Retooling for the upturn
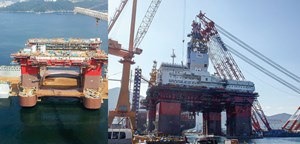
Last year, this report focused on a broad selection of newbuild rigs to illustrate innovations entering the market. The downturn has changed that perspective, as the entry of newbuilds has tapered off, and new orders and contracts have ground to a painfully slow pace. In this market, newbuilds tell a story, but an equally important narrative can be gleaned from the focus of technical papers, and the array of inventions being brought to the market by manufacturers and service companies.
A SMATTERING OF RIGS
Among the shrinking newbuild roster is a handful of Middle Eastern jackups and a semisubmersible working in UK waters.
In early May, Lamprell delivered the Butinah jackup drilling rig to Abu Dhabi’s National Drilling Company (NDC), Fig. 1. The rig, which will work in Zakum field offshore Abu Dhabi, is the sixth in a series of nine units. All nine rigs are Cameron LeTourneau Super 116E (Enhanced) Class designs. With the delivery of the Butinah, Lamprell has delivered 27 newbuild jackups, and its fourteenth Super 116E jackup drilling unit, to various clients during the last nine years.
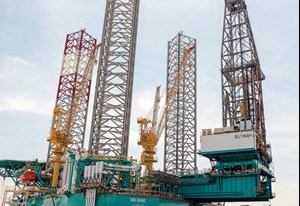
Ensco announced in May that it has a three-year contract with NDC for a new premium jackup, the ENSCO 110, Fig. 2. This newbuild rig was scheduled to commence operations offshore the United Arab Emirates (UAE). NDC also has contracted ENSCO 104 for a three-year term. The rig is mobilizing to the Middle East from the Asia-Pacific region. In addition to ENSCO 110, two more high-specification jackups, ENSCO 140 and ENSCO 141, are scheduled for delivery in 2016 from Lamprell’s shipyard in the UAE.
The ENSCO 110 is based on the Keppel FELS B Class Bigfoot design, which can work in water depths down to 400 ft with a maximum drilling depth of 30,000 ft. The rig has a nominal variable deck load of 7,500 kips and a cantilever load of 2,500 kips. It includes a 1.5-million-lb derrick, TDS-8 top drive and 4-ram 15,000-psi BOP. Ensco customized the rig to add dual drilling fluid capability, and upgraded the living quarters to accommodate 150 persons onboard.
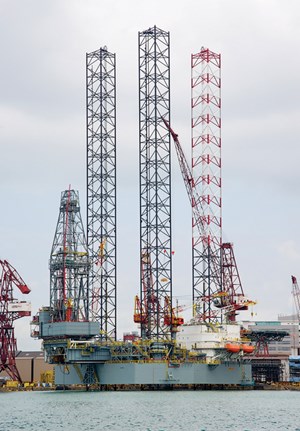
In April, Odfjell Drilling’s Deepsea Aberdeen semisubmersible (Fig. 3) commenced drilling operations under its seven-year contract with BP, on the Quad 204 field development project, West of Shetland, UK. The sixth-generation dual-derrick rig will initially drill two producer wells and one injector on Loyal field before moving onto Schielhallion field.
Delivered from the DSME yard in South Korea, during November 2014, the Deepsea Aberdeen is an enhanced GVA7500, harsh ultra-deepwater and harsh-environment unit like Odfjell’s previously delivered Deepsea Atlantic and Deepsea Stavanger. The unit is designed for operations in harsh environments and at water depths down to 3,000 m. It is equipped with a full, conventional mooring spread for operations in water depths of 70 to 500 m. The rig has a 7,500-mt loading capacity in all operating conditions. Its state-of-the-art, highly efficient drilling system includes a dual derrick with a main and an auxiliary work center to facilitate simultaneous operations. The drilling system has dual, active heave-compensating drawworks for increased performance, efficiency, safety and redundancy.
OTC TECHNOLOGY FOCUS
In the midst of the turmoil in offshore rig markets, the recent Offshore Technology Conference offered some valuable insights on where the industry is focused. The OTC session on Advances in Drilling Technologies presented four of seven papers that dealt with rig-related innovations in dual-gradient drilling, installing managed pressure drilling (MPD) systems on floaters, ultra-deepwater blowout prevention, and avoiding drilling-related non-productive time (NPT), such as stuck pipe.
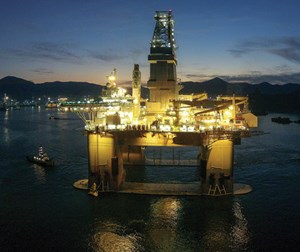
Authors of OTC paper 26056 (Statoil/Enhanced Drilling), “Analysis of field trial well control results with a dual-gradient drilling (DG) system,” presented results of controlled mud pressure (CMP) trials for well control on a rig equipped for DG drilling. The objective was to verify the CMP equipment’s ability to detect and controllably circulate out simulated influxes.
