A series of ultraviolet treatment applications in the Haynesville Shale formation is proving to reduce bacteria at a rate comparable to chemical biocides.
Kembe Kleinwolterink, Brandon Watson and Dave Allison, Halliburton; and Matt Sharrock, EOG Resources
Bacteria can have a highly detrimental effect on hydrocarbon production and transportation, causing major damage to fluids, piping and the formation itself. Aerobic bacteria, which require oxygen to live, produce a biofilm that can reduce reservoir porosity and cause plugging and fouling of tanks and piping. Slime-forming versions of these bacteria can accumulate into a bulky mass that can corrode or pit wellbore hardware, surface piping and storage facilities, significantly shortening their useful life, Fig. 1.
|
Fig. 1. Corrosion and pitting of a wellbore tubular caused by bacteria.
|
|
Anaerobic sulfate-reducing bacteria (SRB) flourish without oxygen. Introduced deep into the reservoir through waterflooding operations or fracture stimulation, SRBs can contaminate an entire wellbore or producing formation. As their name suggests, SRBs reduce sulfate ions to sulfide, forming a corrosive, difficult-to-remove iron sulfide (FeS) scale on metal components. SRBs can also turn sweet hydrocarbon production into sour hydrogen sulfide (H2S) production. Highly corrosive H2S can lead to the catastrophic failure of wellbores and production facilities not specifically designed to handle them and can contribute to other hazards.
During well servicing activities, fracture fluid tanks and other surface storage vessels are common breeding areas for microorganisms. Frac tanks may contain many gallons of bacteria-ridden gel from previous hydraulic fracturing jobs. When new frac gel is added, the bacteria have an additional food source and begin to multiply rapidly, releasing enzymes that degrade gels into sugars, which the bacteria can then absorb through their cell walls.
When pumped downhole for a new frac job, the degraded, reduced-viscosity frac gels travel through the equipment, wellbore and formation, transporting the bacteria with them and spreading the contamination, Fig. 2. This problem is generally most acute during the summer since bacteria are most active at temperatures between 60 and 100°F (16–38°C). Once the bacteria have started to degrade the frac gel, the gel may not be able to perform its desired functions, such as carrying sand and proppants, initiating fractures, diverting fluid flow, reducing fluid friction, enhancing acid stimulation, and other necessary functions to improve the success of stimulation activities.
|
Fig. 2. This photomicrograph uses epifluorescent microscopy to show common waterborne bacteria in a guar solution (100X magnification). The cloudy regions are guar residue.
|
|
Pipelines and other surface handling and gathering facilities are additional possible sources of bacterial infection. A key conduit for bringing hydrocarbons to market, pipelines are usually hydrostatically pressure-tested during commissioning to ensure their structural integrity. This process creates a prime opportunity for bacteria to be introduced into the transportation system.
CHEMICAL BIOCIDES: THEIR RISKS AND LIMITATIONS
Traditionally, microorganisms introduced during the drilling and completion phases and/or in the gathering and transportation phases have been controlled with chemical biocides. To work, biocides must come in contact with the microorganism, since they are targeted to damage the cell wall or disrupt the process of protein synthesis. Biocides pose significant health hazards, and their use is strictly regulated in most countries. Personnel using hazard-rated biocides are required to wear special protective equipment and undergo training on correct handling procedures, disposal techniques, spill avoidance and proper dosing requirements—all critically important in avoiding health, safety and environmental incidents.
Expertise is also required to select the right biocide so as not to interfere with the desired properties of the entire fluid system. Otherwise, chemical compatibility issues involving pH, temperature, salinity and dissolved or non-dissolved materials can occur, rendering the treatment ineffective and potentially damaging other additives.
ULTRAVIOLET BACTERIA CONTROL
Halliburton’s CleanStream system uses UV light to control bacteria in oilfield and pipeline applications while minimizing or eliminating the need for hazardous biocides.
The process, which is widely used in water treatment, food processing and hospitals, is simple and highly effective. As fluids flow through specialized chambers in a mobile unit, the fluid is irradiated with UV light. As this light passes through the liquid media, it is absorbed into the bacteria’s cell wall where it damages the organism’s DNA structure, killing the bacteria colony by rendering it unable to produce proteins or to replicate.
