Digital twin technology offers a unified vision for the future of the industry
Next-generation upstream field development and operations will, over the next 10 years, become increasingly dependent on effective, widespread digitalization—not only in design, but also across contracting, construction and production. The accelerating shift toward digital is, in part, a response to an increasingly challenging time for our industry, when market dynamics and the political environment are combining to force unprecedented changes to how we conduct our day-to-day business.
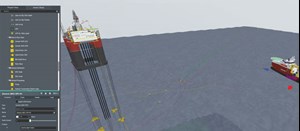
While new exploration is ongoing, many operators have increased emphasis on trying to make the most of fields already in operation; optimization in both cases—creating cleaner and cheaper energy from new and/or existing assets—requires the tools that are the very core of what FutureOn offers. If it is possible to produce better, sooner and with increased efficiency—and to make those decisions earlier—digital twin technology can enable that.
FutureOn emerged from highly respected Norwegian visualization business, Xvision, and has more than 20 years of experience in the subsea sector. And, to further our drive toward the next generation of oil and gas, we have teamed up with U.S.-based Bentley Systems to offer an expanded suite of innovative digital twin solutions specifically targeted at the global exploration and production market.
The strategic partnership—which comes on the back of a significant investment from the Bentley Acceleration Fund at the end of last year, will allow us to accelerate the digitalization of the oil and gas industry. It offers a unique combination of field design applications, a proven API-centric collaboration platform and a fully functional package of digital twin technology.
The solution-focused offering taps into open web standards to facilitate high levels of complex integration and true customization. Taken together, the services open the door to truly transformational change across the economics and efficiencies of offshore development and operations; always a priority in the oil and gas sector but, it must be acknowledged, even more so in the decades to come.
Breaking out of the silo. The embrace of digital, which has been gathering pace in recent years, offers the chance to fundamentally change the state of the industry: development and planning of fields moving from a largely siloed exercise marked by collaboration barriers to an environment in which different companies, separate departments, teams and disciplines are able to work seamlessly toward a shared goal.
What were once isolated islands of information—castaways stranded by licensed or bespoke software, server databases, remote locations and stand-alone documentation—can now be knit together into a coherent whole that paves the way to optimal design, streamlined tendering and contracting, and maximized operations: the alignment of best practice and digital advances.
Cloud technology, software advances, connectivity and physical infrastructure have all helped to facilitate this new way of working. However, while the new tools are immensely powerful in and of themselves, in real-world applications they can only reach their full potential when integrated into a systematic, managed way with buy-in across all levels of business.
Collaboration at the forefront of that initiative. The tools we provide are unique. Our focus on the geospatial environment, the ability to import difficult datasets and the 3D visuals—much of which comes from gaming technology—brings users closer to a real-life, immersive subsea experience from their desktops.
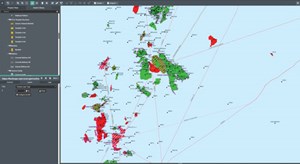
Our field planning package, FieldAP, offers a cloud-based digital platform that provides rapid visual workflows for early-stage subsea engineering work. Multiple data streams from GIS mapping data (Fig. 1) to bathymetry, topography, existing infrastructure and other physical constraints can be combined with proprietary information, such as reservoir information, in addition to well and drilling data, to create an information-rich 3D visualization of any potential project location.
Virtual field development can then proceed according to specific requirements and across a wide range of variables; components including subsea trees, manifolds, pipelines, risers, pumps, and so on, can be deployed or manipulated at the click of a mouse, reflecting the full range of available industry specifications and configurations. The resulting digital model provides instant valuable information at scale, taking full account of both design opportunities and limitations while enabling optimization at the earliest stage.
Crucially, metadata can then be introduced, based on cross-industry standards. The result, built using Bentley’s iTwin and via FutureOn’s FieldTwin API technology, is a virtual twin of the future project that can be utilized in planning. It also allows for the creation of meaningful production forecasts over time. Multiple potential designs can be developed, stored and amended in parallel and at any stage in the process, with an eye to optimizing costs and output. A low bar to participation—thanks to an iterative, easy-to-master interface—ensures that a company’s widest possible range of expertise and insight is brought to the project from day one.
Approximately 15 to 20 models can then—based on feasibility studies, analysis and forecasting results—be narrowed to only a handful of pre-proven options; the digital plan can then be brought into in-house or third-party engineering tools, where the heavy lifting of detailed design can be carried out with feasibility and analysis already completed. Clients already using the FutureOn and Bentley package on real-world fields have not only avoided the significant capex requirements of more traditional digital twin approaches at the operational stage, but they have achieved pre-FEED planning time and investment reductions of at least 60%.