Among their findings was the system’s ability to quickly detect volume imbalances, due to abrupt changes in flowrate into the well. With the DG system, it also was possible to circulate out small gas kicks through the subsea pump module and dedicated well control equipment, when the annular preventer was closed.
A separate technical panel also discussed DG well control, and riser gas handling equipment and methods. For DG drilling, bringing a gas influx from well to surface is very important to well control procedures. The industry is addressing this through riser gas handling equipment, and the IADC’s development of riser gas standards. With risers often constituting a significant part of the wellbore, hydrocarbons in the return flow are often above bubble point pressure at the seabed, resulting in the need for safety measures to handle the gas that occurs in the riser.
While MPD techniques are cost-effective, reliable and safe, their implementation on deepwater wells has been constrained by “industry inertia and questions about reliability, barriers, riser gas management, and general riser interface issues,” say the authors of OTC paper 25946 (ABS/Weatherford/Berkeley & Imperial LP), “Lessons learned and safety considerations for installation and operation of a managed pressure drilling system on classed, floating drilling rigs.”
Their paper presents the review, integration assessment, engineering analysis, and process safety analysis, carried out prior to installing an MPD system on a classed, floating, mobile offshore drilling unit (MODU). In part, the paper addresses experience gained from MPD installations on deepwater rigs. The focus is on major categories of MPD equipment and methods, including installation and operation of a rotating control device (RCD) below the ocean’s surface, and integration with a riser gas handling device; flow and control line redundancy and fail-safe considerations for valving; and piping, umbilicals and hoses in the moon pool area.
Ultra-deepwater BOP operations present many challenges to understanding the system’s integrity and condition. An example, say the authors of OTC paper 25778 (Lloyds Register Energy – Drilling), “Fiber optic sensor-based monitoring system for blowout preventer,” is the difficulty of verifying pipe and shear ram closure during, and after, well control events. Fiber-optics sensor technology is being used to improve on the accuracy of manual volume measurements that are standard. In particular, fiber-optic strain gauges have evolved to a point, where a good representation of what is happening inside a BOP can be derived with sensors on the outside shell of the BOP. Monitoring these data, and watching for signal variation over time, helps assess degradation and failure. The paper presents ongoing work on a fully instrumented, 13½-in., 10,000-psi pipe ram with pressure transducers, accelerometers, flowmeters, and optical
strain gauges.
BOP technology also was cited by the OTC New Technology Committee’s Spotlight Award presentations, which recognized Cameron for its Mark VI High Availability (HA) BOP control system. The technology adds a third leg of control redundancy to the subsea control system’s point-of-distribution (POD) that increases the system’s operational availability. Adding a third POD further reduces the need to retrieve the stack, in the event of a POD failure. The company said the result could be as much as 98% system availability. Cameron tops off the achievement by doing it without increasing the size
of the stack.
Nonproductive drilling time, such as stuck pipe, lost circulation, pipe failure, fishing, and plug and sidetrack, was the focus of OTC paper 25838 (Petrobras/Baker Hughes Inc.), “Automated decision support and expert collaboration avoid stuck pipe, and improve drilling operations in offshore Brazil subsalt well.” The authors examine carnallite-related drilling difficulties, where the creep rate can be eight times greater than common halite, or rock salt. Because the NPT events typically recur over the field’s development, early identification of symptoms in real time can help the drilling team avoid potential incidents.

The paper illustrates a method of preventing drilling problems, before they occur, with a decision support tool that provides real-time, case-based reasoning and expert collaboration for enhanced risk assessment and hazard mitigation. The paper provides a case history, using the approach taken in the drilling of the pre-salt well and discusses the lessons learned during the process.
TOOLS OF THE TRADE
Offshore rig innovations being introduced to the market typically cover a broad spectrum of hardware, software and processes. Here’s a sampling of recent innovation in the news.
MPD. The deepwater rig fleet transition to MPD capabilities is advancing on technology and regulatory fronts. New classifications, expected this year from American Bureau of Shipping (ABS), will address the design, construction and commissioning of MPD systems, subsystems and components. ABS-classed rigs are affected, because the MPD system and subsystems are considered part of the primary well pressure barrier system.
Technology changes are moving the industry closer to a universal kit for MPD conversion aboard floating rigs. A highly adaptable, riser gas handling (RGH) system, developed by AFGlobal, is at the center of efforts to integrate key rig, riser and MPD systems, Fig. 4.
