Execution, collaboration and innovation key to improving economic viability of offshore projects
Although our industry continues to navigate the most severe downturn in decades, growing global demand for affordable energy will, at some point, require increased offshore production. It is important that the offshore industry approach this challenging market as an opportunity, and embrace our collective responsibility to deliver step-changes in innovation that facilitate the more-efficient delivery of incident-free operations.
While the past two years have been taxing on all of us, and the near-term outlook is not overly encouraging, in some ways this prolonged downturn has been both healthy and necessary for the long-term viability of offshore exploration, development and production. From 2009 through mid-2014, as oil prices climbed steadily, an environment emerged in which volume and rig and service availability trumped efficiency. As a consequence, despite oil prices that clearly supported additional investment, operators experienced declining returns.
The combination of these declining returns, the dramatic fall in oil prices that began in the second half of 2014, and a growing imbalance between oil supply and demand, resulted in a slashing of exploration and production budgets, and a dramatic reduction in offshore activity. However, operators recognize that the recent pullback in offshore drilling is not sustainable, and that deepwater assets remain crucial to addressing their reserve replacement challenges.
As such, from the perspective of an offshore driller, it is imperative that we explore every opportunity, including streamlining the business and asset base; improving operational performance; introducing new technologies; and exploring new business and commercial models; to help our customers make their projects economically viable at much lower oil prices.
Driving cost out of the value chain starts with a look in the mirror, and a commitment to challenge every position, process, procedure and practice that does not create demonstrable value. At Transocean, we have streamlined significantly our organization, removing layers of reporting between the rig and senior management, closing and consolidating offices and functions, improving efficiency by eliminating duplicative efforts, and automating some manual functions, all of which have driven considerable cost-savings.
We also have assumed a very thoughtful approach to technical sourcing, whereby we have deconstructed the repair and maintenance of every major component on our rigs to better understand the cost drivers. As a direct result of this effort, we have significantly reduced the maintenance expense of some of our costliest components, such as riser, engines and cranes. We also have materially reduced the cost associated with stacking dynamically positioned rigs, through the use of a fit-for-purpose mooring system, which allows our rigs to weathervane safely in protected and benign waters. As important as these examples, Transocean has adopted a cost-conscious culture that will ensure that we continue to actively seek opportunities to become increasingly efficient.
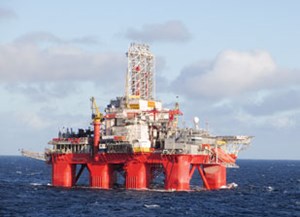
In addition to challenging our structure and various processes, we also have taken a data-driven approach to honestly assess the technical capability and future marketability of each and every rig in our fleet. And, while Transocean has introduced more high-specification, ultra-deepwater rigs to the global fleet since 2008 than any other offshore drilling contractor, we also recognize that we had a number of older, less-capable rigs that needed to be retired and recycled. As a result, since the start of this downturn, Transocean has announced the retirement of 25 rigs (approximately 50% of the total number of rigs in the global fleet that have been slated for retirement); and, as certain rigs roll off of contract, we will likely see a few more of our rigs meet the same unfortunate fate. While it is certainly difficult to say goodbye to assets that have delivered so much value to the company for so many years, we recognize that the technical capability and efficiency of our fleet is critical to reducing well costs.
On the operational performance front, we are harnessing knowledge from past offshore wells to establish metrics for each critical activity, and identify and share best practices across our fleet. Since 2010, Transocean has drilled 3,933 wells, representing 357 years of operating time. This number includes 1,000 ultra-deepwater wells drilled across all major, worldwide ultra-deepwater basins.
Through the analysis of detailed activity logs and durations, we are able to identify opportunities to improve performance in critical activities, reducing both flat spots and well costs. A perfect example of this performance improvement can be found in a review of Statoil’s Gymir deepwater campaign, where the Transocean Spitsbergen (Fig. 1) and her crew drilled the last seven wells of the campaign 40% faster than the industry average in the Barents Sea. And, as a direct result, Statoil was able to drill two more wells than originally planned.
