Artificial Lift
What’s new in artificial lift
Part 2 – Fourteen new downhole/ surface system developments from 10 companies for electrical submersible pumping and other artificial lift operations.
James F. Lea and Herald W. Winkler, Texas Tech University, Lubbock, Texas; and Robert E. Snyder, Executive Engineering Editor
Part 1, presented last month, covered 15 recent developments in three categories of artificial lift technology: beam and progressing cavity pumping (PCP) and plunger lift.
This concluding article introduces 14 new developments from 10 companies. Eight of the presentations include new downhole and surface equipment for ESP systems. The remaining six items cover miscellaneous contributions for new downhole pumps, operations monitoring/ control and soap stick launching.
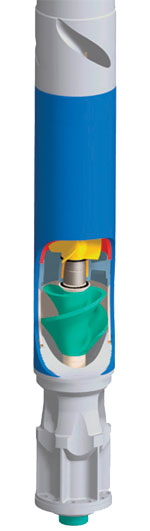 |
Fig. 1. High-volume rotary/ vortex ESP gas separator.
|
|
ELECTRICAL SUBMERSIBLE PUMPS (ESPs)
Described here are eight equipment and instrumentation/ software developments including: an ESP gas separator; downhole monitoring tool; coalbed methane dewatering motor; ESP optimization; a smart system controller; rod pump replacement; a service to reduce costs; and a low-profile cable protector.
High-volume ESP gas separator. Multi-phase fluid wells historically have been challenging for ESP electrical submersible pump systems and, consequently, a constant goal for the industry is to push the limits of gas handling technology. Baker Hughes Centrilift, Claremore, Oklahoma, a leader in gas handling technology, recently released its newest high-volume rotary/ vortex downhole gas separator, GasMaster, designed to maximize production from wells with significant free gas content, Fig. 1.
The new separator incorporates dramatic design changes compared to standard gas separators, improving total flow rate through the separator into the pump while providing better separation efficiency. Centrilift engineers determined that, at high gas volumes, older separator designs did not provide enough pressure increment to overcome flow losses within the unit, and the inducer design choked at higher rates.
Based on this research, the company realized that a new approach to gas separator pressure charging was required, which led to development of the high-angle vane auger design (HAVA), incorporating the optimum vane angle for efficiently handling free gas and larger two-phase fluid volumes.
Further testing indicated that improvement to the intake/ base, discharge head/ diverter and spider bearing was needed to optimize fluid path geometry throughout the gas separator. Various configurations were tested in the high-pressure gas loop test facility in Claremore until designers were satisfied that this goal was reached with the new system’s component parts. Improved production rates and higher separation efficiencies obtained confirmed the success of these designs.
The new separator is available in both rotary chamber or vortex options and high/ low flow options to specifically fit each well application. The gas separator also incorporates a range of abrasion protection levels that can be customized to specific well conditions.
Downhole monitoring tool. Baker Hughes Centrilift is developing a full suite of downhole monitoring gauges, another important tool used with optimization services. In 2004, the company introduced the GCS Centinel downhole monitoring system, designed specifically for use with ESP equipment, Fig. 2. The gauge tool provides data on pump intake pressure, and intake and motor winding temperatures, along with system diagnostics. The digital data transmission system eliminates potential interference and resulting inaccurate information or even loss of downhole data, which can occur with traditional analog data transmission systems.
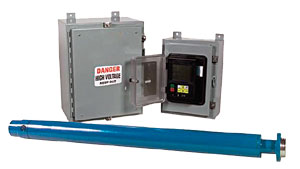 |
Fig. 2. Downhole monitoring system designed for ESP equipment use.
|
|
The new system’s surface electronics panel receives signals from the surface inductor panel and displays data through the graphics display panel standard within the GCS family of products. The surface inductor panel, or choke panel, is the interface between the ESP power system and the surface electronics equipment, filtering the digital communication signal from the AC power line.
