Russian manufacturing facility, new winterized train rig address specific conditions
The Russian economy has long relied on the oil and gas industry to drive growth, with areas such as Samotlor field responsible for the country skyrocketing to prominence in the global energy marketplace. Operating in the country, however, can present a challenge for companies that are unfamiliar with the ins and outs of equipment design regulations, and unprepared for the harsh reality of Siberian operating conditions, which regularly stay in sub-Arctic temperatures for long periods.
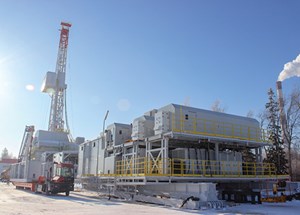
As Russia continues to strengthen its position in the global economy and secure its role as a leader in energy production, the need for National Oilwell Varco (NOV) to further develop its presence in the country became increasingly apparent. Understanding the unique needs of the market and responding with the best technical solutions is now more critical than ever.
In early 2011, the NOV leadership team was contacted by the Kremlin in Moscow, with a request to build a drilling rig and downhole tool manufacturing facility in the heart of Russia. Prior to this engagement, NOV made several independent attempts to establish manufacturing operations in Russia, but such attempts had been unsuccessful. Though there would certainly be challenges, the company understood the value of establishing an in-country foothold, and acted on the opportunity when it presented itself, moving to secure an appropriate amount of space in a logistically advantageous area.
Six months later, the location of the new facility was designated as Kostroma, Russia—a historic, provincial city of approximately 350,000 people, 200 mi northeast of Moscow, on the banks of the Volga River. Reasons for choosing this location included access to the federal highway and railroad systems; seasonal access to the Volga River for shipping to and from St. Petersburg and the Caspian Sea; close proximity to Russia’s largest steel mill, owned by Северсталь (Severstal), whose product will be used to produce the material necessary for manufacture of capital equipment and to upgrade the existing rig fleet; and access to skilled welders, CNC machine operators, and mechanical and electrical engineers in the Kostroma region.
The new, 137,795-ft² facility would be built to address the needs of the unique Russian market, allowing the company to employ local citizens, design region-specific solutions and deliver services to customers without worrying about the logistical headaches of global shipment.
In 2012, a project team—consisting of rig experts, rig design engineers, civil engineers, and legal and financial specialists—was put into place, and construction of the Kostroma facility commenced in late 2013. As the Kostroma facility was being built, Russian customers frequently indicated that they did not want a Canadian- or North Slope-style drilling rig, with computerized drilling systems, touchscreens and automated technologies. Such additions were unnecessary for the type of drilling being carried out in the region. Additionally, the restrictive cost of these technologically advanced rigs, at approximately $50 million per unit, meant that they would often never be used. With oil pricing equilibrium where it was, customers were looking for a rig in the range of $15 million to $25 million that could be safely, and cost-effectively, used in the harsh Siberian environment, and provided with aftersales support and spare parts. Reliability was also a major concern, as the rig needed to be operated continually at temperatures as low as –40°F (–40°C).
After years of planning and construction, the Kostroma facility officially opened its doors in 2016, bolstering the Russian workforce by hiring 200 local personnel with deep knowledge of the region and its expected design and safety standards. The newly-built facility added regional capabilities for improved collaboration between businesses, enhanced service and support, and reduced delivery times—by more than a month in most cases. Conversations continued with local customers, who were still asking for a rig that could address the gap in the market for a region-specific model.
Finally, as the culmination of years of research and development, NOV has now designed and built a rig that is optimized for Russian and CIS environmental conditions and operational requirements, with the first newbuild completed in March 2018. The extreme weather, 1,500-horsepower, 320-metric ton (MT) winterized train rig meets both API and Russian requirements and has a strong focus on safety, due in part to an echelon configuration, capable of moving 1,148 ft, Fig. 1.
The robust rail system is designed for pad drilling, allowing the train rig to move from well to well without rigging down. The new rig features an effective modular design and quick connections for cabling, as well as advanced drilling controls integrated with established machinery. Additionally, the optimal location of the drill-floor electrical room reduces cable runs and improves troubleshooting.
Some of the challenges that NOV met along the way were that the new rig had to be designed to cope with an extreme lack of infrastructure and heavy cranes in remote drilling locations in Siberia, while at the same time being able to operate autonomously for months at a time when access to the rig by truck or aircraft is impossible, due to weather or the vast and rugged geography of Russia. The mast and substructure design of the new rig had to enable quick and easy rig-up at ground level, while the rig, itself, had to protect both the crew and the equipment from the harsh environment. Additionally, new and improved welding procedures had to be created and implemented by the Russian workforce to address the role of the frigid temperatures in equipment manufacture and delivery.
The technical specifications of the train rig are as follows:
- Mast
o Low-pivot cantilever mast
o Sling-line raised by drawworks
o Height of 152 ft
- Substructure type
o Quadra-lift, drawworks raised
o Assembly at ground level
o Floor height at 32.8 ft
o Setback capacity of 5,000 m of 127-mm drill pipe
- Drawworks
o NOV Type DSGD-375
- Top drive
o TDS-11SA
- Iron roughneck
o NOV ST-80C²
- BOPs
o Spherical and double ram BOPs with 13⅝-in. bore and 5,000-psi working pressure
- Driller’s controls
o Amphion system
- Rotary table
o NOV D-375
- Mud pumps
o Two 1,600-horsepower FD-1600 pumps
o Brandt King Cobra Venom linear shale shaker
- Optional equipment
o Backup generator sets
o High-torque TDS-11SH top drive
o Third mud pump
o Reserve tanks
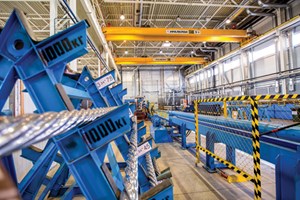
In addition to the winterized train rig, the Kostroma facility also manufactures drill bits, downhole motors and underreamers, fishing tools, drilling jars and completion tools, Fig. 2. The facility’s location enables aftermarket service and repair that was previously impossible to perform, due to constraints on supply chain. If there is such demand, the Kostroma facility has the ability to manufacture other land drilling rigs, including rapid deployment, self-propelled and trailerized mobile drilling rig models. Onsite drilling simulators ensure that customers and personnel are up-to-date on drilling controls technology, and that oilfield workers can continually be developed and trained.
NOV has invested significantly in Russia and, despite current international tensions and obstacles, believes that it is in a prime position to serve the needs of the Russian and Former Soviet Union marketplace. It has been well-documented in regional rig fleet surveys that a significant portion of rigs—possibly more than 50%—are over 20 years old and nearing the end of their service life. Additionally, there is concern that the rig decommissioning rate might exceed the ability to replace the aging fleet. Companies that can adapt to this changing landscape and effectively react to regional demand will be in an advantageous position when, over the next five years, the more than 400 land rigs that fall into this category are replaced.
- Applying ultra-deep LWD resistivity technology successfully in a SAGD operation (May 2019)
- Adoption of wireless intelligent completions advances (May 2019)
- Majors double down as takeaway crunch eases (April 2019)
- What’s new in well logging and formation evaluation (April 2019)
- Qualification of a 20,000-psi subsea BOP: A collaborative approach (February 2019)
- ConocoPhillips’ Greg Leveille sees rapid trajectory of technical advancement continuing (February 2019)