Immiscible mixed gas enhances EOR economics, increases permeability in swelling clays
A mixed gas consisting of CO2, N2 and minor amounts of carbon monoxide (CO) has been found uniquely applicable to increasing matrix permeability, enhancing the rate of oil recovery, decreasing the Mcf/bbl ratio, operating at pressures lower than typical CO2 MMP, and mobilization of asphaltenes while operating at immiscible conditions.
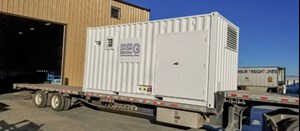
Until recently, CO has never been considered beneficial to recovering oil. In addition, there is concern about its toxicity and potential corrosiveness. Laboratory work over the last five years has shown utilizing diluted CO, as part of a mixed gas displacement process, recovers nearly as much oil as CO2, but at a faster rate. CO also can enhance permeability in shale reservoirs and mitigate the effects of any asphaltene precipitation. Handled properly, it is safe. The method has already received a permit for pilot testing in the state of Wyoming, under a simple sundry notice, after satisfying all safety concerns. With the proper additive, CO is not corrosive to oilfield tubulars, due to its being a reducing agent rather than an oxidizing agent.
EOR techniques that can be applied to shale oil are being studied and field tested. Both miscible CO2 and light hydrocarbons are being evaluated. However, some initial results proved disappointing, due to loss of the CO2 along fractures to adjacent wells, high compression costs, large volumes of gas required per barrel of oil recovered, extremely low matrix permeability, and/or limited recovery factors. Additionally, Devegwoda (2018) has suggested asphaltenes may result in pore plugging of shale oil reservoir. Alternately, at least one company has reported on the successful application of CO2 for EOR of a shale oil.
Additional applications for the mixed gas are: heavy oil recovery at or near reservoir temperature and pressure, augmentation of poorly performing CO2 floods, lowering capital and operating costs for new CO2 floods, and extending the operating life of an aging waterflood.
MIXED GAS COMPONENTS
The mixed gas used in these experiments consisted of CO2 with minor amounts of N2 and CO. CO has been identified as the “workhorse” in this mixture of gases. CO is far safer to handle than H2S, both in the laboratory and in the field. In fact, it is 15 times safer than H2S, which the oil industry has learned to handle safely. Furthermore, unlike H2S, CO has a density similar to air, so it does not concentrate or collect in low spots.
Carbon monoxide is a unique, triple-bonded, molecule. The triple bond allows shifting of the electron cloud between both carbon and oxygen atoms with higher electronegativity residing on the carbon atom. This triple bonding has similarities to certain bonds within an asphaltene molecule, plus carbon monoxide’s polarity may also interact with asphaltene’s functional groups. CO’s molecular diameter is 50% smaller than CO2’s, resulting in faster movement through a reservoir and greater access to the oil-rich, lower permeability zones.
Carbon monoxide is 44 times less soluble in water than CO2 at 70 psi and 100°F. Thus, in mature waterfloods, CO may migrate from the more permeable watery zones into the tighter, low-permeability, poorly swept zones, thereby recovering bypassed oil.
Due to carbon monoxide’s critical temperature of -222°F, the mixed gas only exists at immiscible conditions. Thus an immiscible, low-pressure, mixed gas was investigated to determine its potential technical and economic advantages as compared to pure CO₂.
Carbon monoxide has been found to be more soluble in aromatic ring compounds than paraffinic compounds (Luhring, 1989, and Koelliker, 1993). Rising bubble testing, WAG studies, and slim tube testing have shown the potential for CO to mitigate asphaltene-related problems and to recover heavy, asphaltene-rich crudes at low reservoir temperatures and pressures. If asphaltene-type molecules are blocking the shale oil pore throats (Devegwoda 2018), injecting CO may remediate this problem.
Swelling clays (smectite, smectite/illite, montmorillonite, and bentonite)—common to shale oil reservoirs—have significant amounts of ferric oxides/hydroxides both interlayer and especially on clay edges. Thermodynamics strongly favor CO as a reducing agent for ferric oxide/hydroxide molecules and conversion to ferrous oxide (wustite), with subsequent release of adsorbed, immobile water of hydration and a decrease in diameter of approximately 1,161 pm to 218 pm.
Since the swelling clays most likely occur on both sides of a pore throat, the total increase in the effective pore throat diameter would be over 90%. CO, coupled with certain other additives, has shown the potential to retard tubular corrosion (Cabello, 2013) in the presence of CO₂ and water, due to the reducing capabilities of the CO acting on oxidized tubular goods.
Recovery of oil by pure CO2, versus the mixed gas (CO2, N2 + CO), was evaluated at different conditions and concentrations. Six different oils, ranging in API gravity from 18° to 42°, were tested at 38% to 105% of CO2 MMP’s.
