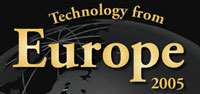 |
Norway |
|
Hot prospects await cold gas
Remote offshore gas fields are the target of a new technology alliance between Statoil, Linde and Aker Kvaerner, focused on developing cost-effective marine solutions for producing and handling LNG.
Global LNG trade keeps growing. In 2003, global LNG movements totaled almost 6 Tcf (170 Bcm), equivalent to over one-quarter of all trade in natural gas. Annual LNG production, driven by burgeoning demand in the US and elsewhere, was expected to increase 13% during 2004, once all the numbers are tallied. This trend should continue.
Demand for energy also generates opportunity for its supply. Such supply chain opportunities have been recognized by Statoil, which is a partner in offshore licenses containing large stranded gas reserves around the Atlantic margins, including deep waters off Nigeria, Venezuela, Brazil and Angola, where no ready, local gas market exists.
However, offshore LNG technology must be developed and commercialized economically. Accordingly, Statoil is tapping into LNG process technology from Linde and the globally-based offshore design and project execution skills of Aker Kvaerner. “Energy companies are increasingly interested in developing stranded gas reserves,” said Ingve Theodorsen, Statoil’s vice president for Research and Technology. “The technology alliance we have formed with Linde and Aker Kvaerner will strengthen Statoil’s capabilities in the management of the offshore gas and LNG supply chain.”
Strengthening the alliance. The alliance builds on an existing collaboration between Statoil and Linde that developed and qualified the high-efficiency Mixed Fluid Cascade (MFC) liquefaction process for LNG. It has also led to a new generation of spiral-wound heat exchangers that is crucial in the cryogenic cooling of gas to – 258°F ( – 161°C) to produce LNG.
Both breakthroughs are key to the Statoil-led Snøhvit development in northern Norway, featuring Europe’s first LNG production plant, due onstream in 2006. The new heat exchangers will also be incorporated into Shell’s LNG projects in Australia and Brunei, and into the firm’s Sakhalin project off eastern Russia.
Aker Kvaerner, too, has worked closely with Statoil for the past two years on evaluating methods for exploiting stranded gas reserves, not involving pipelines to shore.
Moving offshore. LNG production plants, to date, have been sited only onshore, due to their huge scale, technical complexity and overall economics. However, new market drivers (as in availability of stranded gas), are shifting the emphasis offshore.
“LNG projects are huge undertakings costing billions of dollars,” said Dag Jenssen, managing director of Aker Kvaerner Engineering & Technology. “To move such plants offshore requires a deep engineering understanding of all aspects of floating marine structures and associated technologies, and LNG storage and transfer systems.” Added Jürgen Bokämper, Linde’s senior vice president for natural gas plants, “We expect the three companies to drive toward more cost-effective solutions for offshore LNG production.”
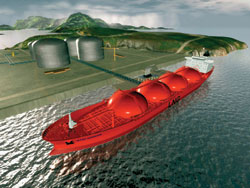 |
A barge-mounted LNG processing plant to be sited at Melkøya island offshore Norway is an example of cooperation underway between Statoil, Linde and AkerKvaerner.
|
|
Shared experience. The firms already have worked together on the Snøhvit development that features a barge-mounted LNG processing plant at Melkøya island near Hammerfest.
“Another very important undertaking we worked on together in 2003, before the alliance formed last August, is a possible development option for NnwaDoro, two very large gas fields operated by Shell and Statoil offshore Nigeria,” said Oscar Graff, vice president for LNG production in Aker Kvaerner and member of the alliance Steering Committee. “For this, we worked as a team to deliver a commercial LNG solution, based on an FPSO vessel (FPSO) in 4,265 ft (1,300 m) of water. The Linde MFC process was sized to deliver 6.4 million US tons (5.8 million metric tons) per annum of LNG from a single process train, with storage capacity for 8.5 MMcf (240,000 m3) of LNG and 4.25 MMcf (120,000 m3) of condensate.”
The FPSO concept, about 1,400 ft (427 m) long and 310 ft (94.5 m) wide, would off-load in side-by-side fashion to an LNG carrier at rates up to 353,000 cfh (10,000 m3/hr), and would also deliver propane and butane. The topsides design included a fully integrated, modularized production process, keeping modules to within a weight of 13,200 US tons (12,000 metric tons).
One clear benefit of locating LNG production offshore in deep water comes from cold seawater available at around 3,300 ft (1,006 m) below the surface. “Using cold seawater in the process cooling circuits could help boost LNG production efficiency by up to 25%,” said Graff. 
|