What’s new in artificial lift?
So, what is new in artificial lift? Each year, for over three decades, the keepers of these pages have asked this question. They have searched far and wide to report on new products and technologies that help improve well performance and reduce lifting costs.
Artificial lift is recognized as a large and technically important segment of the oil and gas industry. Underscoring its importance are the numerous mergers and acquisitions that have altered the landscape of product and service providers.
Hence, it may be helpful to pause and not only ask “what’s new?” but also to ask “who’s new?” Or, at least, “who’s who in artificial lift?” To that end, we offer the following on the M&A race that has reshaped today’s artificial lift playing field.
WHO’S WHO IN ARTIFICIAL LIFT?
Hold on to your “nodding horses.” They’re off and running. And, here’s how the race is shaping up.
In 1980, Hughes Tool Co. acquired the Centrilift line of electric submersible pumps (ESPs) from Borg Warner. Hughes also acquired Submergible Oil Services (SOS) in 1980 and combined it with Centrilift. In 1987, Baker International Corp. and Hughes Tool Co. merged to form Baker Hughes Inc. In 1997, Centrilift strengthened its capabilities with the acquisition of Oil Dynamics, an ESP competitor with specialized technology.
Starting in 2007, GE was gaining a sizable toehold in the oil and gas industry through strategic acquisitions. In 2011, GE acquired Wood Group’s well support division, which was comprised of three business units – ESPs, pressure control (surface wellheads and trees) and logging services. This represented GE’s first major position in the artificial lift business (Wood Group ESP).
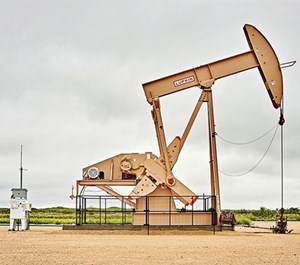
Then in 2013, GE acquired Lufkin Industries, a provider of artificial lift technologies with a leading position in rod lift systems that dates back almost a century, Fig. 1. Through its long history, Lufkin expanded its artificial lift offerings with acquisitions of companies and/or assets from Delta-X, Nabla, American Manufacturing, Churchill, International Lift Systems, Petro Hydraulic Lift Systems, Pentagon Optimization Service and Quinn Oilfield Supply. Combining Wood Group ESP with Lufkin created a major presence for GE in the artificial lift business.Fast-forward to 2017, when Baker Hughes and GE Oil & Gas combined to form BHGE. Since both GE and Baker Hughes were major players in artificial lift, their merger established the overall global leader in artificial lift technologies. Their hold on the ESP business is significant, since Baker Hughes led the ESP market and GE held the third-place position.
The new company’s portfolio includes ESP systems, rod lift systems, horizontal surface pumps (HSPs), progressive cavity pumps (PCPs), and gas lift systems, along with monitoring and control systems.
Some might say that BHGE wins the gold “pumpjack” award in the artificial lift race. But, there are others in the field, and the finish line is a moving target.
Borets. Established in Russia more than 100 years ago, Borets is a leading global provider of ESPs. The company dominates the ESP-driven market in Russia. Headquartered in Dubai, Borets has 11 manufacturing facilities in five countries, and has a sales and service presence in over 15 countries.
In 2008, Borets acquired 62% of the ESP division of Weatherford International. Weatherford retained 38% ownership. In 2013, Weatherford sold its share of the joint venture to Borets and exited the ESP segment of the artificial lift business. While Borets’ focus has been on ESPs, they also provide HSPs, PCPs, surface control and monitoring systems.≠
Dover Artificial Lift (now part of Apergy). Dover Corporation is an American conglomerate manufacturer of industrial products, founded in 1955, which built a significant presence in artificial lift through numerous acquisitions. The company’s artificial lift portfolio comprised many leading brands, such as Norris, Harbison-Fischer, Theta Oilfield Services, PCS Ferguson, Alberta Oil Tool, UPCO, Pro-Rod, Oil Lift Technology, and Spirit Global Energy Solutions.
