Casing exit system delivers economical solution for high-value wells
Drilling and completing wells in challenging downhole conditions can present an operator with numerous unexpected situations, such as collapsed casing, stuck bottomhole assemblies (BHAs) and missed pay zone targets. A common solution to these problems is to perform a casing exit and create a secondary wellbore from the existing motherbore, which allows these issues to be managed or eliminated completely.

This solution is typically applied when the time and cost of alternatives such as a new well are not economical, when there is risk of the existing wellbore not being isolated, or when a relatively small intervention can bring operations back on track. Casing exits have proved their value in a variety of unique applications, such as multistring exits, heavy wall and/or high yield casing, and unconventional casing dimensions. They can help mitigate the amount of nonproductive time (NPT) in response to contingency scenarios. Drilling a new well or section of an existing well, cutting and pulling casing strings for openhole sidetracks, and section milling are all alternative methods that can impose significant time penalties in comparison to a casing exit.
SCENARIO CHALLENGES
To create an exit, or opening in the existing casing, a whipstock assembly and milling BHA are used to direct a mill toward the side of the casing to open an access hole. This process is usually preceded by a wellbore preparation run, using mills and a scraper to the targeted window depth to confirm that the whipstock BHA can be installed without issue. This run will replicate the dimensions and stiffness of the whipstock BHA, and is essential for debris and obstruction removal. After the mills and scraper are tripped back to surface, the whipstock BHA is made up.
The whipstock BHA consists of a whipstock and mills. This BHA is deployed to its target depth and the whipstock is oriented in the azimuthal direction required to achieve the desired sidetrack. A window is milled through the casing, and a specified amount of formation is also cut to enable the subsequent passage of a drilling BHA. Often, this process of cutting the window and drilling formation is completed in a single trip.
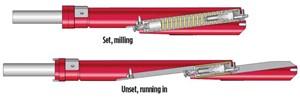
In ultradeep waters, milling an exit into the casing string above an expandable string may be a common practice; however, this approach requires re-drilling and re-casing an entire hole section. Most scenarios require two to three days for the exit and more than a week for re-drilling and re-casing. Under more challenging conditions, operational timeframes may have to be measured in terms of weeks.
Value proposition. A more cost-effective option involves milling a casing exit through an expandable liner when either incorporated in the original well design or used as a contingency string to get casing seats back to the required target depth. These liners typically provide large inside-diameter (ID) sizes that necessitate a bigger window size and consequently will not slim the well design, even after setting additional casing seats.
Creating a large enough window may require a unique whipstock solution, requiring three to four trips to open the ID to accommodate later passage of other BHAs. Creating such a window can be hampered by poor cement quality, or even a complete lack of cement on the backside of the casing. Two causes of inadequate cementing include casing with insufficient centralization, and cement that is contaminated by wellbore-fluid. In other instances, an exit is required at a depth in the well where cement was not previously required on the back side. In these situations, the operator may elect to perforate the casing and pump cement at the window depth prior to the exit, or they may pump cement after the window is cut to isolate the casing anulus if required.
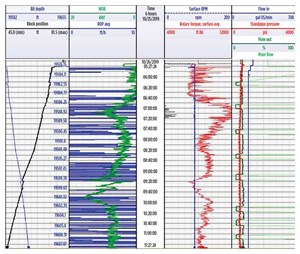
When faced with low-quality cement or a complete lack of cement, the mill can potentially jump off too early and create a shorter window than desired. Additional mill runs can remediate the issue, but only at the expense of extra rig time. Unsupported casing exits also increase the likelihood of under-gauge milling caused by increased vibration associated with the milling process. When milling a window in this scenario, using minimal weight toward the end of window helps to prevent the mill from jumping off the casing lip and leaving an incomplete window. Having a third mill in the BHA can also assist in keeping the milling BHA on the whipstock face to minimize the potential for an early exit.
As with no cement, channeled cement can also be a challenge. This occurs when there is cement in the annulus, but it does not completely surround or bond to the casing. In this case, oil, gas, or water can travel through the channels, up the hole, and outside of the casing, resulting in a compromise of well integrity.
Milling also requires the operator to maintain flow rates sufficient to keep the mill face clean and lift cuttings to the surface, or to magnets mounted along the milling string. When flow rates are restricted, the cuttings may not be lifted as desired, which can result in prematurely wearing of the mill, overheating of the BHA, and increasing the potential for packing off around the BHA. To compensate for low flow rates, the rate of penetration can be decreased to minimize the volume of cuttings being generated and lifted over a given time. High-viscosity/high-yield sweeps also can be pumped more frequently to assist in moving cuttings up the hole.
OFF-THE-SHELF SOLUTION
After an operator elects to utilize a casing exit system, available equipment often requires customization, which adds a layer of difficulty and can lead to costly NPT. Available systems that require minimal to zero modifications are ideal because they eliminate the wait-time associated with fabricating and deploying customized equipment. Especially in deepwater or other high-value settings, such readily available systems are of great interest to operators.