The RGH technology establishes the MPD prerequisite of a closed loop drilling (CLD) system by diverting annular flow, so that gas in the riser can be directed away safely from the rig floor. It also facilitates an MPD-ready rig by providing for easy addition of MPD riser components.
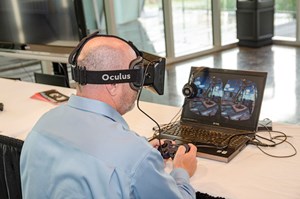
The component design of AFGlobal’s RGH system generally contributes to industry standardization by providing a common design point that accommodates the various rig and service company equipment. The technology is based on a specialized riser joint made up of several component units, including an MPD adapter. Adding the adapter to the RGH system allows a rotating control device to be fully integrated with the riser and control systems as a standard procedure.
Training. Imagine running casing in virtual reality. That’s what Frank’s International is doing with its training program. The casing and tubular service company is experimenting with training that recreates teachable situations on the rig. High on the “how cool is that” scale, are plans to use the Oculus Rift—a head-mounted display that has the gaming community buzzing about its anticipated release this year. The “fully immersive,” 3D virtual reality device is the creation of Oculus VR, which was bought by Facebook for $2 billion earlier this year, Fig. 5.
Training employees, by using video games and virtual reality experiences, is a more efficient way of learning, because it creates a more “hands-on” approach that sparks engagement in the classroom, according to Jacke West, training director at Frank’s International.
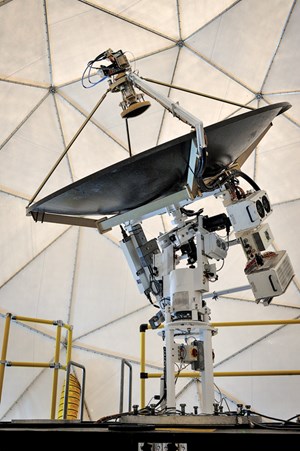
Frank’s training software is from the Louisiana Immersive Technologies Enterprise (LITE), a partnership between the Lafayette Economic Development Authority, the University of Louisiana at Lafayette, and Louisiana Economic Development. A long way from traditional PowerPoint presentations, the LITE programs engage employees with custom-made video games that teach them rig safety, rules and procedures.
Communications. Offshore operations place high demands on communications. Harris CapRock is opening up the channels with unified management of satellite, wireless and terrestrial connectivity service. The CapRock One system transparently switches between the various transport mediums to optimize communications, wherever a rig is stationed, Fig. 6.
A multi-band antenna allows for connectivity to C-, Ku- and Ka-bands, with no additional moving parts, so that any satellite orbiting the Earth can be accessed with no technician intervention. The system’s Intelligent Communications Director monitors the operator’s traffic and routes traffic intelligently over the most appropriate network path, based on speed, latency, location and cost.
Computers. The rig floor is not a computer-friendly environment. In addition to potential trauma to sensitive parts, caused by shock, vibration, heat, weather and “Bubba” (human error), they must also be certified for use in designated hazardous locations. Laversab’s Model 2850 Class 1, Division-2 / Zone-2 computer is designed to take it and dish it out. It functions from -40°C to +50°C, is impervious to salt-fog, is sealed to IP-65 standards, and can withstand vibration of 3G RMS. Small and light, it works on the rig floor and can be mounted on vehicles.
The computer features a dual-core Intel Atom processor and uses a solid-state drive for storage. And, you can read the screen, thanks to a 15-in. sunlight-readable display with auto-dimming, coupled with a low-reflection touch-screen. Communication I/O includes Ethernet, long-range 900-MHz wireless, dual USB ports and RS232 or 485 connections for serial interface. The device operates on 90-260 VAC or 9-36 VDC power.
- Coiled tubing drilling’s role in the energy transition (March 2024)
- Advancing offshore decarbonization through electrification of FPSOs (March 2024)
- Subsea technology- Corrosion monitoring: From failure to success (February 2024)
- Digital tool kit enhances real-time decision-making to improve drilling efficiency and performance (February 2024)
- E&P outside the U.S. maintains a disciplined pace (February 2024)
- U.S. operators reduce activity as crude prices plunge (February 2024)
- Applying ultra-deep LWD resistivity technology successfully in a SAGD operation (May 2019)
- Adoption of wireless intelligent completions advances (May 2019)
- Majors double down as takeaway crunch eases (April 2019)
- What’s new in well logging and formation evaluation (April 2019)
- Qualification of a 20,000-psi subsea BOP: A collaborative approach (February 2019)
- ConocoPhillips’ Greg Leveille sees rapid trajectory of technical advancement continuing (February 2019)