Developments can be installed by standard jackup rigs.
George Morrison, Aquaterra Energy
A new minimum-facilities platform was recently installed offshore West Africa for a major operator. It is the first application of Aquaterra Energy’s new platform concept, Sea Swift.
The structure was designed, managed and installed by the company’s personnel, and was fabricated locally in the UK. A second, almost identical, structure has also been built in the UK and will be installed for the same operator offshore Angola during 2008. The new conductor-supported platform uses a field-proven technology for reducing costs in shallow-water field developments by combining the advantages of a platform with the rig-run benefit of a subsea development in a package with lower capital and installation/intervention costs than either.
INTRODUCTION
The new structure, located in an 89-ft (27-m) water depth, was installed using a conventional drilling rig. The platform is composed of a subsea “mini-jacket” weighing 50 t (45 metric tons, mt) and a topsides with a gross weight of about 121 t (110 mt), including all equipment. The structure is supported by three 30-in. conductors which are drilled through, and then grouted within the “mini-jacket” structure. The subsea and topsides structures were installed in early November 2007; work is progressing well with the installation and commissioning of the topsides equipment.
MARGINAL FIELDS
Traditional approaches to platform design and installation provide limited scope for new equipment and techniques to make significant differences in project costs. Use of the innovative platform allows operators to take a broader view of development costs.
The technologies’ features can provide operators an opportunity to attack platform and project obstacles such as vessel scheduling, capital costs and the effective cost of money on projects that have a long delivery time to first production. These advantages in critical path and development costs can convert uneconomic fields to marginal ones and marginal fields to more attractive developments.
NEW PLATFORM
The platform offers the market a proven, versatile and cost-effective product, while allowing installation by standard and low-spec jackup drilling rigs.
Well conductors supporting the platform topsides is an idea with previous applications, but the new platform has advanced this structural configuration from a project-specific solution, developed sporadically by operators with specialized needs, to an optimized and widely applicable product.
Applications range from simple wellhead platforms to self-contained minimum-facilities structures and reasonably large, modular structures for more demanding or larger requirements. Figures 1 and 2 show a simple, minimum-facilities satellite platform suitable for use in about 98 ft (30 m) of water, in a relatively benign environment.
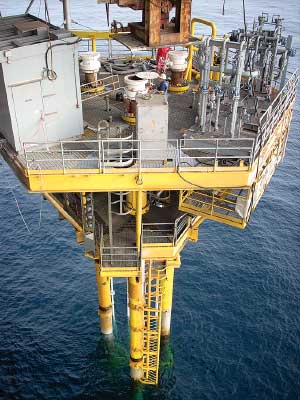 |
Fig. 1. The conductor-supported platform was installed in shallow water.
|
|
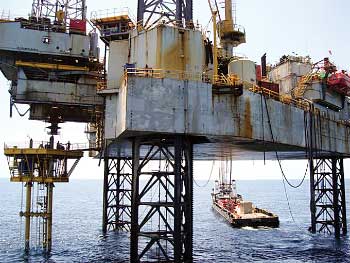 |
Fig. 2. View of the platform structure beneath the drilling rig.
|
|
GENERAL BENEFITS
The first benefit is the simplification of the project critical path, which may result in cost savings.
Every offshore field development requires a drilling rig and a supply boat. The new platform concept starts from an assumption that a client does not want to contract vessels unnecessarily, and is engineered for installation using only these vessels. Removing the need to coordinate the rig and other specialist vessel schedules represents a significant simplification, while removing the charter and rental costs of a heavy lift vessel and transit barges. On a recent West African development using two of the new platforms, the total installed cost was estimated to be less than the line-item costs from mobilizing a heavy-lift vessel to install a traditional platform design.
Structure size. A traditional jacket, for use in 98 ft (30 m) of water, results in an overall structure height in excess of 131 ft (40 m). With the new platform’s structure using the conductors for much of the leg span, a similar water depth can be accommodated with a main subsea support structure of less than 33 ft (10 m). This size reduction allows structures to be built using a wider range of fabrication yards-often opening opportunities to increase local content-and reduces material requirements, manufacturing times and fabrication costs. Being designed to fit on a supply vessel offers reduced shipping costs and lowers complexity. An entire conductor-supported platform can be shipped anywhere using standard freight lines.
Subsea alternative. The new platform is comparable to “subsea on a stick.” It offers advantages over subsea solutions due to the accessibility of Christmas trees and other infrastructure. A small work boat or helicopter can carry out remedial or regular maintenance work.
The new platform design can allow scheduling advantages due to its construction, which requires simple fabrication and limited long-lead items. This allows a delivery schedule of around six months, once a design has been approved, which compares favorably with quoted delivery times for subsea equipment.
SPECIFIC APPLICATIONS
Bases for the new platform’s design were often project specific. Some operators looked at the new platform as an inexpensive tool to allow additional wells to be drilled on platforms where every slot was occupied. Adding a rig-installed, bridge-linked platform alongside existing infrastructure provided an attractive option.
Others used the new platform as an extension to template-based pre-drilling. It can be used to pre-drill and complete wells, and to install export risers and pipelines, prior to the arrival of a process platform. This allows earlier startup than either platform drilling or traditional pre-drill options, because there is no requirement for rig operations to drill or tie back wells after platform installation.
For some prospective field developments, an Extended Well Test (EWT) is required to prove commerciality. For a marginal development, tying up a drilling rig for an extended period, or having to tie the well back to other infrastructure to test, can tip the commercial scales to the uneconomic side. The new platform design offers a reusable EWT platform that does not tie up a more expensive vessel and does not require tieback to other infrastructure to test. It also allows a well that has proven its commerciality to be shut in and then tied into export infrastructure easily on completion of the test.
In the same way, other marginal field developments have identified the design’s minimized abandonment and disposal costs as important factors in project economics. Abandonment and removal of the structure can be completed by a rig and supply vessel, without requiring additional vessels. This simple removal and reuse benefit becomes extremely attractive to a marginal-field development team.
In areas where a number of fairly similar prospective short-lifetime developments exist, but with each one being marginal, the option of reusing the platform on a number of fields in sequence can make each development an attractive option. In these cases, renting the platform can shift development costs from upfront capital costs to longer-term, operational-cost budgets.
|
THE AUTHOR
|
|
George Morrison is the managing director of Aquaterra Energy. After graduating from Aberdeen University with a BSc with honors in civil and structural engineering, he worked for Nowsco, BJ Services and a Norwich engineering firm.
|
|
|