MAURO DA CRUZ and EDWIN VERVEST, BP; HENDRAYADI PRABAWA, Schlumberger
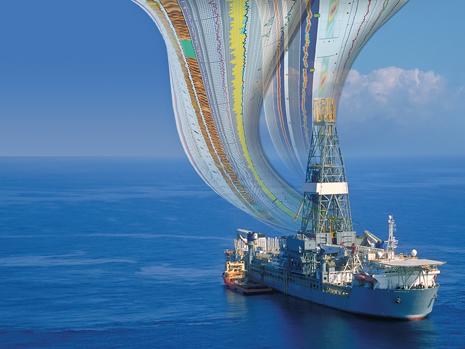 |
The combination of high-speed telemetry, multifunction LWD, magnetic resonance LWD, formation pressure-while-drilling, sonic-while-drilling and seismic-while-drilling services formed a complex BHA while drilling an ultra-deepwater exploration well offshore Angola in one run. |
|
In a deepwater deviated well offshore Angola, BP and its partners, Sonangol E.P., Sonangol P&P, Statoil Angola A.S., Marathon Oil and Sonangol Sinopec International (SSI), have successfully acquired the world’s largest-ever suite of measurement-while-drilling (MWD) data in a single bottomhole assembly (BHA). Combining seven different services, the BHA included a rotary steerable system (RSS), measurement and telemetry service, logging-while-drilling (LWD) magnetic resonance service, multifunction petrophysics platform, formation pressure service, and sonic and seismic services.
Measurements from these services were integrated and used for real-time drilling parameter optimization and formation evaluation. These data were shared with experts located remotely around the world, monitoring the progress of the well and supporting critical decisions. The LWD services were used to monitor pore pressure, perform formation evaluation, select pressure tests and acquire seismic check shot times. Net reservoir sand and continuous permeability values were estimated for completion design optimization.
THE PSVM DEVELOPMENT
BP is operator for the development of a series of deepwater oil discoveries, offshore Angola in Block 31. The first project in the program comprised Plutão, Saturno, Vênus, and Marte (PSVM) fields, in an approximately 2,000-m water depth, approximately 400 km northwest of Luanda. Plutão Alpha was one of two Plutão field segments on the PSVM core segments that were developed initially.
The first well. Well-1 was spudded in 2010 and completed with an 8½-in. production section. This directional well, with a challenging trajectory, was drilled into a horst block adjacent to a fault terrace system, where individual fault throws were estimated to be in the range of 50 m to 100 m. It targeted the highest elevation of a structure containing a turbidite channel and encountered lithologies that included claystone and argillaceous sequences at the top of the reservoir.
Although Well-1 was primarily a production well, a variety of measurements were made during its drilling, not only to optimize well placement, reduce rig time and minimize drilling risk in this deepwater environment, but also for use in overall field appraisal. Another objective was to evaluate, at the earliest opportunity, the most appropriate LWD solution for use in wells during subsequent field development. In response to this request, Schlumberger designed a BHA for the production section, made up from the most complete set of LWD tools ever deployed together in one run, which soon became known as a “mega-combo.” The TeleScope high-speed telemetry-while-drilling service was a key enabler for delivering such a broad range of real-time data while drilling.
Pre-drill BHA modeling. One of the key drilling objectives was to stay at or below a 60° inclination to avoid complications in later wireline evaluation runs. A build-and-drop profile, dictated by surface and subsurface locations, was planned for the 8½-in. section. Minimizing torque, drag, shocks and vibrations would be important for maintaining connectivity between the tools and delivering high-quality LWD data from the long BHA.
Advanced software and engineering workflows were used to model the dynamic behavior of the BHA. Schlumberger modeling software was used to model and predict drillstring dynamics under axial and shear loads, as well as bending and torsional moments due to the drilling operation. A finite-difference scheme in space and time was used to simulate the behavior of the interactions between the BHA, drill bit and rock face. The modeling process provided an enhanced understanding of the dynamic behavior of the drillstring and its sensitivity to vibrations. As a result of the study, recommended drilling parameters were proposed and referenced during operations.
Directional drilling. Well-1 was drilled from the Discoverer Luanda drillship in a 2,015-m water depth. A mud motor was used for the jetting of the 36-in. conductor and drilling of the 26-in. hole and 17½-in. sections. An RSS was used in the 12¼-in. section and 8½-in. production section. Schlumberger also provided the necessary tubulars, stabilizers and subs, and the company’s directional drilling experts provided real-time support during drilling. The recording system provided the interface to MWD and LWD data and the real-time outputs needed for directional drilling. Also available were interpretation programs used in real time or run offline.
