Unplanned downtime plagues the oil and gas industry. A 2016 report found that the industry averages more than 27 days of downtime each year, resulting in an average $38 million in financial per company. Some companies saw individual downtime losses amounting to more than $88 million. Reasons for the devastating financial losses are varied. Aging assets, retirement of experienced workers, and low prices resulting in diminished profit margins and limited investment contribute to the industry’s unplanned downtime.
Service loops are the heart of rigs in oil and gas fields, but they also require frequent maintenance and are susceptible to failure. A new rig technology from igus improves reliability of service loops and dramatically reduces downtime. The igus e-loop was designed specifically with a system that is more modular and robust, compared to other products, Fig. 1. With localized assembly teams, the motion plastics specialist can quickly assemble and deliver retrofit units to rigs around the world, including rigs in Texas, New Mexico, the Gulf of Mexico or anywhere in North America. “Practically, any oil and gas rig would see tremendous value in the e-loop,’’ said Jason Freed, igus’ Texas-based manager for oil and gas. “Besides a reduction in downtime, the e-loop is easier to maintain in the field and improves overall rig safety.”
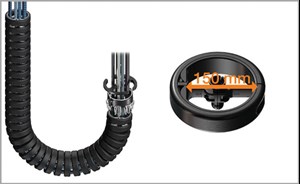
Traditional service loops lead to cable breaks and snags. The intent of the new design was to deliver a product that solves both of these issues. “The design idea for the e-loop came from a maintenance background,’’ said Tim Schneebeck, who spearheaded the e-loop product design and oversees the company’s oil and gas products division from igus’ headquarters in Cologne, Germany. “That is why modularity and product robustness are some of the key priorities of the e-loops. The others are safety, durability, simplicity and cost efficiency.”
One of igus’ first e-loop applications was installed at a potash mine in Canada, where workers frequently experience downtime, due to high winds and freezing temperatures. An 8-hr retrofit remedied the problem, Fig. 2. The following day, a blizzard that would have required a temporary shutdown before the retrofit, swept through Bethune in Saskatchewan, Canada, where the rig is located. This time there was no stoppage, no safety concerns and no snags on the rig. “Continuous operational time and prevention of downtime are paramount for drilling rig operations,’’ said Alan Kwoo of igus Canada, who helped design the energy chain retrofit. “Lost production means lost revenues.”
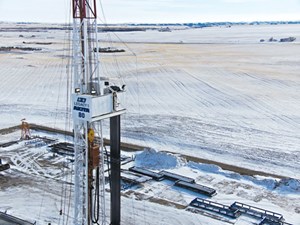
Initial analysis. Service loops are the energy source for drilling rigs. The loops power a large electrical drilling motor that is installed in a derrick, which supplies the torque to turn the drillstring. The system allows the drill to reach depths down to 10 km. Electrical service loops provide the power to the main motor and auxiliary power for other functions, such as lighting, lube oil heaters and cooling fans. They also power control, data and instrumentation functions.
Schneebeck said the e-loop evolved by analyzing service loops on top drive systems. “The major problem we see on these service loops is the potting, which makes the entire system of protecting hoses and cables rigid and inflexible. If you have a problem on just one of the loops, the whole system needs to be replaced,’’ Schneebeck said. Many rigs in the U.S. have simple service loops in which there is no potting around cables and hoses. “A simple bag protects and collects all cables and hoses,’’ Schneebeck said. “The more automated the rig gets, the more advanced the service loop gets—up to a full potted version.”
Potting is a glue-like substance that is poured into the protection hose for the cable. It is used as a strain relief and protects the system from water draining into the system. The non-modular system requires workers to change the entire loop if there are issues with just one cable. That means longer downtime, more NPT and less efficiency. “The major problem we see on these service loops is snags,’’ Schneebeck said. “One of the main problems with potting is that it is rigid and inflexible.”
