Cummins Inc.’s new QSK95 engine will be configured as a ready-to-install offshore drilling power module (ODPM) with 2.1-megawatt (MW) output. The 95-liter 16-cylinder engine is the world’s most powerful high-speed diesel, according to the company. The engine is rated at 3,000 hp (2125 kWe) at 1,200 rpm to align with a standard output node used for moored semisubmersible drilling rigs, jackup rigs, drillships, and floating and gravity-based production platforms. Other large high-speed diesels require 20 cylinders to achieve the same output, the company said. Additionally, compared with medium-speed engines, the QSK95 reduces the space envelope by up to 40%, with approximately 33% less weight.
The QSK95 Modular Common-Rail System (MCRS), with up to 2,200-bar high-pressure fuel injection, results in smoother, quieter and more fuel-efficient operations. For critical emergency power, the unit ramps up in seconds to provide power without interrupting operations due to the faster transient response provided by four compact turbochargers with the simplicity of single-stage air-handling.
The power module will be available in a cost-effective, standardized base package, or with the option of customizing the unit to meet specific installation needs. The control system comes with a full suite of operational data, multilingual touch screens and safety protection features, providing easy interface with the rig’s local network with remote monitoring available. It will join the QSK60 Offshore-Drilling Power Module with 1.3-MW prime power output, recently introduced by Cummins. The two drilling-module engines share the same fuel system, turbocharging and electronic control systems to offer the benefit of installation and service commonality.
The engine will offer a major advantage when it comes to meeting EPA Tier 4 and IMO very low-emissions marine regulations. By utilizing the company’s Selective Catalytic Reduction (SCR) aftertreatment system to replace the exhaust muffler, the module retains an almost identical envelope. Using SCR requires no change to the cooling or ventilation requirements of the power module in order to meet emissions levels. While achieving Tier 4 low-emissions, the SCR system is capable of achieving fuel savings of 5–10%, lowering the overall cost of operation by more than the cost of Diesel Exhaust Fluid (DEF) required for SCR, the company said. The fuel savings are incremental to that of the QSK95 meeting Tier 2 emissions without after-treatment, according to the company.
Service intervals are a minimum of 500 hours, with the option of much-extended oil-change intervals available by using the Eliminator oil purification system, which is mounted on the engine. The goal of a leak-free engine is achieved by premium “press-in-place” seals on all critical joints, such as flywheel housing, gear housing and oil pan-to-cylinder block. 
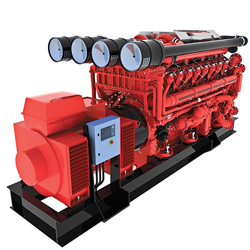 |
Cummin’s new 95-liter, 16-cylinder engine, rated 3,000-hp (2125 kWe) at 1,200 rpm, is the world’s most powerful high-speed diesel, according to the company. |
|
Upgraded hydraulic roughneck
Aker Solutions’ recently developed tri-grip torque wrench is available with the 1898/1899 roughneck system. The new design incorporates the efficiency and handling capabilities of the original MH torque wrench into a new higher performance tong.
The tri-grip tong features up to about 140,000 ft-lb torque capacity and 60° rotation. Slipping problems are reduced or eliminated as a result of the increased grip area.
The wrench’s configuration secures 40% higher torque capacity compared to a two-grip tong with equivalent clamp force, according to the company. The clamp force can be reduced for corresponding torque setting, resulting in less wear on tool joints and reduced risk of radial deformation of the box end. Rotational force is applied through chains, securing an optimal radial bearing around the rotating tong’s circumference.
The new tong utilizes the same framework and rails as the MH 1898/1899 machines, and is suitable for installation on rigs where a MH roughneck is currently installed. Because a minimum of new instrumentation has been incorporated into the upgraded iron roughneck, a new machine can be installed in existing MH roughneck interface.
The tong also incorporates a new jaw design for improved safety and efficiency. Worn-out dies are easily removed by disengaging a socket cap bolt, eliminating need for hammer and chisel, and reducing the time required to change dies as well as less time spent in the “red zone” on rig floor. 
