Technology solutions help optimize drilling performance in tight-margin plays.
C. L. Brillon and R. S. Shafer, ConocoPhillips, and S. Segal, Schlumberger
Coiled Tubing Drilling (CTD) has revolutionized the shallow-gas drilling market in Western Canada. Increasing costs have driven operators to test the traditional limitations of CTD. Using technology innovations coupled with changes in drilling techniques, ConocoPhillips has been successful in improving CTD efficiency. The company has recently tackled the challenge of expanding CTD capabilities in two important areas: directional drilling and deep vertical drilling.
INTRODUCTION
Recognizing that there are some aspects of well construction that are best accomplished with a rotary drilling unit, and that there are other tasks best served by using Coiled Tubing (CT), ConocoPhillips proved that hybrid drilling units have a major effect on controlling drilling costs. These rigs perform well when drilling large-diameter surface holes and when assembling casing strings. In addition, they mobilize quickly and have short rig-up/rig-down times, Fig. 1. Generally, hybrid rigs are capable of high ROP. In fact, it is not uncommon for a hybrid CTD rig to drill two shallow gas wells per day during the summer.
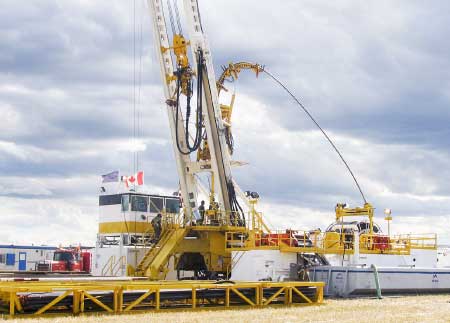 |
Fig. 1. A hybrid drilling unit is easily configurable from rotary drilling mode to CTD mode. As the derrick is folded down, the coil rises into position.
|
|
CTD rigs reduce overall drilling time by eliminating drill pipe connections, Fig. 2. CTD rigs maintain the well under control all of the time, however past experience with CT revealed limitations. When drilling directional wells with CTD using a mud motor and an adjustable bent sub for steering, borehole diameters were limited to about 6¼-in. In addition, steerability control became problematic with increasing depth. When drilling vertical wells with CT, drillers had difficulty maintaining verticality below about 5,000 ft (1,500 m).
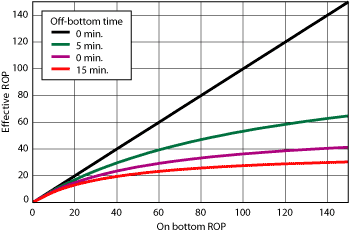 |
Fig. 2. Effective ROP for conventional drilling must include off-bottom time while making connections or performing directional surveys.
|
|
Solving directional-control problems and extending CTD depth range will provide access to a large number of Western Canadian Sedimentary Basin plays. The operator combined hybrid drilling unit with new CTD steering technology in a controlled two-phase test. The first phase was intended to address directional steerability issues. Using lessons from the first phase, the operator hoped to be able to significantly extend the practical CTD depth range.
BALANCING THE ADVANTAGES
Conventional drilling can deliver high ROP’s while on bottom, but, in many cases, these are offset by connection time. Making short trips to ensure proper hole cleaning also takes additional time. Accounting for connection and short-trip time, effective ROP bcomes much less than actual ROP. As the ROP is increased, this off-bottom time has a greater impact on drilling costs. In hard formations with low ROP, the connection time becomes less of a factor. However, in hard-rock drilling where directional control is required, connection time, survey time and the large amount of time necessary to orient the drilling motor all contribute to off-bottom time and, thus, reduce effective ROP considerably.
In CTD, all rotation comes from one source, the mud motor, so ROP is limited by the maximum motor speed. With conventional rotary drilling, the motor speed is complemented by drillpipe rotation, transferring greater rotational speed to the bit. To offset this advantage, CTD campaigns need to be properly planned and executed.
CTD can bring additional benefits in safety. Current rig designs have incorporated many automated features reducing personnel contact with equipment.
