Chevron’s Chambers sees digital transformation affecting upstream positively for years to come
The digital transformation continues to progress throughout the upstream oil and gas industry, as companies seek to further enhance technology, gain greater operational efficiencies and boost safety and ESG efforts. Accordingly, during the back half of September, SLB held its annual Digital Forum in Luzern, Switzerland. During that week, World Oil Editor-in-Chief Kurt Abraham visited with Chevron’s Vice President for Subsurface, Kevin Chambers, to discuss his company’s digital efforts and how he sees the industry progressing, as a whole.
World Oil (WO): As you know, your company and SLB had a joint entry in this year’s World Oil Awards that became a finalist technology. It is called OneSTEP EF Efficient, Low-Risk Sandstone Stimulation Solution. Can you describe this technology, what makes it unique, and what it will do for the industry?
Kevin Chambers (KC): What's unique about this technology is that it combines what typically are multiple stages of an acid treatment, including the pre-flushes with brine and other chemicals, that you do before the acidizing. And it combines it all into one package. The fundamental benefit of this approach is that it keeps the ions suspended in solution, because a major problem with acidizing is that you can get some precipitation in the reservoir. In particular, in heterogeneous sandstone reservoirs, where you've got different mineralogy. So, you get different interactions, and you get precipitates that prevent you from getting the full benefit of the stimulation job. You don't get as effective a treatment and, therefore, you get lower results after the fact. And so, the benefits beyond just fundamentally trying to prevent the precipitation are that the volumes are much lower, as well.
So, roughly 40% less fluid. Let’s make up a number, for example, a thousand-barrel treatment. Now you only need a 600-bbl treatment. That, of course, has some direct benefits financially. It's less time that you're mixing and pumping the chemicals. It's less flowback that you've got to deal with. So lower disposal, because when you flow back the spent acid, it's a hazardous waste that's got to be dealt with. You have, again, lower pump times, so you've got lower human exposure, there's lower corrosion rates and, importantly for gas wells and low-pressure reservoirs, by putting less fluid into the reservoir, you've got a better flowback typically.
And, fundamentally, it's addressing safety. It's improving the safety by lowering the exposure to humans and the flowback materials. It's lowering cost, again with the lower pumping times. The effectiveness, we think, is going to be better as well, with not having that risk of precipitation in the reservoir. You'll spend less and get better oil and gas production stimulation effect coming back.
WO: So, it’s now going to be literally a triple play of benefits?
KC: Exactly. It's all three together—safety, cost and performance. All three—it's a great combination.
WO: Moving a little closer to the theme of the forum, obviously digital transformation of the industry continues. In your estimation, from an operator’s point of view, how far along is this process really?
KC: I'd say we're making some real, tangible progress, but we've got some ways to go. The thing I'm most excited about is that we're taking on the data challenge, which historically has been a stumbling block. We, in our company, and many in the industry, have tried before to introduce integrated workflows, where incorporating the geology and reservoir engineering and wells disciplines together. But the data has always been problematic, because, the software vendors, including SLB, historically tied the data to the application. So, if you're using SLB software for one part of the workflow and Halliburton for another, they were not inter-operable.
The fundamental breakthrough has been this OSDU, the “open subsurface data universe.” And it's an open source—so it's open to everybody. I think there's currently 230 member companies . The idea is to define the data standards and the APIs, which are the connections between the different types of software. That allows the data to be liberated, so that whatever application you're using, you can call well data or geophysical data, or whatever geologic data that you need. I'm really excited about that. It started out as an aspiration several years ago, and we've made great progress over the last couple of years. In fact, there was an announcement [here at the forum] about this new MEDS (Microsoft Energy Data Services) product that Microsoft developed in collaboration with SLB to deploy OSDU in a commercial form, basically for the industry. That was a huge breakthrough. The other thing that we've made great progress on is partnerships. We're very proud of this Triple Crown partnership with SLB and Microsoft. The three of us announced it at the last digital forum, three years ago in Monaco.
WO: And you've made great progress since then.
KC: What I like about this approach, the strategic partnership, is you take the strengths of the three partners to end up with a better solution than any of the partners independently could have come up with. I like to say, one plus one plus one isn't three, it's five or six. So, yes we've made great progress in our partnership. We've started to deploy the foundational technology, that is what we call PTS, Petro Technical Suite, in the cloud this year. It's the software that does the geologic interpretation, the model building, the reservoir simulation. It's SLB software, supported by Microsoft cloud infrastructure in (Azure), supported by Chevron expertise on use cases and the physics that go into the software. That has come a long, long way. And we're now at the point of being able to benefit from a system that’s much more extensible and open, and to better integrate the wells or drilling part of the workflows, and eventually scale up to our future state of integrated production data.
You've gone in and developed the field, you've drilled the well, and now it's been on production for a year or two years, and you're collecting real-time data: pressure data, temperature data. And we want to cycle that back into the system and say, “what do we need to do next, to actually optimize this well performance?” That part is really, really exciting.
