Behavioral safety digitization supports reduction of offshore incident rates
Considering behavioral-based safety observations, paper and card documentation is still traditionally the preferred practice on many offshore assets, costing operators valuable time and affecting operational efficiencies. HSE advisors are often consumed by lengthy, manual data inputting, rather than adding value on the ground by removing risks and identifying training needs—devaluing skills in admin-based tasks. Within the North Sea, alone, many still use analogue reporting methods. However, there is an accelerated move toward a digital approach.
By law, companies are required to have reporting systems that capture accidents and incidents at work, with many offshore assets adopting behavioral safety observation card systems for employees to identify both safe and unsafe practices at work. These systems worked well when originally introduced, with companies paying for usage and maintenance.
Behavioral based safety—striving to reduce human error. Going back to the 1930s, behavioral-based safety (BBS™) is not a new concept in the industry. Herbert Heinrich, the American industrial safety pioneer, produced research, which concluded that as many as 90% of all workplace incidents were directly attributed to “human error” or the unsafe actions of workers. As behavioral safety programs rolled out across the world, it wasn’t until the 1980s that the British Health and Safety Executive (HSE) commissioned a number of studies, aiming to embed BBS within the oil and gas industry.
Enhancing safety culture on the ground, BBS has since become a key aspect of offshore management systems. However, outdated data collection processes, using paper cards and manual entry systems, have created a laborious and inefficient system, with workers struggling to keep up with input and being unable to identify safety trends. Through spreadsheet programs, information is often processed with varying degrees of impact, and insight is lagging, due to how much time the procedure takes to record the card information.
Digitization—driving safety efficiencies. As industry leaders seek tools and solutions to tackle ongoing challenges, digital innovations are at the helm of this search for improvement. Since early 2021, there has been an accelerated uptake of innovative cloud-based technologies across the energy industry. This has been enabled by the high computing power delivered via cloud platforms.
With the ability to process and house vast amounts of data, cloud systems have become a vital element of the digitization process. Technologies, such as digital solutions expert Fennex’s Behavioral Based Safety Solution (BBSS), have been developed to automate the offshore safety processes, using artificial intelligence (AI) and machine learning (ML).
In a first for the industry, BBSS was deployed across Noble Drilling’s global fleet, Fig. 1. The digital solution transformed the drilling company’s critical HSE reporting system. The fully automated, cloud-based solution used AI and ML technologies to optimize safety observation processes across its 20 drilling units—delivering a 70% saving on program cost and a 30% increase in employee engagement, plus an overall 15,000 man-hours saved per year.
Based on multiple contributing factors from millions of data points, the technology delivered a standardized process to capture, analyze and produce real-time, reliable safety data across the contractor’s assets. Aligning the information against Noble’s key performance indicators, the system empowered employees by providing a live feedback point. Key HSE decisions could be made, based on trends identified and the findings presented through the platform. Over the past 18 months, the drilling company saw a reduction in not only its environmental impact but an increase in the safer execution of tasks. This information was also used by the client to share with its own customers to report its performance in a clear and transparent way.
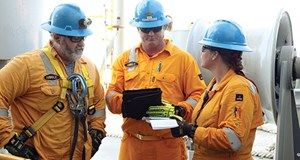
Accessibility engagement and employee buy-in. Implementing new systems, such as BBSS, can bring challenges, with employee buy-in typically acting as one of the most important pieces of the puzzle. Engagement is crucial in the delivery of new processes offshore, with a particular focus on making users feel confident in the output effectiveness.
For Noble Drilling, to ensure that all personnel have the ability to submit safety observations, a three-point data collection system was established. Collecting information using an app, desktop input or through analogue paper cards, the program captured the information to produce a standardized data set. Utilizing QR codes, personnel could participate using one of the three methods, each being unique to the site or offshore installation and optimizing both online and offline data sourcing. By scanning the QR code, users could upload safety observation entries from safe locations in seconds, Fig. 2. This resulted in capturing and reporting at-risk and unsafe behaviors, as well as positive observations, in real time, improving worker engagement.
When access to digital tools was unavailable, or if the user preferred analogue, the system was able to scan paper-based cards. Using unsupervised machine learning algorithms and AI, the solution was able to successfully analyze multiple handwriting styles and extract the text, key and value pairs from documents—providing optimum accuracy of data input, to be combined with the entries from the mobile app and PCs. These efforts saved hours of manual input, contributing to significant time savings.
