In GOM’s deepest productive well, the operator optimized underreaming-while-drilling operation using FEA.
M. Frenzel, Smith Technologies; and Bobbie Jo Kull, Chevron
Deepwater exploration in the Gulf of Mexico presents a number of unique challenges to drilling technology. In the Walker Ridge area, Chevron is developing the Big Foot prospect (Block 29) and the high-profile Jack discovery (Block 758), which drilled to a record setting 28,175 ft and is the deepest productive test well in the GOM to date. Because of the extreme depth in these wells, the initial hole size must be relatively large to provide adequate clearance inside the final casing string for a successful completion. Drilling a large diameter hole is not particularly difficult; however, there is a unique set of issues that need to be addressed in the planning stage to ensure proper and efficient well construction.
INTRODUCTION
One of the most successful methods to minimize costs and address the challenges is underreaming while drilling. During this process, a pilot hole of a smaller diameter precedes an underreaming/hole opening tool placed above it in the Bottomhole Assembly (BHA). At the appropriate depth, a surface command activates the underreamer tool to drill a larger diameter wellbore than the ID of the previous casing string.
Using reamers in combination with downhole motors and/or rotary steerable tools presents another set of issues. Generally, the reamer must be reliable and strong enough to withstand the added weight of the directional BHA component (rotary steerable system/motor), which is hung below, and still deliver a quality wellbore at maximum ROP.1,2 These issues led the operator to contact Smith Technologies to help optimize the BHA design, including reamer placement and the proper PDC bit selection, to avoid a costly and time-consuming trial-and-error process to maximize performance.
To accomplish the task, the service company used a proprietary suite of simulation software to model drillstring behavior and BHA configuration. The patented modeling process provided an in-depth understanding of the complex downhole behavior critical in increasing directional-drilling efficiency.
PERFORMANCE OBJECTIVES
When drilling homogeneous formations, the bit and reamer’s cutting structures generally function well enough together to drill and underream the wellbore at an acceptable/economic ROP while avoiding damaging harmonic vibrations. However, in applications where the bit is in a relatively hard formation, such as sand, and the underreamer is in a softer lithology, such as shale, the BHA/bit can react with excessive lateral and torsional vibrations.
These damaging vibrations are not only harmful to drillstring integrity, but also adversely affect the sensitive electronic sensors in the Measurement while Drilling/Logging while Drilling/Rotary Steerable System (MWD/LWD/RSS) systems. When vibrations damage the MWD/LWD/RSS systems, the entire assembly must be tripped out of the hole costing the operator an entire day, or more, of rig time. While drilling previous wells in this deepwater environment, several downhole tool failures pushed operating costs upward and accentuated the need to optimize the entire BHA as a system.
In this case, the operator’s goal was to drill and underream as effective as possible while keeping the BHA “healthy” to the total depth/casing point and minimize the number of trips. This required an in-depth investigation of the bit and reamer’s cutting structures, in addition to their interaction with the physical characteristics of the anticipated stratigraphic column. The BHA design would have to effectively balance the cutting structures of the reamer and the pilot bit to minimize vibrations, regardless of the formation type or transition, while allowing maximum ROP.
INTEGRATING ENGINEERING RESOURCES
To address these challenges, the service company recently formed a separate Smith Borehole Enlargement (SBE) division to develop optimized bit/reamer solutions regardless of the formation type. Balancing the two cutting structures is paramount in providing complimentary performance under a wide variety of drilling conditions. The careful balancing of cutting structures significantly reduces downhole vibrations, allowing the bit and reamer to work together as an efficient unit. Operated at the WOB and RPM values identified as “best” for the particular application, the life and performance of these specialized downhole tools translates directly into increased BHA management and drilling performance with decreased risks/exposure.
Modeling solutions-Dynamic FEA system. Because the drillstring acts as a single complex mechanical system, all elements (nodes in the Finite Element Analysis (FEA) mesh) must be analyzed as a function of time to understand dynamic behavior. To solve this challenge, the service contractor used the Integrated Dynamic Engineering Analysis System (IDEAS) and i-DRILL optimization software.3,4 These are comprehensive, time-based, 4D modeling tools that accurately predict the bit and drillstring’s performance using a FEA system.
Using this proprietary software, the service company’s drilling optimization groups focused on calibrating a virtual model using drilling data from offset wells. This validation modeling reproduced a working virtual model, bringing the previous wells’ behavior to life. This model allowed the teams to run multiple simulations with different BHA components to essentially “re-drill” the same interval multiple times through a variety of lithology types to understand the BHA/drillstring behavior associated with specific changes.