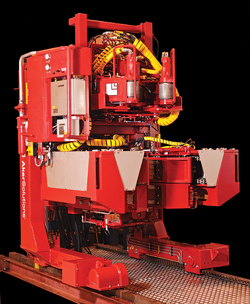 |
The tri-grip tong features up to about 140,000 ft-lb torque capacity and 60° rotation. |
|
Tong cassettes for casing running
Traditionally, casing companies provide tongs that are hung on lines, and are manually swung on and off the pipe. Mechanized tong manipulating systems were a big improvement over manual movement of the power tong but required a lot of space, often installed in front of or alongside the existing rig roughneck. In addition, most installations require separate power units to be provided and rigged up with the tongs. It made sense for traditional roughneck manufacturers to provide modular systems for which third-party casing running companies could interface casing/tubing tongs.
The roughneck carriage (transport frame) usually has a drill pipe module (tool frame) installed to make-up/break-out the drill pipe joints. Although the roughneck manufacturer can provide casing tong modules, which would allow drilling contractor personnel to handle all aspects of tubular handling in addition to drill pipe, the operator usually hires tubular running companies to deal with casing and completion tubulars. This is due to the numerous specialized requirements associated with power tongs, and the tubular running company’s expertise in achieving proper make-up of these threaded connections.
Frank’s Casing Crew & Rental Tools’ RTS-H product line consists of tong cassettes that interface with increasingly commonplace modular iron roughneck systems being employed by most offshore rig contractors. The RTS-H is capable of making up and breaking out a large range of pipe sizes. The company currently can provide two different tong cassette sizes, a 75/8-in. casing and tubing tong cassette, which can accommodate tubular sizes ranging from 4-in. to 75/8-in. diameter with torques up to 30,000 ft-lb, and a 143/8-in. cassette that can accommodate 7-in. to 143/8-in. tubulars with torque up to 70,000 ft-lb. The larger cassette includes features to quickly adjust the spacing between the power tong and the integral backup tong, allowing casing or riser running modes.
These tongs can be supplemented with the company’s proprietary Fluid Grip head to eliminate die marking on CRA completion tubulars. Their Data Trek Computerized Torque Turn systems are available for all of its tong cassettes, including optional servo-valves for more stringent connection makeup requirements. The company can also provide its own carriage that can run on the rig rails or rails provided by the company in cases where the rig’s Iron Roughneck is not of a modular design.
To use the tong cassette, the cassette frame hooks and latches into place onto the roughneck carriage, the hydraulic connections are made up, and the pneumatic umbilical is connected. The entire switch-out operation can typically be completed in 30 minutes. Once the carriage and cassette have been mated, they can be driven to and from the well center remotely from the driller’s control station or a wireless pendant. The tong operator controls all the tong and cassette functions from his separate remote control console. This control scheme maintains the rig’s ESD (Emergency Shut Down) and ZMS (Zone Management Systems) to prevent collisions with other automated rig systems. 
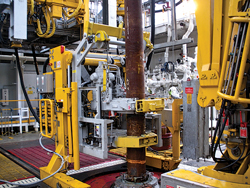 |
Frank’s RTS-H tong cassette is available in two tong cassette sizes, a 75/8-in. casing and tubing tong cassette, and a 143/8-in. cassette. |
|
Automatic pipe loader
Atlas Copco has developed an Automatic Pipe Loader (APL) system for its RD20 mobile rotary drill rig that does not require any hands to touch the pipe from the time it arrives at the site and is loaded onto a rack system to the point it’s added or removed from the drill string.
The APL system can be used with standard RD20 pipe, as well as other types of oilfield or external upset pipe ranging from 3½-in. to 133/8-in.-OD casing. It is designed to work with any RD20 Range 3 model, and in some cases with earlier Range 2 models.