FIELD TESTS
Phase 1 points the way. To address the problem of directional control, the operator turned to Rotary Steerable Systems (RSS). These are well suited for CT applications and offer several unique advantages:
- Tool communication and directional surveying while drilling
- Equipment availability in hole sizes larger than 6¼-in.
- Standard conventional-drilling BottomHole Assemblies (BHA) are used
- No off-bottom time required to orient the toolface, compared to ratchet-type orienting devices used with standard adjustable bent subs
- No difficulties orienting the BHA due to drag
- No complicated surface system to control wireline-orienting devices
- Reduction in borehole tortuosity and the elimination of slide drilling
- Improved ROP by maintaining full WOB.
The operator chose the fully rotating PowerDrive family of RSS tools from Schlumberger, which have previously been used successfully in this hybrid drilling technique. Communication with the tool is achieved by adjusting the pump flowrate to specific levels for designated time periods in a defined sequence. These downlink pulses, sent through the mud column, activate new steering-orientation settings. Meanwhile, the RSS continues to drill, eliminating off-bottom time and maximizing effective ROP.
One of these tools is the PowerV vertical drilling system, which automatically maintains borehole verticality. The operator identified borehole drift as one of the problems addressed in the tests. The vertical drilling system requires no interaction by the driller because it senses the slightest deviation from vertical and applies automatic correction via the RSS pads to bring the borehole back to vertical, Fig. 3.
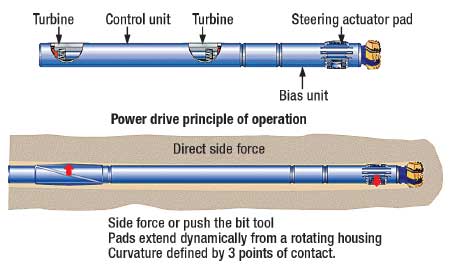 |
Fig.3. RSS/BHA schematic.
|
|
Three initial wells targeting the Belly River Formation were selected for the steerability test. These wells ranged from 2,132-ft to 2,624-ft (650-m to 800-m) TVD. The typical well profile in this area is a simple build-and-hold, with DogLeg Severity (DLS) limited to 5°/100 ft (30.5 m) and maximum deviation of 45°, Fig. 4. A hybrid CTD rig was chosen to drill the wells. All three wells were well within the rig’s capability in terms of borehole diameter and TD. While real-time directional data was sent uphole during drilling, the tool string configuration called for the drilling motor to be placed between the direction and inclination sub and the RSS. This configuration prevented real-time confirmation of the RSS’s reception of steering commands. However, previous experience indicated that it would work as expected.
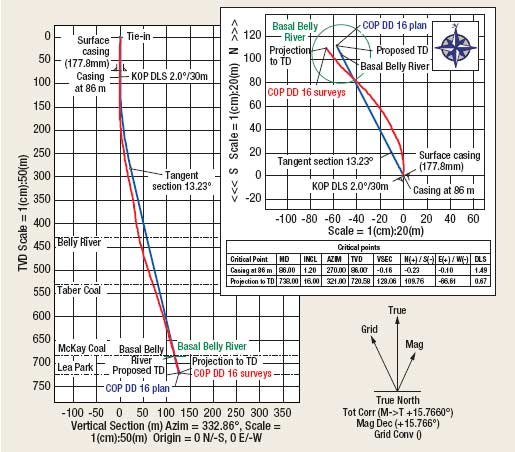 |
Fig. 4. Directional plan and actual plan for Well COP DD 16.
|
|
Objectives for the phase-1 tests were obtaining accurate directional surveys while drilling, establishing tool communication during drilling operations and demonstrating that the directional assembly could produce the required DLS.
The first test well had tool problems due to an incorrect pump-liner size that affected mud flowrate and interfered with tool communication. However, the problem was resolved and the second well was successfully drilled with CT. Different problems were encountered on the third test well, preventing the RSS to kick off to drill the directional section. The tool problem in the RSS assembly was not related to CTD. Accordingly, despite the problems on the first and the third wells, sufficient lessons from the second well proved that they could be steered accurately using RSS with CTD. The results from the second well satisfied all of the phase-1 objectives.
