Taking the next step in offshore digitalization
With its diversity of energy sources and opportunities for sector coupling, the North Sea will play a crucial role in meeting the world’s growing need for reliable, affordable and sustainable electricity. The region has been integral in supplying energy to Europe through its oil and gas fields for decades. Now, it is poised to accelerate the quest for net zero by becoming a global center for offshore wind and a test bed for new technologies and concepts aimed at decarbonizing offshore hydrocarbon production.
Siemens Energy is supporting these decarbonization efforts by collaborating closely with major North Sea operators in the areas of electrification, automation and digitalization. Over the years, we have been part of several groundbreaking projects, including Aker BP’s Ivar Aasen production platform, which, in 2019, became the first manned facility on the Norwegian Continental Shelf (NCS) to be operated remotely from an onshore control room in Trondheim. We are now applying the experience and lessons learned from Ivar Aasen to the Yggdrasil (formerly NOAKA) field development project.
Collaborative venture. Aker BP, and partners Equinor and PGNiG Upstream Norway, are developing the area comprising three fields. As part of the project, the Fixed Facilities Alliance, which includes Aker BP and Aker Solutions, and Siemens Energy, will provide the complete electrical, instrumentation, control and telecommunication (EICT) systems for the Hugin A, Hugin B and Munin platforms.
All three platforms will feature a high degree of digitalization and automation. Like Ivar Aasen, they will be operated remotely from an onshore operations center. The concepts and technologies employed will enable Aker BP to significantly reduce manning levels in the field and contribute to strategic goals that the company has established for production costs (<7$/boe), CO2 intensity (<4kg CO2/boe), and the highest possible production efficiency.
Laying the foundation for low-manned operations. Offshore producers are under pressure to improve efficiency, reduce break-even prices, and lower the carbon footprint of their operations. De-manning has long been viewed as a means of achieving these goals. However, technology barriers have historically limited offshore de-manning efforts to simple wellhead platforms without processing capabilities.
This has changed in recent years, as increased connectivity and digitalization advancements have opened the door to safe and cost-effective remote control of larger, more complex production installations. Original equipment manufacturers have also made progress in improving the reliability of their products while at the same time minimizing maintenance requirements. Together, these developments have allowed operators to rethink facility operating models and opened the door to manpower reductions that have previously not been possible.
To reduce manning to the greatest possible extent in the offshore production environment, the concept of de-manning must extend beyond facility operation to include shutdown, maintenance, and start-up. While the precise strategy and number of persons on board (POB) will look different for every company and facility, certain core aspects form the basis of any de-manning initiative, Table 1.
The items shown in Table 1 loosely define an infrastructure, from which operators can build a unique de-manning strategy and realize the following benefits:
- Reduced OPEX by decreasing offshore headcount. POB reductions are achieved by removing the need for onsite control room operators through remote process control. Automating certain manual tasks (i.e., equipment inspections) also reduces the number of process operators and maintenance technicians. Additionally, condition-based maintenance (CBM) campaigns minimize full-time onsite maintenance staff. This is further enabled by remote field support and collaboration (i.e., connected worker concepts).
- Improved safety of both the people and the plant. Studies have shown that human factors contribute to most offshore incidents. Reducing the need for human intervention limits worker exposure to high-risk environments while reducing the potential for human error inherent in all manual actions.
- Increased uptime, due to less unplanned downtime from the condition-based, predictive analytics deployed to enable CBM. Opportunities also exist to reduce planned downtime by selecting material and equipment, based on reliability and maintainability for longer mean time between overhauls (MTBO).
- Reduced carbon emissions and environmental impact from fewer shutdowns results in reduced flaring, venting and blowdown. A reduced number of POBs also translates into fewer helicopter trips and lower emissions. The value of this benefit varies significantly, based on the geographical location of the operating asset and the associated carbon tax regime.