Scenario staging. The modeling allowed in-depth contingency planning and the quantitative arrangement of many “what-if” scenarios. Some of the key questions asked were:
- Should we add stabilization above and/or below the hole-opener?
- Where do we place the underreamer in the BHA, with respect to the bit and LWD equipment, to minimize lateral and/or torsional vibrations?
- Do the cutters on the bit need to be the same diameter as the cutters on the underreamer?
- What WOB and RPM parameters provide the best performance in salt? Are they different for sediments-sand and shale?
- What are the lateral vibrations calculated to be at the bit, MWD/LWD and hole-opener? Do they exceed limits of survivability?
- Which PDC bit design has the best chance to drill the entire hole section (approximately 8,000 ft) as effectively as possible without dulling prematurely?
- Does a 1/8-in. under-gauge expandable stabilizer above the hole-opener improve lateral vibration or does it increase torque significantly?
- Will a pass-through stabilizer above the hole-opener accomplish any lateral vibration mitigation?
The analysis methodology included the operator’s prioritization of the optimization goals based on past experience. This enabled the engineering team to focus on downhole and surface data to identify the changes that would produce the greatest improvement and the ability to quantitatively estimate the new drilling assembly’s performance in the new well.
Figure 1 shows the relationship between ROP, lateral vibration at the hole-opener and at the MWD/LWD tool as a function of the two specific cutting structures, the BHA and lithology type. This provided an opportunity to investigate many the potential scenarios that would be cost prohibitive to investigate at the well site. The operator could not afford any further downhole tool failures or unnecessary trips for new BHA components in the high-cost, deepwater GOM environment. A well-planned BHA with a pre-set range of operating parameters reduced risk and increased the confidence that well objectives would be efficiently delivered at high ROP with maximum total footage/minimal runs to TD as shown in Fig. 2.
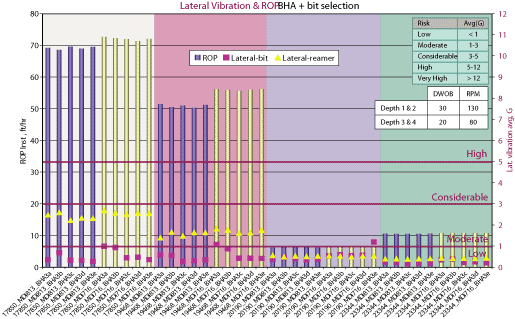 |
Fig. 1. Summary of multi-variable analysis comparing ROP and vibrations.
|
|
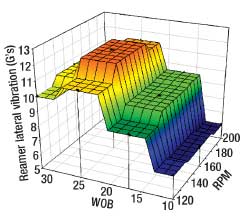 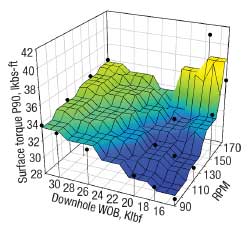 |
Fig. 2. Sensitivity plots identifying critical parameter relationship.
|
|
PROCESS BENEFITS
With so much at stake, the operator looked to the modeling technology to minimize risk and identify BHA components in a configuration that would improve the drilling processes. Through the course of the month-long optimization project, the service company’s engineers looked at each piece of the drillstring, from the diameter of the drillpipe down to the placement of the individual bit and reamer cutters, to determine their effect on BHA performance, Fig. 3. The simulations revealed that some BHA designs resulted in poor drilling performance. Some of the systems had low ROP, while others generated lateral and torsional vibrations.
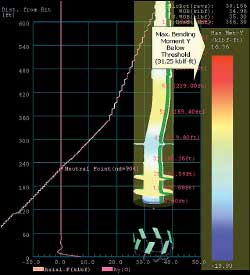 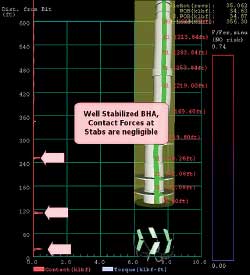 |
Fig. 3. Virtual analysis-maximum bending hi-low (kft-lbs) and maximum stabilizer contact force (klbs).
|
|
In the final analysis, however, the lessons learned and trends identified through hundreds of dynamic simulations were statistically weighted according to the operator’s goals to improve ROP with reduced vibration. Specifically, interbedded formations with different unconfined compressive strengths posed a significant challenge to balancing the cutting structures while maintaining the dynamic behavior of the entire BHA system within the limits of the operation. To accomplish these goals, the service provider designed and tested new and modified technologies/tools, Fig. 4, and PDC bits to solve the challenges inherent to the specific well design.
 |
Fig. 4. Concentric reamer with new-style cutter blocks.
|
|
RESULTS
The results of the analysis were successful. The entire hole section was drilled with one rotary steerable BHA, one bit and one hole-opener at a respectable ROP, Fig. 5. Vibrations were dramatically reduced compared to previous wells in this area, Fig. 6. The resulting ROP improvement resulted in a significant days/cost savings compared to the Appropriation For Expenditure (AFE) plan, Fig. 7.
