Well Control and Intervention
Igniting a blowout depends on careful planning and evaluation
Making the decision to ignite a blowout should be done carefully, aided by pre-written plans and forethought. Many, but not all wells are voluntary ignition candidates. Setting certain blowouts on fire may be mandatory, including some H2S wells.
Daniel F. Eby, P.E., Engineering Manager, Well Control, Cudd Well Control, Houston
The decision to ignite a blowout should not be taken lightly. Purposely setting a well on fire can have serious consequences. Loss of the rig, and the ensuing well control operations, can be very costly.
However, in certain cases, it may be desirable to set the well on fire. In most cases, it is prudent to consider the relevant factors, if the well blows out and igniting the flow is an option. Examine the following topics when considering voluntary ignition during well planning and operations:
- Well ignition and/or blowout contingency plan
- Ignition of non-toxic blowouts
- Ignition of hydrogen sulfide (H2S) wells
- Ignition methods
- Radiant heat.
WELL IGNITION PLAN
API RP 68 (Recommended Practice for Oil and Gas Well Servicing and Workover Operations Involving Hydrogen Sulfide) states that a Well Ignition Plan (WIP) should be written for wells containing dangerous H2S levels. Absent a formal plan, operators should at least consider that there might be circumstances requiring the ignition of a blowout. This is true for H2S wells, as well as non-H2S wells, so a WIP should be considered. It can be written as a stand-alone document or included in a Blowout Contingency Plan (BCP).
In addition to an H2S presence, the blowout flow’s nature can be a major factor in deciding to light the well. Not all wells should be ignited, even some H2S wells. Here are some examples:
- Flange or other leaks that may be controlled by pumping junk shots
- Drill pipe blowouts, where the flow exit point is advantageous to gas dispersion
- Low-rate blowouts that may be controlled by momentum kills
- Wells that have a high likelihood of bridging
- Wells for which the blowout control method is not difficult and can be employed fast
- Remote well sites, where there is no immediate threat to life
- Wells where environmental damage will be minimal, or where the pollution is easily controlled
- Wells that have a high content of CO2, water or other constituent that will likely prevent the well flow from combusting
- Locations where there will be undesirable combustion of radioactive sources or other hazardous materials at the wellsite.
These items should be clearly defined in the WIP or BCP.
These plans should include the decision-making process for lighting the well. API RP 68 recommends that on-site operator personnel be empowered to ignite the well and to include this in the WIP. Empowering personnel before the event to ignite the well will ensure that the operator’s management team agrees with operational staff decisions. Eliminating the inevitable delay when management has to be consulted is beneficial. Generally, the sooner the well is ignited, the better the likelihood that ignition will protect personnel.
The presence of a WIP or policy greatly enhances the operator’s decision-making. Blowouts can be stressful for personnel that do not normally deal with them. If a written plan is in place and practiced, the operator can deal better with all issues presented by a major well control event.
NON-TOXIC BLOWOUTS
Igniting non-H2S blowouts is generally not considered when developing a WIP. Although rare, wells in this category can be voluntary ignition candidates. There are factors that may require that the well be set on fire:
- Pollution impact. Sometimes, it is desirable for pollution reasons to conduct well control while the well is on fire. If the blowout effluent contains oil or condensate that may cause serious pollution, igniting the well may be desirable. In one such example, a well was producing high volumes of condensate that would have entered the public water supply of a major North Texas city, if the well had not been on fire.
- Economic impact. If the well is among or near the general public, it may be desirable to ignite the blowout. Large-scale evacuation of local residents for extended periods of time can be costly, both directly and indirectly. From a public relations standpoint, be sure to explain the situation adequately. The general public is likely to misunderstand any decision to set a well on fire.
HYDROGEN SULFIDE BLOWOUTS
H2S dangers are well known and documented. Blowouts in H2S wells can pose immediate dangers to life and health. Operators drilling wells where H2S is a known hazard may or may not have a clear-cut policy regarding ignition of the well if a blowout occurs.
API RP 68 states that well ignition should be considered as a last resort when human life is endangered, or there is no hope of controlling the well under prevailing conditions. These bases are generally sound. Any threat to human life from an H2S blowout should mandate that the well be ignited.
However, deciding whether there is no hope of controlling the well is subjective. Well control experts have experience in controlling wells that most operators’ drilling and production personnel do not possess. Situations that operator personnel consider difficult to control are often straight-forward to handle. They can be done in relatively short periods of time.
Burning H2S creates sulfur dioxide (SO2) that is also highly toxic. Therefore, the situation is still dangerous, and a safety system should be put in place to monitor for SO2.