WO: And you also want to ask, “when do we need to do maintenance?”
KC: Exactly. We already have software that predicts whether there is an artificial lift problem. Is your submersible pump not working at its right efficiency? We can diagnose that from surface and downhole measurements. We want to close the loop. You optimize the development up front, and then you have an evergreen real-time value chain way of optimizing the system over time. That is our vision, and we've made great progress in the last three years with the partnership towards achieving that vision.
The other part of it I'd like to speak to specifically is this integration with Wells. Many people call it drilling and completions. We call it Wells at Chevron. Our Wells colleagues had their own independent Chevron platform, and they were using another vendor software to support it. What we’ve done is collaborate with them, and now, they've completely embraced this Triple Crown partnership, Fig. 1.
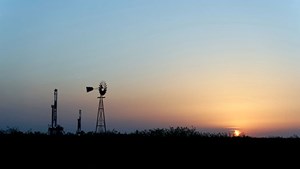
By the end of this year, we will have deployed a new software package called DrillPlan that was developed by SLB, which optimizes the drilling planning process. In the past, we had a proprietary package that was expensive to maintain, with a lot of manual hand-offs of data between teams. In this new system, the data flows seamlessly between the Earth modelers and the drilling engineers, and they can use that real-time data, the latest interpretation of geologic formation in their well designs. It's really exciting.
The next extension after the design of the well is actually drilling it. Here you use DrillOps, which is another new piece of software that SLB has developed. And the expertise that Chevron brings is around alarms. Let me explain, we have a drilling support center Houston, where we monitor our complex wells like in the Gulf of Mexico, and remotely drill others, like in West Texas.
We oversee those wells in a centralized U.S. control center, called the Decision Support Center, where we can visualize and provide expertise in drilling wells. We're going to be able to integrate alarms into this DrillOps application, so that when our engineers are drilling the wells, they will know that there's a potential problem ahead they need to deal with. It's going to close the loop and, again, allow us to go seamlessly from the geologist to the reservoir engineer to the drilling engineer and, eventually, the production engineer for the full life of the field.
WO: That’s impressive. It's almost like you're integrating all the different phases of a well’s life or stringing them together. And the alarms are like the babysitter of the child that will hear exactly when things are safe, right?
KC: Yes, we've got to do these things safely, and drilling is a hazardous process. Having the latest, greatest seamless information is critically important, as opposed to the past. Maybe a drilling engineer had an Excel spreadsheet where they're tracking their work, and they need to transfer that data to somebody else who in turns needs to do something with it. Now, it's all done again in the system. The data, on the OSDU platform, supports the data types and the data is entered and updated once, and then everybody in the system has access to the same data. It's reliable and consistent, and that's a breakthrough.
WO: That's quite a difference, compared to what the industry was used to 30 years ago.
KC: Well, what still has to happen is that OSDU make further progress. We've proven that it's going to have longevity. So, our vision is that it evolves into something like the Apple apps. With the iOS operating system, people can go in and add applications. Everybody has that standard opportunity, and it's just the marketplace for bringing the best-in-class technology. We're still waiting for the industry to fully embrace this open development model and get to that point, where it's the clear place to go. That's the opportunity still in front of us. I think we're on a good path. Again, a lot of partners and competitors are signing up for OSDU.
WO: It seems like the industry is in more of a mood for collaboration these days than it used to be.
KC: Yes, it comes back to my comments that I think we've all recognized that none of us can do it alone, and, in particular, in the context of the Energy Transition. That was a common theme throughout the forum: that no single company, whether it's an operator, supplier or technology company, is going to solve the problems. It's a partnership. And you leverage the strengths of the partners.
WO: Obviously, the digital transformation is helping to streamline various operations and processes, and make the industry more cost-efficient. Are there any specific examples you can provide?
KC: I'll talk about cost efficiency and safety. One of the examples I wanted to share was that we're doing a field trial right now, where we're testing a wearable skin patch, and it's coupled with an iPhone. The skin patch takes biometric measurements on how much you're sweating and measures the electrolytes in your sweat. It is actually for managing heat fatigue. The idea is that workers on an offshore platform may be working in West Africa or Thailand, where it's really hot and humid. And maybe Midland (Texas), too, where heatstroke and heat fatigue are a big issue.
This is a really cool system that will alarm, and it will even provide recommendations to the wearer to take a break, drink fluids orgo rest and cool down. It's a really cool new technology that we're trying out and an example of where we're integrating the safety piece.
Cycling back to the DrillOps example with integrating the alarms, that's something where we've got a lot of experience in geo-steering wells remotely and overseeing wells from our Decision Support Center. And we're able to bring that experience and expertise, couple it with SLB's software, and to then deliver this integrated system into DrillOps.
Another thing on the cost-savings side is that Chevron did benchmarking a few years ago. We looked at our cost of compute, and we didn't think that we were competitive with the marketplace. So, we adopted a platform model. Chevron used to have 42 distinct IT groups that supported upstream, downstream and midstream. We've consolidated those into 13 platforms that are functionally driven. I oversee the subsurface platform. There's a wells platform, there's a surface platform, there's a finance platform ,etc. And what we've done is bring together subject matter experts in that function with IT colleagues, articulate an aspiration and plot a path to deliver digital solutions at much lower cost. We think digital is a key component and helps us better manage costs.