A secondary objective of the tests was to evaluate the use of the hybrid drilling unit. A comparison of CTD using the hybrid rig versus drilling with a conventional drilling rig and jointed pipe showed that CTD gained a clear efficiency advantage, Fig. 5.
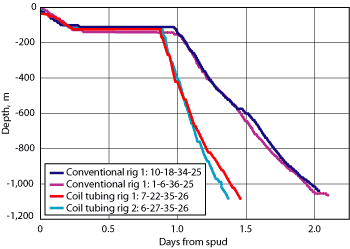 |
Fig. 5. Compared with conventional rotary drilling using jointed drillpipe in moderate formations, CTD shows a clear advantage..
|
|
Phase 2 goes straight and deep. The rig was depth-rated to 7,216 ft (2,200 m) and the BHA design included drill collars to maintain CT tension. Two techniques were tested to maintain borehole verticality; the first, using a drop-bit and a low-speed, high-torque motor and maximizing hydraulic differential pressure to increase WOB. The second technique used the vertical drilling sytem. A polymer mud system was chosen in lieu of the gelled-chemical mud used previously. Polymer muds protect the formation from high filtrate invasion, thereby improving the quality of openhole logs.
Objectives of phase 2 were establishing successful CTD capability past 3,570 ft (1,500 m), providing effective deviation control, and decreasing overall drilling time.
Records from offset wells indicated no problems with borehole deviation on the first well of phase 2. However, the second well was in a difficult-drilling area. Nevertheless, the remedies for deviation control were considered sufficient.
In the first test well, deviation below the casing shoe rose to 3.25° within 164 ft (50 m) and increased to 4.5° within the first 328 ft (100 m). The drop-bit technique was applied and deviation decreased quickly to 1°. However, while maximizing differential pressure, too much WOB was applied, eliminating the drop-bit correction. The drillers concluded that CT had an inherent problem of maintaining verticality, even though the BHA was designed to maintain string tension. It was suggested that, at a threshold, excess or minimal WOB caused different problems. The bit would not correct for deviation at minimal WOB; the bit would walk at excessive WOB. A safe drilling-parameter range was defined to achieve and maintain borehole verticality.
On the second well of phase 2, a deviation problem was anticipated from offset data. The well was drilled using RSS controlled by the vertical drilling system. Surface casing was set at 3° deviation, so the vertical-drilling-system tool was expected to immediately guide the wellbore trajectory back to vertical after drilling out of the shoe. But deviation built to 4.5° within 328 ft (100 m) of the shoe. The RSS was replaced and deviation rose to 6.3°. The previous RSS was tested and found to be working properly. Drilling ahead with a reduced WOB while waiting for a drop bit to be delivered, the RSS began to bring the well back to vertical and deviation was reduced to 1°. WOB was then increased in an attempt to maximize ROP, but deviation again climbed to 2°. When the bit reached 3,936 ft (1,200 m), the RSS was able to drill a vertical hole, even when ROP was maximized. Analysis of the BHA indicated it had a natural tendency to build inclination, which increased with more WOB. The vertical drilling system could not overcome this build tendency.
The third well of phase-2 testing targeted the deeper Turner Valley Formation. Planning and preparation for the job was similar to that for the second well. There was no offset data at the relevant depths. The Turner Valley Formation is a limestone formation with high compressive strength, requiring a three-cone diamond-insert bit. Despite the use of a 6¾-in. RSS and an additional stabilizer, the BHA rigidity was insufficient to prevent inclination build. Deviation built to 4.4° within the first 262 ft (80 m) out of the casing shoe. After removing two of the stabilizers, the vertical drilling system tool was able to reduce inclination to 1° and maintain it at that level. Subsequently, severe bit-wear problems occurred which were not caused by CTD; drilling was suspended at 7,019 ft (2,140 m).
Despite several unrelated problems, the operator concluded that two of the three phase-2 objectives had been satisfied. CTD depth range was extended below 7,000 ft (2134 m), and drillers were able to control deviation after determining the WOB threshold. Overall, effective ROP was at the field average. The third test well encountered geological conditions, unrelated to CTD, which caused excessive drilling time.