In October 2014, Dover Artificial Lift announced that it had acquired Accelerated Companies, whose core offerings included ESPs, jet pumps, gas lift systems, surface pumping and modular process systems. In 2017, Dover added PCPs to its portfolio with the acquisition of PCP Oil Tools of Argentina.
In December 2017, Dover Corp. announced its plan to spin off its upstream energy business into a standalone, publicly-traded company. This month a new company, Apergy Corp., was formed. Apergy’s principal products consist of Dover’s artificial lift equipment and PCD cutters for drilling. Apergy also provides a full automation offering, consisting of equipment, software and IoT solutions for downhole monitoring, well site productivity enhancement and asset integrity management. Apergy has a global presence, with operations in the United States, Canada, Latin America and the Middle East.
Endurance Lift Solutions. Endurance was formed in 2014 and acquired the assets and operations of John Crane Production Solutions (JCPS) in October 2016. Following the acquisition of JCPS, Endurance combined operations with two related companies to create a single artificial lift company providing reciprocating rod lift and plunger lift applications. The company operates as a subsidiary of Synergy Energy Holdings.
Halliburton was founded in 1919 and is considered the world’s second largest oilfield services company. For years, Halliburton has had a presence in the artificial lift and production services segment of the oil and gas industry, but was never considered a “major” player in artificial lift. In 2012, Halliburton acquired a small ESP company, Global Artificial Lift, formed in 2008.
In July 2017, Halliburton announced the acquisition of Summit ESP, a leading provider of ESP technology and services. Now, Halliburton Artificial Lift offers several key lift methods, including ESPs, HSPs, PCPs, and the associated power, control and monitoring systems.
Liberty Lift Solutions. Liberty Lift’s core management team consists of former Weatherford and Lufkin executives, with more than 125 combined years in the artificial lift business. The company is focused primarily on beam pumping systems. However, their product line has expanded to provide a solution for all stages of the production lifecycle.
In addition to conventional and enhanced geometry beam pumps, Liberty Lift has introduced Long Stroke pumping units, gas lift systems for both tubing and wireline retrievable equipment, and a line of jet pumps with JJ Tech that incorporates a surface power fluid system, prime mover, surface pump and downhole jet pump.
Schlumberger was founded in Paris in 1926, and is recognixed as the world’s largest oilfield service company. In 1998, Schlumberger acquired Camco International (gas lift and gas compression), which included REDA ESP pumps. Then, in 2012, Schlumberger initiated a strategy to bring together leading sucker rod pump companies in North America to expand its artificial lift offering.
In 2013, Schlumberger acquired several companies, including Shores Lift Solutions, which provides beam pumping units, sucker rods, optimization solutions and field services.
In 2014, Schlumberger acquired 12 firms, including ESP deployment technology developer ZEiTECS (once wholly owned by Shell Technology Ventures), KUDU Industries (PCPs), Don-Nan (a downhole rod pump manufacturer and pump service provider), Grimes Sales and Service (the unique HG curved-beam pumping units), and others. In 2015, Schlumberger acquired Cameron International, which had a small footprint in the artificial lift business.
Schlumberger now delivers leading technologies across a wide artificial lift spectrum, including rod lift, ESPs, HSPs, gas lift and PCPs.
Valiant Artificial Lift Solutions. Formed in 2016, Valiant is led by Gareth C. Ford, former president and CEO of Wood Group ESP. Valiant’s focus is on ESPs, HSPs and PCPs. The company has an operating presence in Oklahoma, the Permian basin, and Bogota, Colombia.
Weatherford. On most scorecards in the first decade of this century, Weatherford International emerged as the industry’s artificial lift leader, in terms of scope of product offerings and market share. Then, as described, the artificial lift landscape began to change.
Its product offerings include automation and control, capillary injection systems, Corod continuous rod systems, conventional sucker rods, rod guides, gas lift systems, jet pumps, hydraulic piston pumps, plunger lift systems, PCPs, long stroke pumps, beam rod pumps and subsurface rod pumps. As mentioned, Weatherford exited the ESP segment in 2013.
