The next generation of land drilling: Hybrid-powered rig combined with energy storage
As drilling contractors strive to reduce operating costs while meeting tighter emissions standards, generator sets fueled by natural gas, combined with energy storage, are revolutionizing how power is deployed in land drilling applications. Building on over a decade of proven technologies, Caterpillar is leveraging solutions specifically for drilling applications.
With a new system, the company is pioneering ways to help drilling contractors meet emissions reduction targets, capture and use flare gas, and lower the operation cost—all without sacrificing durability and performance. In Wyoming, Ensign Energy Services Rig 147 uses an innovative system that consists of three 1-MW Cat® G3512 generator sets fueled by natural gas, paired with lithium-ion batteries that store electrical energy, Fig. 1.
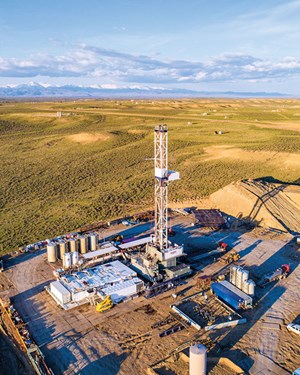
Engineers from Caterpillar are demonstrating savings with the hybrid solution, starting in April 2019. The results were compared to a diesel generator-powered system without energy storage and manual controls.
Caterpillar’s energy storage system is fully integrated, automated and optimized to efficiently power drilling rigs. Key components of the system that enable seamless operation between gensets and energy storage include a smart engine management system, bi-directional power inverters, and a Cat Microgrid Master Controller (MMC).
The company is taking technology (energy storage/microgrids) already developed within Caterpillar and bringing it into a different application—a containerized solution that’s rugged and suited for the rigors of drilling. The solution developed involves burning more natural gas as opposed to diesel fuel. That is a shift in the land drilling market that has been seen over the last couple of years.
The packaged solution is housed inside a 20-foot ISO container, minimizing the drilling platform’s footprint. Retrofit options are also available for the G3512 generator sets. “From a footprint perspective, the G3512 generator set is within a couple of inches of the footprint of its diesel counterpart,” says Christopher Berrie, a drilling account manager for Caterpillar. “That is a huge advantage for our customers, as alternative solutions are much larger and heavier, and would require a redesign of the drilling rig. The gas G3512 easily fits in the existing footprint of the rig.”
The natural gas gensets meet EPA non-road mobile emission limits and are paired with a lithium ion-based energy storage system connected to a 600-V transformer bay. The solution’s integrated control system automatically uses battery power when needed, and the automated controls require little to no interaction from an onsite operator.
The energy storage component includes a bi-directional power inverter that determines when it needs to charge or discharge. The power conversion system provides grid sync and forming functions. Meanwhile, the Cat MMC divides load between the energy storage system and gensets to optimize performance, service life, and economy.
TRANSIENT LOAD MANAGEMENT
Due to the demanding applications of drilling operations, customers require extremely responsive performance that diesel-powered systems are known to provide. With the energy storage system, gas engines can achieve comparable transient performance by responding to changing demands with quick surges.
In Wyoming, Ensign Energy Services Rig 147 solves this challenge with the battery energy storage system (ESS), enabling the generator and the battery to work in tandem. The battery is quick to pick up an energy load when the generator ramps up. As the generator continues to increase activity, the ESS reduces power, and the rig experiences a smooth power transfer. Energy storage allows the generators to run at higher loads (70% to 80% of nameplate capacity) while also using fewer generators to handle transient loads.
Therefore, if a quick load spike comes in, the batteries are going to take that power, as opposed to the engines. And the engines will continue to run steady with an easy load, because the batteries are assuming those high transient loads that are required to run the rig.