The APL is a stand-alone system and features its own hydraulic power unit that operates at a maximum capacity of 64 gpm at 3,000 psi. The pipe loader does not draw on the hydraulic power of the RD20 to avoid compromising its drilling performance. The APL is operated by the assistant driller standing off to the side of the platform, just over the driller’s shoulder. He controls the functions with a wireless remote control unit that can rest on a stand or be carried with a shoulder harness. The APL handles drill pipe, collars and casing. Hydraulic slips allow pipes to fall, one at a time, into the cradle of the pipe-loading arm. Clamps are engaged and the loading arm is raised into position under the rotary head. Additional safety is built into the clamping system, which cannot disengage if the pipe is raised above 15°. The operator and pipe handler must be in communication, as the pipe can only be released when the driller releases it.
A stand-alone camera system may be installed at the top of the tower so the driller can see when the pipe is properly threaded into the top drive. This saves the driller’s neck from straining to see the operation from the working floor. The camera also ensures proper connectivity before the clamps are released from the loading arm.
Pressure gauges allow the operator to torque the pipe to the correct pressure. The 35,000-lb (15.8 metric tons) APL system is transported as an oilfield skid. It can handle Range 2 drill pipe and Range 3 casing up to 45 ft (14 m) and a tubular weight range up to 6,000 lb, or 8-in. collar at 160 lb (72 kg) per ft. The APL system is adaptable for drilling off the ground or when sitting on top of a 10-ft (3-m) substructure. The first prototype was shipped to Australia for testing last year, with primary testing completed in 2011. Regular production versions of the APL are now available for order. 
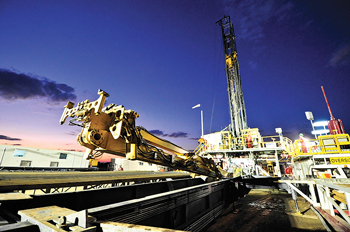 |
The Automatic Pipe Loader (APL) system can be used with standard RD20 pipe, as well as other types of oilfield or external upset pipe ranging from 3½-in. to 133/8-in. OD casing. The APL system can handle Range 2 drill pipe and Range 3 casing up to 45 ft and a tubular weight range up to 6,000 lbs. |
|
36-in. Jet String Elevator
Frank’s has developed an industry first with the 36-in. Jet String Elevator, a slip type elevator capable of lifting a 200-ton string of casing without the use of padeyes, load rings or lift subs attached to the pipe. The tool can lift a joint of casing from the vertical or horizontal position with either bails or slings attached to the elevator, making running the 36-in. jet string safer and more efficient.
Development of the elevator was driven from the technical challenges behind the running of 36-in. flush OD casing. The ability of this tool to lift casing from the horizontal to the vertical position and run the entire string of casing removes the need for multiple tools and leads to a safer and more efficient operation. This flush OD is important during the jetting operations due to the time and equipment needed to remove welded or bolted padeyes and the risk of damage and safety concerns that are inherent during this process.
The 36-in. Jet String Elevator was utilized in Beaumont, Texas during the recent running and pulling of 36-in. casing. The elevator was run in hole with eight joints of casing until hole conditions dictated pulling and then running a smaller string of casing. The initial running and subsequent pulling of the casing was completed without incident and in a safe and controlled manner.
The Jet String Elevator is designed to be fully automatic, utilizing hydraulics to control the tool’s latches and cylinders, allowing for a more hands-free running operation. The elevator is also equipped with the company’s patented “Interlock System,” a work environment safety improvement that prevents the elevator and spider from releasing casing pipe simultaneously while making-up pipe or during running operations. 