Using a standard whipstock system, along with additional mills in the BHA, can help to achieve a right-sized window. This opening will allow large drilling assemblies to pass through when continuing to drill the well. It will also enable more complex BHAs pass through without difficulty. This capability takes on greater importance when running advanced electronics and measuring technology that sends data to the surface. In addition, it allows larger casing strings to be used, which in turn result in more completion options and more production.
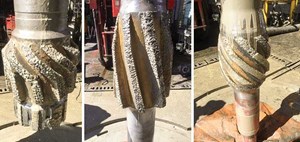
An integrated whipstock system, that includes an anchor, increases flexibility for installing a range of casing sizes. Each anchor, without modification, can catch multiple casing sizes. If applications will not permit a standard anchor to work, the modifications are very minimal and can usually be made within a 24-hour period, which can result in substantial time savings for the operator.
GOM APPLICATION
An international oil company (IOC) was drilling a vertical well in the ultradeep waters of the Gulf of Mexico when a solid-expandable liner collapsed. The operator sought a whipstock solution to open a window as deep as possible. Specifically, the IOC wanted to install an exit in the 13⅜-in. expandable liner to enable a 13½-in. drilling BHA and 12¼-in. casing to pass through without issue. Before this event, a cased-hole sidetrack had never been executed using a whipstock to remediate a problem in 13⅜-in. expandable liner.
The job presented numerous challenges. First, to reduce NPT on the deepwater rig, the IOC requested an off-the-shelf sidetrack solution to achieve its desired timeframe—other service providers would be unable to deliver a comparable solution without keeping the rig waiting on equipment. The operator also wanted to perform a deep exit to avoid re-drilling and re-casing a 3,000 ft hole. Other challenges included exiting the thin-walled expandable liner, channeled cement, and reduced flow rates imposed by the low-pressure limits of the expandable liner. Circulating at flow rates that are too high had the potential to collapse the liner and compromise the channeled cement.
Pre-job planning. The operator called on Weatherford to quickly develop a solution. After meeting with the IOC engineers, Weatherford whipstock experts proposed using an available integrated Shallow-Angle QuickCut and MultiCatch whipstock anchor system, both of which had demonstrated extremely high success rates.
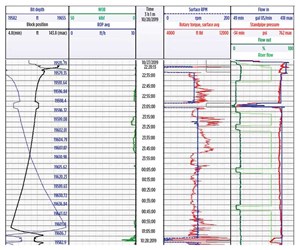
The Shallow-Angle QuickCut system (Fig. 1) employs a unique milling technique, which involves milling along (but not through) a section of the whipstock, to deflect the assembly through the casing wall and create a smooth, seamless transition from the main bore to the lateral section. The shallow-angle whipstock system is typically used to minimize doglegs for extended-reach wells. Its length accommodates advanced technologies such as rotary-steerable systems (RSS), completion strings, expandables, screens and inflatable accessories. In addition, the milling bottomhole assembly and whipstock are designed for safe, quick rig-floor makeup. The aggressive lead mill geometry improves rates of penetration and gauge retention.
The whipstock system consists of a 2.0° single-angle concave assembly, along with a lead mill, secondary mill and steering mill. The lead mill makes the cut while the secondary mill profiles the cut. The steering mill follows behind, to help keep the milling BHA on the concave face of the whipstock, and then polish the cut. The steering mill also enables longer ratholes to be completed, which is increasingly important when exotic jewelry is run downhole on the first pass after the window has been milled.
The MultiCatch whipstock anchor has a field-proven design for use in casing exits, multilateral installations, and wells with wellbore restrictions, Fig. 2. It anchors the whipstock concave assembly and locks it against the casing wall for window-milling operations. Mechanically or hydraulically actuated, the MultiCatch anchor can catch multiple casing sizes and weights, rather than being limited to, or dependent on, a single specific casing ID. This capability eliminates hazards posed by unknown or multiple casing weights in a wellbore, or by casing IDs that have changed as a result of wall loss from wear and tear.
This versatility also reduces risk by providing more leeway when dealing with wellbore obstructions or restrictions. Mechanical or hydraulic actuation modes allow for complete well control while circulating and logging or during measurement-while-drilling orientation. The hydraulic mode does not require a false bottom, thus avoiding the cost of a bridge-plug installation. Its robust, rugged design delivers superior radial anchoring performance for increased torque requirements.
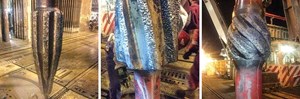
Three-trip strategy. Working in conjunction with the IOC engineers, the Weatherford team developed a plan. They would use a system designed for a standard exit out of casing from 13⅜- to 14-in. This system had an 11½-in. outside diameter (OD), and only needed minimal modification to install a sizable window in the ID of the expandable liner. They planned to execute the operation in three trips and end with the 13½-in. window. Compared to re-drilling and re-casing the well, the three-trip operation would still save significant time.
Although the operation was unprecedented, offset data from similar operations provided sufficient evidence to support the potential success of the operation. Because of Weatherford’s global footprint in well construction technologies, such as expandables, tubular running services, and intervention, the whipstock team was able to draw inferences from prior applications in various uncommon casing sizes for guidance. The case histories involved exits with analogous modifications and additional milling trips to open the window to drift ID. Prior experience combined with knowledge and engineering support from regional and global experts allowed for timely decisions to move the plan forward.
