Automation and control: How IoT optimizes oil and gas operations
CURT AHART, Digi International
Companies in the oil and gas industry face significant challenges, from market volatility and energy price fluctuations to the evolving energy landscape and pressure from regulators and environmental organizations. These companies also operate in some of the most hazardous and demanding environments, placing stress on personnel and equipment.
Further, like every company, there is the ever-present need to increase productivity and cut costs while doing more with less amid pronounced labor shortages. These challenges and business needs aren’t new to oil and gas companies, but they necessitate proper solutions to mitigate potential risks and dangers. One solution many forward-thinking companies continue to leverage is the Internet of Things (IoT).
Oil and gas companies use IoT devices and sensors to connect physical objects, like downhole wells, pumps, tanks and meters, etc., to the Internet. Once these objects are connected, companies can enjoy the benefits of autonomous collection, exchange and eventual data storage within a centralized cloud-based remote management platform equipped with an intuitive dashboard for ease of use. These data will enable mission-critical visibility, allowing companies to make real-time decisions, launch service tickets and monitor the health and status of their equipment, unlocking greater operational efficiency, increasing worker safety and retention, reducing failures and enhancing environmental protection.
ENHANCING OPERATIONAL EFFICIENCY THROUGH AUTOMATION
One of the greatest benefits of an IoT deployment is improved operational efficiency, Fig. 1. During the last oil crisis, when oil became extremely cheap, operators sought to reduce costs however they could. Nevertheless, they still needed to run their businesses. In other words, they needed a way to endure the shocks of oil dropping from $80/bbl to $50/bbl, while still having the ability to make money and avoid going out of business.
With IoT sensors and devices, oil and gas companies found a way to reduce operational costs and to protect profit margins more effectively. Specifically, the ability to capture more data from every part of the value chain and analyze it in near-real time helped optimize reservoir management, increase facility performance, proactively schedule maintenance and eliminate product waste.
There are many different machines and processes in an oil field that, when automated through IoT, enable greater operational efficiency that is impossible through manual intervention or “eyeballing” numbers. IoT sensors also can help operators understand the rate at which a well produces product, to maximize efficiency. New wells are the most productive at the beginning of their lifecycles and get managed down until eventually capped. During this phase of a well’s lifecycle, companies should implement the most automation through IoT, because the well is not producing nearly the same amount of product as initially.
Another area where IoT can improve operational efficiency is via sensor-based tank monitoring. The tanks that store crude oil and wastewater are situated on-site for drivers to pick up the fluids. However, oil wells are usually in far, remote areas. Operators must know exactly when to dispatch these drivers for maximum efficiency. With IoT sensors monitoring tank levels and sending alerts when the tanks require emptying, companies will have the real-time visibility necessary to dispatch trucks automatically. This precision will eliminate needless truck-rolls, saving money on fuel and optimizing route scheduling.
Oil and gas companies can improve many other processes through IoT-supported monitoring and automation. For instance, there are gas meters that track the flow of natural gases from the well to a midstream pipeline, analyzers that monitor separator performance, tank level sensors observe the productivity of a well in barrels per day, infrared flare monitors that monitor the burn-off of gas by flares in production sites with no gas pipelines, etc. In the past, these processes were monitored or collected manually or through expensive private or satellite networks. However, cellular technology makes communicating with these sites much more economical and affordable, enabling companies to install larger IoT deployments for automation and remote monitoring capabilities, Fig. 2.
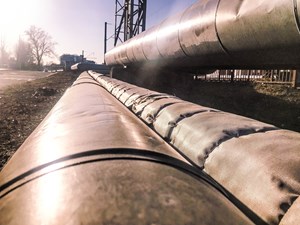
CLOSING THE SKILLS GAP WITH WORKER SAFETY
One of the greatest challenges facing the oil and gas industry is the aging workforce, paired with the gradual decline in available replacements.1 According to a survey from Patch Personnel, approximately 10% of the oil and gas workforce possess zero to 10 years of experience.2 The remaining 87% have ten-plus years of experience, with 49% having over 20.2 These findings highlight the lack of early and mid-career professionals, which is particularly concerning, as the current older workforce ages and retires. Put simply, the industry’s workforce is dwindling, and there aren’t enough young professionals coming in to replace them.
The consequences of this exodus are multifold, with one of the most serious being that as skilled workers leave, a knowledge gap emerges. For example, veteran oilfield workers understand how to operate complex machines, interface with programmable logic controllers and use other instrumentation. The rate at which these employees are retiring means the valuable skills accumulated won’t transfer cleanly to the next generation.
Companies must bolster retention efforts to prevent this knowledge from disappearing. To that end, they should implement IoT solutions to automate various tasks (like sending people into the field to perform actions manually) and enhance worker safety. Specifically, oil and gas companies must utilize a combination of IoT sensors and remote monitoring technologies to capture more data and gain greater awareness of workplace environments and the potential hazards therein.
Closing the widening skills gap will require better worker safety, which will help attract new workers and retain current ones. Because oil fields are often in remote locations, it can be dangerous for workers to commute to these places, especially during the winter months, when roads become slick and visibility is limited. By using IoT devices to automatically monitor and collect data readings from meters across oil fields, companies can minimize the number of trips workers must take, keeping them out of harm’s way. Fewer truck rolls also mean better environmental stewardship, but this article will discuss sustainability in more depth later.
An IoT-based monitoring system, like a canary in a coal mine, can also detect the presence of harmful substances or airborne chemicals, allowing operators to determine if a remote wellhead is safe for workers. This technology can capture data in real time from above-ground pumps to ascertain if other hazards like spills and leaks are imminent, alerting personnel to possible safety issues so they can avoid injuries and fatalities.