Not all H2S wells have the same ignition criteria. Offshore well control can be much more difficult during a fire. Losing the offshore structure, due to fire damage, greatly complicates well control. Fire damage to a platform or jackup barge can be extensive, and debris removal can be lengthy. Secondary damage to the well from falling debris can, sometimes, render surface well control intervention impossible.
Other factors that may make ignition undesirable are:
- Damage to adjacent wells is likely. Heat damage can result in leaks or additional blowouts
- Damage to platform and general oilfield infrastructure, such as pipeline gathering systems, can also occur from fire
- Unknown platform stability in a fire situation for floating platform structures, such as TLPs and spars
- Modern offshore platforms have sophisticated fire suppression systems installed for the production and well bay areas. These systems are not designed to fight a blowout’s pressurized flow. However, the system may, in some cases, put out a blowout fire, if the well flow is small or the well partially bridges. If this happens, flow ignition will have not have made the blowout safer to control.
Weather offshore may also make dealing with H2S blowouts easier, because wellheads and rigs are elevated and are, therefore, more susceptible to wind that can disperse the flow. However, calm conditions can exist offshore, and wind presence cannot be relied upon as a safety factor.
IGNITION METHODS
Once ignition criteria are in place, and well conditions have been met, the flow is actually ignited. API RP 68 recommends that on-site personnel make the final ignition decision. API also states that the responsible person be designated in a WIP. Office-based supervisors should also be notified if time permits, and if the time required does not endanger personnel at or near the site. This implies that the well should be ignited in a short amount of time after the blowout occurs.
The tool used to light the flow is typically a flare gun. Numerous, different types of flare guns and flares are available. Each has its own characteristics regarding range, flare material and duration of flare burn. Most of the commercially available flare guns have limited ranges. Therefore, they may not be adequate for igniting the flow. Flare rifles are also available and are likely a better choice for safely igniting a blowout. The rifles have much greater ranges for their use.
Personnel safety is the most important factor in all well control operations. A well should not be ignited, if this will endanger the personnel charged with setting it on fire. If the ignition process poses a danger, it should be aborted and the area evacuated. Ignition should then be delayed until all risks have been mitigated, and the procedure can be done safely.
Every blowout is different, so the procedure for igniting a well cannot be written for every circumstance. However, certain procedures should be included in most situations, to safely ignite the flow. When the order to ignite a well is given, these guidelines should be followed:
- Evacuate all personnel
- Rescue injured personnel. Get them immediate medical attention
- If possible, divert the well to a pit and ignite the flow there
- If possible, limit the blowout’s exit point to a single source by closing BOP stack valves, tree and wellhead valves, chokes, etc
- Evaluate wind and weather conditions to ascertain whether the situation might endanger personnel
- Determine if ignition via a flare gun is possible from the facility, i.e., strong prevailing winds away from the firing point, H2S-free atmosphere, available cover from a flashback and clear escape access
- Establish the flare gun’s range and whether well access within this range is safe and possible, given the presence of H2S and heat radiation
- Clear all personnel, local residents, etc. within a 1-mi radius, except for personnel required at the firing base. The radius may have to be expanded, depending on the well’s flowrate and the H2S concentration. This distance should be determined whenever H2S contingency, well ignition and blowout contingency plans are written
- Approach the well from the upwind side while monitoring H2S levels. Once within a safe range, a single man should fire the flare gun and ignite the flow. Escape from the area should be made immediately, due to possible secondary explosions and falling debris
- Once ignition takes place, the well should not be approached until it stabilizes. Conditions should permit access with reasonable safety under strict supervision of well control specialists.
HEAT RADIATION
Heat radiation from a well fire should be considered when developing a WIP. Contingency plans should be developed that consider ignition consequences. If the decision to ignite has been made, the radiant heat effects must be tolerated. The “hot,” “warm,” and “cool” safety zones described in the Site Safety Plan must consider radiant heat effects generated by the fire.
The radiant heat generated will result in numerous issues that must be dealt with during the blowout intervention. Some of the more critical problems that the fire will present include:
- Over-pressure from ignition
- Secondary explosions from flammable materials, pressurized containers, oilfield explosives and/or gas accumulations inside rigs
- Debris created by the fire, including equipment, and on-site chemicals and radioactive materials
- Radiant heat effect on equipment – wellhead components; other wells on the platform or pad; equipment needed for intervention
- Additional time required to control the blowout – water availability, firefighting, wellhead removal/ replacement and capping
- Combustion of blowout effluent
- Radiant heat effect on personnel.