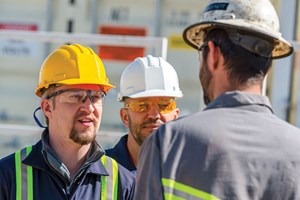
“I think this system could be the solution to several problems facing drillers today by lowering emissions from power generation, lowering fuel consumption and cost, and increasing performance of natural gas gensets,” said Ensign Energy Services’ operation manager, Nick Schaneman. “At Ensign, we pride ourselves as leaders of innovation and technology. We couldn’t be happier to partner with Caterpillar on this project to move the industry forward”, Fig. 2.
MULTIPLE BENEFITS
For drilling contractors and energy management companies looking to reduce operating costs, the advantages of the hybrid power solution are many and include:
- Lower greenhouse gas (GHG) emissions
- Reduced fuel consumption
- Reduced gas flaring
- Improved power quality
- Increased uptime
- Long-term efficiency
- Lower maintenance
- Noise reduction.
One of the major benefits is a significant reduction in fuel cost, achieved by utilizing readily available field gas, which eliminated approximately 28,000 gal of diesel fuel over 14 days. Using field gas, fuel savings from the hybrid solution totaled $1.4 million on an annualized basis. Additional savings are realized by eliminating the need to truck diesel fuel into the site.
Individual states, organizations, and site-specific locations are implementing new regulations to comply with stringent emission standards, which hybrid systems can help address. The energy storage system can help address these internal targets and demands by providing significant emission reduction benefits.
The analysis concluded that there was a 50% reduction in NOx emissions, compared to that of a drilling rig using diesel-powered generator sets in the same application. Meanwhile, total greenhouse gas (in C02e) emissions were 10% less than the baseline diesel-powered system, an important achievement for customers and sites with strict emission requirements.
Lifecycle greenhouse gases are further reduced if the system is powered with captured flare gas. The gensets run on a wide variety of gases, including captured field gas, which can significantly reduce the volume of well gas that is flared during drilling operations. Further, in instances where the gas requires treatment, Caterpillar has partnered with GTUIT to offer customers a comprehensive solution that utilizes GTUIT’s mobile gas processing systems. Field gas normally flared is, instead, gathered, then treated to be used in land drilling operations.
Improved uptime and capital efficiency were realized with the hybrid energy storage system, which is a huge improvement, in terms of uptime and providing operators instantaneous power.
When a generator set stopped unexpectedly, due to a fuel supply issue during tripping, the rig continued to work uninterrupted with power supplied by the energy storage system. The automated control system started an engine and brought another unit online. In the rare instance when the total power demand of the rig temporarily exceeds the combined rated power of all three G3512 generator sets, excess power demand is met by the energy storage system.
The lean-burn gas engines further reduce the operational bottom line, providing sustainable efficiency over the long term. Integrated automation technologies resulted in a 24% reduction of engine hours over 14 days, compared to using power systems with manual controls.
It is more efficient and cost-effective to run fewer engines at higher loads. The new technology eliminates the debate about how many engines to have online at a given time, because the system automates the process, thereby optimizing performance and reducing operating costs. The reduction in operating hours translates into less maintenance required to run the gas-powered generator sets.
The hybrid system components are easy to integrate into existing drilling rig and future new builds. In addition, the energy storage solution has demonstrated exceptional performance in diverse ambient conditions and altitudes; the drilling rig site in Wyoming is at an altitude of 7,000 ft, with wide temperature variations.
Overall, energy storage solutions integrated with natural gas, dual-fuel, or diesel technology can reinvent land drilling operations by lowering fuel costs, maximizing capital efficiency, and meeting lower emissions regulations. This hybrid system is a significant reduction in the total cost of ownership for drilling contractors and operators.
- Bringing geosteering efficiency to coiled tubing drilling operations on the North Slope of Alaska (March 2025)
- Overcoming real-time LWD limitations of longest horizontal drilling: A unique experience from Abu Dhabi (March 2025)
- Drilling advances: Could drilling save the world? (March 2025)
- Integrated managed pressure drilling system improves insights for enhanced performance (January 2025)
- The future of connectivity and automation in wellsite operations and workflows (January 2025)
- Digital transformation: Next-generation flexible control system modernizes wellsite operations (January 2025)