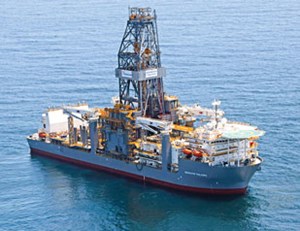
We are also using our extensive database of information to drive improvements in equipment reliability and our maintenance programs. For instance, over the past two years, through detailed root cause analysis, we have improved BOP reliability by 65%; and, over that same time horizon, by carefully analyzing actual usage and wear, we have redesigned our maintenance processes and compressed our between-well maintenance time by more than 40%. While we have made meaningful progress to date, we continue to look for additional areas, where we can enact similar step changes, as the combination of all of these initiatives can help operators to improve the economics of their developments.
In addition to using data to drive operational performance improvements, Transocean continues to identify opportunities to solve customer challenges through the introduction of new technologies. As well depths increase, well pressures intensify, and formations become more challenging, it is imperative that offshore drillers work closely with operators and other service providers to jointly define cost-effective solutions.
As a technical leader and innovator, Transocean has a long history of accomplishments and contributions that have gone toward improving offshore drilling. These range from one of our predecessor companies pioneering early versions of deepwater drilling methods in the 1950s, to the introduction of the first ultra-deepwater, dual-activity drillship in the late 1990s. The innovation continued this year with the introduction of the Deepwater Thalassa (Fig. 2), a drillship that features our patented, dual-activity drilling technology, industry-leading hoisting capacity, Transocean’s designed and patented Active Power Compensation hybrid system, and a dual blowout preventer. The drillship is designed to operate in water depths of up to 12,000 ft and drill wells to a depth of 40,000 ft. It is also upgradeable to accommodate a 20,000-psi BOP system.
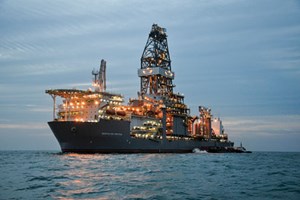
In addition to streamlining the business, high-grading the fleet, improving operational performance, and introducing new technologies, we believe that it is necessary to contractually align with our customers’ business objectives. Earlier this year, Transocean was awarded a contract for the Transocean Spitsbergen, based upon an innovative, yet pragmatic approach that is helping our customer, Hurricane Energy, commence its drilling program in the North Sea.
The contracted day rate is priced below market, but it includes escalators triggered by performance that are ultimately recognized, based upon the success of the overall drilling program. Hurricane Energy appreciated the efforts and the flexibility demonstrated to help this program come together, and applauded Transocean’s willingness to “put skin in the game.” This is the type of innovative and collaborative commercial alignment that will be necessary across the industry, moving forward.
Ultimately, it is important that we remember that this downturn will not last forever, and that we should all be preparing for the recovery, Fig. 3. How will we reactivate dynamically positioned rigs in a timely and efficient manner? Perhaps more importantly, how will we rehire, train and certify our crews to ensure incident-free operations, and a consistent level of high performance across a growing, active fleet? How will we ensure that the cost savings and performance improvements that we have recognized in the past two years are sustainable during the upturn? At Transocean, we are asking, and answering, these questions with the belief that we, as an offshore industry, must find a way to make offshore projects economically viable through the cycles.
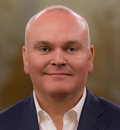
- Applying ultra-deep LWD resistivity technology successfully in a SAGD operation (May 2019)
- Adoption of wireless intelligent completions advances (May 2019)
- Majors double down as takeaway crunch eases (April 2019)
- What’s new in well logging and formation evaluation (April 2019)
- Qualification of a 20,000-psi subsea BOP: A collaborative approach (February 2019)
- ConocoPhillips’ Greg Leveille sees rapid trajectory of technical advancement continuing (February 2019)