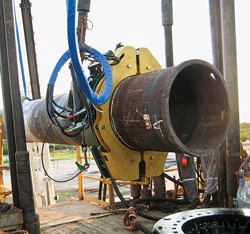 |
Frank’s developed its 36-in. Jet String Elevator, a slip type elevator capable of lifting a 200-ton string of casing without the use of padeyes, load rings or lift subs attached to the pipe. |
|
Below Tension Ring Rotating Control Device
Weatherford’s patented Model 7875 Below Tension Ring (BTR) Rotating Control Device (RCD) is a pressure-control solution for annulus gas diversion and drilling operations. It is the industry’s first RCD to be integrated with the riser below the water-line, and the first to conform to API 16RCD drill-through specifications. When mounted below the tension ring on a floating rig, the RCD creates a positive seal around the rotating drillpipe and tool joints to positively divert annulus returns. It can also divert mud and cuttings through a dedicated choke manifold, enabling use of managed pressure drilling (MPD). This particular RCD was purpose-built for applications in the deepwater environment and includes numerous features that are necessary for below-tension-ring deployment. For example, it is designed to take typical tensile loads seen in 21¼-in. riser systems. The tool body enables deployment through most rotary tables. The bearing assembly is deployable through standard riser systems and is designed to accommodate 65/8-in. drill strings and associated collars with hard banding. The RCD enables rapid transitioning from MPD to conventional drilling, and vice versa.
The 7875 BTR RCD is part of the company’s SeaShield RCD series and is based on the Model 7000 series dual-element RCDs. Its below tension ring location requires no modifications to the rig’s existing telescoping slip joint and mud returns system in the moon pool area. The RCD is configured below the tension ring as an integral component of the riser. When the self-lubricating bearing and annular seals assembly is latched into the body, annulus returns are stripped from the drill string and positively diverted to a dedicated choke manifold and other rig equipment through flexible flow lines that also serve to compensate for rig heave movement.
The bearing-and-sealing element assembly hydraulically latches inside the bowl, improving safety by eliminating the need for personnel to loosen and tighten the clamping mechanism from beneath the rig floor. The bearing assembly running tool, its control console and stabbing stand facilitate installation and improve safety by enabling positioning and removal of the bearing and sealing element assembly.
The RCD can accommodate large-diameter drill strings. It also can accommodate drilling with casing operations with 7-in. and smaller casing. The top flange design makes it possible for the RCD to become an integral part of the riser system, thereby forming a closed-loop system that provides enhanced pressure control. The flange design also accounts for tension in the riser string, enabling the RCD installation to take place without affecting non-drilling activities.
Typical applications for the RCD include MPD on complex deepwater wells, including HTHP and extended reach wells; offshore drilling that presents the risk of two-phase flow; MPD, air drilling and underbalanced operations; and drilling in shallow-gas formations.
The Model 7875 BTR RCD was recently installed on a deepwater well offshore Indonesia so the operator could fully enclose the well bore and all drilling fluids in a closed loop and employ advanced drilling techniques without compromising the rig’s heave compensation. 
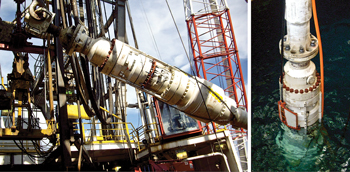 |
Weatherford’s Model 7875 Below Tension Ring (BTR) Rotating Control Device (RCD) pressure-control solution for annulus gas diversion and drilling operations is the industry’s first RCD to be integrated with the riser below the water line, and the first to conform to API 16RCD drill-through specifications. |
|
Mitigating stick-slip in real time
Stick-slip occurs to varying degrees in every well. It is the inability of the driller to properly identify stick-slip that leads many to believe that they are not experiencing it. Even minor stick-slip can lead to significant reduction in drilling performance. Traditional instrumentation systems only provide torque and Rpm readings once or twice per second (1 Hz to 0.5 Hz). Canrig Drilling Technology’s REVit allows the driller to read these values, calculate stick-slip severity 500 times per second (200 Hz) and instantly identify if stick-slip is occurring. The software’s automatic, instantaneous response to torque anomalies helps provide a more steady-state operation that is easier to analyze and improve.
REVit is a proven implementation of Shell’s Soft Torque technology that has been in development for over 20 years. Systems are currently running in most major shale plays in the US, Canada, Algeria and Saudi Arabia. Its use regularly increases rate of penetration (ROP) by 40–70% and significantly reduces bit wear, according to the company.
