BY RYAN STRICKLIN, Chesapeake Energy; JEFF COBURN and SALLY CHARPIOT, Halliburton
The pursuit of hydrocarbons usually involves technologies that enable economical access and recovery of ever-more-challenging reservoirs. So, typically an article like this would discuss technologies that overcome challenging conditions such as extreme depths, temperatures, pressures and rock density. In the Barnett shale, however, where three decades of advancements have expanded the reservoir boundaries and extended drilling activity, there is a new twist for technology. Where urban growth and reservoir meet, it is imperative that the operational and technological solutions proactively address social responsibility and community interests.
Of the 25 counties that span the 5,000-sq-mi Barnett shale field, there is one county that stands out as the convergence between urban growth and reservoir potential: Tarrant County, home to Fort Worth, Arlington and the Dallas/Fort Worth international airport. As a result, while the Barnett shale served as the proving ground for shale development, it has now emerged as the proving ground for modern urban drilling.
As a major operator in the area, Chesapeake Energy is taking very seriously the opportunity to provide leadership in pioneering the new frontier of modern urban drilling. Chesapeake has striven to go beyond the safety regulations enforced by the Texas Railroad Commission and the quality of life issues regulated by the local municipalities. Chesapeake has been working with suppliers such as Halliburton to apply technologies that can help them exceed the regulated wellbore architecture requirements. In this arena, they are committed to communication, information availability, and remaining supportive of the social, economic and environmental wellbeing of more than 1.9 million people in Tarrant County.
DRILLING MOMENTUM
The first well was drilled in the Barnett in 1981, and at that time, the play straddled only Wise and Denton counties. By the end of the first decade, there were a few dozen wells drilled annually and the total number of producing wells was just approaching 100. After two decades, the number of producing wells edged up to nearly 1,300; and after three decades, the number of producing wells broke 15,000. Today, there are four core counties and an additional 21 non-core counties affected by the Barnett Shale play. In 2011, there were 2,023 drilling permits issued for the area, down from the peak of 4,145 in 2008 due to a decline in gas prices.
The first two decades were spent figuring out the puzzle of economically unlocking and recovering the hydrocarbon from the source rock. Drilling and production activity began to take off in the late 1990s when high-volume gel fracturing gave way to the success of water fracturing, significantly reducing completion operations costs. Then, just after the turn of the century, advancements in horizontal drilling, and eventually, efficiency in horizontal completions dramatically increased reservoir exposure, and thus, production results. This, in turn, led to pad drilling, helping make drilling in urban settings more manageable by reducing surface presence by as much as 90%. Chesapeake has had as many as 26 wells radiating off of a pad site near Fort Worth.
In remote locations, operations can be endless with trucks rolling on or off the rig site at any hour of the day or night. However, in an urban setting, although operations can continue around the clock, delivery of materials or personnel is limited to a 12-hr span. Trucks are only allowed to enter or leave the pad site between 7 a.m. and 7 p.m. This provides for a better sustainability of the routine ebb and flow for the community adjoining the drill site.
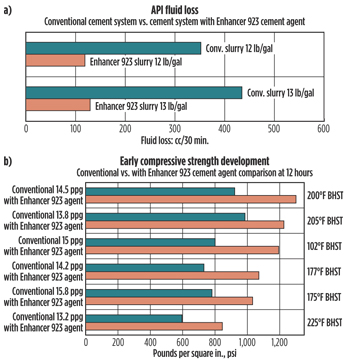 |
Fig. 1. When tested against equivalent conventional cement slurries, slurries blended with the Enhancer 923 agent dramatically reduced a) fluid loss and b) achieved compressive strength significantly earlier. |
|
SUSTAINABILITY
Chesapeake has teams of people dedicated to cooperative planning for environmental and community sustainability. These teams strive to keep open channels of communication in order to answer questions and understand concerns. The goal is to continuously find ways to adapt their projects in order to manage and even reduce the visual and sound impact—and to sustain water and air quality.