The objective for igus was to design a modular system that reduces maintenance and cost, but also withstands snags, which are the most common failures for service loops. “Snags lead to cable damage, but handling the loops during a rig move is also a contributing factor,’’ Freed said. “Replacing items of the e-loop, bumper, links and cables having robust cable protection is probably the most unique thing of the e-loop.” Most service loops require continual maintenance. In addition, snags in service loops caused by high winds put workers in peril, as they attempt to untangle high-voltage cabling. The e-loop is also designed to drop-safe requirements. Dropped equipment is one of the biggest safety hazards in drilling operations. “Safety is one of the key priorities for e-loops,’’ Freed said.
Costly corrosion. Corrosion also leads to costly downtime in the oil industry. The total annual cost of corrosion is $1.3 billion in the oil and gas industry. Materials used in oil and gas exploration are exposed to some of the most aggressive industrial environments, leading to materials degradation that can harm the environment and threatens worker safety. Most service loops are made of steel, and, therefore, susceptible to corrosion.
The e-loop from igus solves the corrosion issue with its tech-up, cost-down components that are reliable in any weather, such as sea water, freezing temperatures, high winds, dust and heat, Fig. 3. “At its core, the e-loop is made from polymer parts, and the rope at its core is not metallic, and therefore cannot corrode,’’ said Scott Parker, the igus e-chain Industry Manager for Canada. “Hardware is made from stainless steel to avoid any corrosion on the fasteners. Because of the polymer base, there is no need for lubrication and no chance of the e-loop seizing in corrosive environments.”
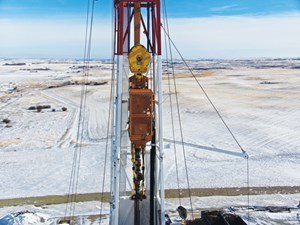
The self-lubricating properties of igus materials also dramatically reduce maintenance time and costs, expanding the operational capacity envelope of a rig. The technology combines the advantages of a polymer energy chain with a composite rope that possesses high tensile strength. The tensile forces are absorbed by the rope and passed through the mounting brackets into the support structure. The design relieves cables of any strain and ensures a defined cable bend radius. The modular e-loop also withstands vibrations and shocks. “igus has a long history of working in the offshore market, including having the first continuous flex-cable rated with DNV GL for offshore applications,’’ Parker said. “Because igus energy chain systems are polymer, they have been successfully used in many offshore applications. In this market, any product that is resistant to salt water and does not have to be maintained or replaced frequently increases production time while reducing costs.”
Safety concerns. Service loops also present numerous safety concerns. Repair work on rigs is quite dangerous, with multiple moving parts and components. There are also flammable chemicals and the possibility of natural gas or oil escaping from the well. The deadliest rig incident occurred in 1988, when 167 workers were killed at the Piper Alpha oil platform in the North Sea. Only 61 workers survived the tragedy.
In the application in Canada, high winds frequently foiled workers and forced operations to shut down. “We tried multiple ways to combat the wind messing with the service loop,’’ said Justin Amyotte, a field superintendent with AKITA, the drilling contractor. “We even went as far as to set up the rig in the direction of the predominant winds. We had a worker stationed on the floor watching the service loop at all times during high winds. We shut down, if conditions were too bad. The rig cables prior to the retrofit were wrapped, but wraps wrinkle and snag easily when they come close to the rig frame. That causes rips or pulls on the cables. The package containing cables and hoses is also costly to replace. Sometimes, the wind gusts and grabs the service loop and sends it into mast beams. Hopefully, the driller sees it and stops and fixes the snag. If he does not see it, the cords get damaged. That results in even longer downtime,” Amyotte concluded.
Untangling snags in cables that contain high-voltage wires is a hazardous job. “There was more than one occasion, where the service loop became snagged on the top drive, resulting in a dangerous overhead safety incident with high-voltage cabling,’’ said Darren Hrynkiw, a senior manager for K+S Potash Canada. “Multiple engineered safety solutions were explored, but in most cases, the solution presented other maintenance or sometimes even new safety concerns.”
