Organophillic, clay-free fluid maximizes asset value and reduces cost offshore Abu Dhabi
An innovative fluid solution helped an operator in the offshore Abu Dhabi area of the UAE to achieve a quadruple win: 1) Time and cost were reduced approximately 50 days and $12.5 million, respectively; 2) productivity was increased 300%; 3) an ERD well achieved a record-breaking 18,674-ft horizontal section, which was the longest ever recorded in the UAE at the time; and 4) a record ROP of 2,350 ft/day was achieved. These successes resulted largely from the use of Halliburton’s mainstay processes, which include collaborating (listening and responding to the customer’s needs), service quality execution (delivering the right valued solution), and continuous improvement.
The Baroid team worked continuously with the customer to maximize asset value and reduce costs. New challenges arose during the initial planning stages, when the customer elected to extend the horizontal reservoir section from the planned range of 17,751 ft to 27,751 ft. This change would result in a lateral section of 18,674 ft. Innovation was needed to enable the customer to drill this long horizontal section, by keeping torque and drag to a minimum, and to complete the well with the longest reservoir liner section in the UAE.
Finally, the fluid must be non-damaging to the reservoir, to ensure that the customer’s objective of extended reservoir contact was attained. Based on the drilling target, design specifications, offset field experience, and laboratory testing, INNOVERT, an organophillic clay-free, mineral oil-based fluid system, coupled with the N-FLOW 325 filter-cake breaker system, was identified as the optimum cost-effective solution.
The recommended fluid system is a high-performance, lubricious organophillic, clay-free invert, emulsion drilling fluid with specific thixotropic and fragile gel properties. These properties are recognized for enabling extended-reach drilling, by minimizing pressure spikes and variances when pumping and circulating fluid around the well—the equivalent circulating density (ECD) effect. Moreover, the drilling fluid minimizes fluid losses to the formation being drilled, avoiding reservoir damage and preserving producibility, achieving a primary objective for the customer.
The recommended filter-cake breaker system helps to maximize reservoir producibility by removing the deposited filter cake. This removal occurs in combination with an acid precursor and an acid-compatible surfactant. The acid-compatible surfactant water wets and initiates dispersion of the filter cake, enabling the acid to attack the filter cake components without causing emulsion blockages common to regular surfactants, oil mud components, and acid. Equally important to the success of the filter-cake breaker system is ensuring that the filter cake components are predominantly acid-soluble and form a thin, easily removable, impermeable membrane on the reservoir wellbore wall.
Beginning with a design specification for ERD, the local technical team performed a detailed, step-wise process of creating and testing all fluid solutions, touching on base oil lubricity, rheology, ECD and hole-cleaning characteristics, fluid stability, and fluid loss control/filter-cake composition. The efficacy of the filter-cake breaker system was evaluated through a repeated sequence of tests that replicate the deposition, break-up and dissolution of the filter cake and, finally, flowback of oil.
Confirmation of fluid formulations. Simulations of bottomhole pressure conditions, ECD, hole-cleaning, and tripping constraints were performed, using proprietary wellbore hydraulics software, DFG. These combined methodologies confirmed that the fluid formulations were scoped and optimized correctly for the customer’s planned drilling and completion operations. In addition, displacement operations were modeled and optimized, using a hydraulics simulation package, CFG, to ensure that the formulation of the filter-cake breaker system was displaced properly into the open hole.
Originality in the fluid design was the use of calcium bromide (CaBr2) brine. Conventionally, invert emulsion fluids (IEF) use calcium chloride (CaCl2) brine as the internal phase to provide water-phase salinity, viscosity, and some density. Primary density is controlled through the addition of barite and ground marble. In this application, design specifications severely limited the addition of particulates, requiring a higher-weight brine to impart density to the fluid. Thus, CaBr2 was used in combination with BARACARB, a sized, ground marble bridging agent for HPHT fluid loss control and filter cake formation, without compromising the viscosity or fragile gel properties of the fluid system or causing formation damage.
Field operations initially focused on logistics. For nearly a decade, water-based fluids have been used to drill and complete the reservoir section, leading to a significant transition for the introduction of an IEF. A total fluid volume of 11,500 bbl, including contingency, was built at the drill site, aided by a hydraulic shear unit, to ensure that the rheology modifier (polymeric base) underwent appropriate shearing to obtain the rheology profile required, incurring no NPT and no interruption of the critical path timeline. Properties of the field-mixed fluid met the design parameters determined in the initial solution creation process.
