A couple of weeks ago, I was involved in a conversation with workmates about wellbore cements. Somewhere in the conversation, mention was made of an alternative to Portland cements—geopolymer sealing materials. To a man, the group muttered, “huh?” That led to some question-asking and material research on our part. The questions included:
What is geopolymer sealing material? From 2003 to 2006, Brookhaven National Laboratory (BNL) developed a new type of cost-effective, acid-resistant casing sealant produced through alkali activation reaction of sodium silicate aimed, primarily, at highly concentrated H2S environments with high temperatures. Partners in the project included Halliburton, AltraRock Energy Corporation and Sandia National Laboratory.
BNL and partners approached the project with specific material criteria, including:
- One dry component product
- Plastic viscosity of 20 to 70 cp at 300 rpm
- Maintenance of pumpabiity for at least one hour at 85°C
- Compressive strength greater than 200 psi
- Self-degradable by injection with water at a certain pressure
- Expansion and swellable properties greater that 10% of the volume of the sealant
- Compatibility with drilling fluids and mud
- Excellent permeability through porous structures corresponding to soil stabilizing grout
- Bonding strength to rock surfaces greater than 50 psi
- Anti-filtration properties
- Low-cost materials, equal to or less than conventional Portland cements
- Usage to cement casing without self-degradation.
Why was geopolymer sealant developed? The sealants, developed as an alternative to traditional cements, were designed to lower raw material costs by using industrial waste, such as granulated blast slag from steel manufacturing and fly ash from coal-fired generation plants. The result is a lower-cost, higher-performance alternative to traditional Portland cements. And, there are other benefits, including acid and CO2 resistance, a simple setting control without retarders, heat and thermal resistance from refractory cementitious properties, and cost-effectiveness.
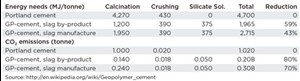
There are four categories of geopolymer sealants: Slag-based, fly ash-based, rock-based and ferro-sialate-based.
What is the primary benefit of geopolymer sealants? While many point to the cost-effectiveness, ease of placement and structural integrity of geopolymer sealants, perhaps the most important benefit is its reduced carbon footprint, particularly with respect to its increasing application as a building and roadway construction material to replace concrete (interestingly, concrete, a mixture of cement and aggregrates, is second only to water in usage in communities around the globe). Portland cement is a serious atmospheric polluter, whose manufacture involves the calcination of calcium carbonate, which, in turn, produces serious amounts of CO2. The production of one tonne of Portland clinker directly generates 0.55 tonnes of chemical-CO2 and requires the combustion of carbon fuel that produces another 0.40 tonnes of CO2. In other words, 1 tonne of Portland cement = .95 tonnes of CO2.
The need for geopolymer standards. ASTM International (formerly the American Society for Testing and Materials) organized a symposium on Geopolymer Binder Systems that included discussion of the adoption of standards. They concluded that to do so requires the existence of standard geopolymer binders but that “presently, every expert is presenting his own recipe, based on local raw materials (wastes, by-products or extracted). There is a need for selecting the right geopolymer cement category.” The Concrete Institute of Australia has produced a recommended practice for geopolymer concrete that provides background information on geopolymer chemistry and materials, and properties of geopolymer concrete. Recommendations on modification to current standards are given in the document.
The path forward. I think it is clear that geopolymer sealants have great potential for application in oil and gas well cementing. However, development of current and next-generation geopolymer technologies is still underway. And we have a huge infrastructure built on the mixing and pumping of Portland cements. And, one must take into account our extreme reluctance, in many parts of the industry, to take on new, but unproven technology. Having said that, it appears to me that geopolymers have enormous potential to improve well integrity, lower costs and seriously lower CO2 emissions. Hopefully that will lead to field trials and, if those are successful, early adoption.
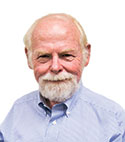
- Coiled tubing drilling’s role in the energy transition (March 2024)
- Using data to create new completion efficiencies (February 2024)
- Digital tool kit enhances real-time decision-making to improve drilling efficiency and performance (February 2024)
- E&P outside the U.S. maintains a disciplined pace (February 2024)
- U.S. operators reduce activity as crude prices plunge (February 2024)
- Drilling advances (January 2024)