OTC 2022 recognizes Spotlight on New Technology® Award winners
In mid-March, the Offshore Technology Conference (OTC) announced the winners of its 2022 Spotlight on New Technology Award. This prestigious award is presented to OTC exhibitors who are revolutionizing the future of offshore energy through technological advancement and innovation. In total, 14 companies, including seven small businesses, were recognized this year for their breakthrough hardware and software technologies.
Recipients of this year’s award were selected, based on the following criteria: novelty in the marketplace; level of innovation; demonstrated success; broad commercial appeal; and ability to make a significant impact across the offshore industry.
“Every year, OTC receives hundreds of award submissions showcasing remarkably impressive and groundbreaking technological advancements in the offshore energy sector,” said Paul Jones, chairperson, OTC Board of Directors. “The companies awarded today represent some of the most innovative and advanced technologies around, which we trust will shape and transform the industry for years to come.”
Since 2014, OTC has recognized the innovation and technologies developed by small businesses. In order to qualify for the small business award, companies must meet the above criteria, be independently owned and operated or registered as a nonprofit organization, and have no more than 300 employees in the 12 months prior to the application deadline.
Founded in 1969, OTC’s flagship conference is held annually in Houston. For more information, visit www.otcnet.org.
2022 SPOTLIGHT WINNERS
There were seven winners among the larger firms category, as outlined below.
FIRST ELECTRIC SUBSEA VALVE ACTUATOR.
Bosch Rexroth has produced the SVA R2 (Fig. 1), with safety by springs and as compact as hydraulic actuators. This disruptive innovation for electrically actuated valves in the subsea process industry combines safety, efficiency and electric operation for depths up to 4,000 m. Although it is a small component, it should have a big impact on sustainability and productivity.
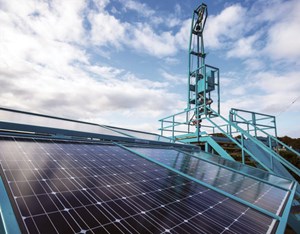
The SVA R2 has seamless integration with subsea equipment. It is the same size as existing hydraulic cylinders and includes standard ROV interfaces for easy handling. Power supply and communication are handled with just a single cable—like a sensor. This device speeds up installation and commissioning in the field with digital twins and standardized interfaces. Operators can easily automate existing equipment with simple retrofit solutions.
FIRST FULLY AUTONOMOUS WELL INTERVENTION SYSTEM
Expro has developed Galea™, a system that replaces larger, conventional, and labor-intensive wireline rig-ups to perform a range of routine slickline operations, Fig. 2. Galea reportedly decreases deferred production, lowers OPEX costs, reduces HSE exposure for personnel, and significantly lessens the carbon footprint of intervention operations.
Galea can be configured in different operating modes to suit a range of applications and environments. In fully autonomous mode, the system is permanently installed onto the wellhead and deploys a tool string into the well, either at regular intervals or defined by well conditions. Between interventions, the tool string is parked within a short lubricator section.
In semi-autonomous mode, a pre-programmed intervention sequence is initiated locally or remotely. This configuration is particularly suited to multi-well platforms or pads where regular interventions are required. Manual mode enables a quick rig-up intervention solution that is operated locally using familiar wireline winch controls.
MPD AND RGH JOINT
The Oil States MPD (managed pressure drilling) and RGH (riser gas handling) Joint (Fig. 3) is a step forward in integrating managed pressure drilling and riser gas handling into a drilling riser. The system's innovative design solutions, such as retrievable packers and pull-in bridle, provide reduced NPT, fast rig-up time, and improved riser gas handling.