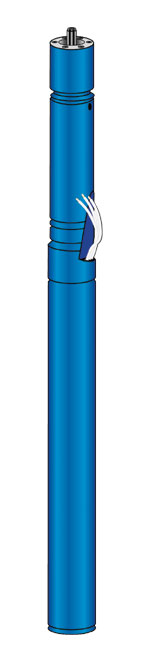 |
Fig. 3. Slimline design ESP motor for coalbed methane well dewatering.
|
|
The company is continuing to add tools and expand system monitoring and production control capabilities. The new tool, combined with the GCS Electrospeed II variable speed drive and the GCS vortex motor controller, allows active real-time production monitoring and control, as well as ESP performance monitoring. Predictive analysis of equipment performance is now within reach, as are the use of adaptive control strategies geared to maximize system performance linked to real-time technical and commercial drivers.
Coalbed methane water pump motor. Coalbed methane (CBM) production continues to grow in the US and is garnering more attention worldwide. However, a constant challenge for CBM operators is economically dewatering the coal seams to release gas. Baker Hughes Centrilift has developed a new motor with an integral seal specifically for CBM low-cost applications.
The 450 CBM motor is a two-pole, slimline design for 5-1/2-in. casing, Fig. 3. Traditional oilfield technology ESP systems are economically challenging in CBM applications, but water-well systems require larger-diameter equipment for the same horsepower. The new motor’s integral seal design significantly reduces motor/ seal costs while offering higher operating parameters and a more robust design vs. water-well pumping systems. This new motor has an operating temperature rating of 212°F (100°C).
It can deliver up to 30 hp in a 4-1/2-in.-diameter design. This allows the unit to be run in 5-1/2-in. casing vs. 7-in. casing necessary with water-well pumping systems for comparable horsepower, thus providing operators significant drilling and completion cost savings.
The innovative integral seal design is a single chamber bag seal section attached to the motor, minimizing the number of necessary components and reducing cost and installation time. Additional technical features include: 1) the high-load, self-aligning thrust bearing for the motor, which carries rotor stack and thrust from the pump; and 2) the premium face mechanical seal, designed to handle coal fines in the fluid.
ESP optimization. Baker Hughes Centrilift is introducing a range of optimization services to offer technologies and processes necessary to tailor solutions for a specific well or field performance improvement. This will integrate a broad range of expertise and technologies to achieve the lowest possible total lifting cost, making a sustained contribution to present and future net asset value.
A key tool supporting the ESPeXpert Optimization Services is the new ESPeXpert software tool powered by Centrilift’s industry leading Autograph PC sizing and simulation software. In-house experts can use this new tool to automatically match downhole/ surface performance measurements, using both data provided by the SCADA system and equipment sizing information. It also provides a built-in, rules-based diagnostics engine.
This new functionality enables early identification and prediction of challenges or anomalies in the well, or the ESP, to enable performance intervention. This rules-based process enables prediction of possible future divergence from optimal performance based on the company’s unique Centrilift knowledge base.
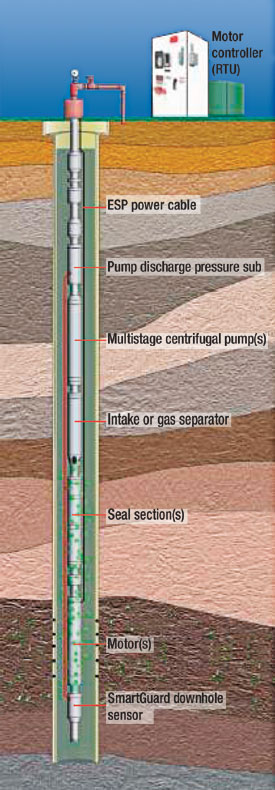 |
Fig. 4. Downhole sensor and surface interface system to control submersible systems.
|
|
The optimization services also will offer remote monitoring and control through a joint venture partner, providing next-generation low-power, wireless technology via radio, satellite or cellular communications.