Field development in digital twin era. The proven benefits of the FutureOn digital approach can apply across the full lifecycle of field development and operation. During the concept stage, for example, our shared and collaborative platform uses an open API to be able to integrate data from multiple disparate sources: third-party backend systems, existing domain software, different vendors and disciplines. This “platform as a service” provides a common digital workspace that breaks down barriers between potential silos and enables efficient collaboration across even remote work settings. It also reduces the time spent searching for data across, for instance, server folder structures and data hierarchies. Associated requirements for manual validity checks, which often need to be repeated, are also minimized.
An engineer can rapidly access information in the digital twin about a specific asset in a geospatially correct environment, including the latest validated data: process flow diagrams, piping and instrumentation diagrams, materials and test certificates, product specifications, inspection findings, maintenance records and integrity risk assessment reports. The technical codes and standards used for compliance also can be included.
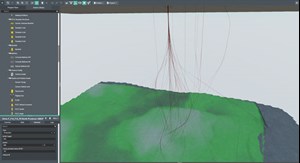
Access to this single-point, data-rich visualization—particularly when combined with parallel organizational changes—boosts efficiencies and increases the time available to discuss a wider range of project alternatives while improving decision-making quality. Metadata functionality brings even wider benefits; physical asset properties can be input, captured and digitized to enable smart virtual assets for use across a range of workflows and software applications in several disciplines.
As an example, pipeline metadata, including diameter, wall thickness, u-value and steel type, can be accessed or transmitted and consumed in pipeline engineering workflows, such as stability analysis, free span analysis, flow assurance, pipeline stress analysis or for cost estimation. Furthermore, well trajectories (Fig. 2) can be generated automatically, using integrations with third-party trajectory generator tools, as well as directly imported from other types of systems.
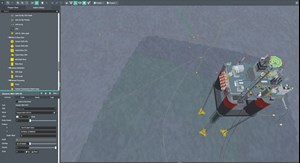
Overall, the integrated semi-autonomous digital approach to field development can highlight problems, such as layout conflicts or budget constraints while facilitating previously unfeasible assessments. The latter include radical field layouts and/or incorporation of rolling geology updates when planning well trajectories, Fig. 3.
Accurate cost estimation is an additional benefit: the length of any connection, flowline, pipeline, riser or umbilical can be established with a high degree of accuracy, based on real-world data, as incorporated into the platform. An extensive bill of materials can be generated at the press of a button and exported to external cost calculation tools; full economic feasibility can be modelled and considered at the earliest stage, based on variables including oil prices, tax pressures and lifting costs. Equally, uncertainties can be assessed to support risk assessment and establish overall risk levels.
Benefits across project lifecycles. Furthermore, FutureOn digital models established during the concept and planning stage can, along with Bentley’s software, be used as a foundation for continued and seamless application of the technology during the subsequent operational phase. This is both a time and money-saving alternative to the usual option of building a new digital field twin from scratch.
Once a project is live, links can be established between the 3D visuals and live data from a range of inputs: IoT edge devices, data historians or infrastructure. Analytics based on the digital representation of the field can be leveraged to provide increased insight and context, allowing real-time results from all elements of a project to inform improved decision-making. Dovetailing with a company’s existing digital infrastructure and reporting practices can increase the value of the digital twin even further.
In reality, what does that look like? Data on asset integrity, inspections and HSE monitoring can be gathered, organized, analyzed and presented in the context of either a single project or a portfolio, offering vital insights to operations management. Areas in need of closer examination are highlighted, while machine learning and artificial intelligence can be brought to bear on asset integrity data streams, enabling predictive inspection and maintenance regimes that avoid costly over-inspection and excessive routines.
Digital field twin technology can, additionally, combine with production calculation engines and simulation software to compare real-life outputs with set targets and estimates, as well as feeding into automated production forecast workflows. The latter frees engineers from what has traditionally been a time-consuming task, leaving more scope to focus instead on troubleshooting and optimization; deviations are highlighted instantly, corrective actions employed, and production output maximized.
Other benefits of the digital twin technology—particularly important as the industry moves into the net zero era—include AI and machine learning analysis of power consumption and carbon emissions, highlighting any problematic assets that might require investigation and/or remedial action. Algorithms can translate insight from the digital twin into recommendations for overall carbon reductions, accounting for multi-dimensional constraint spaces.
At the tendering stage, digital twin technology can streamline the bidding process while increasing security over sensitive and proprietary data. A central cloud-based platform and 3D visualization containing all relevant information allows access to be controlled by the operator over time. This not only governs when and what potential contractors can see, but restricts future use by unsuccessful or non-bidders and guards against misuse, unauthorized access and even theft.
Updates to project materials can be incorporated into bid preparation on a rolling basis, collaboration between partners and consortia can be both facilitated and optimized, and overall time from invitation to tender through to award can be minimized. Fresh thinking from would-be suppliers can even be accommodated and/or evaluated in real time, as product innovations or bespoke solutions become available.