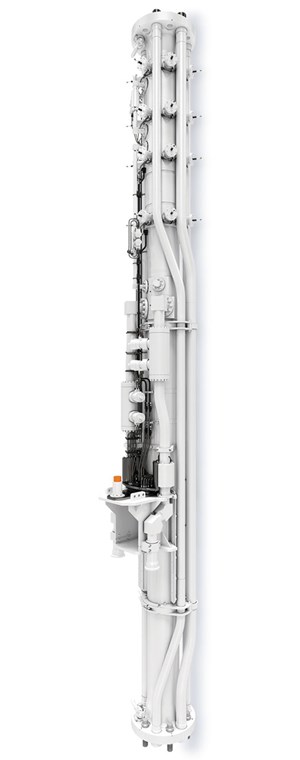
Designed to improve safety and increase operational efficiency, the joint’s hands-free flowline and umbilical stabbing remove the need for man-riding. This joint is around half the length and up to one-third the weight of conventional RIJs, making it easy to handle and fast to rig-up.
Being fitted with twin, retrievable stripper packers and bearing assembly, the joint is completely serviceable while over well center. Stripper packers are run and retrieved by drill pipe tools, removing the need to pull the RIJ from the string or return to the onshore service center to replace annular seals.
A 15K HPHT RISER SYSTEM
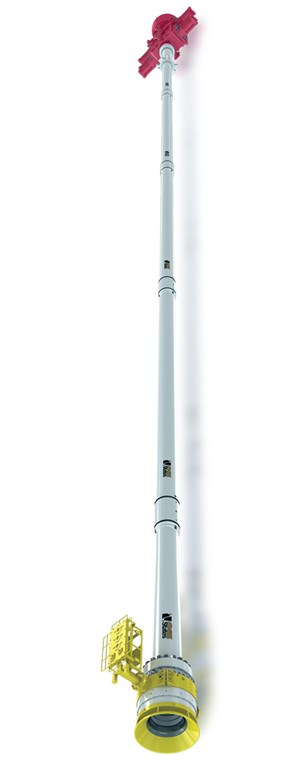
Oil states and TotalEnergies have produced a 15K high-pressure, high-temperature riser system for subsea drilling applications in shallow water, Fig. 4. The Merlin™ system enables cost-effective drilling of shallow-water HPHT wells with a jackup rig while offering superior fatigue performance and improved safety with automated connection make-up. The system is believed to be the first-of-its-kind design-rated for sour service applications.
Drilling wells from a jackup utilizes a dry surface BOP and an HP drilling riser, complete with a hydraulic subsea connector to the subsea wellhead. Quick connections are used to interface with the rig surface 18 ¾-in. BOP stack. A landing joint provides interface between the BOP and the tension joint. The connections on either end of the tension joints can be designed to be project-specific.
VACUUM-ASSISTED PURE OIL RECOVERY
R3 Environmental Systems’ innovative technology is a highly efficient, environmentally friendly method for recovering drilling fluid and water from waste mud/cuttings, Fig. 5. The recovered fluid (marketed as “SecondSource Drilling Fluid) has been independently verified to be equivalent to virgin drilling fluid—the result being one of the most environmentally friendly drilling fluids on the market.
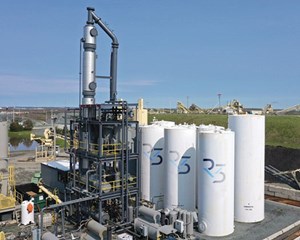
As a result, companies can significantly reduce the amount of virgin drilling fluid that they need to purchase, transport, and eventually dispose of. Recovering and reusing the base drilling fluid instead of using new drilling fluid is an opportunity for the industry to meaningfully reduce greenhouse gas emissions while maintaining quality standards. The technology helps reduce the carbon footprint and other environmental impacts of oil and gas E&P.
EXTREME-PERFORMANCE INSTRUMENTED WIRELINE INTERVENTION
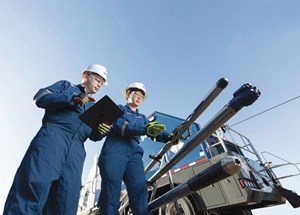
Schlumberger has devised the ReSOLVE iX extreme-performance instrumented wireline intervention service, Fig. 6. It leverages intelligent downhole technologies to optimize results in extreme conditions, such as HPHT, sour, and restricted-access environments. The combination of innovative hardware, automation, and digitization enables operators to monitor and control intervention in real-time and take immediate action to address downhole challenges.