While new software communications technologies are critical for providing, displaying and manipulating data, people are the key to the new optimization services. The company will use its worldwide network of local experts with extensive training not only in ESP and PCP design, deployment and operation, but also in reservoir and production characteristics, completion design and data monitoring and transmission technology. The operational strategy is to make as many informed, real-time production performance decisions as close to the wellsite as possible with the goal of continually improving present/ future net asset value.
Smart system controller. Wood Group ESP, Inc., Midland, Texas, has developed a new bottomhole sensor that does much more than just give pressure readings. This breakthrough in downhole monitoring has broken barriers and presented numerous methods of assisting operators in maintaining their submersible equipment in more productive and cost-effective ways. This Smart Guard sensor and surface interface system, Fig. 4, is a reliable, accurate and cost-effective way of putting the operator in control of submersible equipment. Some of the improved capabilities include:
- Pressure accuracy, 0.1% psi/bar
- Temperature accuracy, +/ – 1.8°F (+/ – 1.0°C)
- Vibration accuracy, 1%
- Current leakage detection
- Temperature shut-down capabilities
- Discharge temperature/ pressure
- Flow rates, and
- 30-day memory.
A few of the many applications include: 1) ability to eliminate cycling in CO2 applications and wells with very high GLRs; 2) ability to access accurate, reliable information for sizing/ troubleshooting; 3) operating from the pump intake as opposed to relying on the surface controller; and 4) temperature shut-down capabilities, an intricate feature as operators venture into deeper, hotter production zones.
These and many more features are assisting operators in solving problems, analyzing failures and extending running times in areas once thought impossible.
ESPs to replace rod pumps. Wood Group ESP, Inc. has developed a new line of low-volume pump stages. This new line is loaded with higher efficiencies, wider vane designs, beefed-up thrust washer areas and lower operating ranges, Fig. 5. Efficiencies of these new stages are much higher than the old technology still being used in today’s market. In many cases, a typical 5,000-ft design can require 100 less stages to lift the same total dynamic head (TDH) as the old stage designs.
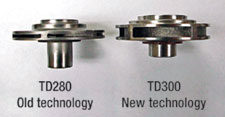 |
Fig. 5. Lower-volume pump stages. New, wider vane design, right, reduces ESP stages.
|
|
The wider vane designs have been accepted by operators faced with the challenges of trying to maintain small-volume pumps in CO2 floods, and producers with high GLRs. This breakthrough has greatly reduced gas locking/ plugging problems previously associated with narrow vane clearances and fluid paths. The thrust-washer areas have been greatly increased to extend run times in both ideal operating conditions and harsh environments.
Finally, there is an option for operators with low-volume applications that suffer from deviated wellbores or wells that are just too deep to achieve long run times with a conventional rod pump. This issue has been resolved with development of the TD150. This stage has an operating range of 80 bpd to 280 bpd. Further, the new ESP’s operating cost is now competitive with that of today’s rod pumping systems.
Lifting service reduces ESP costs. The Axia Lifting Service from Schlumberger, Sugar Land, Texas, is an end-to-end offering to improve production and reduce lifting costs in wells and fields with operating ESPs. The service uses well/ field information in combination with real-time ESP operational data for surveillance/ control of submersible pump operation, and broader evaluation of field-wide production improvement opportunities, Fig. 6. The results are more efficient field operations, reduced lifting system costs and increased production.
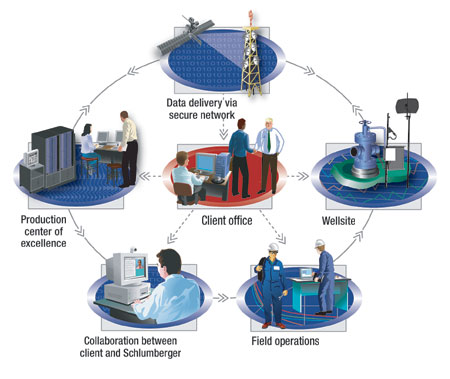 |
Fig. 6. Broad-based lifting service evaluates/ controls field and downhole operations for overall ESP optimization.
|
|
The foundation of the new lifting service is based on reliable REDA ESPs and Phoenix downhole monitoring systems. The service is completed by expertise from the Schlumberger Data and Consulting Services team, the espWatcher surveillance/ control service with integration of the LiftPro well optimization process. The Axia service seamlessly integrates downhole equipment with expert analysis through secure, remote connectivity to provide operators a simple interface to their own processes. Operators can now rely on the new lifting service to improve their own multi-well, field and reservoir management workflows, while increasing their personnel’s productivity.
