating emulsions in crude oils.
KEY PROPERTIES OF W/O EMULSIONS
Detailed properties of the emulsion, together with interfacial properties of the crude, are key factors that need to be understood. The more important considerations in W/O emulsions are:
- Reduction of interfacial tension in the range of HLD>0 to decrease the average droplet size to make the W/O emulsions more stable.
- Emulsions with small droplets form stable emulsions.
- A high acid number indicates the presence of components with interfacial activity in the oil that stabilizes emulsions.
- Acid treatments can precipitate asphaltenes and molecules with interfacial activity that stabilize emulsions.
- High interfacial viscosity and deformation resistance of the emulsifier film reduces coalescence of water droplets in the emulsion. Low pH values in the aqueous phase can lead to high interfacial viscosity and a viscoelastic film that produces a mechanical barrier to droplet coalescence.
- High viscosities of external phase crude oil decrease the coefficient of diffusion and decrease the droplet collision frequency, increasing the apparent stability of W/O emulsions.
- Divalent cationic molecules, such as calcium and magnesium, may produce a compact film around the droplets.
Microemulsion treatment. The mobilization of high-viscosity W/O emulsions from the formation rock to surface facilities is difficult, especially at low temperatures. To restore an oil’s viscosity to increase mobilization and optimize production, a fluid with low viscosity and interfacial properties that destabilize or break the emulsions should be used for wellbore clean-up. In this scenario, a custom-designed, single-phase microemulsion treatment, to break the W/O emulsion and promote flow, may be beneficial and extend the well’s production life.
Microemulsions are single-phase, bi-continuous systems, in which oil and water coexist, separated by an interfacial film of surfactant molecules. They are thermodynamically-stable systems composed of a solvent or oil, brine, surfactants, and optional co-surfactants and linker molecules. To predict the behavior of the microemulsion, when it contacts W/O emulsions, some important tests that need to be evaluated for each particular crude oil system are emulsion breaking and sludge destruction, without adding mixing energy (diffusion process) to the microemulsion/crude oil emulsion system.
A good microemulsion formulation must tolerate changes in salinity, temperature, and type of oil to which it is exposed.
LABORATORY TESTS
Samples of crude oil and formation water from a California well were used to determine the effectiveness of microemulsions for breaking emulsions. The crude oil sample of 21.3°API had a high viscosity and very low pourability properties. Several tests were performed with the sample to determine the cause of its unusually high viscosity, Table 1.
The water and sediments content from the crude oil sample were determined to be 29.2 vol%, where 11% were solids. These solids include fine particles that could act as a mechanical stabilizer of oil droplets in crude oil emulsions. The fine solids were smaller than the emulsion droplets. They migrated to the oil/water interface and were wetted by both oil and water. The effectiveness of these fine particles on stabilizing the emulsion depends on factors, such as particle size, particle interactions and wettability of the particles. The production water showed the presence of chlorides in a concentration of 18,000 mg/L.
Characterization by microscopy. Optical microscopy was used to determine the presence of W/O emulsion in the California sample. As with most techniques, proper sampling was critical. The most common sampling is performed by deploying the sample droplet between an object slide and a cover slide. However, some form of sample cell may have optical advantages, for example capillary flat tubes. Inside a capillary, the sample will remain protected against evaporation, movement can be avoided, and the emulsion can be seen without altering the size and/or distribution of the internal phase.
Figure 2 shows two images of crude oil and the small water droplets in oil that range from 1 to 2 microns. Figure 2a shows a sample without dilution in a thin/flat glass capillary, with the ends of the capillary sealed to minimize sample movement within the capillary space. Figure 2b shows the microscopy image of the sample diluted with xylene. The typical information found in these images is droplet size, geometry and droplet size distribution. The water-in-oil droplets observed are very small and indicate that this is a difficult emulsion to break.
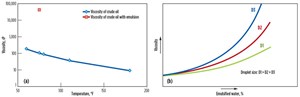
Viscosity evaluation. The viscosity of the neat crude oil sample (without emulsified water) measured at various temperatures is shown in Fig. 3a. The viscosity decreased with increased temperature, which is a typical behavior encountered in crude oils. The sample of the same crude oil, with 29.2% water and sediments, has much higher viscosity. The viscosity measured at 75°F increased from approximately 100 cP to 42,000 cP by having 29.2% internal phase. The plot shows that the apparent viscosity grew with a noticeable increase, as the amount of emulsified water approached the limit of a high-concentration internal phase.
The increase of the emulsified internal phase in the crude resulted in an increased viscosity. Figure 3b shows the typical behavior of the changes in relative viscosity with the increase of emulsified water and various values of average droplet size. A transition occurred, because the spherical drops reached the state of close packing, leading to changes in the rheological behavior of emulsions.
Such change in viscosity behavior is more significant when the average size of water droplets is very small. The droplet size influences the volume-to-surface area ratio, leading to a more pronounced viscosity increase with decreasing average droplet size.