PREDICTIVE MAINTENANCE
It is not just the employees that must work in these demanding environments but the equipment and machines, as well. For instance, operators use strong chemicals to help pull crude oil out of wells; not only this, but major oil fields in the U.S. are also in places like Texas, New Mexico, North Dakota and Alaska, where it can get very hot or cold. As such, this equipment (including the IoT devices monitoring them) must be ruggedized and capable of enduring extreme temperatures, moisture, shocks and vibration, as well as corrosive conditions. Some machines, in specific areas where volatile gases and fumes are present, must be explosive-proof. These IoT devices also need sufficient battery life, since they are located in hard-to-reach places and must remain operational for long periods.
Of course, despite a machine’s ruggedness, it is not indestructible; eventually, it will break down. Operators can use IoT to enable predictive maintenance, which involves collecting and analyzing quality data over time from machines, to help operators maximize uptime and predict breakdowns before they occur. Without the ability to forecast when parts need to be replaced, companies risk a machine unexpectedly failing, resulting in a chain reaction of increased downtime, reduced productivity and lost revenue. Predictive maintenance ensures machines remain on schedule, avoiding expensive replacements and eliminating the need for technicians to make emergency on-site visits.
Furthermore, operators can protect their machines through IoT-enabled security and surveillance solutions. Sensors can alert personnel if an unauthorized individual enters a designated area, thwarting equipment vandalism or theft while protecting any employees currently on-site.
BOLSTERING ENVIRONMENTAL STEWARDSHIP
It is no secret that the oil and gas industry is under intense scrutiny from regulators and the larger public concerning environmental stewardship. Fortunately, the data insights possible through IoT solutions and complementary technologies enable companies to take note of every leak or emission, preventing fixable issues from spiraling into the latest news headline.
Remote monitoring solutions use IoT sensors to measure emissions, hydrocarbons and other chemicals in the air, soil or groundwater. Should levels go above a set threshold, suggesting a danger to the environment, the remote monitoring system will notify requisite personnel to take immediate action and mitigate the environmental impact. Some of these systems are advanced enough to shut off equipment automatically; for example, if there is a failure and product is collecting on the ground, the IoT-powered solution will trigger a shutdown, saving the company from an expensive cleanup.
Oil and gas companies also can use IoT monitoring systems to optimize energy consumption across operations. By combining IoT sensors with artificial intelligence (AI) and machine learning, companies can forecast energy needs, ensuring energy management aligns with regulatory constraints. Additionally, IoT monitoring systems help oil and gas companies demonstrate their adherence to stringent regulatory requirements through solid numerical evidence.
These solutions collect and manage data much more effectively than human monitors, improving accuracy and ease of report generation. With this information, companies can prove their compliance with regulatory requirements, protecting themselves against litigation and fines. Plus, such data will be critical in building a better public image and challenging false accusations.
CONNECTIVITY IS THE CORNERSTONE OF IOT
Although recognizing the need for IoT is an easy decision in the oil and gas industry, deciding what constitutes the perfect IoT solution is more difficult. Companies obviously should prioritize those IoT devices and sensors that are rugged and can withstand harsh environments. However, outside toughness, connectivity is the foundational component of a successful deployment. For example, ideal IoT devices can run on both public and private cellular networks, with failover capabilities between multiple networks to maintain consistent connectivity, safeguarding operations.
Edge intelligence is also critical. Note that leading IoT providers will put the computing power in their devices at the edge of the enterprise network. As such, sensor data processing occurs immediately and closer to the place of data generation. Because the data don’t go to the cloud, there is a significant decrease in latency. This unique feature of edge computing supports fast machine-machine communications and automation, allowing operators to gain invaluable real-time insights. Edge computing speed also enables companies to detect whether a situation is moving toward a failed condition. Even if connectivity to the core data center or cloud goes down temporarily, a device leveraging edge computing will continue logging data to prevent gaps in historical data.
Finally, companies should look for an IoT provider that has experience with 5G connectivity, as it makes it easier to incorporate technologies like A.I., which will be a game-changer in the future energy landscape. Faced with a shrinking workforce, pressure from environmental agencies and market volatility, it is paramount for oil and gas companies that they leverage 5G bandwidth and edge intelligence to process massive volumes of data and harness the power of advanced technologies like A.I.
REFERENCES
- https://data.bls.gov/timeseries/CES1021100001?amp%253bdata_tool=XGtable&output_view=data&include_graphs=true
- https://www.patchpersonnel.com/employment-survey/
About the author
CURT AHART is a senior IoT executive with an entrepreneurial approach and passion for customers, new product innovation and business growth. He has more than 35 years of experience in technology with leadership positions in business development, sales, strategy, strategic marketing, product management, engineering, M&A and analyst relations. Curt has served in these roles with startups to Fortune 50 companies. Mr. Ahart has extensive knowledge in wireless technologies, cloud services and IoT applications.
Related Articles
- Modernizing rod-lift automation for deviated wells (June 2025)
- The future of connectivity and automation in wellsite operations and workflows (January 2025)
- Digital transformation: Next-generation flexible control system modernizes wellsite operations (January 2025)
- Offshore Technology: Safer by technology (January 2025)
- Integrated automation technologies and proactive support network optimize drilling performance (December 2024)
- Digital control architecture optimizes plunger lift wells (November 2024)
- Subsea technology- Corrosion monitoring: From failure to success (February 2024)
- Applying ultra-deep LWD resistivity technology successfully in a SAGD operation (May 2019)
- Adoption of wireless intelligent completions advances (May 2019)
- Majors double down as takeaway crunch eases (April 2019)
- What’s new in well logging and formation evaluation (April 2019)
- Qualification of a 20,000-psi subsea BOP: A collaborative approach (February 2019)