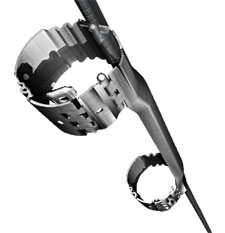 |
Fig. 7. Low-profile ESP cable protector.
|
|
Low-profile cable protector. The Cannon Services, Stafford, Texas, cable protector has proven to be an ideal solution for securing, supporting and protecting both round and flat ESP cable configurations downhole. The protectors are available for single and dual completions, and have been used as deep as 18,500 ft on single ESP completions, and 12,000 ft on dual ESP completions. Company engineers regularly create custom designs and configurations to accommodate unique cable bundles and other special requirements such as round-to-round, flat-to-flat and round-to-flat cable splice protectors.
The new low-profile protector, Fig. 7, is designed with a minimal running profile to protect ESP cables where running clearances are critical, such as casing liners or casing patches. The standard- and low-profile protectors can be installed and removed quickly, and they are reusable. All protectors are extremely durable and are manufactured from a variety of materials including low-carbon and stainless steel. The company maintains a comprehensive stock of protector components, to provide immediate customer response.
MISCELLANEOUS
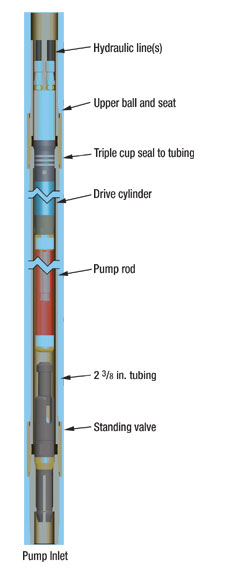 |
Fig. 8. Small-diameter hydraulic diaphragm pump.
|
|
Six items under this category include: insertable diaphragm pumps, twin screw pump technology, a new water-cut meter, data recording options, an automatic soap stick launcher, and solid chemical sticks.
Insertable diaphragm pumps. SmithLift, Orem, Utah, a division of Smith International, Inc., has developed and is in the process of testing, a new, small-diameter pump designed to be inserted inside 2-3/8-in. or 2-7/8-in. production tubing on capillary tubing, Fig. 8. The pump is designed to produce wells from 10 bpd to 300 bpd and depths to 12,500 ft.
The pump is powered hydraulically from surface via hydraulic fluid transmitted through a single capillary line. This system gives the performance advantages inherent to the diaphragm design, such as no seal wear, high efficiency, solids handling, and the ability to pump off continually without damage. These advantages, combined with the ability to insert or remove the pump quickly (up to 3,500 ft/hr) using capillary tubing technology, provide a cost-effective artificial lift solution.
The pump can be installed into an existing tubing string as long as the string has a standing valve below the fluid level in the well. The pump is inserted into the string in the same way as conventional capillary tubing tools are installed, and can be installed into a pressurized tubing string if required. Once in place, the packer is activated to seal the pump to the tubing string for pump operation. A small hydraulic package is all that is required on the surface, giving a low-impact, low-profile installation. Several power options are available, including electrical power, gas engine, differential gas pressure, solar and wind.
Twin screw pump technology. CAN-K Artificial Lift Systems, Edmonton, Alberta, makes several types of surface and downhole twin screw pumps, including:
- ESTSP (Electric Submersible Twin Screw Pumps); downhole; 5.38, 6.75, 7.75 in., and larger
- TDTSP (Top Drive Driven Twin Screw Pumps); downhole high-temp.; 5.38, 6.75 and 7.75 in., and larger
- TuDTSP (Turbine Prime Mover) or TsDTSP (Twin Screw Prime Mover), high temperatures; downhole, trial phase; 218 to 350° C
- Surface Transfer Twin Screw Multiphase Pumps; patented downhole technology on surface, and
- Sub Sea Twin Screw High Pressure Multiphase.