WO: And there are even more examples of digital efforts underway within Chevron, correct?
KC: Yes, there's an MOU that we signed with Delta Airlines and Google around sustainable aviation fuel. One of the things that Chevron is focused on, in our energy transition, is renewable fuels. And Delta has made a commitment that by 2030, they want to use 10% sustainable aviation fuels in their fleet of planes. What we're doing at Chevron is providing a batch of fuel, and then we're partnering with Google. And Google has set up the infrastructure for collecting the data on the emissions, when they actually fly that plane, five years in the future. It will then help set a baseline for the emissions that are coming from these sustainable aviation fuels.
WO: Shifting topics a bit, how prevalent do you think remote controlled offshore operations are becoming, using onshore installations/bases?
KC: I think that's an emerging area, as well. So, we've done some piloting recently on a couple of platforms that were developing in the Gulf of Mexico, where we've used remote cameras and other devices to inspect the facilities, Fig. 2. And the idea is that in the future, we can bring that onshore. You basically use high-resolution images, cameras and digital technology to confidently inspect how the construction is going from onshore. So, have oversight to it and then be able to inspect it at the same time. We think that's a great application.
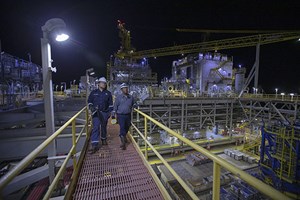
Another example was during one of the recent storms in the Gulf of Mexico, where we were able to centrally pull together all of the data from the PI tags that are tracking pressures and temperatures and sensor measurements. This was all around the Gulf of Mexico, from the subsurface infrastructure to the pipeline infrastructure, and streaming all that data together and basically demonstrating that it was reliable, that the sensors were working.
WO: Is there anything else you would like to add?
KC: Actually, there are two other cool digital applications examples I’d like to share. . One is we've got a 600-megawatt co-generation facility in Bakersfield, California that’s part of the steam generation we need there. We've been operating more than a hundred years in the San Joaquin Valley. We moved all of the monitoring and control of those co-generation facilities to our Houston Pipeline Center where we’re doing all the pipeline monitoring—over 3,000 miles of pipeline—remotely and controlled from our Houston operations center.
The last one I want to share is something my colleagues in facilities engineering are really excited about, which is 3D printing. We have these big offshore LNG facilities, our offshore fields, and onshore plants at Wheatstone and Gorgon, in Australia. We've proven that we can 3D-print parts for those facilities. It's going to allow us to avoid major disruptions.
For example, you might have a critical piece of equipment that goes down and with the current supply chain situation in the world, it might take a long time to get a replacement part. We wanted to preemptively prove that we could 3D-print some of the parts. We've done that. I think that's going to be an emerging technology that will be the wave of the future. You will not have to depend on a supplier or keep inventory on your site. You'll have the ability to print it in real time and secure that part.
WO: One gets the impression that this line of endeavor has been pursued somewhat more quietly in the industry.
KC: I think that's fair to say. It’s like the OSDU story. There are big challenges around standardization, so I think that is part of the issue—getting agreement on standard designs, and agreements on QC around the kinds of parts that are going to be printed. It's not that we can't do it, but to do it at scale and consistently and repeatedly and with confidence—that's the growth area. So, you're right, it's been under the radar a little bit, but I think we'll see it emerging as a major new way that we run the business.
------------------------------------
KEVIN CHAMBERS is vice president of the Subsurface organization in the Chevron Technical Center. In this role, he is responsible for stewarding Chevron’s subsurface technical experts, who provide data-driven and digitally enhanced, customized solutions in exploration and reservoir management. Mr. Chambers has been instrumental in developing INTERSECT—an industry-leading reservoir simulation platform—in partnership with SLB and TotalEnergies. He currently serves as executive sponsor for Triple Crown, the industry’s first three-party partnership between Chevron, SLB and Microsoft, which is creating innovative petrotechnical and digital technologies and pioneering an integrated upstream environment. Mr. Chambers received his BS degree in chemical and petroleum refining engineering from Colorado School of Mines and an MS degree in chemical engineering from the University of California-Berkeley. He joined Chevron as a production engineer and has held numerous engineering, research, asset development, planning, and management positions in his Chevron career.
Related Articles- Sustainability: Meeting new drilling demands with smarter power management (November 2024)
- Cutting-edge choke condition monitoring: What can we do to prevent choke failure? (November 2024)
- Digital control architecture optimizes plunger lift wells (November 2024)
- Cognite: “Un-siloing” data with generative A.I. (November 2024)
- Automated intelligent chemical injection technology minimizes corrosion/scaling, extends ESP run life, increases Permian production (November 2024)
- Industry at a Glance (October 2024)