MIXED GAS DEVELOPMENT
Five years of development, testing, and subsequent patenting of this mixed gas technology strongly supports the potential for EOR/IOR applications. The mixed gas has been subjected to testing of interfacial tension (IFT), linear corefloods on preserved core, column testing, slim tube testing, rising bubble testing, WAG testing, and all supporting analytical requirements.
Interfacial tension. IFT’s of a crude oil and formation water, after CO introduction, were determined by Surtek, Inc., a third-party laboratory, using the du Noüy ring apparatus. Test results demonstrated a 16.5% reduction in IFT at atmospheric conditions. At higher pressures, the IFT reduction will increase due to the increased solubility of CO in oil and water. Lower IFTs allow the conversion of oil droplets to oil “worms” that can transect smaller pore throats and increase oil cut.
Packed column. Packed column experiments were conducted by Markey (2015). For each experiment, a 17-cm × 2.5-cm column was filled with a mixture of 95% 140-150 mesh sand and 5% (v/v) bentonite. The column had 35% porosity and an absolute permeability of 108 md to 100,000 TDS brine. Injecting a 50,000-ppm brine at 1,000 psi and back pressure of 500 psi dramatically lowered the permeability to 4.5 md. After the brine injection, the column was “produced,” using gravity and vacuum-aided drainage, and approximately 2 PV of CO were then injected and allowed a 48-hour soak. When a second slug of 50,000-ppm NaCl was injected subsequently, the effective permeability had increased to 8.7 md (a 193% increase), Fig. 1.
The effects of CO on permeability having three phases present (50,000-ppm brine, residual oil, and CO) were tested on a fresh column. Injection sequence consisted of brine injection followed by injection of a 36° API, 3.9-cp oil. The packed column was placed under a vacuum, then flushed with 3+ PV of the 50,000-ppm brine solution to achieve residual oil saturation. Next, 2+ PV of CO were injected and allowed to soak for 96 hr. Finally, 3 PV of the 50,000 TDS brine were again injected, and the effective permeability measured to compare pre- and post- CO treatment effects.
Figure 2 shows post-CO treatment effects on the three-phasephase system (oil, water, CO). The pre-CO absolute permeability was 4.5 md, and the effective permeability for the oil was only 1.8 md. However, post-CO treatment, the effective permeability to brine, in the presence of both residual oil and residual CO, increased to 8.8 md. These tests demonstrated the increase in effective permeability caused by CO increasing matrix permeability.
Linear core flood testing conducted by Surtek, Inc., showed a significant increase in core permeability, both during and after CO injection. Fluids were injected into a 12.5 cm × 2.5 cm core plug held in a stainless-steel core holder. A preserved Cretaceous sandstone core, from a depth of 9,359 ft., having spotty oil shows, and a permeability of 10 nanodarcys, was utilized. Core mineralogy was 89.2% quartz, 4.2% kaolinite, 2.2% siderite, 1.6% chlorite, 1.4% smectite/illite, and 1.1% illite/mica. The smectite/illite is the primary swelling clay. (Shale oil formations can have 20+% swelling clays vs this 1.4%). An 18,143-ppm TDS brine, simulating formation water, was injected at a pressure of 1,000 psig against a 400-psig back pressure.
The initial absolute permeability of the core was 10 nd when saturated with formation water. A total of 2.8 pore volumes (PV) of CO were then injected and soaked for 48 hr, followed by another 1.55 PV of CO. The core was then flooded with formation water, and the effective permeability was found to be 30% higher than the previously measured absolute permeability. The cycle of CO injection, shut-in, CO injection was repeated a second time.
After the second cycle, the effective permeability to formation water was 50% higher than the initial absolute permeability. The effective permeability to CO, at irreducible water saturation, also increased during CO injection. It was three times higher during the second cycle than during the first cycle. This indicates successive treatments of CO injection continues to increase matrix permeability with no evidence of clay migration.
Slim tube testing. A total of 32 slim tube tests were conducted at various pressures with oils ranging from 18° to 42° API gravity. The tests required 5-20 hours of constant monitoring. The slim tube consisted of a 60 ft., ¼-in. diameter, coiled, stainless steel tubing packed with a mixture of 140 to 230 mesh to achieve typical permeabilities from 0.8 to 2.5 Darcies. Both the rate and volume of produced fluids were recorded.
The slim tubes were prepared by injecting 1.25 PV of as-received crude at reservoir pressures and temperatures. Mixed gas was injected into the oil-filled slim tube at 0.1 ml/min. At the completion of a test, the slim tube was cleaned with hexane or hexane-methanol-hexane, and the oil content in the cleaning fluid was measured. Injection pressures varied from 38% to 105% of the oil’s CO2 MMP. Slim tube testing results strongly demonstrated the advantage of employing the mixed gas for EOR/IOR as compared to pure CO2 under immiscible conditions. A few representative, low-pressure, tests using a 36°API paraffinic oil with minor aromatics, are discussed below.
