“The auto industry is testing self-driving cars. Big deal. The oil and gas industry is working on remote-controlled drillships.” From the company’s recent announcement, one could conclude that National Oilwell Varco is not impressed by Tesla. The oilfield services company said it plans to begin testing technology that would allow it to place remote-controlled and automated drillships on the world’s oceans in just a few years. “The testing will begin onshore in Norway and then on a ship in the North Sea,” said National Oilwell Varco Chief Technology Officer Hege Kverneland. “A lot of the operations and support activities that you’re doing on a drillship, you can support them from shore,” Kverneland said.
The same can also be said for activities at the other end of the upstream pipe, where advances in production automation, remote monitoring and control, and similar functions have been abetted by the Industrial Internet of Things (IIoT), among other things. Monitoring and control system provider Orbcomm lists seven oil and gas assets that it thinks should be remotely monitored: compressors, tanks, Lease Automatic Custody Transfer (LACT) meters, rectifiers, test points, pigs, and gas meters. The company also offers guidance to remote monitoring system selection:
Equipment interface. Look for solutions that connect to multiple equipment interfaces and can be configured to report at the frequency that meets your company’s requirements.
Human interface. Look for a solution that offers a cloud-based interface so that an authorized user can view the data from a portal or mobile device. Also, a solution that delivers alerts by email, text message or phone helps ensure the appropriate personnel are notified.
Power. Look for monitoring solutions that use a power source that works with the equipment already in use. For example, a unit paired with a rectifier can run off the rectifier’s power source or requirements. A tank level monitor can be solar-powered. Also, having a back-up battery or a solar option is important, where power outages might occur.
Costs. Evaluate both the initial and ongoing costs. The remoteness of a location and number of assets being monitored must be taken into account when choosing a solution. Often, deploying a full-scale SCADA system in a remote area can be cost-prohibitive. Look for a solution that can still meet the local monitoring and control functions that the company requires, without the financial burden.
Communications. Look for a solution that functions with multiple communication modes. A solution that includes cellular and satellite messaging will provide cost-effective options for areas with and without terrestrial coverage. Back-up communication when the primary network fails is key.
Reports and data integration. A solution with customizable reports will convert data into important information. Integrating data into enterprise systems will ensure that everyone from accounting, production and maintenance can understand what is happening at remote sites.
All are good points. Meanwhile, a study by the U.S. Marine Board of the National Research Council (NRC), done for the U.S. Bureau of Safety and Environmental Enforcement (BSEE), made some points of its own about remote real-time monitoring (RRTM):
“Whereas RRTM can provide the rig with technical support and access to onshore expertise, during the committee’s workshop, the U.S. industry expressed a belief that responsibility and authority for operational decision-making should remain offshore. Situational awareness on the offshore facility is important, and RRTM data do not always provide the necessary context.
“The use of RRTM is variable across the offshore oil and gas industry, and diverse RRTM technologies are available. No RRTM industry standard or standard practice exists, and the industry exhibits varying levels of maturity in its use of RRTM. Thus, a standard approach is not likely to work or to be needed for every company or every well.
“The committee views RRTM as best available and safest technology (BAST), when such technologies are consistent with the principles of ALARP (as low as reasonably practicable). The director of BSEE establishes BAST through a documented process, but determining RRTM as BAST in some contexts would not mandate its use across the board. The decision to use RRTM occurs when such technologies are available and “economically feasible.” BSEE could use existing regulatory requirements, such as the Application for Permit to Drill (APD) and the Safety and Environmental Management System (SEMS) plan, to advance appropriate use of RRTM. By encouraging offshore operators to address RRTM in their APD or SEMS plans, BSEE could allow operators to determine the circumstances under which RRTM should be used and challenge them to do so, when BSEE believes that RRTM is necessary for managing risk.
RRTM information—whether in real time or archived—could also benefit BSEE in its inspection activities and support inspectors’ review of safety-related information before they visit offshore facilities. Preparation, prioritized by risk, could allow for more efficient scheduling and effective execution of BSEE inspections.” Pardon the bureaucratese, but—as those of a certain age can remember about E.F. Hutton TV commercials—when BSEE speaks, people listen.
The NRC study’s point about the lack of industry standards in this area is noteworthy. Assuming such standards turn out to be necessary or desirable—you never know—who will create the “API monogram” version of RRTM? Place your bets. WO
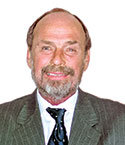
- Advancing offshore decarbonization through electrification of FPSOs (March 2024)
- Executive viewpoint (November 2023)
- What's new in production (October 2023)
- FPSO technology: Accelerating FPSO performance evolution (September 2023)
- A step-change in chemical injection (August 2023)
- Integrating production expertise with digital capabilities drives next-generation autonomous well control solutions (June 2023)