Now available in two sizes, ReSOLVE Family services comprise the 31/8-in ReSOLVE instrumented wireline intervention service and 21/8-in ReSOLVE iX extreme-performance instrumented wireline intervention service and can be adapted to meet an operator’s objectives and maximize intervention impact. ReSOLVE iX service capabilities are uncompromised by its size and enable intervention in extreme conditions, such as complex completions with small restrictions and sour and HPHT environments.
AUTONOMOUS DIRECTIONAL DRILLING
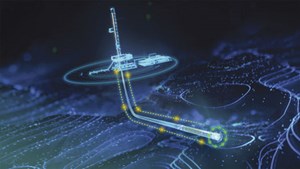
This service by Schlumberger leverages automation and digitalization to advance offshore exploration and production, Fig. 7. This tool drills wells—regardless of the field, rig, or trajectory—in the most efficient and consistent manner possible, says the vendor. And this is done by focusing on Intelligent planning and execution capabilities, along with surface automation that complements a powerful suite of downhole automation features incorporated in the firm’s steering tools.
Autonomous directional drilling stays right on a trajectory plan, because this tool measures the exact strength of the earth’s gravitational and magnetic fields every second, and uses 3D reservoir mapping in real time to help pinpoint its exact subsurface location, and determine the precise steering responses needed. This enables real-time reservoir characterization and getting to the sweet spot in the pay zone.
2022 SPOTLIGHT SMALL BUSINESS WINNERS
There were seven winners in the Small Business category, including one firm with two wins.
SUBSEA FLOW TEMPERATURE MONITOR
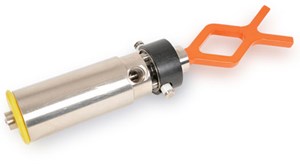
ClampOn devised this monitor as a non-intrusive sensor that determines the temperature of the flow medium from outside the pipe, Fig. 8. The sensor measures the pipe surface temperature underneath insulation and calculates the temperature of the flow medium, using algorithms that compensate for ambient temperature and insulation coefficients.
This monitor can be used as a stand-alone temperature sensor. The instrument can be retrofitted to existing installations, for example, to replace broken intrusive sensors. It also can be integrated into ClampOn’s range of Compact Subsea sensors to provide temperature measurement alongside sand monitoring, pig detection, vibration monitoring or leak detection.
The sensor utilizes the firm’s well-established DSP subsea hardware platform, which has been in operation for more than 20 years. It is built into more than 4,000 subsea sand monitors, pig detectors, leak monitors and vibration monitors.
CODRIL™ CORE BIT
CoreAll’s Intelligent Coring System and Logging While Coring tool provide real-time transmission of gamma-ray, resistivity, downhole vibration and core jam indication. The CoDril™ tool (Fig. 9) is a supplemental downhole convertible core bit, allowing the operator to select between coring and drilling modes. This saves a complete round trip to change the BHA every time.

HYDRAULIC TORQUE WRENCH
The MXT+™ Hydraulic Torque Wrench (Fig. 10) combines the best of HYTORC’s original MXT Wrench with the latest advanced technology. It delivers significant advances in industrial bolting by integrating dual-reaction technology, auto-release, integrated cycle counter and coaxial drive into one flexible tool. The cycle counter monitors tool use and schedules preventative maintenance and calibration. This feature helps maintain the tool at peak performance

The MXT+ tool is offered in a range of sizes for tackling tough bolting jobs, resulting in faster, safer and more reliable bolting. It is constructed from higher-strength materials for rugged industrial use and highly repeatable performance.