As seen in Figure 3, at 38% of MMP, the mixed gas recovered 63% of the OOIP when 0.6 PV had been injected- vs only CO2’s 28%. Similar results were obtained at 47% of MMP, where the mixed gas recovered 73% of OOIP at 0.6 PV injected vs only 40% for CO2.
Another set of slim tube tests demonstrated the effectiveness of pure CO to achieve rapid oil recovery. In one run, CO was injected until gas breakthrough at 0.4 PV injected. An additional 0.6 PV of pure CO2 was then sequentially injected. Results were compared to a pure CO2 flood. As shown in Figure 4, the CO, being a smaller molecule, and having some solubility in oil, resulted in a very early recovery of oil before gas breakthrough. The CO/CO2 process recovered the same amount of oil as the pure CO2 process, but at a much faster rate. Thus CO was again shown to be the “workhorse” leading to the increased rate of oil recovery-in addition to its
other benefits.
Another slim tube test was designed to investigate recovery of residual oil after waterflooding. A slim tube was filled with oil and formation water injected until the oil cut was 1%. Mixed gas injection results were compared to pure CO2. Both the mixed gas and pure CO2 lowered the residual oil saturation from 38% to 8%. However, the mixed gas recovered the oil about two times faster than the CO2. This test suggests economic extension of an ageing waterflood, at existing reservoir pressures, may be feasible.
Based on these and other slim tube tests, the authors are confident that the mixed gas of CO2 + N2 + CO can achieve a lower-pressure, faster, more economical oil recovery, as compared to pure CO2. The slim tubes did not contain any swelling clays. Thus, field applications for reservoirs containing swelling clays should enhance project economics by increasing the rate of oil recovery while employing only 50% of the injected gas.
ON-SITE MIXED GAS PRODUCTION
Mixed gas can be generated on-site from most any hydrocarbon source at a cost comparable to purchasing CO2. Either gasification processes or EEG’s patented internal combustion technology are available to produce the mixed gas, Fig. 5. Additionally, “green” electrical energy is a byproduct, since all greenhouse gas emissions go downhole and are recycled. Since only 4-5 Mcf/bbl recovered is required compared to 10-12 Mcf/bbl for CO2, project economics are favorable.
APPLICATIONS
Based on geochemical principles, thermodynamics, and this extensive testing, CO has been identified as the major asset or “workhorse” for potentially increasing project economics of various EOR/IOR projects. Application of CO contained in the mixed gas can benefit several different types of oil reservoirs in the following manners.
Shale oil EOR. Increase matrix effective permeability by 1.8 to 4 times; operate at lower pressures to avoid gas losses; use 50% less Mcf/bbl recovered (as compared to pure CO2); recover oil 1.5-3 times faster; increase oil cut, due to lower IFT; access smaller pore throats and tighter areas by the CO; remediate asphaltenes if blocking pore throats, use mixed gas as solvent; and achieve faster, lower cost, higher EUR, utilizing either Huff-n-Puff or displacement. Heavy oil recovery. Recover heavy oil at, or near, natural reservoir temperatures and pressures; remediate formation damage caused by prior introduction of steam; lower operating and production costs, due to need for minimal to no heating; decrease produced oil viscosity; help protect tubulars; mobilize asphaltenes; minimize the Mcf/bbl recovered. Enhanced waterfloods. Extend economic operating life of ageing waterfloods; lower residual oil saturation; operate at existing waterflood pressures; increase effective permeability if swelling clays are present; lower IFT to increase oil cut. CO2-type floods. Enhance economics of typical CO2 floods by operating at pressures of 50–70% of CO2 MMP; recover oil 1.5–3 times faster; remediate any formation damage; increase matrix effective permeability if swelling clays are present; mobilize asphaltenes; utilize 50% less Mcf/bbl recovered (compared to pure CO2).
ACKNOWLEDGEMENTS
Portions of this article were published previously in SPE paper 179540. Intellectual property presented is protected under an issued patent and several patents pending.
- Shale technology: Bayesian variable pressure decline-curve analysis for shale gas wells (March 2024)
- U.S. oil and natural gas production hits record highs (February 2024)
- When electric meets intelligence: Powering a new era in hydraulic fracturing (January 2024)
- Next-generation electric fracturing system improves efficiency, ESG performance (January 2024)
- Going global with unconventionals (December 2023)
- Singlet oxygen-generating treatment technology achieves sustainable operations, helps operators meet production goals (November 2023)