For primary features of twin screw pumps, they are: positive displacement pumps, through which the medium moves axially in a continuous straight path. They have the least shear rate compared to any pump used in the industry, hence, produce the least emulsion. And they have the least intake pressure requirement.
The pumps can be designed for temperatures exceeding 350°C; and to handle gas up to 95% (GVF) and slugs of 100% gas. When used in adiabatic compression, there is major savings in hp, which is critical in low viscosities and in high gas content. High pressure capability is possible up to 3,500 psi differential pressure, using patented downhole module technology and unequal screw design-hybrid pump-compressor/ pump technology.
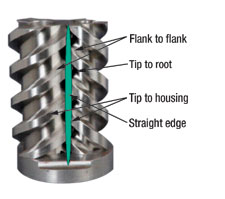 |
Fig. 9. Twin screw pump, least slippage screw design.
|
|
Downhole stages of unequal screw design are shown in Fig. 9. This is the least slippage screw design. It is suitable for low to high viscosities using the same pump. For high gas content, because power consumption of a PD pump is proportional to swept volume and delta pressure, using a smaller displacement to lift will save power. Therefore, a proposed solution is to use high-capacity stages at suction, and lower-capacity stages at discharge, like a tapered ESP. Bypass valves are used as required between stages.
For advantages of using downhole twin screw pumps: they handle medium at the source and increase production, with reduced pump size. And they control production by merely changing speed and temperatures.
Further advantages are, the pumps move larger capacities to surface, and basically eliminate all surface facilities up to the gathering station. And for high temperature operations, the submersible motor will handle up to 218°C; with top drive systems, temperatures go up to 280°C; and top-drive, specially built models can go up to 350°C.
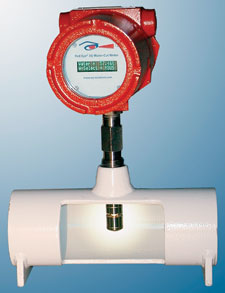 |
Fig. 10. Second-generation water-cut meter.
|
|
Improved water-cut meter. eProduction Solutions, Inc., Kingwood, Texas, a Weatherford International Ltd. company, recently introduced its new Red Eye 2G water-cut meter, combining the latest in optical sensing technology with the company’s field experience in high water-cut measurement, Fig. 10. The new design offers the latest in instrumentation for accurate phase fraction measurement.
The original Red Eye (1G) water-cut meter measures the oil in a mixture of oil/ water by passing a beam of infrared light through the stream that is absorbed by oil but not water. It was designed for high water-cut measurements, and its performance in that condition stands unmatched. Red Eye 2G extends performance to wide-range measurements (low to high water cut) by simultaneously measuring multiple infrared frequencies. Both meters operate independent of water salinity, and the 2G also has low sensitivity to entrained free gas.
From an operations standpoint, this new-generation meter features simplified calibrations, lower cost installation, and an improved user interface. The electronics are mounted directly to the measurement probe so there is no field wiring other than power and output signal cable. The new meter’s configuration software can run on a PC or hand-held PDA. The NOC (net oil computer) module can include a local keypad/ display interface and/or a wireless link to a hand-held PDA for the ultimate in operator convenience.
Data recording options. IHS Energy’s FieldDIRECT services – a Web-based data collection service for virtually instant communication between field and office operations, engineers and management – recently released Version 3.0 of its Production Explorer software offering to include additional data fields to track compressors, electric motors and engines, beam pumping units, ESP, gas lift, plunger lift wells and chemical usage.