Uphole data transmission. The high-speed telemetry service was used in the 12¼-in. and 8½-in. sections to accommodate the high volumes of real-time data from the mega-combo. The service incorporates a high-speed telemetry platform that uses new compression algorithms downhole to supply more data transmission at a given physical telemetry rate and new modulation methods to push mud pulse signals farther. At the surface, new signal detection and noise cancellation methods demodulate extremely weak signals at high telemetry rates to enhance data quality.
Multifunction LWD. A multifunction LWD service was placed just behind the RSS to deliver resistivity, neutron porosity, azimuthal gamma ray and density, elemental capture spectroscopy and sigma measurements, Fig. 2. Making these measurements close to the bit helped to minimize effects from mud filtrate invasion and borehole damage, while providing critical real-time data to steer the well.
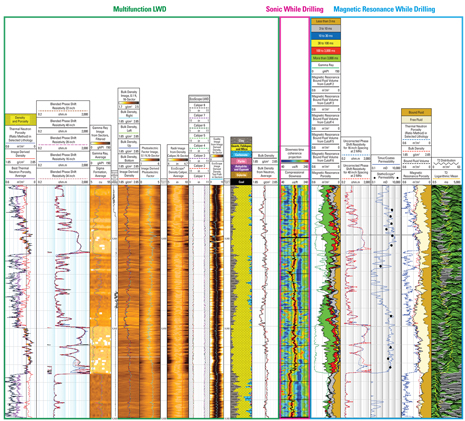 |
Fig. 2. The mega-combo suite of LWD services transmitted data in real time to remotely monitor the drilling process, optimize pore pressure, perform formation evaluation, select pressure tests and acquire check shot times. Net-to-gross and continuous permeability values were estimated for completion design optimization. |
|
Magnetic resonance. The magnetic resonance (MR) tool delivered real-time evaluation of formation productivity through reliable determinations of mineralogy-independent porosity, bound and free-fluid volumes, and pore size from which permeability was estimated, as well as identification of in-situ fluids. The MR data, combined with the multifunction LWD measurements, provided volumetric determination of the fluids in the rock, Fig. 2. Combined services were also used to select pre-test pressure depths to minimize the number of potential dry tests.
Formation pressure. The formation pressure-while-drilling (FPWD) service was run to enable accurate and efficient measurement of formation pressure in the drilling environment, and to provide direct formation pressure and mobility data for fluid typing, reservoir pressure management, and mud-weight control and optimization. It also provided information for reservoir management, such as pressure depletion and communication mechanisms, and completion design.
Extensive planning was conducted before the job, leveraging broad knowledge and experience of drilling in deepwater turbidite environments offshore Angola. The focus was to maximize formation tester probe seal success and minimize operational time. Pre-testing was specially designed in terms of expected formation flowrates and volumes. It addressed operational specifics, including pressure testing in unconsolidated sandstones, orientation if needed, recovery from lost seals and dry tests. Objectives included helping to optimize mud weight while drilling, evaluating and assessing supercharging risks, and gauging noise due to mud pump circulation.
As drilling started, a first pressure point was acquired to confirm pore pressure and optimize mud weight. Drilling was completed safely and the FPWD service was deployed a second time in a reservoir management mode to perform fluid identification through gradient analysis and to establish vertical compartmentalization. A total of 22 pressure tests were acquired with 100% seal success.
With the combination of FPWD, multifunction LWD and MR services, four flow units were identified using gradients and excess pressure techniques. This was particularly important information for guiding development plans and understanding fluid movement inside the reservoir, especially for future water flooding strategies.
Sonic-while-drilling. The sonic-while-drilling service provided real-time formation slowness measurements in the openhole section, including compressional (DTc) with a full slowness projection log, Fig. 2. The sonic data were acquired both during drilling and while pulling out of the hole, where it spanned the 95/8-in. casing. The cased-hole data were evaluated for qualitative interpretation of top of cement. Subsequent analysis indicated that the top of cement seen in the LWD sonic was at the same depth as seen in the wireline cement bond log.
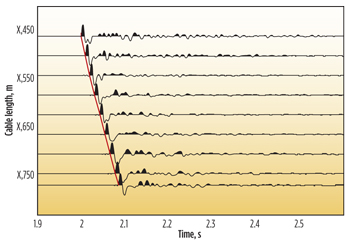 |
Fig. 1. Downhole hydrophone data showed good-quality waveforms. The first arrival times (red solid curve) were used for velocity computation. |
|
Seismic-while-drilling. The seismic-while-drilling (SWD) service delivered real-time check shot and interval velocity data. These data from the downhole hydrophone data showed good-quality waveforms, Fig. 1. The SWD service acquired borehole seismic data during drillpipe connections, and the acquisition took less time than it takes to make a connection, making it transparent to the driller and using no additional rig time. Seismic data were also recorded on the trip out of the hole. The information provided helped reduce uncertainty ahead of the bit and provided waveforms of sufficient quality and coverage to be included in look-ahead vertical seismic profile (VSP) processing.