During field trials, this UV light bacteria-control process deactivated waterborne microorganisms within microseconds. At treatment rates of up to 120 bbl per minute (bpm), recorded disinfection quality was equal to or better than with chemicals. The effectiveness of the UV light process is dependent on: • The rate of fluid flow • The intensity of the UV lights • The transmittance level (T) of the fluid (i.e., its ability to let incoming radiation pass completely through as measured by the ratio of incident radiation to transmitted radiation).
For best results, it is recommended that T be measured at a radiation wavelength of 254 nm, which is in the germicidal UV-C spectrum.
Field data indicates that a transmittance rate of at least 50% at 80 bpm provides a minimum standard and will produce successful results. Should the liquid contain a high level of non-dissolved solids that could potentially block the light and limit transmittance, it may be necessary to place filters between the water source and the service unit to ensure high-quality performance. Pre-job testing and onsite quality-control monitoring permit this determination to be made.
Finally, it should be noted that while this new process is highly effective at killing bacteria that are already present, it does not provide residual kill capacity to address potential recontamination. Where recontamination is a concern, a low dose of biocide (about 10% of the usual dose) can be used as a supplement. For example, a 5 million-gallon water frac treatment that normally requires 5,000 gallons of biocide can now be treated using one UV light bacteria-control service unit and 500 gallons of biocide to address recontamination. If wellsite logistics permit the utilization of UV light service on the fly, biocide usage can be reduced to zero unless long-term protection is desired.
SAFETY CONSIDERATIONS
Unlike biocides, the UV light bacteria-control process does not require elaborate safety precautions or complicated procedures, eliminating or significantly reducing HSE issues like transportation of hazardous materials and the potential for material spills. Service is delivered by a mobile unit that contains no moving parts, Fig. 3. Sensors built into each chamber are combined with a computer control system to monitor UV light intensity, electrical current and chamber temperatures, helping to ensure a safe working environment.
|
Fig. 3. During field trials, the UV light bacteria-control mobile unit deactivated waterborne microorganisms at rates of up to 120 bpm.
|
|
Should a drop in light intensity occur, the control panel will display an alarm to notify the operator. Because each chamber has multiple bulbs, losing one will not disable the system. The incident rate of bulb failure is less than three bulbs per 100 million gallons treated. If a significant number of bulbs were to fail, the transfer rate may require adjustment to maintain effective bacteria disinfection. In the unlikely event of a major disruption, a bypass manifold isolates the UV chambers while allowing fluid to continue flowing through the unit, assuring that no disruption occurs in essential operations and permitting real-time repairs to be made.
RESULTS
In a series of applications in the Haynesville Shale formation, the UV light process has been shown to reduce bacteria at a rate comparable to those of chemical biocides without any of the hazards associated with biocide use.
These treatments began in April 2009 and are being conducted by EOG Resources, which has to date used the UV light bacteria-control process on 11 multistage horizontal wells in East Texas. This region provides an excellent testing environment since its warm temperatures, high rainfall levels and abundance of organic matter can make bacteria control a challenge even with aggressive biocide use. There was also a desire to minimize or reduce the potential environmental hazards associated with biocides.
Results to date indicate that water treatment using the UV light bacteria-control process is beneficial and cost-effective. Current plans call for utilizing the system on six additional wells through the end of 2009, after which a determination will be made on how to proceed going forward.
Expectations are that the UV light bacteria-control process will play an enhanced role on the remaining wells. Currently, small amounts of biocides are being used to disinfect tanks before UV light-treated water is introduced into them. Based on the pending review, it is anticipated that biocide use can be discontinued on future wells in the program.
Performance results presented here for two wells in this ongoing field trial are representative of the overall performance of the UV light bacteria-control process.
Watkins-1H well. This eight-stage horizontal well in Shelby, Texas, was successfully drilled to 14,888 ft MD. During the three-day operation, about 3.4 million gallons of water were treated with the UV light bacteria-control process at an average rate of 80 bpm. Transmittance was monitored during the operation to ascertain water clarity and averaged an acceptable 54.6% at a wavelength of 365 nm.
Water samples were gathered on the input and output side of the UV light mobile unit, with serial dilution tests performed on stages 1, 3, 5 and 7 to determine the effectiveness of treatments.
