New Bit Designs
Halliburton Security DBS
Design science combines with application expertise to produce breakthroughs
Roller cone designs are inherently difficult to balance, due to the large number of design variables. To overcome this, Security DBS developed the patented Energy Balanced bit technology that enables a roller cone bit to be balanced, both by volume and by force, Fig. 1. Volume balancing equalizes rock removal among all the cones, while force balancing ensures all cones are subject to equivalent loads of weight-on-cone, bending moment and force-on-bearing. Thus, no one single cone or bearing system is over-stressed.
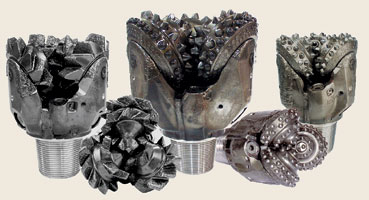 |
Fig. 1. Energy Balanced bits equalize rock removal among all cones.
|
|
Balancing the amount-of-rock-drilled/ forces-per-cone improves the cutting structure-to-rock interface dynamic of a roller cone design. In addition, Energy Balanced series bits can incorporate patented, oriented tooth and/or chisel-shaped inserts set perpendicularly to the scraping direction, to remove a greater volume of rock. Oriented teeth provide uniform stress by preventing high loads on the corners of inserts, reducing chipping and broken teeth, and moderating twist force on inserts, decreasing risk of insert loss.
In addition, these bits consistently produce better dull conditions than conventional bits, so more aggressive designs can be developed. This makes it possible in many cases to recommend one IADC code softer when specifying this line of bits. For example, in an application that normally requires a 517 IADC standard bit, a 447 or even a 437 IADC Energy Balanced bit can be recommended, increasing rate of penetration while still achieving the required durability.
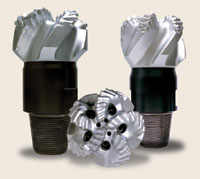 |
Fig. 2. FM 3000 series bits with Z3 cutters were developed to provide much greater cutting efficiency in hard rock drilling applications.
|
|
Fixed cutter bits. Advances in fixed cutter technology have produced a step-change in application-specific PDC bit design. The FM3000 series bit with new Z3 cutters combines force management and drilling dynamics optimization technology with advanced cutter technology, Fig. 2.
Force management employs CAD software to provide a precise, 3D definition of cutter interaction with the rock, allowing cutter positioning that harnesses forces for maximum drilling efficiency. Similarly, drilling dynamics optimization incorporates precise modeling of actual cutting dynamics for better directional response and longer cutter life.
The FM3000 series bit features highly abrasion-resistant Z3 PDC cutters, designed for hard rock drilling applications. Development of Z3 cutter technology required focusing on a new variable besides the balance between impact and abrasion resistance, that is, cutter efficiency. Cutter efficiency is the ability to maintain a sharp cutting edge throughout an interval, so less energy is required to shear the rock. The cutter provides significantly greater cutting efficiency, delivering 13.5 times the abrasion resistance of industry standard cutters with no loss of impact resistance.
In addition to abrasion and impact resistance, the cutter delivers a third performance dimension, Thermal Mechanical Integrity (TMI) qualified cutters. These cutters incorporate interface features that mitigate harmful, residual stress components, with diamond table technology that increases abrasion resistance without compromising impact resistance.
Field results show that incorporating these cutters in the FM3000 series bits provides a substantial advantage in addressing specific drilling needs, such as hard rock drilling. In direct offset comparisons, these bits and cutters delivered as much as a 22% increase in footage drilled and 41% improvement in rate of penetration.
Custom design process. To realize the full potential of technology innovations, Security DBS provides the process of DatCI (Design at the Customer Interface) service that incorporates first-hand customer input into the bit design function. In a method that decentralizes the process, the DatCI service employs a global network of ADE (Application Design and Evaluation) service specialists, who work directly with customer personnel. 
|