CONCLUSIONS
CTD offers advantages in high-ROP environments. However, even in hard-rock drilling situations, the ability to maintain the bit on bottom, eliminate connection and surveying times and achieve directional control without the use of a traditional orienter saves additional time that tips the scale in favor of CTD.
Both drop-bit technology and RSS tools can successfully control deviation and regain verticality in a deviated well. It appears that drop-bit technology is at a disadvantage due to reduced ROP when compared to standard PDC-bit designs. Additional testing is still required in order to optimize the BHA for use with RSS. Because rotary drilling can be used to augment motor power, motors used in CDT applications should use the even-wall design to minimize stalling under high-torque conditions.
ACKNOWLEDGMENTS
This article is derived from AADE paper AADE-07-NTCE-31, “Pushing the Envelope with coil tubing drilling,” presented at the 2007 AADE National Technical Conference and Exhibition, Wyndham Greenspoint Hotel, Houston, April 10-12, 2007.
BIBLIOGRAPHY
C.L. Brillon, R.S. Shafer, A. A. Bello: “Pushing the Envelope with Coil Tubing Drilling,” AADE-07-NTCE-31, AADE National Technical Conference and Exhibition Wyndham Greenspoint Hotel, Houston, Texas, April 10-12, 2007.
Shafer, R.S.: “Step Change in Remote Exploration,” SPE/IADC 105051, SPE/IADC Drilling Conference, Amsterdam, The Netherlands, February 20-22, 2007.
Bourgoyne A.T., Chenevert M.E., Millheim K.K., Young F.S.: Applied Drilling Engineering.: SPE Testbook Series Vol.2, Society of Petroleum Engineers, Ninth Printing 2003.
Steve Devereux: Practical Well Planning, PennWell Publishing Company, 1998, ISBN 0-87814-696-2.
Gilles Gabolde, Jean-Paul Nguyen, Drilling Data handbook, Eight Edition, Editions Technip, 2006.
C. Pratten, Rotary Steerable Systems in the Gulf of Mexico - A Step Change in Drilling Performance, AADE 01-NC-HO-22, AADE 2001 National Drilling Conference, Houston, Texas, March 27 - 29, 2001.
F. J. Schuh, P. Herbert, J. Harrell, The New Generation of Rotary Systems May be Closer Than You Think, AADE-03-NTCE-02, AADE 2003 National Drilling Conference and Exhibition, Houston, Texas, April 1-3, 2003.
C. Sidwell, J. Jares, M. Durant, Rotary Steerable in 6” hole Key to Economic Wellbores, AADE-03-NTCE-03, AADE 2003 National Drilling Conference and Exhibition, Houston, Texas, April 1-3, 2003.
C. Lenamond, L. Marques, M. Anderson, S. Mota, Performance Gains for Rotary Steerable Through Specialized Bit Design, AADE-05-NTCE-46, AADE 2005 National Drilling Conference and Exhibition, Houston, Texas, April 5-7, 2005.
|
THE AUTHORS
|
|
Chris Brillon is a drilling engineer currently working in ConocoPhillips’ Wells Technology Group in Houston, Texas. He started as a drilling engineer with ConocoPhillips in 2005 in Calgary, Alberta. Brillon has been involved with CTD programs in Holland, Australia, Canada, and the US. He graduated in 2002 from the University of Saskatchewan with a BSc in mechanical engineering.
|
|
|
Randall Shafer works in ConocoPhillips’ Corporate Technology Group in Houston, Texas. His focus is Arctic drilling and extending new technology such as casing drilling and coil tubing drilling throughout the company. He has worked in Russia, Norway, Africa, and the UK. Shafer has a BS degree from Penn State and an MBA degree from the University of Chicago.
|
|
|
Steven Segal is the sales and marketing manager for Schlumberger Drilling & Measurements in Canada, based in Calgary, Alberta. He started with Schlumberger in 1991 in Aberdeen, Scotland and has held numerous field, technical and managerial roles over the past 16 years. Segal has a master’s degree in Electrical Engineering from the University of Nottingham, UK.
|
|
|