Applying low-manned principles on Ivar Aasen. The Ivar Aasen field is 180 km (112 mi) east of Norway’s coast. The ocean’s depth beneath the Ivar Aasen platform is approximately 110 m (355 ft). Field reserves are estimated at over 200 MMboe. First oil was achieved in December 2016.
A low-manning concept was considered from the earliest stages of the Ivar Aasen field development project. Siemens Energy was selected as the sole provider of the EICT packages for the platform. This afforded several advantages, one being that it simplified the process of developing a digital twin of the facility. To enable the low-manning concept on Ivar Aasen, a CBM model has been adopted through remote condition monitoring of platform equipment, Table 2.
Time stamping—a distinctive, event-driven, “on-change” data-sampling method—is employed to help control room technicians better ascertain event sequences in operational data, considerably enhancing diagnostics. The condition monitoring application is connected to the platform’s EICT systems.
After a trial period in 2017 and 2018 of operating the platform using two control rooms—one on the platform and an identical one onshore in Trondheim 1,046km (650 mi) away—Aker BP gained confidence in the land-based control room’s ability to operate the platform competently and safely. In January 2019, the decision was made to begin monitoring the platform solely from the Trondheim onshore control room, Fig. 1.
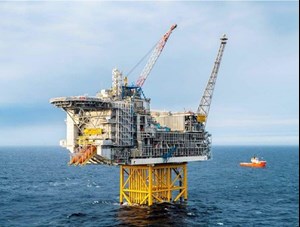
Technicians in the remote-control center use typical office facilities, including desktop PCs that present visual dashboards with detailed information. Depending on their roles and access privileges, stakeholders can view customized data to provide CBM oversight and engineering support. The onboard control room has been left intact and operationally ready, should it be required.
The high connectivity level provides equipment vendors access to their respective operational data to better support their relevant responsibilities for the platform’s maintenance work. Data from the platform are analyzed, using Siemens Energy’s analytic software. KPIs from individual signals and combinations of signals are compared to baseline equipment operating signatures to identify anomalous behavior patterns, such as unusual vibrations or pressure flows.
In addition, CBM helps optimize the platform’s spare parts inventories, freeing up capital that a traditional maintenance approach might otherwise tie up. A high-fidelity “as is” digital twin of the Ivar Aasen platform was developed and is continuously updated. It includes all the platform’s equipment and processes.
Today, Aker BP has a digital program comprising digital twins, aiming to harmonize technology, partnerships, processes, and execution capacity across projects and all producing assets. Strategic partner Cognite constitutes an Industrial DataOps platform powered by a flexible data model, while Aize provides a visualization and collaboration application that delivers the twin to the end-users. Data from the EICT provider is essential to this digital twin ecosystem in Aker BP.
Taking the next step. Building off the experience of Ivar Aasen, Siemens Energy is now continuing to work closely with Aker BP on the Yggdrasil development project. The area includes several fields and is estimated to contain around 700 MMboe. Yggdrasil will include 55 wells tied back to three offshore platforms (Hugin A, Hugin B, and Munin). Siemens Energy has been selected as the sole provider of EICT packages for all three facilities.
The Munin unmanned production platform will be installed at a water depth of 105 m (344 ft) in the northern part of the Yggdrasil area. It will be connected to 23 wells and is designed without a helideck or living quarters. Manned maintenance campaigns will take place annually. The Hugin A production, drilling, and quarters platform will be installed in the southern part of the area and receive the oil production from the Munin and Hugin B platforms. Frøy field will be developed with the Hugin B unmanned wellhead platform, which will be tied back to the Hugin A platform. A total of nine subsea templates will be tied back to Hugin A and Munin.
The digital twin, combined with work processes, is a central part of the operations strategy for Yggdrasil. Since last autumn, the digital team for Yggdrasil has worked to build a digital platform in collaboration with Cognite and Aize. The data platform is built on Cognite’s flexible data model solution and the Microsoft Azure Data Factory. It is the foundation for the Yggdrasil digital twin ecosystem. Data from Siemens Energy are included. Two full-scale simulators also will be installed, one for operator training and the other for engineering and service.