Testing was conducted using the industry-standard Optimization of Biocide/Bactericide Concentration for Water Treatment procedure. Aerobic-culture media vials containing phenol red-dextrose broth were used to detect the presence of aerobic bacteria. Anaerobic-media culture vials contained a sulfate solution with an iron nail, Fig. 4. Before the UV light bacteria-control treatment, testing revealed a contamination level of 1–10 million colony-forming bacterial units per cubic centimeter (cc), Fig. 4a. Yellow vials indicate the presence of bacteria; red vials are bacteria free. After the UV light bacteria-control treatment, testing showed just one to 10 bacteria per mL for an effectiveness rate of 99%, Fig. 4b.
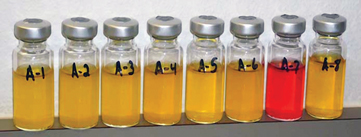
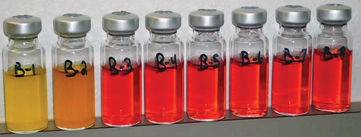
|
Fig. 4. Watkins Stage 1 aerobic test results.
|
|
In the anaerobic tests, before the UV light bacteria-control treatment, testing revealed an estimated 10 to 100 colony-forming bacterial units per cc, Fig. 5a. Black vials indicate the presence of SRBs. Clear vials are bacteria free. After the UV light bacteria-control treatment, testing showed no SRBs for an effectiveness rate of 100%, Fig. 5b.
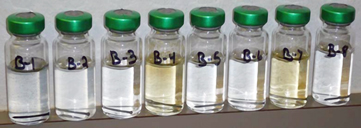
|
Fig. 5. Watkins Stage 1 anaerobic test results.
|
|
The results of the serial tests show an average aerobic bacteria reduction of 94.75% and an average anaerobic bacteria reduction of 97.48%, Fig. 6. These results are comparable to bacterial reduction rates associated with chemical biocides but without the environmental hazards associated with biocide use.
|
Fig. 6. Results of all Watkins tests.
|
|
Gammage-1 well. This nine-stage Haynesville Shale well in Nacogdoches, Texas, was drilled to 16,070 ft MD. During fracing operations, the UV light bacteria-control process treated about 3.7 million gallons of water at an average rate of 80 bpm. Serial tests were performed on stages 1, 3, 5, 7 and 9 using the standard testing procedure employed on the Watkins-1H well. All stages showed excellent results for both aerobic and anaerobic bacteria with reductions of 99% or greater consistently recorded. Results for all tests on the Gammage-1 well are shown in Fig. 7.
|
Fig. 7. Results of all Gammage-1 tests.
|
|
CONCLUSION
Through ongoing applications in a challenging environment, the UV light bacteria-control process has demonstrated that it can minimize the amount of chemical biocides that are injected into reservoirs and released to the environment. This technology, suitable for oilfield and pipeline operators, represents a viable bacteria control method.
|
THE AUTHORS
|
|
Kembe Kleinwolterink has been overseeing the field trials of the UV light bacteria-control process since it was first deployed in Kilgore,Texas. Having graduated from Iowa State University with a BS degree in mechanical engineering, he worked for Halliburton as a Field Engineer in Production Enhancement. Kleinwolterink is currently the Halliburton District Technical Manager for the Kilgore/Bossier City District.
|
|
|
Brandon B. Watson is an Account Representative for Halliburton in Tyler, Texas. Watson has a BBA degree in management and a BBA degree in human resource management from Lamar University in Beaumont, Texas. During the last three years, he has been Halliburton’s in-house engineer for EOG Resources in Tyler, Texas. Prior to that assignment, Watson was a Halliburton technical professional in Kilgore, Texas.
|
|
|
Dave Allison, located in Duncan, Oklahoma, is responsible for introduction and utilization of new technology for Halliburton’s Production Optimization and Conformance Service Lines. He was a Product Champion for Swell Technology and has managed new product development activities for cementing and production enhancement activities. Allison, who holds multiple patents, has published papers on stimulation, completions, sand control, coiled tubing, tubing-conveyed perforating and cementing. He holds a BS degree in civil engineering from the University of Pittsburgh and a MS degree in engineering management from Oklahoma State University.
|
|
|
Matt Sharrock is a Petroleum Engineer for EOG Resources in Tyler, Texas. He has a BS degree in petroleum engineering from The University of Texas at Austin and a MBA from The University of Texas at Tyler. During the last year, Sharrock has been designing completions for the Haynesville reservoir. Prior to that assignment, Sharrock worked in the reservoir, drilling, completion and production disciplines in the ArkLaTex and Mississippi area for EOG Resources.
|
|