Implementing the plan. The company dispatched whipstock supervisors to the rig, and the first-run modified BHA arrived at the deepwater rig within three days. Additional BHAs and a contingency mill arrived within the following two days: a total of 16 mills, nine of which had custom ODs, had been dressed, inspected, and dispatched. The operator and service company agreed to waive the wellbore preparation run because of the reduced OD of the tools.
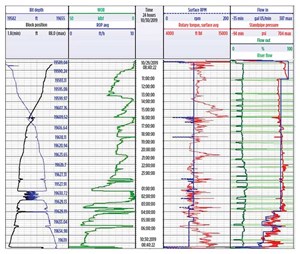
Run 1. On the initial run, the company deployed the BHA with the hydraulic-set, shallow-angle QuickCut whipstock system to mill the window and rathole. The drilling crew tripped in the hole at a rate of four minutes per stand. Initial attempts at measurement-while-drilling readings to check the whipstock orientation were unsuccessful; however, reverse circulating and pressuring up later cleared obstructions to enable a successful reading. The tool face was determined to be oriented at an angle of 266° and the whipstock at a depth of 19,582 ft.
Once anchored, the system was ready for milling. The system, with its shallow-angle ramp, decreased the likelihood of an early exit compared to systems with high angles closer to the kick-off point. While milling the window, a pressure limitation of approximately 700 psi resulted in maintaining the flow rate below 200 gal/min to avoid casing collapse, Fig. 3. Normally, milling BHAs of the size used on this job would require a flow rate closer to 500 gal/min. In just over 6 hours (hr), the system cut a 27½ ft long window, and in just over 10 hr, and reamed a planned 45-ft length of rathole.
As the lead mill moved along the whipstock and cut into the casing, the pilot of the mill reached its coring point. A cored mill will produce a negative impact on milling performance. Coring occurs when the center of the lead mill cuts against the edge of the casing window. If the center of the mill does not move past the casing edge, then the casing can wear a hole in the tip of the mill. When a sudden drop in torque signified that the lead mill had approached its core point, the driller increased weight to quickly move beyond this troublesome point, and resumed milling with no coring impact on mill efficiency, Fig. 4. The entire first run lasted 60 hr and facilitated the running of subsequent BHAs to open the window without having to drill additional rathole.
Run 2. On the next run, the Weatherford crew deployed a second BHA to mill open the window to 13-in. The BHA consisted of three mills similar to those used on the first run: a 12½-in. taper mill, a 12¾-in. secondary mill, and a 13-in. steering mill. Keeping the torque and weight low during this run helped to avoid twisting off and losing the lower hole section, Fig. 5. Milling and reaming on this run took just under five hr, Fig. 6.
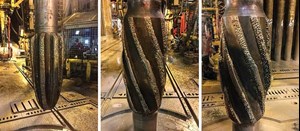
Run 3. The final BHA was run to fully open the window to 13½-in. and elongate the window for future drilling and completion BHAs. It included a 13¼-in. OD tapered mill and two 13½-in. OD watermelon mills spaced out to create a longer window. Reaming lasted two hr until there were no issues sliding through the window without pumps or a rotary, Fig. 7. The run took a total of 29 hr to complete the operation and polish the window. Similar to the previous two runs, all mills and tools came out of the hole in good condition, Fig. 8.
Magnets installed along the work string and at the surface circulation system revealed that a total of 1,842 lb of wet cuttings from the milling operation were recovered during the sidetracking operation. After that, a 13½‐in. motor, 13½‐in. rotary steerable assembly, and 12¼-in. casing were run through the window to finish this contingency hole section. Throughout the operation, the shallow-angle whipstock maintained a low dogleg and smoothly transitioned from the main bore to the sidetrack, all while minimizing risks associated with thin-walled liners and channel-ed cement.
VALUE DELIVERED
The industry’s first-ever cased-hole sidetrack using a whipstock system in a 13⅜-in. expandable liner resulted in success. From picking up the whipstock to laying down the final milling BHA, all operations took approximately five days. By sidetracking from a collapsed expandable liner, the re-entry operation eliminated the time and cost associated with re-drilling and re-casing the interval. In total, the operation saved the operator 14 days, valued at $14 million, compared to the other option of sidetracking the 16-in. casing and re-drilling an entire hole section. This sidetrack operation also proved that a casing-exit solution is a viable approach to limiting NPT in unique situations.
- Driving MPD adoption with performance-enhancing technologies (January 2024)
- Rig electrification drives down emissions, bolsters efficiency while improving onshore drilling economics (October 2023)
- Wellbore seal control and monitoring enhance deepwater MPD operations (October 2023)
- Advancing casing drilling to deepwater: Rethinking top hole well construction (August 2023)
- Mobile electric microgrids address power demands of high-intensity fracing (July 2023)
- Utilizing electronic data captured at the bit improves PDC design and drilling performance (July 2023)