In addition to routine control room tasks, Aker BP will have all the required facilities and systems to support maintenance and modifications. Several integrated operational rooms that cover dedicated functions will be established. An example of such a function is support for rotating equipment, where experts can monitor and investigate any circumstances that may occur and develop reports and work orders for further actions. Control room operators will have continuous programs, where different scenarios can be rehearsed to keep the operators prepared for critical situations.
Digital support systems will be based on Siemens Energy’s Omnivise for Offshore (O4O), which provides dashboards, interfaces, and reports for condition and performance monitoring. O4O is being adapted according to Aker BP’s organizational structure, demands, and unique work processes.
Alliance model. In keeping with the principle of close collaboration, Yggdrasil is being developed under Aker BP’s Alliance Model. Four alliances spanning from drilling activities, subsea, pipelines and platform constructions are involved. Siemens Energy is part of the Fixed Facilities Alliance, which will deliver the engineering services and construction of the Hugin A and Hugin B topsides and jackets.
A core tenet of the Alliance Model is to select strategic partners for the project early and involve them in all phases, including conceptual studies, front-end engineering, construction, commissioning, operations, and maintenance. The intention is to facilitate cooperation between parties and streamline decisions and work processes by creating a single integrated team. It forms the basis for a long-term strategic partnership based on trust, collaboration, empowerment and transparency.
The Fixed Facility Alliance for Yggdrasil includes Aker BP, covering top project management; Aker Solutions, overseeing engineering activities and construction; and Siemens Energy, providing the EICT technology and services. The organizational structure is matrix-based, with a low degree of hierarchy, so there are short paths for decisions. The Norwegian Ministry of Petroleum and Energy (MPE) approved the plans for development and operation of Yggdrasil in June 2023. Onshore construction work for the project began this autumn. Start of production is expected in 2027.
Developing fields of the future. The oil and gas industry faces several challenges in the coming years. In addition to mounting pressure to decarbonize operations, producers must contend with operating long-term in a highly uncertain environment. This is particularly a concern for the offshore industry, where long project cycle times and high development costs leave many companies exposed to market volatility. Given the current outlook, it is no surprise that operators have increased efforts to reduce risk and lower break-even prices through de-manning of fields.
Many forward-thinking operators, like Aker BP, have already adopted low-manning initiatives for greenfields, and others are following suit. While the objective of these initiatives is similar, the process for getting there will look different for every facility. Ultimately, driving a successful implementation requires a combination of technology expertise and an understanding of the business situation. Both criteria should be prioritized early in the project timeline when selecting partners.
REFERENCES
- Settemsdal, S., "Updated case study: The pursuit of an ultra-low-manned platform pays dividends in the North Sea," OTC paper 29606, presented at the Offshore Technology Conference, Houston, Texas, May 2019.
- LaGrange, E., "Building a low-manned production installation: Considerations for rotating equipment, electrical & automation systems and digitalization," SPE paper 205427, presented at the SPE Offshore Europe Conference & Exhibition, virtual, September 2021.
- LaGrange, E., B. Bollinger., and A. Elnaamani, "Digitally transforming offshore production: Making low-manned brownfield installations a reality," OTC paper 30996, presented at the Offshore Technology Conference, virtual, Houston, Texas, August 2021.
- Executive viewpoint: Advancing offshore crane safety through collaboration (March 2025)
- What's new in exploration: Gulf of what? Mar del Norte ~1519? Gulf of North America? (March 2025)
- Decarbonizing Scope 3 emissions: The responsible approach to energy travel (February 2025)
- The future of connectivity and automation in wellsite operations and workflows (January 2025)
- Digital transformation: Next-generation flexible control system modernizes wellsite operations (January 2025)
- Advancing MPD operations with integrated riser joint technology (January 2025)