Microemulsion fluid formulation. Compatibility of the solvent and co-solvent is important in deriving the microemulsion formulation. A solvent/co-solvent mixture that produced good miscibility with the crude oil was used to formulate the microemulsion to treat the oil sample. To design a robust microemulsion treatment fluid, a combination of ionic and nonionic surfactants, capable of efficiently microemulsifying the solvent/co-solvent oily phase, was used. Lipophilic and hydrophilic linkers were added to the system to make a stable microemulsion. The microemulsion formulation was based on Winsor phase behavior, where Winsor IV (single-phase microemulsion) is the desired behavior in which the fluid will have low interfacial tension and high oil solubilization, and produce coalescence of emulsified water droplets, and high oil production efficiency. Table 2 shows a generic formulation of the microemulsion fluid, formulated to treat the oil used in this study.
Successful microemulsions treatment for heavy crude emulsions requires ultra-low interfacial tension, and low inherent viscosity to effectively solubilize oil and mobilize crude with tightly bound water-in-oil emulsions. A fluid with these characteristics is capable of mobilizing W/O emulsions, viscous sludge and hydrocarbon deposits effectively without creating additional emulsification problems.
Dynamic interfacial tension. The dynamic interfacial tension (IFT) between crude oil and the microemulsion was evaluated, using a spinning drop tensiometer. In the tests performed with the crude oil described in Table 1, the interfacial tensions were measured until equilibrium was attained or until the drop of crude oil was solubilized completely by the microemulsion fluid. The oil was preheated at 80°C (176°F) and then injected into the microemulsion that was already in the capillary at the same temperature. As soon as the samples were in contact, the first measurement was performed. The initial interfacial tension measured between the two fluids was 1.0 mN/m. After a few minutes in contact, the interfacial tension between the liquids dropped dramatically, Fig. 4. After 20 min., the IFT decreased 80%, and at 100 min., the system reached 0.1 mN/m. After the 100-min. interval, the system turned very dark, making it impossible to record further measurements.
Sludge filter cake clean-up. A modified HPHT filtration test was performed to evaluate the effectiveness of the microemulsion to break and remove viscous crude sludge or viscous W/O emulsions. The sludge (mixture of viscous emulsion with solids) was made by mixing 75 vol% California crude with 25 vol% of water-based drilling fluid formulated with bentonite, poly-anionic cellulose, calcium carbonate and barite.
The cleaning test procedure began with the formation of a cake of the sludge in a 40-micron ceramic disk for 2 hr at 500 psi and 150°F. Then, the excess sludge was removed, leaving the induced cake in the ceramic disc. The next step was the addition of the microemulsion, and 100-psi differential pressure was applied to the cell. When the cell reached 150°F, the bottom stem of the HPHT cell was opened carefully, and the breakthrough time for the treatment fluid to pass through the sludge cake was recorded. It was established previously that the high viscosity of the oil used was due to tightly-emulsified water droplets.
Figure 5 shows the filtrate collected as a function of time. The very small droplets size of the W/O emulsion and high viscosity of the sample probably delayed the breakthrough time. The figure shows a moderate but exponential increase in filtrate collected over a 3-hr period. From previous studies, non-emulsified crude oils produce sludge that is relatively easy to break, and the total filtrate is collected in around 15% of the time that was required in the test described here.
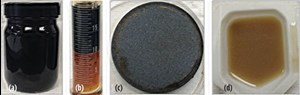
Figure 6a shows the filtrate that was collected during the sludge treatment with the microemulsion. The filtrate was a mixture of the California crude and the microemulsion fluid. Over time, the oil separated from the treatment fluid, due to the ultra-low interfacial tension, Fig. 6b. The residual solids on the disc were rinsed with fresh water. These were easily removable, leaving the disc completely clean (Fig. 6c), indicating that the microemulsion fluid effectively solubilized the crude oil and changed the wettability of the solids from oil-wet to water-wet. Evidence of the dispersion of the residual solids in water, and their water-wet condition, is shown in Fig. 6d.
MICROEMULSION SEPARATES WATER FROM HEAVY OIL
A novel, single-phase microemulsion, which used a non-aromatic solvent/co-solvent mixture as the oil phase, effectively treated the emulsified crude. The procedure successfully reduced interfacial tension and capillary forces breaking the water-in-crude oil emulsion, increasing mobility of the produced oil.
Viscosity measurements and microscopy techniques proved valuable to confirm the water-in-oil emulsion of crude oil.
Knowledge gained from laboratory tests and, microemulsions formulations can be used to systematically develop a custom solution, depending on well requirements and crude oil characteristics.
ACKNOWLEDGEMENT
This article is adapted from SPE paper 171140, presented at the SPE Heavy and Extra Heavy Oil Conference, held in Medellin, Colombia, Sept. 24-26, 2014.
- What's new in production (February 2024)
- U.S. operators reduce activity as crude prices plunge (February 2024)
- U.S. producing gas wells increase despite low prices (February 2024)
- U.S. oil and natural gas production hits record highs (February 2024)
- Dallas Fed: E&P activity essentially unchanged; optimism wanes as uncertainty jumps (January 2024)
- Enhancing preparedness: The critical role of well control system surveys (December 2023)
- Applying ultra-deep LWD resistivity technology successfully in a SAGD operation (May 2019)
- Adoption of wireless intelligent completions advances (May 2019)
- Majors double down as takeaway crunch eases (April 2019)
- What’s new in well logging and formation evaluation (April 2019)
- Qualification of a 20,000-psi subsea BOP: A collaborative approach (February 2019)
- ConocoPhillips’ Greg Leveille sees rapid trajectory of technical advancement continuing (February 2019)