TURNING THE CORNER
The discussion of these companies is meant to serve as an indicator of how the industry is changing. Obviously, there are many more players on the global artificial lift field. We survey close to 100 companies each year for this feature alone.
With the development of the shale oil boom, North America has been the primary driver for artificial lift demand and recent M&A activity. According to ADI Analytics, in the U.S., over 95% of oil wells require artificial lift, with the bulk of those utilizing rod pumps. Artificial lift used in Asia is fairly even across ESPs, PCPs, rod pumps and gas lift. Russia relies heavily on ESPs. Rod pumping is the leading artificial lift method globally, followed by gas lift, ESPs and PCPs. Figure 2 illustrates the share of these artificial lift units worldwide.
While providing our perspective on “who’s who,” we offer the following on “What’s new in artificial lift?” for 2018.
BEAM/ROD LIFT DEVELOPMENTS
The basic beam rod pump system consists of three components: a surface pump, a connecting rod string, and a downhole plunger pump.
BHGE’s Lufkin Gen 2 beam unit. This is a new generation of the iconic beam pumping unit (BPU) introduced by Lufkin in 1925, Fig. 1. The units have been redesigned and standardized—making them safer and easier to install—while the focus remains on reliable technology that enables operators to produce efficiently and cost-effectively.
The gear reducer design has been improved with new lifting features to increase safety. The structural bearing-to-load ratio has been improved by more than 21%. Nord lock washers were added to maintain torque on connections, and slots were added in many areas to make assembly quicker. The crankshaft is larger in diameter, the crank has sleeved holes, and there is more space between crank pin holes for longer run life. Tick marks have been added to the crank to aid visual weight location for proper balance. Counterweights have been reshaped to provide both minimum and maximum weight on the crank, with no auxiliary weights required. This reduces the need for additional weight inventory. Super nuts are installed on crank pins to avoid the use of hammer wrenches and their related safety challenges. Lubrication wipers are standard issue in all gear reducer sizes for proper lubrication, even at very slow speeds.
Coiled rods provide strength and extended lifespan. The couplings of conventional rods often create a concentrated side load where they contact the tubing. This can lead to premature wear. Coiled rod has proven to significantly reduce side loading and frictional rod-on-tubing wear by spreading the contact points across a longer area of the rod and tubing. Lightning Production Services (LPS) provides coiled rod for mature conventional and unconventional wells. Coiled rod offers superior strength and an extended lifespan, due to increased corrosion resistance under alternative loads and high service loads in both rod-pumped and PCP wells.
Shot peening is an integral part of the LPS coiled rod manufacturing process. The technique helps increase the rod’s surface tension, reducing surface imperfections that are susceptible to corrosion that can lead to reduced run life.
With complete control of the steel mill, tight surface inclusion specifications are driven to high standards, which help prevent the acceptance of micro-constituents that reduce the strength of the metal. It is important to begin with the highest quality of steel possible, which means LPS eliminates metals and rods with surface inclusions that may increase corrosion related failures. The steel is produced with clean manufacturing practices that create a reduction in non-metallic inclusions and an improved capacity to resist contaminated products. The process creates a superior product, even before quench and tempering operations begin.
LPS coiled rod is engineered and tested at an in-house laboratory. A series of trials is conducted to verify the rod’s enhanced properties, including the National Association of Corrosion Engineers test, in addition to full-scale fatigue analysis in neutral (air) and corrosive (CO2 and H2S) environments. Finally, an engineer reviews the rod string configuration to ensure optimized results in the specific application.
LPS coiled rod is available in several configurations. To eliminate mishandling or improper installation, LPS has service locations strategically placed in major oil and gas basins. The company’s crews are experienced in testing with Flushby units and perform all tasks necessary for proper installation, including onsite welding, Fig. 3.
LINEAR LIFT PUMPS
Linear lift units can provide a cost-efficient, compact, lighter-weight alternative to traditional beam pumping units in many multi-pad, horizontal well applications.