Accelerating the path to first oil. Satisfied customers among some of the industry’s biggest companies are testament to what can be achieved with digitalization. One European multinational seeking to optimize the engineering, feasibility and FEED phases of a project—in large part due to an enduring low commodity price environment – employed FutureOn digital twin technologies to speed time to first oil.
A number of challenges were posed by conventional working practices, such as stand-alone spreadsheets and siloed engineering software. This resulted in multiple revision cycles, misalignment between internal disciplines, and excessive engineering during preparation of field layouts and schematics. In addition, activities including assessment of geohazards and decisions on pipeline routing were viewed as more challenging and time-consuming than necessary. For an organization that prided itself on its ability to bring projects online as quickly and safely as possible, and where strong production performance is an imperative, moving to a next-generation solution was essential, Fig. 4.
The client engaged FutureOn in 2019. The optimization plan is intended to deliver expected improvements
to pre-FEED practices across time, quality, safety and cost. Within a year, a full range of benefits was achieved from the adoption of a collaborative digital tools package, including FieldAP and FieldTwin. Key drivers, in addition to an accelerated path to production, included anticipated reductions to capital and operational expenditure.
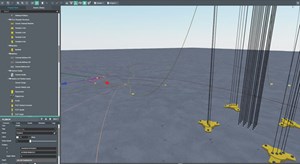
Multiple teams and individuals worked across a shared platform, moving away from the inefficiencies of sequential and cyclical practices toward a continuous model of progress, where different teams were able to cross-validate and collaborate in real time. FieldAP enabled the integration of metadata within all assets in the digital twin, including subsea trees, pipelines and umbilicals, Fig. 5. A wide range of data types and inputs was delivered in a consistent format, with new data added throughout the project lifecycle. Engineers were able to focus on increasing value, thanks to a consistent export architecture that reduced the time necessary to prepare and review deliverables.
Overall, the digital twin approach streamlined the transfer of information between different disciplines and project phases, significantly reducing the potential for errors and delays during transfer of information by more traditional methods, such as email. Traceability also was improved. FieldTwin also removed the need for third-party creation of the CAD drawings typically involved at the pre-FEED stage, reducing the associated workload by 30%, compared to traditional methods. Time spent by subsea engineering on evaluating options for the development phase also was reduced significantly.
Finally, the operator was particularly impressed with the ease of exporting the pre-FEED information required for the preparation of invitation to tender packages for the wider supply chain. Overall time savings of 50% were achieved across the pre-FEED phase, in addition to the creation of overall deliverables. Continued use of FieldTwin is expected to lead to savings of between one and two years from discovery to first oil, with the solution now being rolled out to a range of the multinational’s global projects.
Enabling evolution across oil and gas. Evolution of the oil and gas sector is inevitable as the industry gears up to meet the demands of both economics and the shift toward a net zero world, which is why FutureOn and Bentley have teamed up to provide a suite of tools essential to enabling the next generation of exploration and production.
FieldTwin, FieldAP, and iTwin provide the digital solutions that are key to a new way of working: an open and collaborative approach to field design, based on data-rich 2D and 3D visualizations, the inclusion of metadata on assets and costs to enable reliable early-stage production and financial forecasts, and the facilitation of fully-functional digital twins to streamline the operational phase.
The impact of FieldAP can be transformational. The technology creates a living, breathing blueprint for your field development, where design changes applied to one segment are instantly reflected across the entire project work scope. Updates made in one corner of the globe are communicated in real time to all involved parties, prompting immediate meaningful feedback. Collaboration is turbo-charged, mistakes are minimized, risks are controlled.
And for operational assets, FieldTwin and iTwin combine to provide additional lifecycle benefits. Via the Internet of Things, the platform provides real-time monitoring of every facet of any ongoing oil and gas project: equipment, well production, engineering activity and vessel status/positioning. Timelines are optimized, data are stored and secured at cloud level, and historical inputs and artificial intelligence are integrated for use on future well planning, drilling, installation and operations.
Digital twin technologies provide a route to the next generation of field development; FutureOn and Bentley offer the ability to make better and faster decisions, to optimize the economics of any project and to meet policy demands, such as reduced emissions.
The technology—as represented by FieldTwin, FieldAP and iTwin—enables the improved communications and increased collaboration necessary to achieve the shortest possible path to first oil, the best returns over the life of any asset, and minimized impact on the environment.
- Aramco's upstream digital transformation helps illuminate the path toward excellence (June 2024)
- Adopting a holistic approach to cybersecurity (March 2024)
- Embracing automation: Oil and gas operators leverage new operational efficiencies (May 2024)
- The five A’s on the road to completions automation (May 2024)
- Improving drilling and logging operations with a new measurement platform (December 2021)