The program works by dampening torsional oscillation in the drill string. Technicians are trained to provide the driller with tuning that matches the equivalent spring and mass system of the top drive-and-drill string configuration. They also provide the operator with regular reports to ensure that the system is being used optimally for a maximum return on investment.
The system is primarily an upgrade to the Canrig AC top drive controls and is independent of other rig controls. The rig can run normally with or without the system being operational. The software can be turned on or off with a single button and has built-in safety features to prevent the driller from using it improperly. It requires minimal input from the driller; all required input is provided by Canrig’s RIGLINE 24/7 call center. The company’s technicians are trained in drill string design and are supervised by drilling engineers as they continuously monitor the performance of the rig to help the driller optimize the system. The technicians also can provide training or troubleshooting. 
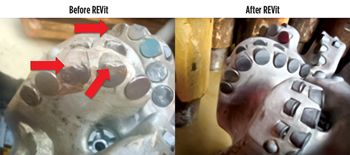 |
Canrig Drilling Technology’s REVit has been shown to significantly increase ROP and reduce bit wear. |
|
Mud pump pressure relief valve (PRV)
Expro’s patent-pending PRV Max upgrade includes a compact Hydraulic Pressure Unit (HPU) and remotely operated touch screen PLC control panel. Individual HPUs for each PRV allows each valve and HPU to operate autonomously. The system protects positive-displacement mud pumps from excessive pressures, increases relief pressure accuracy, repeatability and allows reset to occur in a time-efficient and cost-effective manner.
The upgrade offers several design improvements including a small footprint HPU that can be mounted on top of the valve to reduce space requirements for the system. The control panel footprint has also been reduced to just under 24 sq in., and the control is now HMI based. The time for the valve to fully open is less than 375 msec after mud pressure reaches the set point. Each HPU pressure is displayed on HMI with low-pressure alarm. Metal-to-metal sealing provides extended service life between maintenance periods. During tests witnessed by DNV, the PRV performed 250 trip cycles without the need for redressing, the company said. The PRV is ATEX-certified for hazardous areas–the PRV and HPU are Zone 1 certified and the control panel is Zone 2 certified. In addition, Expro Valve is DNV and ABS type approved.
Optional benefits include data logging for each trip cycle event (recording pressure buildup, time and trip set pressures), and a screen prompt informing the operator when it is time for routine maintenance and service work based on the number PRV trip cycles. Other options include rig air presure monitoring, audible/visual alarm, and communication with customer PLC.
The PRV Max is constructed using non-interacting mechanical components, meaning that a single point of failure will not spread to other valves. The valve is virtually maintenance free, according to the company. Tungsten carbide sealing components provide high erosion resistance and extended trim life without the use of elastomeric components, extending service life between maintenance periods. 
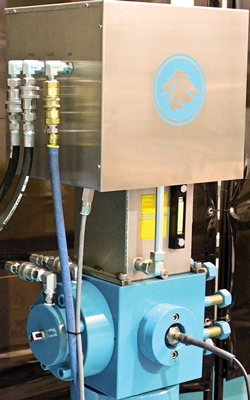 |
Expro’s PRV Max upgrade includes a compact Hydraulic Pressure Unit (HPU) and remotely operated touch screen PLC control panel. Individual HPUs for each PRV allows each valve and HPU to operate autonomously. |
|
Quadraplex pump technology
White Star Pump has developed the industry’s first commercially viable quadraplex mud pump, the Quatro, which is available in nine models ranging from 750 hp to 2,450 hp. Each offers a number of features including a 1,597 gpm flow rate for models 1,000 hp and greater, with higher flow rates for low-pressure applications. All Quatro models are rated at 7,500 psi.
The pump’s design results in significantly lighter weight compared with conventional triplex pumps, as much as 25–35% less, important for installation aboard offshore rigs. The compact size, only 82-in. wide, reduces pump room space requirements in an offshore rig by almost 50%, and ensures that they can be transported by a standard trailer.