This data can be entered at the well site into a Windows CE-based, hand-held device with an extensive but easy-to-use interface. The information is then sent to the company’s Web-based database. With a user name and password, a user – typically production, engineering and marketing staff – can view plots and reports on the Web-based application and/or through Production Explorer, a PC application.
The Englewood, Colorado-based company has continued to evolve FieldDIRECT services’ features and functions based on feedback directly received from pumpers and field personnel over the past five years the service has been offered. The service has more than 16,000 wells on the system, making field data available daily for spotting trends and troubleshooting by users anywhere in the world, providing companies with direct and indirect savings at every step in the data recording and reporting process.
Automatic soap stick launcher. Lightning Industries, Inc., Hobbs, New Mexico, offers the Lightning Autoloader, a step into the future for the gas industry, and the safest and most technically advanced autoloader on the market today, Fig. 11. This soap launcher is equipped with patented safety check valves to prevent blowouts. It will clear the tubing without dismantling the equipment when a soap stick lodges in the tubing. With safety in mind, the system loads from the ground using a 100 solid chemical stick rack; no ladder is needed.
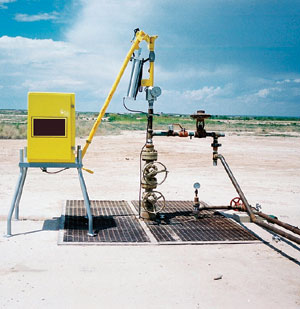 |
Fig. 11. Automatic soap stick launcher.
|
|
In operation, the system loads a soap stick into the horizontal, hinged container resting in place on the back of the box shown. The upper hydraulic chamber then lifts the long tubular and hinged container to vertical and the soap stick falls into the check-valve-closed upper top string section, after which, valves automatically close the top section and open the tubing to the soapstick, and the hydraulic chamber relowers the installation tubular.
The system is programmed via a user friendly controller or by a SCADA system. It increases production by monitoring the wells; and it has the capability to shut wells in for a predetermined time, then automatically restart them. It has excellent capability for remote, marginal or offshore uses.
Chemical sticks, of which soap sticks are one of many types, are used to place a small amount of a particular chemical in a well, usually at the bottom or close to the perforated interval. Upon dissolution, the sticks will perform a needed function such as scale removal, foaming of water and/or oil, corrosion inhibition, paraffin inhibition or numerous other functions. The success, following the use of chemical sticks, will often result in the saving of considerable money by reducing wear and fatigue on metal equipment surfaces, and time in labor cost and lost production for the oil/gas companies. Often, as in the case of water removal from gas wells, the increased production will pay for the treatment in a matter of hours.
Chemical sticks. Many operational problems can be solved using solid chemical stick technology. Select Industries, Wichita Falls, Texas, can help with all solid chemical stick applications. The company’s capabilities extend further to soap, acid, corrosion, scale inhibitors, paraffin control, oil foam and soluble pigs. The company’s trained staff can make recommendations using analytical data, or formulate a custom solid chemical stick for wells not within normal parameters.
Solid chemical sticks are advantageous to producers as they require no bulk tanks, containment or other environmental dangers associated with liquid products; plus they are cost effective.
THE AUTHORS
|
 |
James F. Lea, professor and Roy Butler Chair Holder, Texas Tech University, Lubbock, holds BS/MS degrees in ME from the University of Arkansas, and a PhD in ME from Southern Methodist University. He worked for Sun Oil Co. as a research engineer from 1970 to 1975; from 1975 to 1978, he taught engineering at the University of Arkansas; and from 1979 to 1999, he was leader of optimization and artificial lift at Amoco EPTG. He served as Chairman of Petroleum Engineering at Texas Tech from 1999 to 2004. Mr. Lea is a registered professional engineer in Texas; he has authored/ co-authored several patents, as well as publications on artificial lift.
|
 |
Herald W. Winkler is former chairman, now professor emeritus and research associate, in the Department of Petroleum Engineering at Texas Tech University in Lubbock, Texas. He is presently working as a consultant in artificial lift, specializing in gas lift.
|
|
|
|
Part 1 |
|