OVER-PRESSURE FROM IGNITION
Over-pressure from the gas cloud detonation can be very dangerous and damaging. In open areas, over-pressure from ignition dissipates naturally, but it can cause flying debris that endangers personnel. In a large gas cloud, concussion from over-pressure can be very dramatic. This is another reason that all personnel should be evacuated; care must be taken when igniting the well.
Over-pressure from a gas cloud explosion can be calculated using several different methods. The WIP can include calculations for different vapor clouds, so that decisions can be made in the ignition procedure and the distance required to safely light the well.
SECONDARY EXPLOSIONS
Secondary explosions are almost assured during a rig fire. Numerous items on rigs can be subjected to sufficient heat that causes them to explode. Accumulator bottles, oxygen-acetylene cutting equipment, diesel tanks, perforating charges and other common oilfield explosives, production separators and other production equipment, etc., can all be dangerous when a well is on fire. Thus, it is important to allow the situation to stabilize before making an assessment after ignition.
Gas accumulation inside rig structures is very dangerous. If this gas is not ignited, radiant heat and fire impinging on the structure can cause the gas inside to explode or ignite.
DEBRIS CREATED BY FIRE
Most rig fires create significant debris, removal of which can be a lengthy process, increasing the well control time in almost every event. The quantity of debris to remove is directly related to the operational environment. Onshore production fires usually have less debris to remove than offshore drilling rig fires, for obvious reasons. Oilfield chemicals can be very flammable and hazardous. Oilfield radioactive materials can also be a hazard if subjected to fire. Workers at the blowout must take necessary precautions when dealing with all kinds of debris.
RADIANT HEAT EFFECT
Fire-generated heat will likely render the wellhead unusable for capping. Depending on circumstances, the temperature at the well can reach 3,000°F. When the wellhead is subjected to high heat for extended time, it is usually cut off, and an emergency wellhead is installed. This process can be done while the well is on fire.
Fire can also damage nearby wells. In some cases, considerable time is spent constructing heat shields to protect other wells in the slip, well bay, or at the pad from radiant heat. Production equipment may also be damaged and can present a danger until hydrocarbons are purged from the system.
Equipment used to intervene must be protected from radiant heat. Corrugated tin is used to build heat shields for dozers, excavators, pumps, etc., that are required near the well. On inland water jobs, additional firefighting monitors are used to keep dredge barges, firefighting barges and tugboats cool while they are near the fire.
ADDITIONAL TIME REQUIRED TO CONTROL A BLOWOUT
Firefighting operations can require large quantities of water. Additional time will be needed during early blowout stages to set tanks or dig a pit for storing water. Well control experts use water as protection from the fire during the job. The volume of water required to manage the fire will greatly exceed the amount required to actually extinguish it when the well is ready to be capped. Thus, a great deal of time and energy is spent gathering and storing water. This is also true for managing runoff water used to protect personnel.
Fires can cause enough damage that it is not prudent to cap the well on the existing wellhead. When the damaged wellhead is removed, an emergency wellhead is installed, generally a low-pressure installation. Therefore, the well is usually not shut in after the capping BOP is installed, but the well is diverted to minimize wellhead pressure. A snubbing unit is then rigged up. The blowout is diverted during snubbing until the well is configured, so that it can be killed while minimizing wellhead pressure. These post-capping kill operations can be lengthy.
Capping the well while it is still burning involves safe, proven techniques. However, this takes additional time to build access ramps for the Athey Wagon used during capping.
COMBUSTION OF EFFLUENT
Incomplete combustion of blowout effluent can be a problem. Oil wells that do not burn cleanly can build up petroleum coke near the wellheads. This was especially true during well control in Kuwait after the Gulf War. Coke deposits formed because of the long time that many wells burned before blowout control began. A single well fire is not likely to burn for an extended period. However, formation of a coke deposit cannot be discounted.
Another side effect of incomplete burning is smoke. Weather conditions must be favorable, to prevent smoke from hindering work during the well job. This can even occur in gas wells, including a propane storage well fire.
Sustaining the fire can be problematic, with numerous reasons that it may go out. Water coning, partial bridging, solids production and other factors related to changes in flow characteristics have put out fires in the past, innumerable times. Thus, workers at the blowout should remain vigilant and be prepared to re-ignite the well at all times.
RADIANT HEAT EFFECT ON PERSONNEL
Radiant heat is calculated as heat flux. Well fires generate tremendous radiant heat. On-site personnel must endure and control the amount of heat to which they are subjected.