The quadraplex pump’s design symmetry is the result of employing one suction desurger and pulsation dampener per pair of cylinders, which provides for near-perfect fluid balance. This naturally stable power and fluid balance, in turn, delivers a near-zero-discharge pulse, providing smooth fluid flow. The quadraplex design balances the pump, with the fourth cylinder serving to improve crankshaft timing, enabling a smoother running pump with less vibration. Additionally, the compact frame is designed to efficiently carry load forces directly to the double roller bearing, while the bearing placement between cylinders reduces load and flexing of the frame and crankshaft. All combine to deliver improved bearing, crankshaft and gear life.
The pump features a fully machined and assembled crankshaft, which compares favorably with other mud pump designs that utilize casting or welded construction. The design also incorporates the shortest distance between each cylinder and bearing of any mud pump, virtually eliminating crankshaft flex, according to the company.
The quadraplex pump’s fluid modules can be replaced in the field in about 45 minutes by removing six bolts, the company said. The modules’ quick replacement is a result of the pump’s seal assembly design and a module mounting system in which the modules are housed inside the pump frame.
The company also offers a proprietary real-time pump-monitoring system that closely monitors all aspects of the quadraplex pump’s system via data-acquisition sensors and can alert the operator of any problems locally and remotely. The data-acquisition sensors can detect deviations from normal operating conditions before they are perceived, resulting in a larger window for preventing critical failures. Sensing whether the top or bottom valve in a particular cylinder is starting to leak or stick with 100% accuracy, the pump system monitor will reduce guesswork and downtime. 
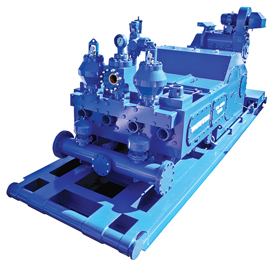 |
White Star Pump’s Quatro, the industry’s first commercially viable quadraplex mud pump, offers a number of features including a 1,597-gpm flowrate for models 1,000 hp and greater, with higher flowrates for low-pressure applications. |
|
New top drive drilling system
Drawing from its experience as a top drive maintenance, repair, and rebuild/ recertification company, Global Drilling Support (GDS) has designed, manufactured and built a top drive engineered from the ground-up to effectively address critical downtime and longevity issues. The GDM (Global Drilling Machine) 850 Top Drive was introduced on Nov 3, 2011.
The top drive incorporates a robust mechanical design that minimizes failure points, while delivering outstanding torque and high-rpm performance. The design provides easy access to maintenance areas and built-in work platforms to increase the safety and productivity of rig personnel.
Manufactured under an API 8C License, the top drive system offers a number of key features. It uses a GE motor and a unique self-aligning coupling that can add to motor life. The top drive also features a solid drive pinion, which is supported from the top and the bottom for increased reliability. A helical gear assembly contributes to the unit’s higher torque capabilities, longer life and quieter operation, while forced-spray lubrication ensures consistent lubrication of all key parts of the top drive. The system’s submerged thrust bearings extend the top drive’s operational life and reliability by two to three times, according to the company.
The top drive also includes a state-of-the-art control system with a comprehensive maintenance module that provides for a proactive approach to servicing the unit, adding to its reliability and long life. The control system automatically recognizes pipe position relative to the mast, ensuring a higher level of personnel safety. The unit’s advanced pipe handling system adds significantly to the speed and productivity of drilling operations.
Previously proven as an aftermarket component on a wide range of top drive models, the company’s proprietary remote IBOP actuator is a key element of the top drive, offering a number of features not found on conventional IBOP actuators, including opening and closing actuation while in rotation. The IBOP actuator also provides for manual operation through actuation cams, eliminating the need for rotating seals. The actuator incorporates a compact design with fewer moving parts and easy field installation with independent mounting to the valve body.