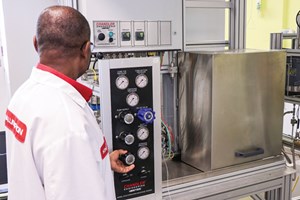
Drilling operations. The drilling of the extended lateral reservoir section went smoothly, encountering minimum fluid losses and no tight hole conditions. Enhanced ROPs were observed, relative to earlier offset wells, averaging 80 ft/hr and achieving a record of 2,350 ft/day. Fluid density was adjusted twice (from 1.19 to 1.24, then to 1.26 SG) while drilling, because of greater-than-expected formation pore pressure (later attributed to the presence of a live injector well). These adjustments were achieved through the manipulation of the CaBr2 density with minimal effect on fluid viscosity.
Wellbore hydraulics were monitored, using the wellbore hydraulics software and fluid parameters from the daily mud reports, Fig. 1. Of particular concern were hole-cleaning and good ECD management. The former affects ROP and ECD; a net accumulation of cuttings will restrict annular flow, affecting circulating pressures. The latter relates to induced wellbore instability, relative to the fracture (lost circulation) and pore pressure (influx and hole collapse) gradients. Look-ahead hydraulic simulations were used to provide guidance regarding ECD conditions, as applied to tripping, ROP limits and circulation rates for multiple stands ahead of the bit.
One significant interruption to drilling operations occurred when the BHA needed to be changed out after drilling 10,000 ft of the lateral; the trip out lasted for 12 days. While out of the well, surface samples of the fluid were subjected to static aging to evaluate potential changes in downhole fluid properties. This was necessary for well control and preparations for tripping back into the well. Testing demonstrated that the fluid maintained its properties over an extended static period—emulsion stability, rheology, gel behavior and fluid loss control remained tight, with only a marginal density variation (SAG) of a 0.01 SG difference. The promise of stable fluid and well conditions was confirmed, when the customer was finally able to trip back into the well; no tight spots were observed, and surface samples taken as the fluid was circulated out again showed little degradation relative to fluid specifications. Drilling continued successfully for an additional 8,674 ft to section TD.
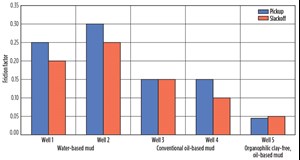
The fluid was subjected to a final, extended static period after reaching TD. Completion operations included running a slotted liner; however, an unplanned break in operations resulted in a 25-day delay, during which the fluid remained in the well. When the liner was eventually run, no obstructions were encountered, and the liner successfully landed at TD. The properties of the fluid reported during the last circulation with liner at bottom were closely comparable to those at the end of drilling; major differences were changes in fluid density (1.28 SG vs. 1.24 SG at the end of drilling), as a result of no circulation to homogenize the system.
Excessive friction was a concern from the start of well planning and while drilling. Significant effort was made at the design stage to identify a base oil with the greatest lubricity for the fluid formulation. This effort resulted in the lowest friction factors ever observed for drilling and liner running operations at this locality—a colossal 80% reduction from 0.23 for WBM to 0.05 for INNOVERT, respectively. Figure 2 shows the data collected from five wells within the same field.
A final critical phase for well construction, after the liner was in place, was to displace the well to the filter-cake breaker system. The filter-cake breaker system is mixed at surface, then circulated through the displacement string. The acid pre-cursor enables the filter-cake breaker to be placed uniformly over the entire reservoir section without hot-spotting, which is a common hazard of conventional stimulation jobs using live acids, such as hydrochloric acid (HCl). After its placement, the filter-cake breaker system is activated by bottomhole temperature and begins the process of removing the in-situ filter cake. To cover the reservoir section in the 18,674-ft lateral, 1,625 bbl of filter-cake breaker were pumped and allowed to soak.
The success of the total operation was reflected best by the production rates on start-up, which were 300% greater than initially forecast. An additional bonus is that production showed (and continues to show) a very low water cut (<0.1%).
In conclusion, this case represents the successful uses of multiple firsts for the customer and Baroid—the longest lateral section at 18,674 ft; the first application of a CaBr2 formulated, low-solids fluid system; and a field record ROP of 2,350 ft. Collectively, these successes can be attributed to the 300% above-forecast production rate and the estimated 50 days and $12.5 million saved against AFE.
- Coiled tubing drilling’s role in the energy transition (March 2024)
- Oil and gas in the Capitals (February 2024)
- Digital tool kit enhances real-time decision-making to improve drilling efficiency and performance (February 2024)
- E&P outside the U.S. maintains a disciplined pace (February 2024)
- U.S. operators reduce activity as crude prices plunge (February 2024)
- Drilling advances (January 2024)