For example, if a driller named John Smith submitted a safety observation and forgot to input his last name, the algorithms would capture the remaining data and calculate that John, from the specific asset and department, was likely to be John Smith. If the information was deemed to be incorrect, it would be immediately flagged for the team to review.
The cloud-based tool further utilized algorithms in the app-based function to capture voice recordings, if the user wished to dictate his/her safety observations. This enabled those less comfortable with a digital approach to easily use analogue format to access the system. The smart tool was able to recognize multiple dialects and phrases to create a seamless reporting process.
With over 30 different reporting languages, the digital solution was able to capture data from the multi-national workforce, translating written and spoken entries. Introducing this unique feature delivered additional cost and time savings, by eliminating the need for translators whilst continuing to deliver real-time data safety observations. Results showed that the use of this multiple access system promoted engagement among personnel, with a 30% increase, compared to previous methods. This allows data entry to be attractive and accessible to the workforce, removing the perception of laborious tick box exercises.
Knowledge/skill improving safety performance. Hiring personnel with relevant skills and knowledge is essential in the energy sector. However, capabilities can often be lost, if those in skilled offshore disciplines are underutilized and tasked with actions, such as data inputting, which takes time and costs money. By introducing technology solutions to mitigate risk and reduce time spent on tasks that can be automated, companies can benefit economically. Noble Drilling recorded 15,000 man-hours saved per year by implementing BBSS, which allowed workers to add value to the assets by significantly reducing admin time. Personnel, including management and supervisors, were also able to focus on the rig floor—identifying potential risks and fulfilling training needs, which contributed to increased overall safety performance.
Using captured data from millions of records, the system was able to use analytics to ascertain predictive insights, with up-to-date indicators of safety trends. Fundamentally, this improved risk awareness served as a base-level predictive tool. This allowed for informed, data-driven decision-making facilitated by reliable, transparent information, resulting in an annual program cost saving of 70%, the equivalent of $1 million.
Promoting receptive safety culture. Implementing a requirement for daily safety observation cards can result in quantity over quality submissions. Noble Drilling identified that when a voluntary participation system was implemented using BBSS, they found that the quality of results increased significantly, with some employees submitting multiple forms each day. The introduction of the digital solution meant the impact was immediately recognized, with significant reduction in injury rate following implementation.
Data captured from October 2020 to May 2022 showed that the first aid injury rate fell from 1.16 to 0.66, demonstrating a 43% reduction. Similarly, the recordable injury rate fell from 0.4 to 0.26, showing a 35% reduction. Allowing users to see tangible outcomes from their input in daily and weekly meetings, alongside visual dashboard representations in communal areas, further encouraged engagement—promoting a receptive, positive culture for change amongst the workforce, Fig. 4.
Seeing the results that they had attributed to the new system provided personnel confidence in the working process and increased buy-in for regular interaction with the smart tool, without the need for mandated participation. Through deep analysis of vast amounts of data, the smart tool was shown to create a safer workplace by mitigating future risks and hazards, while improving safety culture. Implementing the cloud-based solution resulted in a simplified and streamlined process, quick and accurate access to critical safety data, and a secure, scalable processing of BBS observation and analytics.
Harnessing the power of advanced digital technologies and a fully automated behavior-based safety system, this scalable innovation delivered significant benefits in efficiency and sustainability. Delivering unprecedented processing speed and transparency enabled Noble Drilling to make informed decisions, whilst improving safety performance, increasing workforce engagement and improving its positive safety culture.
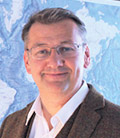
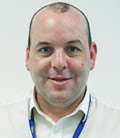
- Executive viewpoint: Advancing offshore crane safety through collaboration (March 2025)
- What's new in exploration: Gulf of what? Mar del Norte ~1519? Gulf of North America? (March 2025)
- Decarbonizing Scope 3 emissions: The responsible approach to energy travel (February 2025)
- The future of connectivity and automation in wellsite operations and workflows (January 2025)
- Digital transformation: Next-generation flexible control system modernizes wellsite operations (January 2025)
- Advancing MPD operations with integrated riser joint technology (January 2025)