There is usually great interest in knowing “how hot will the fire be?” However, it is not possible to calculate the temperature that personnel will be subjected to during the job. Radiant heat is calculated as heat flux, or the amount of energy that flows through a given area in a specific time period. Typical values heat flux are in Table 1.
|
TABLE 1. Typical heat flux values. |
|
|
Heat flux
(btu/ft2/hr) |
Effect |
|
|
|
|
|
444 |
Heat flux from the sun on a clear day in the tropics |
|
|
2,030 |
Heat flux 10 cm away from a 100-W incandescent light bulb |
|
|
3,172 |
Causes burns to human skin after 10 sec |
|
|
15,859 |
Causes burns to human skin after 1 sec |
|
|
31,718 |
Heat flux from a propane torch at the flame tip |
|
|
317,181 |
Heat flux from an oxy-acetylene torch at the flame tip |
|
|
For comparison, the heat flux for an example blowout was calculated. The data are detailed below:
- 40-MMcfd blowout flowrate
- Blowout through 9-5/8-in. casing (exit diameter = 8-1/2 in.)
- Sub-sonic flow (atmospheric pressure) at the surface
- Well flow is 100% methane with no fluid
- Sensor height for the heat flux calculation is 5 ft above the ground
- Gas exit temperature = 75°F
- Meterological conditions set to worst case wind speed = 3.36 mph
These data are typical of a normally pressured, US onshore or offshore well. The data were input into Breeze Haz Professional Version 3.2.8 software to calculate heat flux from the example blowout. Calculated values for the flame characteristics are in Table 2.
|
TABLE 2. Flame characteristics. |
|
|
Calculated values |
Value |
|
|
|
|
|
Vapor density |
0.045 lb/ft3 |
|
|
Compressibility |
0.998 |
|
|
Flame extent |
101.61 ft |
|
|
Flame lift off |
23.75 ft |
|
|
Total flame height |
125.36 ft |
|
|
Average flame diameter |
34.57 ft |
|
|
The heat flux calculated for this example is in Fig. 1. The curve shows that the flux can cause burns in 10 sec as far away as 130 ft. The calculations are for a vertical fire, and the flux is equal in all directions around the flame. In other words, the heat flux values have a circular distribution. In actual fires, this does not normally occur until debris is removed from around the well, and the flow is vertical.
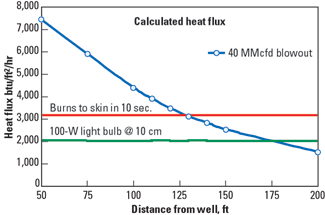 |
Fig. 1. This calculated heat flux is typical for a vertical fire in a 40-MMcfgd blowout.
|
|
Multi-dimensional fires are not likely to have circular heat flux distribution. Actual radiant heat distribution depends on debris around the well. As debris is removed and the area around the wellhead is cleared, heat flux will increase in some areas and decrease in others. Weather conditions will also have an effect. Strong winds will skew the distribution to the downwind side.
CONCLUSIONS
The decision to ignite a blowout cannot be taken lightly and should not be spur-of-the-moment. Planning and forethought will make the decision easier. The process should be outlined in a WIP or a BCP.
Non-toxic blowouts can also be candidates for voluntary ignition. This is highly dependent on numerous factors that should be examined prior to a blowout. H2S blowouts may or may not be candidates for voluntary ignition. However, most H2S wells are candidates for voluntary ignition.
Igniting the well should be done by individuals prepared to perform the job. A flare gun or rifle should be used from a safe distance to light the well as soon as possible. If a decision to ignite the well is made, the resulting fire’s effects are numerous and will need to be mitigated for the blowout’s duration. 
BIBLIOGRAPHY
1. Sensors Online website, October 2003.
2. American Petroleum Institute RP 68, “Recommended practice for oil and gas well servicing and workover operations involving hydrogen sulfide,” January 1968.
THE AUTHOR
|
 |
Dan Eby is manager, Engineering Services, for Cudd Well Control, a division of Cudd Pressure Control. He is involved in all phases of well control engineering, including blowout contingency planning, relief well planning, dynamic well kill design and execution, engineering and field operations. Mr. Eby has worked in more than 30 different countries and has 25 years of experience with several major oil companies. He graduated from Texas A & M University with a BS degree in building construction in 1977, followed by a BS in civil engineering in 1979. He is a licensed professional engineer in the State of Texas and a member of SPE, National Society of Professional Engineers, Texas Society of Professional Engineers, and IADC.
|
|
|
|