DRILLING AND LWD PERFORMANCE
Directional Well-1 was drilled with an high rate of penetration and achieved the objective of staying at or below a 60° inclination. No significant stick/slip, shocks or vibrations were observed while drilling, and real-time data from all downhole tools were sent uphole without any interruptions. The same assembly was used to drill out the casing shoe and reached TD in one run. After pulling out of the hole, no wear or damage was seen on any of the components of the long assembly.
The mega-combo LWD service successfully delivered an unprecedented range of reliable measurements in one BHA, and all the tools performed to specification, Fig. 3. The real-time data were shared with experts located remotely around the world to monitor the progress of the well and support decision-making.
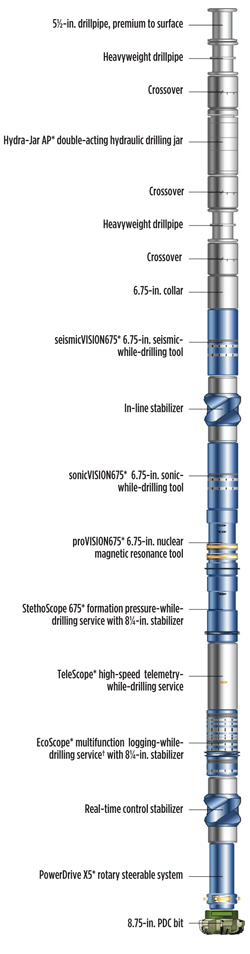 |
Fig. 2. The mega-combo suite of LWD services transmitted data in real time to remotely monitor the drilling process, optimize pore pressure, perform formation evaluation, select pressure tests and acquire check shot times. Net-to-gross and continuous permeability values were estimated for completion design optimization. |
|
Wireline logging runs performed after drilling included the MDT modular formation dynamics tester to acquire formation pressures and fluid samples. An advanced acoustic scanning platform measured acoustic formation slowness and identified and characterized anisotropy. Integrated dual oil-base micro-imagers characterized formation structures, dips and facies. The real-time and recorded-mode mega-combo data were compared with equivalent wireline logs and were found to correlate the well, validating the quality of the LWD data.
BUILDING ON SUCCESS
The results and relative value delivered by the real-time mega-combo measurements assisted in the design of optimum BHAs and wireline programs for subsequent wells. The BHAs for the next two wells completed used the same combination of LWD services, with the exception of seismic-while-drilling. Based on the success of the mega-combo LWD system evaluation strategy described in this case study, BP has applied it elsewhere in Angola. The success of the strategy has also led to LWD service opportunities with other operators working in challenging deepwater areas, such as West Africa and Brazil. 
ACKNOWLEDGMENTS
The authors would like to thank the BP, Sonangol E.P., Sonangol P&P, Statoil, Angola A.S., Marathon Oil and SSI partners of the PSVM development for allowing the use of the data, and for their support and permission to publish this article.
NOTES
Japan Oil, Gas and Metals National Corporation (JOGMEC), formerly Japan National Oil Corporation (JNOC), and Schlumberger collaborated on a research project to develop LWD technology that reduces the need for traditional chemical sources. Designed around the pulsed neutron generator (PNG), EcoScope service uses technology that resulted from this collaboration. The PNG and the comprehensive suite of measurements in a single collar are key components of the EcoScope service that deliver game-changing LWD technology.
The author
MAURO DA CRUZ has been the New Well Delivery petrophysicist for BP Angola since 2011. He currently manages all petrophysics operations, as well as interpretation of new wells that have been drilled in Angola for all blocks. Prior to this role, Mr. da Cruz was a wireline field engineer for Schlumberger. He has six years’ experience with Schlumberger, starting as a wireline field engineer in Angola for two years before spending more than four years as senior and general field engineer in the North Sea and Nigeria. He received his BS degree in electrical and electronic engineering from the University of Kwame Nkruma, Kumasi-Ghana. EDWIN VERVEST, based in London, is the New Well Delivery team leader for BP onshore North Africa, working on Algerian and Libyan projects. He has an MS degree in petroleum engineering from Delft University of Technology in the Netherlands. HENDRAYADI PRABAWA has a BS degree in electrical and civil engineering from Bandung-Indonesia. He joined Schlumberger in 1984 as a field engineer, with assignments in Nigeria, Angola, Congo, Indonesia, Japan, Thailand and Brunei Darussalam. Since 2009, he has worked as principal petrophysics LWD domain champion in West and South Africa. |
|