PETROLEUM TECHNOLOGY DIGEST
Horizontal drilling increases injectivity and recovery: An update
Depleted reservoirs get a second chance with low-cost drilling and completions.
Scott Robinowitz and Robert V. Westermark, Grand Directions, Tulsa, Oklahoma
Grand Resources is applying horizontal waterflooding in various Midcontinent fields. The company is quickly learning how to apply low-cost horizontal drilling for injectors and producers to optimize production.
Further developed with US Department of Energy (DOE) funding, this technology has revived oil production from an abandoned oil field on Osage Indian tribal lands, in other fields in northeastern Oklahoma and in a shallow field in southeast Kansas.
Grand focused first on applying horizontal waterflooding in the 25–50 md permeability portion of the shallow Bartlesville formation. We published this story in this space in the March 2004 issue. Results from the first field, Wolco, were not available at that time. This article provides results on that field and other fields drilled since our 2004 report.
REVIEW
In general, success depends on understanding the reservoir, controlling costs, willingness to learn from failures, perseverance and meticulous planning to minimize the chance failure. Since low cost is one of the key enablers to the redevelopment process, it is essential that costs be aggressively contained and closely monitored on all projects. Drilling costs, which include a new vertical well drilled through the target formation, a full suite of logs, casing cemented to surface and cutting the curve and lateral section of the well, consistently average less that $200,000.
Drilling. In some cases, existing—often very old—wells are re-entered. All existing wells in a prospective area are reviewed. If the risk-weighted cost of using an exiting well exceeds the cost of a new well, which occurs frequently in this shallow production region, a new well is drilled. If a new well is drilled, the vertical portion is contracted out, including drilling and cementing casing. Typically, the target formation is fully penetrated for formation evaluation in the vertical section.
A tight, 70- to 90-ft radius curve is cut from below the casing. The target reservoirs are relatively shallow, about 1,600 ft. An inexpensive, short radius, rotary drilling system, invented and licensed by Amoco (BP), reliably builds this section. Periodic downhole surveys are made through the drill pipe to ensure the well is staying on course. Water or mud is the drilling fluid used to drill the curve. Grand has implemented numerous techniques, advancing the short radius technology as a result of drilling these projects.
When the curved section is done, a new BHA is picked up for the horizontal leg. Reservoir evaluation guides the well path parallel to the observed natural fractures, to minimize short-circuiting of the waterflood. Foam/air is used on this section, with a modified air hammer drilling assembly. Lengths up to 1,250 ft have been drilled this way.
Horizontal injectors are placed near the bottom, producers near the top. Modeling and experience agree that this produces a more efficient sweep than a five-spot vertical waterflood.
Completion. The curve and horizontal portions of the well are openhole completed, with no stimulation required. Economics favor this approach, so good formation integrity becomes one of the ideal factors in well-candidate selection. However, the cost of running and cementing a liner is not a show-stopper. The short-radius of the curve allows the use of a conventional downhole pump assembly in the vertical well, with a relatively low-pressure head on the formation.
Heterogeneity. From years of conventional waterflooding, channeling, which is the short-circuiting of flowpaths, has occurred, accentuating the natural heterogeneity of the formation, which is one reason why recovery rates were as low as 15% of the OOIP, even after waterflood. The other reason is that the injection pressure in a vertical well would often exceed formation fracture pressure to achieve efficient flowrates, thereby adding to the water recirculating/poor sweep problem.
Formation heterogeneity usually exists in all aspects of the reservoir: permeability, porosity, fracture density and hydrocarbon saturation. Typically, the mudlog and simple observation of the pit fluids provide a real-time drill stem test, presenting reservoir quality and hydrocarbon saturation. Returns going to the pit will show no hydrocarbons encountered for a few hundred feet followed by strong oil producing sections, and again followed by sections of no hydrocarbon shows.
Formation evaluation. Conventional well logging tools would not pass through the short radius curve. Grand considered various delivery systems, including tractors and drill pipe. Eventually, the company developed a unique logging procedure. Conventional, small diameter logging tools, including gamma ray, density, induction and acoustic borehole televiewer for fracture identification, were modified and were conveyed by conventional sucker rods. To extend the lateral distance of the sucker rod conveyance system, roller rod guides were employed, helping to reduce friction, increasing the distance that the logging tools could be pushed.
FIELD EXPERIENCE
Wolco pilot. The Bartlesville sandstone in northeastern Oklahoma has produced more than 1.5 billion bbl of oil. Recovery is often less than 15% of the OOIP. A Bartlesville reservoir was chosen as Grand’s first horizontal waterflood project. Vertical well logs from the early 1980s indicated a thick, continuous sand with 50%+ oil saturation and 17% porosity, making the pilot appear suitable. Although the pilot area had not been previously flooded, it was located adjacent to an area that had been. The pilot was also located close to an area of the reservoir that contains a 28% porosity, lower member of the Bartlesville formation.