New long stroke pumping unit. Forland Services has introduced a new generation of long stroke pumping units that includes a switched reluctance drive (SRD) and integrated control system, Fig. 4. The units also feature a planetary gear box and open-looped chain/travelling sprocket transmission system, inner-tower counterweight system, and a flexible load belt. The control cabinet includes an integrated power supply, SRD/PLC unit, human machine interface (HMI) module, physical indicators/buttons, and optional remote access module.
Unlike common induction motors, the SRD has large overload capacity and frequent commutation ability that makes it ideal for adapting to field operating conditions. The motor commutation time can be pre-adjusted according to load and stroke, so that the reversing of the polished rod is softer and endures less mechanical impact.
These new long stroke units can achieve independent upward and downward stroke speeds without a variable frequency drive (VFD). This is especially beneficial for heavy oil wells, horizontal wells and wells that are prone to gas lock. Additionally, stroke lengths are automatically adjusted, and the working region of the stroke can be customized with no sacrifice to production capacity.
The integrated SRD functions similarly to a VFD for step-less motor frequency control. This means the upward and downward speeds are individually controlled through the forward and reverse rotary frequency of the drive system.
The control system provides upper (lower) half stroke and the upward (downward) stroke speed adjustment via the HMI, and monitors operating parameters and the polished rod position. It detects over-speed, over-load conditions or under-load shutdown. The smart features provide controller pauses, false alarms and other customizable operator-defined faults. Manual jog up/down of the drive system is possible through the HMI, as is shutdown and restart.
Competitive motor-driven units must complete a defined full stroke. If well conditions and fluid volumes change, their stroke speed must be altered via pre-configured VFD settings to adapt to changes in fluid displacement. The Forland unit automatically adjusts its speed to changing load conditions. In conditions where other units might cause the downhole pump to stick, the Forland unit allows the adjustment of stroke length, avoiding downhole pump damage. It also can narrow the operating range in upper (or lower) sections of a full stroke.
Besides slower operating speeds, which lead to fewer pump cycles and increased pump life, the unique selectable stroke section and independent controllable upward/downward speed make the Forland unit highly efficient. It is able to solve complicated issues in high deviation, high fluid volume, high water-cut, and heavy oil conditions, where other forms of lift tend to cause excessive down time. The 306-in. stroke Forland unit can handle 1,500-bpd displacement at a pump depth of 6,000 ft and 900 bpd at a pump depth of 8,000 ft. This flexibility benefits operators, who experience a high number of failures or costly interventions.
Long stroke units in deep horizontal wells.It can be difficult in deep, high-rate horizontal wells to transition early to rod pumping, to lower OPEX. According to some manufacturers, long-stroke units have high theoretical displacements and should be able to attain 500 to 800 bpd at 100% efficiency to depths of 10,000 ft. In reality, this is not always achieved, which can cause deep, high gas-to-liquid ratio wells to struggle, leading to poor performance.
These types of wells typically experience high initial production rates followed by a rapid decline. High gas-to-liquid ratio increases the risk of gas interference and foam generation. In some cases, engineers are forced to use smaller pumps and equipment because of restrictions caused by smaller-diameter casing selected to minimize drilling costs. Generally, wells at deeper depths are prone to excessive rod loads, increased power requirements and higher frequencies of wear holes in tubing-related workovers.
In addition to these challenges, slug flow behavior from the horizontal has proven to be the root cause of low volumetric efficiency and underperformance in rod pumping. This causes cyclical periods of gas interference, reducing pump reliability, efficiency and capacity. The nature of slug flow encourages solids production and transports solids that can damage the pump. Ultimately, the compounding effect of these behaviors limits drawdown and reserves, and increases operating costs.
The HEAL System (a joint venture product from Production Plus Energy Services and Schlumberger) is a patent-pending, downhole solution that seamlessly joins the horizontal as part of a standard well completion. Designed to perform for the life of the well and with no moving parts, the system is made up of a floating seal, a sized regulating string and the Heal vortex separator.