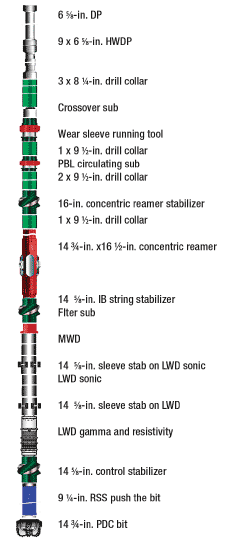 |
Fig. 5. BHA configuration.
|
|
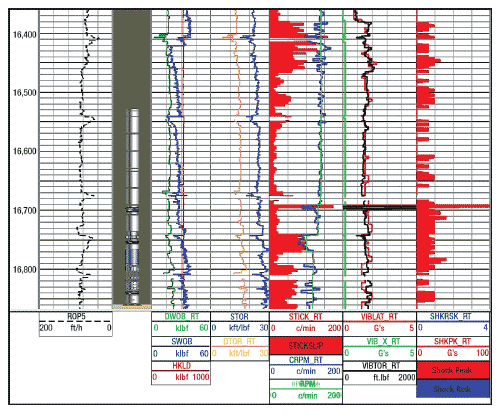 |
Fig. 6. Minimum vibration (track 5) with good ROP (track 1).
|
|
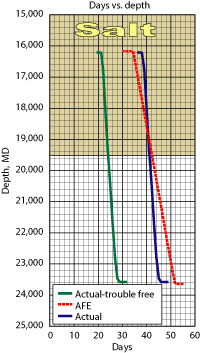 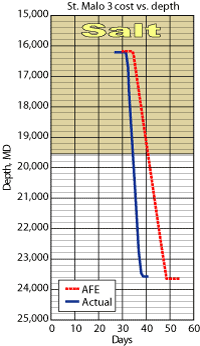 |
Fig. 7. Days vs. depth and cost vs. depth charts showing significant day/cost savings compared to plan.
|
|
The post-well analysis was completed and the drilling team identified several additional BHA/system improvements that could lead to further performance improvements.
ACKNOWLEDGMENTS
The authors thank management at Chevron USA and Smith International for permission to publish this paper. Additionally, special thanks to Craig Fleming, Smith Technologies, for his technical writing and editorial contributions.
LITERATURE CITED
1 Courville, D.F., Childers, R.D., Miller, G.C.: “Wellbore enlargement for a deepwater casing program: Case study and developments” IADC/SPE paper 87153 presented at the IADC/SPE Drilling Conference, Dallas, Texas, March 2-4, 2004.
2 Miller, G.C., Childers, R.D.: “Innovative concentric reamer enhances deepwater drilling operations” SPE paper 84247 presented at the SPE Annual Technical Conference and Exhibition, Denver, Colorado, October 5-8, 2003.
3 Aslaksen, H., Annand, M., Duncan, R., Fjaere, A., Paez, L., Tran, U.: ”Integrated FEA modeling offers system approach to drillstring optimization” IADC/SPE paper 99018 presented at the IADC/SPE Drilling Conference, Miami, Florida, February 21-23, 2007.
4 Frenzel, M.P.: “Dynamic simulations provide development drilling improvements” OTC paper 19066 presented at the 2007 Offshore Technology Conference, Houston, Texas, April 30-May 3.
|
THE AUTHORS
|
|
Mark Frenzel earned a BS degree in geology from Texas A&M University with graduate studies at the University of Houston in both petroleum and reservoir engineering. Frenzel entered the drilling business in 1982 and has worked with a variety of service companies including the applications of low solids drilling fluids, PDC/roller cone bits, PDM’s/turbines, directional drilling, RSS and MWD/LWD systems. His current position at Smith Technologies is focused on their new drilling optimization group that includes i-DRILL and several new real-time services aimed at improving drilling performance.
|
|