What's new in production
If you’re going to be developing a field that requires hydraulic fracturing, you need a thorough understanding of the rock mechanics and the tectonic forces at play. This information is critical to reservoir depletion planning, well planning, and hydraulic fracturing design. Why?
I’m sure that most of our readers know that when you supply enough hydraulic force to fracture a rock, it’s going to take the path of least resistance. Assuming rock properties are relatively homogenous, then the tectonic forces acting on the rock will determine the path of least resistance for the frac fluid. The rock will fracture parallel to the plane of least stress. So, understanding rock properties and in situ stresses is critical to field development planning and hydraulic fracture design. You can’t control where the fracture will go. You can try to predict it, and perhaps you can measure it. You may get it right, or you may get it wrong. But Mother Nature always gets it right!
Sept. 10, 1969, Rulison, Colo. On this date, the U.S. Department of Energy attempted to stimulate the productivity of a gas reservoir by exploding a 40-kiloton nuclear device in a well, at a depth of 8,400 ft below ground in the Mesa Verde formation. The idea was that a huge cavern with a 160-ft diameter would be created, increasing the effective wellbore radius (rw). The device exploded successfully; however, the gas was (and still is) too radioactive to be used.
In addition, the wellbore failed to communicate with the main reserves. The thermonuclear reaction temperature of 50–150 million °F melted the rock and formed an impermeable glass coating around the entire chamber. So, Mother Nature couldn’t be fooled by brute force. Perhaps a bit more finesse would be required.
Feb. 16-20, 2020. NaturaFrac of Spokane, Wash., made its first public technical presentation about the experiments being performed at the University of Washington in Seattle. Why, you ask, should this be of interest to you?
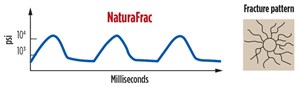
NaturaFrac has developed a fracturing concept, and associated fracturing equipment, to fracture rock formations using pulsed combustion technology, Fig. 1. This creates very strong pressure pulses downhole—strong enough to fracture rock like a chisel. These pressure pulses can be aimed in a direction perpendicular to the plane of least stress, and the resultant fracture happens so quickly that the rock doesn’t have time to turn the fracture parallel to the plane of least stress.
This technique can create near- and far-wellbore fractures in the direction selected—or omnidirectionally. The design parameters for this combustion fracturing technique are: 1) Maximum imparted stress (combustion pressure); 2) Rate of application of imparted stresses; 3) Total time of pulse; and 4) Time between pulses.These pulses are very short, very quick and very powerful.
The pressure pulses can be generated so quickly, because no moving or resetting of the downhole combustion tool is required to generate the next pulse. More importantly, the high rate of application of rapid stress pulses achievable by combustion (but not by hydraulics) is the slight-of-hand that fools Mother Nature into allowing fractures perpendicular to the plane of least stress.
These lab-scaled tests demonstrated the ability to pulse fracture artificial rock 24 in. in any direction, irrespective of the directional forces imparted on the sample rock, Fig. 1. Now, NaturaFrac will start field-size experimentation on in-situ rock. This scaled-up version will use rapid-fire pulses, each with the energy of a few dozen sticks of TNT. Their target is to fracture a natural rock formation about a few hundred feet (fracture half-length), in a direction perpendicular to the plane of least stress.
From an operational perspective, there are no explosives at the surface, thus reducing safety risks. The process uses currently available industrial gases and downhole conveyance techniques already used in the oil and gas industry. NaturaFrac also has designed its system to be used in conjunction with a typical proppant system.
The firm’s current work is being sponsored by the mining industry, as they could not get any traction in oil and gas (I’m actually a bit ashamed!). The mining use would be to omnidirectionally frac both injectors and producers in leach mining. Why injectors, you ask! I’ll save that for a future column. But I will be keeping an eye on this technology’s ability to fool Mother Nature. Now, I just need someone to help me find a way to fool Father Time!!
- Advancing offshore decarbonization through electrification of FPSOs (March 2024)
- U.S. oil and natural gas production hits record highs (February 2024)
- What's new in production (October 2023)
- FPSO technology: Accelerating FPSO performance evolution (September 2023)
- What's new in production (August 2023)
- A step-change in chemical injection (August 2023)
- Applying ultra-deep LWD resistivity technology successfully in a SAGD operation (May 2019)
- Adoption of wireless intelligent completions advances (May 2019)
- Majors double down as takeaway crunch eases (April 2019)
- What’s new in well logging and formation evaluation (April 2019)
- Qualification of a 20,000-psi subsea BOP: A collaborative approach (February 2019)
- ConocoPhillips’ Greg Leveille sees rapid trajectory of technical advancement continuing (February 2019)