PDC bit technology evolves to 4D cutters
PDC-shaped cutters continue to expand their footprint, and they are now used in all the applications drilled with PDC bits. Although the concept of a shaped PDC cutter is not new to the drilling industry, such cutters have become very popular in recent years, thanks to advancements in cutter-rock interaction modeling and cutter manufacturing technology.
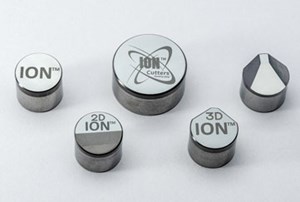
National Oilwell Varco (NOV) developed a line of 2D and 3D cutters in its ReedHycalog business unit. These two application-based geometries are combined with the company’s PDC cutter technology—enhanced with the latest leaching techniques—to drive consistent performance improvements. The 2D cutters are designed for shale applications, with a large chamfer added to the non-cutting side of the cutter. The chamfer reduces the contact surface between the cutter and cuttings, and acts as a flow channel, directing the flow toward that interface, to help with breakage of cuttings ribbons. The 3D cutters, on the other hand, are designed with a chisel-shaped tip that increases stress concentration on the rock to enhance fracture initiation and propagation.
ENTRY OF 4D CUTTERS
Using the lessons learned from modeling, and laboratory and field testing of those two cutters, NOV recently designed the ION 4D family of shaped cutters, Fig. 1. The unique geometry of these cutters consists of a chisel-shaped tip combined with a non-planar face geometry, which gradually transforms from a pointy tip to a large chamfer on the non-cutting side. A closer look at the cutter reveals similarities to previous shaped cutters, including an enhanced 3D cutter at the tip, combined with a modified 2D cutter on the non-cutting side.
The goal when designing the new line of 4D cutters was to build upon the proven advantages of 2D and 3D cutters while at the same time making a cutter suitable for a wider range of applications, such as medium/hard-brittle sandstone and medium/hard-ductile limestone to soft-ductile salt and soft-extremely ductile shale. The new cutters’ geometry was optimized for maximum rock cutting efficiency while maintaining cutter durability via analytical and numerical cutter-rock interaction modeling, finite element analysis, computation fluid dynamics, pressurized drilling tests on different rocks (including limestone, sandstone, shale and salt), as well as field runs in several applications.
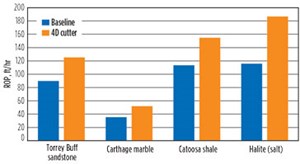
Full-scale pressurized drilling tests were designed specifically to evaluate the cutters’ performance in rock under simulated in-situ conditions, using an 8½-in. PDC bit. Tests on Torrey Buff sandstone, Carthage Marble, and halite (salt) were conducted at 1,500 psi, and the tests on Catoosa shale were performed at 1,800-psi borehole pressure. The results indicated that for the same weight on bit, the 4D cutters improved ROP in salt 61% and reduced mechanical-specific energy (MSE) 20%.
In addition, the ROP improvements in the other three rock types were between 29% and 40%. Resultant torque versus ROP was another performance criterion, which was investigated. ROPs of different-shaped cutters at certain torque settings were compared to evaluate the cutters’ efficiency. This was especially crucial to improving efficiency and aiming for higher ROP, in applications where surface torque was a limiter, Fig. 2.
Some examples of such applications include salt sections in deepwater Gulf of Mexico wells and long laterals in unconventional reservoirs, where frictional energy losses in the drillstring consume the majority of available torque at surface. The use of ION 4D cutters resulted in a 34% ROP gain in salt at the same torque, equivalent to a 22% reduction in MSE. The cutters also helped to achieve an ROP gain of 6% to 15% for the same torque in the other three rock types.
FIELD TESTING
Field testing of ION 4D cutters is an ongoing endeavor. An early vertical test was run in Pinedale, Wyoming, in an interbedded application consisting of sandstone, limestone, shale and salt, with traces of chert in the lower section and compressive strength ranging between 10 ksi and 30 ksi.
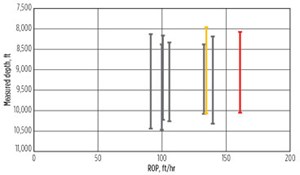
An 8¾-in. six-bladed bit with 4D cutters on the primary blades and the diamondback position drilled 1,974 ft in 12.27 hr, resulting in an overall average ROP of 160.9 ft/hr. This outcome was 45% faster than the average offset ROP of 111.3 ft/hr, and 15% faster than the fastest offset run, regardless of bit design. Also, when compared with the same NOV bit design without shaped cutters, this bit was 19% faster. The rig supervisor commented that the bit drilled significantly faster through the salt zones, as well as in the limestone section interbedded with sandstone and shale. This high ROP was achieved while maintaining a dull grading of 1–1, Fig. 3.
In another run in the Williston basin, 4D cutters were tested in the cone area of an 8¾-in. Tektonic six-bladed bit, which was used to drill the top-hole vertical section—an interval of 6,525 ft—and reach TD at an average ROP of 191.9 ft/hr. The run included drilling through layers of interbedded sandstone, siltstone, shale, halite, limestone, dolostone, anhydrite, and mudstone. ROP in this application was 7% faster than the offset, saving 2 hr of rig time. The 4D cutters came out of the hole with no chipping and no wear on the diamond table. There was only minimal wear on the tungsten carbide substrate. This was attributed to rubbing against the formation, due to the bit’s high instantaneous ROP.
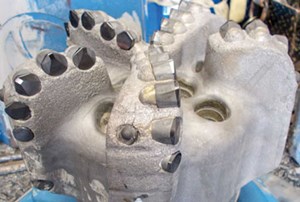
Two additional test runs occurred in two different wells in the Powder River basin, Wyoming. Both tests were done using the same five-bladed Tektonic bit body with 4D cutters placed across the bit profile, Fig. 4. In a lithology of mainly sandstone and shale, one of the bits drilled 7,149 ft at 397.2 ft/hr to complete the section in 18 hr. The ROP for this run was 25% above the rig’s offset average. In the other well, the bit only needed to drill 4,301 ft to complete the interval at an ROP of 623 ft/hr, 13% above the rig’s offset average.
CONCLUSIONS
Since the introduction of PDC bits in the 1980s, the industry has shifted away gradually from roller-cone bits and almost entirely to PDC bits. However, it was only in the past decade that PDC bits truly overtook the market in applications, where roller-cone bits were traditionally the bit of choice, due to the hard and interbedded nature of the rocks. The major factors contributing to this paradigm shift were advancements in PDC cutter manufacturing and leaching technologies. Those improvements, combined with advancements in cutter-rock interaction modeling and testing, have resulted in development of new, robust, shaped cutters.
The superior performance of the new shaped cutters in field applications is backed by thousands of hours of research and development. This surge in R&D is driving interest in shaped cutter technology and inspiring continued new product development to create geometries for varying well types and downhole conditions.
- Applying ultra-deep LWD resistivity technology successfully in a SAGD operation (May 2019)
- Adoption of wireless intelligent completions advances (May 2019)
- Majors double down as takeaway crunch eases (April 2019)
- What’s new in well logging and formation evaluation (April 2019)
- Qualification of a 20,000-psi subsea BOP: A collaborative approach (February 2019)
- ConocoPhillips’ Greg Leveille sees rapid trajectory of technical advancement continuing (February 2019)