The system mitigates slug flow in deep wells that provides complete pump fillage in rod lifted wells, Fig. 5. It is designed to address three major components of artificial lift system inefficiency: 1) the system conditions flow to minimize the causes of slugging as much as possible; 2) efficiently lifts fluids from the horizontal to the vertical; and 3) controls solids production and movement in the wellbore. With slug flow managed, long stroke pumping units can produce with high volumetric efficiency and system reliability, at production rates of 500 to 600 bpd below 6,000 ft. When the HEAL System is installed at initial completion, natural flow can be extended beyond what is conventionally possible. This can close the gap between natural flow and rod pumping, usually filled by gas lift. It makes earlier and simplified transition to rod pumping with lower OPEX a possibility.
HEAL Systems are field-proven in over 300 installaltions across North America, with over 60 of those in the Permian basin. The system has proven the high-rate capacity of long stroke pumping units is possible in the field. A system installed in the Permian with a pump depth of 7,900 ft, TVD, demonstrated reliable 300-to-400-bpd capability, Fig. 6. An installation in the Montney shows a similar capacity for high rates.
Automated resolution of rod pumping issues. In previous World Oil issues (May 2015, May 2016), we discussed Zedi’s nitrogen-assisted Zedi SilverJack 6000 and 8000 hydraulic, linear lift rod pumping technologies, Fig. 7. As part of its smart-field initiative, Zedi has engineered autonomous operation capabilities into the SilverJack pump by installing an algorithm that detects and automatically resolves common rod-pumping issues, Figs. 8 and 9. The algorithm is designed to solve issues such as parted rods, a hole in the tubing, a split barrel, gas lock and stuck downhole pump valves. In addition to detection, the algorithm automates the resolution of treatable issues like stuck downhole pump valves and gas lock.
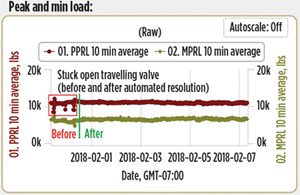
The algorithm is based on pump card analysis. Once an issue is detected, the SilverJack optimization controller can send a notification to the site operator or proceed with automated issue resolution. The changes made by the automatic controller are similar to what an optimization technician would do manually if attempting to resolve the problem, including adjustments to stroke speed/length or changing the bottom position to tag the pump. Aggressive steps like heavy tagging of the downhole pump can be omitted, if so desired.
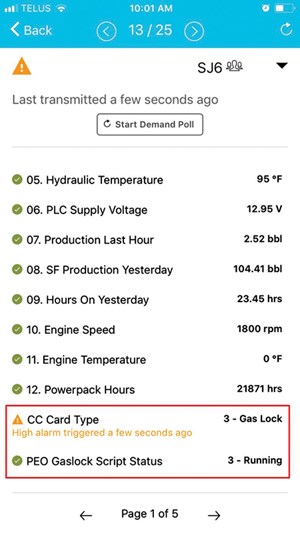
To address the unique configuration of each well, the algorithm can be tuned to only use previously successful steps for a specific well, further improving resolution performance over time. This automation significantly reduces issue resolution time by eliminating the need for manual intervention. Field testing has shown that the time to detect and resolve stuck downhole pump valves can be as little as four minutes.
The autonomous operation is facilitated by the hydraulic drive system of Zedi’s SilverJack portfolio. The operational adjustments required are made by the optimization controller with no need for mechanical changes. The same adjustments can be made on both AC and gas-driven SJ6000 and SJ8000 systems. The algorithm can be added to existing deployments via a firmware upgrade.
AUTOMATION AND CONTROL
Artificial lift control systems have become increasingly important, since any production downtime is extremely costly.
Lufkin Well Manager (LWM). The new BHGE LWM 2.0 rod pump controller provides smarter, more efficient data gathering capabilities and a more intuitive interface that enables operators to maximize well performance while improving artificial lift equipment operations.
More than just a standard rod pump controller, the LWM 2.0 features advanced pump-off control and VFD functions. Additional improvements include a full-color, high-resolution user interface with on-board wifi connectivity, all with no requirements for proprietary software. This allows flexibility of access for personnel, either onsite or remotely, to retrieve the needed information on a computer or mobile device in real time. The LWM 2.0 also functions as a standard programmable logic controller, supporting ladder logic and proportional-integral-derivative control functions with multiple options for input output (I/O) expansion, including analog and digital input and output, general purpose I/O, resistance temperature detector, and thermocouple inputs.