The 850-ton top drive system operates at 1,570 continuous HP and delivers 64,000 ft-lb of continuous torque at 0-116 rpm up to a maximum 250 rpm and 88,000 lb of intermittent torque. Static brake capacity is rated at 60,000 lb, while pipe-handling capacity is at 110,000 ft-lb The 850 delivers 7,500-psi mud flow through a 4-in. passage. The unit weighs less than 35,000 lb and is 23 ft tall with 120-in. elevator links.
In addition to the new GDM 850, Global Drilling Support is developing additional top drive models from 250 to 500 short tons. 
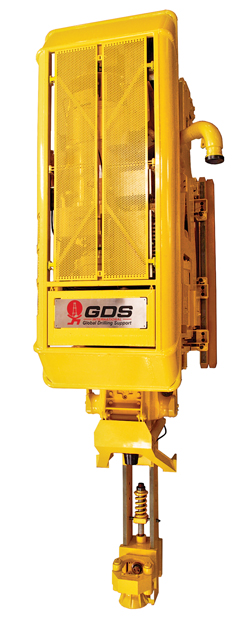 |
Global Drilling Support 850 ton top drive system operates at 1,570 continuous HP and delivers 64,000 ft. lb of continuous torque at 0-116 rpm up to a maximum 250 Rpm and 88,000 lb of intermittent torque. |
|
New iron roughneck
Forum Energy Technologies has launched its new Wrangler Roughneck 120 (WR 120), a completely new design rather than a tweaking or enhancement of existing designs. The pedestal-mounted tool with a hydraulically actuated slewing motor is mechanically deployed and is capable of reaching the well center and the mousehole with its 144-in. reach.
Three newly designed WR 120 units have been installed on jackups over the last couple of months, in addition to one on a land rig.
The new design provides a counter balance thread compensation system with 4 in. of travel while spinning in or out of a connection. The tool can make-and-break bottomhole assemblies (BHA) and the spinner can scope vertically to spin in stabilizers up to 17½ in.
An optional bit-breaker kit is also available. The tool also features a three-jaw clamping system, which minimizes the potential to deform the box, providing much higher accuracy in torque application while minimizing the potential to gall threads.
The roughneck provides 100,000 ft-lb of makeup torque and 120,000 ft-lb of break-out torque with 90° of torque wrench rotation. It can handle 3½–10-in.-OD pipe. No manual tongs are required for drill pipe, drill collars and BHA up to 10 in.
The tool was designed to provide maximum efficiency in running premium connections and extended-length threaded tool joints. Electric controls provide additional installation options. Other features include a dual-spin speed spinner, spinning wrench counter balance for thread compensation, a soft clamp, 90° torque rotation, and three-cylinder torque wrench, in a smaller footprint than other 120,000 ft-lb tools. 
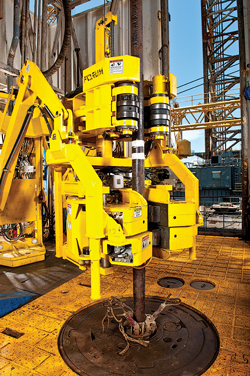 |
Forum Energy Technologies’ Wrangler Roughneck 120 (WR 120) features a three-jaw clamping system, which minimizes the potential to deform the box while providing much higher accuracy in torque application and minimizing the potential to gall threads. |
|
BOP handling systems
J.D. Neuhaus offers equipment that already meets the upcoming regulations to lower a load safely even with an emergency power loss. These regulations are already in place in Norway and will likely soon be adopted in the US On offshore rigs, they are often installed and maintained in place for long periods of time. On older rigs, including those built in the last five years, many of these hoists may not meet the latest safety codes without replacement, the company said.
The company’s hoists are offered with pneumatic or hydraulic operation for the lifting, lowering and traverse operations of BOPs. The handling systems are weather-and corrosion-resistant and are suited for installation in hazardous or other potentially explosive environments.
The handeling system can be provided with joint lifting capacities from 20 to 200 tons. The ultra-low monorail hoist offers a combined lifting capacity from 8 to 200 tons.