Canadian application. The AKITA rig worked well in normal conditions, but the company considered retrofit options, due to the downtime caused by snags on the service line created by the strong winds. “The only other solution is a rigid chain/track type system,’’ Amyotte said. “These can be bent and damaged from tubulars or on a rig move. It also does not function well with ice. Once it is damaged, the rig would be down for repair.” Amyotte learned about the e-loop from Cologne, Germany-based igus, at an industry trade show in Texas.
The e-loop for the rig is about 70 ft, with a bend radius of 500 mm. It is mounted in the middle of the mast and can traverse the 136-ft tall mast by going 70 ft up and down from the center point, Fig. 4. AKITA’s rig was built in 2015. K+S, which has been in operation for 125 years, takes potash crude and further processes it into potassium chloride. Its mine in Bethune, the site of the AKITA rig, is the first greenfield potash mine in Saskatchewan in more than 40 years. AKITA scheduled to retrofit the rig with the igus energy chains in mid-January. The mine had been scheduled to be temporarily shut down in February before activating again in summer. The teams wanted the new energy chains in place for testing before suspending for the rest of the winter.
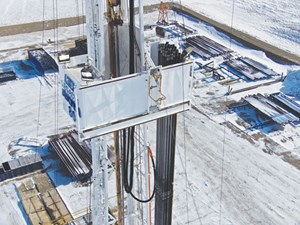
The retrofit required just 8 hr, and it took just 24 hr for the newly installed energy chain to take its first test. A blizzard swept through the region, bringing winds that reached 88 mph, along with snow and freezing rain. The storm knocked out power lines, brought 6 in. of snow and caused numerous power outages. Wind gusts were the highest ever recorded in nearby Regina in January. Temperatures fell to nearly 40°F below zero. Blizzards are no rarity in Bethune, but this particular storm packed a powerful punch.
The AKITA rig, however, with the newly installed e-loop, rolled on. No stoppages, no downtime, and no workers standing on the ground watching for a potential calamity. “Even in those extreme conditions, the loop functioned very well,” Hrynkiw said. “I am always pleased when an engineered solution can be found to eliminate a safety hazard, as this is far more effective than procedural safeguards. We expect little to no maintenance, given its design, and there are no productivity impacts with the installation of this protective system.” While the technology in this application was used for potash, Amyotte said any drilling rig could significantly benefit from the use the igus technology.
Lucrative potash market. While it is not as well-known as oil and gas, potash is one of the most widely used minerals in the world. The K+S mine is particularly noteworthy. It includes two of the top 10 deepest mines in the world. It produced the first tonnes of marketable potash during June 2017. The mine has an estimated life of more than 55 years, and the cost of construction reached more than $4 billion. It produces nearly 2 million tonnes of potash/year.
Dramatic downtime reduction. The objective in any production facility, whether it’s drilling for oil or other minerals, is to eliminate or reduce downtime. “Less downtime equals more productivity,’’ Amyotte said. “And less damage equals saving money.” When engineers at igus designed the e-loop, reducing downtime was the primary objective. One of the most challenging tasks for igus was testing to ensure that the e-loop would remain operational in the toughest conditions.
The e-loop certainly solved the issues for AKITA and K+S. Amyotte said the solution worked better than anticipated and was the most tenable answer to a problem that had faced them for years. “The only other solution available is a rigid chain/track type system,’’ he said. “These can be bent and damaged from tubulars on a rig move and don’t function well with ice. Once they are damaged, the rig is down while we try to fix it. The e-loop allows for freedom of movement while restricting bend radius. It also protects cables better and won’t cause down time, due to needed maintenance and repairs. That’s something that really appealed to us.”
- Coiled tubing drilling’s role in the energy transition (March 2024)
- Digital tool kit enhances real-time decision-making to improve drilling efficiency and performance (February 2024)
- E&P outside the U.S. maintains a disciplined pace (February 2024)
- U.S. operators reduce activity as crude prices plunge (February 2024)
- Drilling advances (January 2024)
- Driving MPD adoption with performance-enhancing technologies (January 2024)