OTHER DEVELOPMENTS
Proper artificial lift selection should include an analysis of the individual well’s parameters and the operational characteristics of the available lift systems.
Lifetime lift system. Comorant Engineering is now offering a Lifespan Lift System (LLS), which uses one completion from early in the well’s life until the well is abandoned. This system utilizes one completion into which multiple lift techniques are deployed without the need for any rig time after the initial installation. The same LLS surface equipment and tubing system are utilized throughout the well’s life cycle.
The LLS uses two pump technologies and a velocity string to lift produced fluids. Three different configurations are available, Fig. 10. From a completion point of view, the inner string is coiled tubing and serves both as a velocity string and a fluid conduit communicating to the wellhead.
Phase 1. During the well’s initial completion and commissioning, coiled tubing is installed. Then as the well pressures and flowrates decrease, the velocity string can be used in several arrangements to manipulate the production flow velocities and rates.
Phase 2. During the next phase of production, a jet pump is installed inside the coiled tubing, by circulating the pump down the wellbore and into a landing assembly previously attached to the coiled tubing. The jet pump can be used for the high water rates typical in the early stages of production.
Phase 3. In the third phase of production, a hydraulically-driven positive displacement pump (Comorant RETRIEVER) is used to lift well fluids. This pump is then utilized for the duration of the well’s life. Due to the pump’s unique features, it can be used with zero bottomhole pressure. It will not gas lock, even in a 100% gas environment.
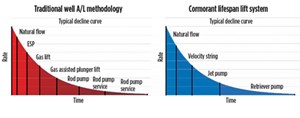
This unique completion and pump configuration reduces operating costs, as well as capital costs. Since a rig is only necessary to initially install the tubing in the well, expensive rig time for change-outs is eliminated. Figure 11 provides a comparison to segmented lift strategies versus the Cormorant integrated LLS.
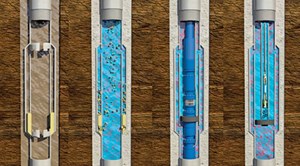
Both of the pump types utilize the same landing assembly, which is attached to the end of coiled tubing. These pumps circulate into and out of the well, allowing easy change-out and maintenance for the pump type, as well as for pump repair and rebuild. The Cormorant RETRIEVER pump is a unique, hydraulically driven reciprocating pump. It offers a long life, fits inside 1¾-in. coiled tubing for use in 4½-in. cased wells, and is capable of 12,000+ ft without high surface unit pressures.
The surface unit is a simple jet pump type surface unit, sized to accomplish the lift volumes projected for the well. During the third phase of operation with a RETRIEVER pump, the unit will operate at significantly reduced flowrates, providing high reliability and long-life surface performance.
Flexible gas separation technology. Black Jack Production Tools’ patented casing gas separator (CGS) is a new production efficiency altering tool that improves gas handling by doubling separation capacity in artificially lifted wells. The low-risk system is easy to install, and is non-disruptive to existing drilling and completion practices, Fig. 12.
NEXT MONTH
Part 2 of this year’s “What’s new in artificial lift?” series in the coming June issue will include a number of recent product developments associated with ESPs, PCPs, gas lift and plunger lift technologies.
- Advancing offshore decarbonization through electrification of FPSOs (March 2024)
- U.S. oil and natural gas production hits record highs (February 2024)
- What's new in production (October 2023)
- FPSO technology: Accelerating FPSO performance evolution (September 2023)
- What's new in production (August 2023)
- A step-change in chemical injection (August 2023)
- Applying ultra-deep LWD resistivity technology successfully in a SAGD operation (May 2019)
- Adoption of wireless intelligent completions advances (May 2019)
- Majors double down as takeaway crunch eases (April 2019)
- What’s new in well logging and formation evaluation (April 2019)
- Qualification of a 20,000-psi subsea BOP: A collaborative approach (February 2019)
- ConocoPhillips’ Greg Leveille sees rapid trajectory of technical advancement continuing (February 2019)