Figure 1 shows the plan view of the original and revised plans. Wells were drilled in a toe-to-heel orientation, consistent with recommendations made in the literature. Injection of 2,000 bwpd was achieved on vacuum or at a zero surface-injection pressure. However, a step-rate test using a BHP sensor indicated that a slope change in the pressure/rate chart occurred at 0.35 psi per ft. This meant that the fracture-parting pressure had been exceeded at a pressure less than the hydrostatic head of water, making it necessary to limit the injection rate.
An injection-profile survey determined that all of the injected water was leaving the wellbore within the area of the curve. Preferential flow out of the heel of the injector is consistent with industry experience. During drilling of the curve, circulation was lost, suggesting that fractures may have also played a role.
Although total fluid injection and withdrawal were as expected, with both the productivity index and the injection index exceeding original estimates, oil production was disappointing, Fig 3. New horizontal well logs indicated the culprit was oil saturation that was greatly below the original 1980s log projections.
The pilot configuration was revised, the previous horizontal producers were plugged back, and new laterals were drilled in the opposite direction into a thin rim of oil, Fig. 1. The revised Wolco pilot has been successful, with producing rates averaging 15 bopd. An economic project has been achieved, but high oil prices have been a key factor.
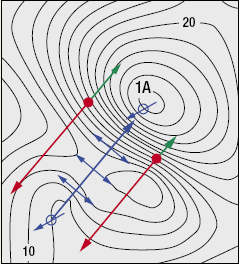 |
Fig. 1. Original pilot had two producers (red, to the SW) and one injector (blue, to the NW). New plan drilled two short producers (green, to the NW) from the same boreholes, but in the opposite direction, and one vertical injector (1A).
|
|
Avant expansion. In this project, located east of the Wolco pilot area, drilling horizontal laterals in the upper “C” zone of a pressured reservoir, containing a high-permeability lower “D” zone, led to significant oil production.
On offset operator has been injecting water for the past 20 years into seven vertical injection wells at over 4,000 bwpd. At project initiation, about 25 bopd was being produced at a 98.5% watercut from eight producing wells. In this area, the high-permeability “D” zone has a thickness ranging from a few feet up to 30 ft, while the “C” zone above it ranges from 40 to 100 ft.
Because of extreme permeability variation within the reservoir, most of the injected water likely flowed through the “D” sand, causing much of the oil in the upper reservoir zone to be bypassed.
Two wells located in an adjacent quartersection to the ongoing water injection, originally drilled and completed in 1914, were re-entered and drilled horizontally as producers in close proximity to one another. They have responded favorably, with a combined production of about 40 bopd and 600 bwpd. A third well has not responded favorably to date, although good oil saturation in the “C” zone was indicated on the logs.
Two other 1915 vintage vertical wellbores in the immediate vicinity were re-entered and drilled horizontally resulting in an additional 50 bopd x 500 bwpd.
The combined production realized from the Wolco field and the Avant expansion, (Fig. 2) is 105 bopd x 1800 bwp. This production has been realized from an area walked away from by the industry as depleted and uneconomical.
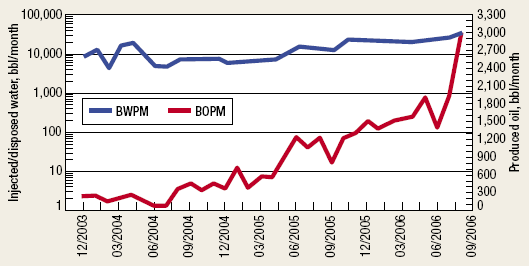 |
Fig. 2. Wolco and Avant Expansion production, original, and after re-drilling / expansion (right of bar)
|
|
Bird Creek field. In this field, which was discovered in 1904, horizontal wells reduced the effects of water coning previously seen in vertical wells, due to the unfavorable mobility ratio between moderately heavy oil and water. The field produces from both the Bartlesville and the underlying Tucker sand, located about 70 ft below. The Tucker is characterized by 18% average porosity, 300-md permeability, 52-cp oil viscosity and 115-psi reservoir pressure. It was the principal target for horizontal well technology. Conventional vertical wells produce 2–3 bopd at a 98% watercut.
The basic procedure used in the Tucker was to drill horizontal producers in the crest of the formation. Seven horizontal wells have been drilled to date, generally 300–400 ft long laterally. The successful horizontal wells are producing 15 bopd, each, at an oil cut of 25%.
It has been difficult to define the geology of the reservoir where there have been few complete penetrations of the sand. Because of this, some of the horizontal wells were drilled too close to the water/oil contact and have not been successful.
Editor’s note: Additional details about the Kansas field, West Savonburg, can be found in paper SPE 99668. 
|
THE AUTHORS
|
Scott Robinowitz, vice president, Grand Directions, Inc., has experience in reservoir engineering and modeling, well completions, equipment design, field operations, environmental compliance and technology integration. scott@granddirections.com |
|
R.V. “Bob” Westermark is president of Grand Directions, a subsidiary of Grand Resources, Inc. He managed Amoco’s Catoosa Research facility after working 24 years for various producing companies.
|
|
|