SOFTWARE APP FOR BOLTING OPERATIONS
The HYTORC Connect Software App (Fig. 11) is used with the firm’s electric torque tools to automate bolting operations consistent with the industry’s 4.0 digital transformation. The app communicates wirelessly with the tool, initializes bolting parameters, guides the operator, monitors results, collects data, and generates complete quality documentation to assure bolted joint integrity.
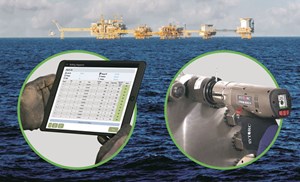
The app simplifies and speeds up the configuration of bolting operations by sending pre-set bolting parameters to the tool. It guides the user during simple or multi-pass sequential bolting operations to ensure job accuracy. Detailed bolting results are captured wirelessly for complete project documentation.
INTELLIGENT LEVEL DETECTION AND DATA ANALYTICS FOR SAND MANAGEMENT
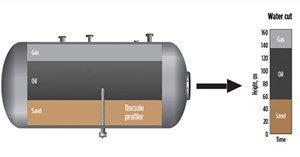
In oil and gas facilities, sand production is an unwanted element. Robust and reliable sensors are critical for automated sand management systems to secure the proper functionality and avoid unexpected shutdowns or reduced production rates. ROCSOLE’s electrical tomography is a real-time non-radioactive monitoring solution (Fig. 12) that physically sees and measures a separator's emulsion layer, improving separation efficiency by optimizing residence time and resulting in higher quality output downstream.
SUBSEA CHEMICAL STORAGE AND INJECTION
Subsea Shuttle’s innovative technology provides subsea chemical storage and injection that satisfy the need for longer and more cost-effective deepwater subsea tie-backs, Fig. 13. The system features a cost-effective modular design and delivers application flexibility regarding injection rates, autonomy, reliability, and compatibility with a wide range of production chemicals.
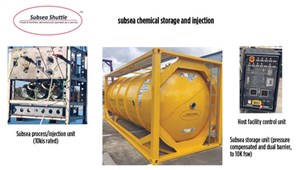
In addition, the technology lowers development costs while reducing host platform space and weight requirements. It eliminates hazardous chemical interaction with offshore personnel while achieving lower chemical costs. The technology also facilitates de-manning of platforms while easing host tie-in burdens.
The benefits of subsea chemical storage and injection include supplementing existing clogged and/or “under-tubed” umbilicals to maintain subsea well production. It also enables production of resources past (further offset) the current limits of “chemical-tubed” umbilicals, developing tie-back opportunities that currently are only possible with new host facilities. In addition, it lowers development costs of tie-back opportunities within current technology reach by removing tubes from umbilicals (and reducing umbilical costs by up to 80%). This technology was previously cited with a World Oil Award last October.
NEW-GENERATION SUBSEA STRAIN MONITORING
KINEKtron® is said to be the world's first fully functional, tested and deployed retrofit subsea strain monitoring system, Fig. 14. The system is capable of measuring strain on structural tubular members. It combines many of Aquatec's existing underwater instrumentation and communications technologies with a new and unique method for measuring strain in a robust ROV-installable package.
Key features also include a unique, multi-point strain transfer mechanism that facilitates high-dynamic range measurement with microstrain resolution. There are also dual through-wter communications and ultra-low-power design technology that provides up to three years’ continuous strain data.
The instrument pod is rated to 150 m and has a protective shroud for secure installation. It handles data acquisition, storage and communications electronics. There is a wetmate connector for surface interaction, plus an ROV handle, pressure sensor, accelerometer, acoustic modem and optical modem.
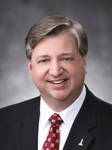
- Regional report: Guyana-Suriname: Rapid expansion of production continues (July 2024)
- Annular safety valves advance flexibility, reliability and safety in completion operations (July 2024)
- Aramco's upstream digital transformation helps illuminate the path toward excellence (June 2024)
- Well decommissioning: Simple solutions to complex problems (June 2024)
- Rethinking sand management for optimized production (June 2024)
- Adopting a holistic approach to cybersecurity (March 2024)