Delta Rigging & Tools is the certified service company in the US capable of installing, inspecting, servicing and certifying J.D. Neuhaus BOP handling systems. The company has developed and can install or can modify existing overhead air supply systems to eliminate sagging and tangling of supply tubes typical in standard installations. The company offers a coiled-hose air supply system to deliver compressed air from a fixed joint on one end of the BOP hoist monorail through a spiraling coil-type self-storing hose to the hoist.
The monorail BOP handling system is deployed with matching air or hydraulic chain hoists working in parallel. The system also has the option of using a positive rack-and-pinion trolley drive, a custom designed clevis attachment to replace the load hooks, hydraulic operation and longer lifts. Air hoists are operated with only 85 psi of pressure, and all load carrying parts have a safety factor of five to one.
Other features include explosion-resistant certifications, a trolley anti-drop and anti-climb system, full emergency stop system, overload protection, and additional customer or application specific options.
Other features include an efficient high-performance vane motor; Delta P overload protection; all-steel construction; built-in chain containers; all-brass-push button control valve; corrosion-resistant coating system; stainless steel fasteners; and 30 ft of lift. 
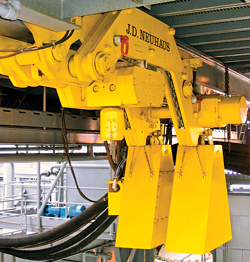 |
J.D. Neuhaus’ monorail BOP handling system is deployed with matching air or hydraulic chain hoists working in parallel. The system also has the option of using a positive rack-and-pinion trolley drive, a custom designed clevis attachment to replace the load hooks, hydraulic operation and longer lifts. |
|
Bottomhole assembly tool
In these days of rig automation and advanced rig mechanization, the industry may wonder why running the Bottomhole Assembly (BHA) still requires more people on the drill floor and more equipment than when tripping in or out. BHA are made up of many different components, each usually having their own specific outside diameter, meaning that for every component, a specific set of hand slips is needed. Furthermore, every component needs to be secured by a safety clamp to prevent unwanted pipe slippage. Setting the slips and fixing the safety clamp are manual processes, which often require two to three persons to complete. It is a potentially unsafe practice, and it is imperative to find a good solution to meet this challenge. National Oilwell Varco (NOV) developed a bottomhole assembly tool (BHAT) that provides a solution to the main challenges faced when handling the BHA, the many different diameters, and running collarless components with relative low loads.
The two design features of the BHAT are that it is a slipless tool that can handle a range of pipe without size component changes. With the common way to support axial weight of a string, the industry has relied on the tapered slip design in combination with tapered bowls. This solution has proven to be safe; the more string weight, the more gripping force a slip has. However, when running relatively light string weights such as when making up a BHA, the gripping power of the slip design is limited, resulting in pipe slipping through the slips. This could result in dramatic consequences when running collarless tubular. To counter this phenomenon, a safety clamp is fixed just above the slip, forcing it further down in the bowl to better grip the pipe should the pipe start to slip.
Holding actual load on pure friction results in a very limited amount of gripping force, depending on parameters including contact materials, initial clamping power, surface roughness and the presence of mud or grease between the two gripping areas. During BHAT’s design, it became apparent that a slip is not needed to hold high axial loads; what really holds axial weight is the combined shear area of all the individual insert teeth penetrated into the pipe. The deeper the teeth have penetrated, the more axial holding power is generated, providing a more predictable mode of operation. The maximum holding force is dependent on the amount of inserts used, the teeth profile, the hardness of the teeth and the pipe, and the initial clamping force to provide sufficient insert teeth penetration. 
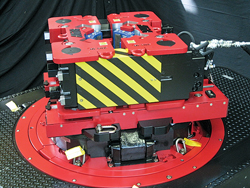 |
National Oilwell Varco's bottomhole assembly tool is a slipless tool that can handle a range of pipe without size component changes. |
|
|