Since gas plays represent an increased probability for annular gas migration, Chesapeake sought to change the odds. Having always taken precautions to prevent gas migration from occurring with specialized equipment and continually monitoring pressure levels, Chesapeake worked with Halliburton cementing to find ways to enhance the integrity of the wellbore architecture. The challenge was to solve a problem before it becomes a problem: mitigate gas migration and control free water on the high side of extended-reach horizontal wells, while enhancing wellbore stability for fracture stimulation operations and production cycling.
Annular gas flow behind casing and liners can be experienced anywhere in the world. Experts agree that the cause of this is very complex and is likely to occur as hydrostatic pressure is no longer transferred from the slurry column to the formation during the initial hydration or transition period to a set cement sheath. In horizontal wells it can also occur if free-water in the slurry is not controlled and water is allowed to gather at the high side, possibly resulting in communication in the annulus.
FOCUS ON WELLBORE ARCHITECTURE
Wellbore architecture integrity is already an oil and gas industry imperative. In urban settings, being able to validate wellbore integrity helps to demonstrate a company’s dedication to supporting the community. Chesapeake was looking for a way to shorten the cementing set time once pumping stops to help mitigate influx from the formation.
In 2010, Halliburton introduced Chesapeake to Enhancer 923 agent as a component in cement designs for gas fields requiring enhanced slurry properties. The resulting slurry delivers significant performance improvements to the overall cement system. As needed, this agent delivers early compressive strength development by catalyzing crystalline growth during curing. Compliant with regulatory requirements, early onset of compressive strength helps prevent fluid influx from the formation before the cement has set.
These agent-blended slurries have allowed Chesapeake to lift the cement a long way without packing off and without lost circulation. The cement has been consistently brought to the surface, representing more than the 1,000 ft above the production zone required. The agent’s ability to increase fluid stability has decreased the need for remediation due to cement fallback that can occur after top of cement is achieved (cement fallback is caused by slurry loss to weak formations or depleted zones shortening the height of annular cement).
One of the benefits realized by Chesapeake is the increased efficiency on the pad sites by avoiding remediation. The average lateral for Chesapeake in the Barnett is 4,000 ft. Using a slurry with the mechanical ability to lock away water in a manner that reduces API fluid loss has helped eliminate possible communication along the high side of these wellbores. Fluid stability has also helped prevent slurry-bridging across thief zones and helped avoid filtrate loss to the producing zones or fresh water aquifers—even while maintaining constant hydrostatic pressure.
Additionally, this cementing system provides lower rheologies as compared to conventional slurries. This helps increase displacement efficiency through higher placement pumping rates while reducing frictional pressures and ECD (equivalent circulating density), once again helping facilitate complete cement coverage for wellbore integrity.
The goal of the drilling engineer is to give the completions engineer the best possible wellbore architecture. An optimally designed cement sheath contributes to successful fracture placement. An optimized cement sheath can mitigate damage to the formation, resiliently maintaining isolation throughout the high pressures of hydraulic fracturing and the drawdown during production.
FUTURE OF WELL CEMENTING
With pad drilling occurring in the shadows of a multi-billion-dollar sports stadium, parking lots of movie theater complexes, and one golf stroke from a tee box, the Barnett shale is unlike other shale plays under development. The vigilance of oil and gas companies to help preserve the wellbeing of the community can be seen in the use of sound walls, emissions monitoring, pad-site vehicle curfews, and the integrity of the wellbore architecture. In tackling the emerging challenge of urban drilling, the cementing operation is not a one-time event. It serves as a foundation for the economics of the oil and gas company, and more importantly, as the safeguard to help protect community continuity and growth. 
The author
RYAN STRICKLIN is a drilling engineer working in the Barnett Shale for Chesapeake Energy. Chesapeake is currently operating six rigs in the Barnett, each drilling an average of two wells a month. JEFF COBURN is Halliburton’s cementing manager for their northern regions. He is responsible for Halliburton’s cementing operations throughout Canada, California, and the mid-continent of North America. SALLY CHARPIOT is Halliburton’s marketing and business analysis manager for the Cementing product service line. She is responsible for helping to commercialize cementing solutions and casing equipment. |
|