According to the Oil and Gas Technology Centre (OGTC), corrosion, alone, costs the UK economy $34 billion every year. A study carried out by the National Association of Corrosion Engineers (NACE) indicates the annual cost of corrosion globally, across all industries, is $2.5 trillion.
It is one of the biggest threats that companies operating in hazardous industries have to manage, particularly in the oil and gas industry, and poses potentially severe safety, environmental, commercial and reputational consequences.
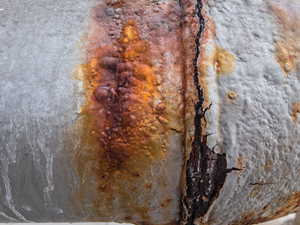
One specific challenge for the oil and gas industry is the presence of external corrosion, which affects structures, piping and equipment, mainly made of carbon steel, Fig. 1. It can also appear in the form of cracking and pitting on corrosion-resistant alloy (CRA) materials, due to the presence of airborne salts or seawater. In general, no component is immune, nor is the issue isolated to one region, with each climate posing distinct challenges in terms of rainfall, wind, temperature and operating conditions. It is, however, prevalent in mature regions like the North Sea, where many assets and infrastructure are operating beyond their expected design life.
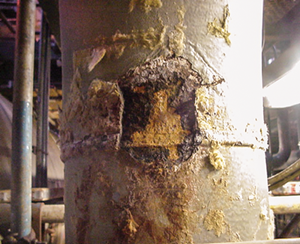
There are many different forms and sources of external corrosion, but they can be broadly split into what can be seen with the naked eye, and what can’t. The latter is more commonly called corrosion under insulation (CUI) and is recognized as the biggest external degradation issue in the oil and gas industry. One study suggests that it’s attributed to 60% of UKCS piping failures. CUI is particularly difficult to detect, because the surrounding insulation or heavy coating conceals the problem, Fig. 2.
In addition, industry initiatives and long-term goals, such as the Maximizing Economic Recovery (MER) strategy, have increased the focus on maximizing production through asset life extension. An unintended consequence of this is an increased risk of visible corrosion and CUI, particularly common for aging assets.
The industry needs advanced solutions that enable more effective mitigation and detection of visible corrosion issues and CUI, to better manage safety, productivity and maintenance costs.
IMPACT OF ENHANCED RECOVERY
Problems caused by external corrosion can develop over years, or even decades. For example, in the North Sea, most platforms were built and coated for a lifespan of 15 to 20 years; however, many are still operating 30 or 40 years later. This environment compounds the contributing factors for structural and equipment degradation.
To tackle this growing issue, the OGTC has launched its vision to eliminate failures caused by CUI in particular, by 2026, dedicating $1.25 million to fund new solutions. If operators can combat this problem, NACE estimates that 25% to 30% of annual costs resulting from corrosion could be saved. With this renewed impetus, backed by industry bodies—including the Energy Institute (Guidance for Corrosion Management in O&G production and processing) and API (RP 583–Corrosion Under Insulation and Fireproofing)—more advanced technologies and analytical approaches are emerging to tackle the issue of external corrosion. Here, we explore a few of the solutions available.
RBI AND DATA ANALYTICS
Risk-based inspection (RBI), combined with intuitive data analytics, provides advanced insights and better efficiency than conventional methods. This is particularly true when detecting and combating CUI, because visual inspection, for example, on damaged cladding, is not particularly reliable on its own.
The use of RBIs and data analytics enables huge amounts of design and operational information to be gathered, tagged and monitored on all sorts of equipment types. These data are then better leveraged to provide an accurate indication as to the risk and remaining tolerance of degradation. The result is more accurate, targeted and proactive inspection routines.
Recent software developments have enabled long-term planning and execution programs for the entire integrity and maintenance scope on an asset. If, and when required, multi-disciplined inspection teams can then carry out condition surveys of the asset, assessing coating and insulation condition, as well as areas prone to corrosion. They are then able to highlight and report findings, and provide solutions to address and manage any serious areas of concern.
The data collected can include the material specification, wall thickness, corrosion allowance, insulation material, coating type/age, cladding condition and probability of water ingress. In conjunction with the physical data collection, information relating to the operating temperature range, external chloride content and infrastructure age can be added to the analysis model—all factors that affect the probability or consequence of failure.
These data are then analyzed by subject matter experts (SMEs), using a range of techniques, including algorithms and data science. This identifies potential problems, reduces waste, and refocuses inspection and maintenance activities by selecting the most effective techniques that concentrate on the areas most prone to threat. This can identify “bad actors,” or items of equipment that are less tolerant to degradation (therefore particularly at risk of premature failure); and where identified, a specific maintenance or replacement plan can be executed to manage them.
ENHANCED INSPECTION TECHNOLOGY
By coupling sophisticated risk-based software with non-destructive testing (NDT) technology, inspections can be enhanced further to detect problematic visible and unseen issues, such as CUI. Advancement of NDT methods has enhanced the efficiency of planned maintenance operations and reduced associated downtime. The application of non-intrusive inspection on equipment, highlighted by RBI and data analytics, has proven to further assure and verify this process.
Oceaneering’s Trip Avoidance X-ray Inspection (TAXI) solution is a recent technology that has fundamentally changed how external corrosion and CUI inspections are carried out while a plant is in-service. In essence, it combines X-rays and digital detection media to deliver extremely short exposure times, providing high-quality digital images of CUI. Importantly, the system has eliminated the risk of radiography affecting production operations, in and around nucleonic level control instrumentation. Using predictive information on how pulses of radiation interact with the nucleonic detectors, Oceaneering can minimize the effects, resulting in reduced plant and equipment downtime, while simultaneously improving process safety and efficiencies.
FIND AND FIX SOLUTIONS
Contrary to CUI, visible external corrosion relies less on NDT, and “find and fix” solutions have become an increasingly common and immediate approach for operators. One such solution is a holding coat—a two-part epoxy paint, designed for use during routine inspection, enables inspection teams to prepare an area of general corrosion and apply a coat on the spot, which arrests the corrosion process. NDT data using digital radiography, MSkip, QSR and guided wave technology options, can be collected from these areas and fed back quickly, affording the operator time to plan and properly repair the affected areas. Some holding coats, such as the solutions Oceaneering provides, are designed to mitigate external corrosion at a certain level for up to five or even ten years, enough to maintain older assets into decommissioning.
These quick fixes give operators room to consider the bigger picture around planning corrosion maintenance and repair. Nonetheless, find and fix solutions are much like a plaster, they offer a temporary solution rather than a holistic approach to detect and mitigate external corrosion much earlier in the process.
MEETING THE INDUSTRY CHALLENGE
The management of external corrosion in oil and gas infrastructure is of paramount importance, for safety and the economic viability of the industry as a whole. Over the last decade, asset life extension has become increasingly important, and with that comes inherent challenges around degradation quantification and mitigation.
It is, however, a challenge that the industry is rising to with advancements in find and fix solutions, the emergence of sophisticated NDT approaches, better use of existing data to predict susceptible locations and failure rates, as well as collaborative industry initiatives to share lessons learned and improve processes.
There is no silver bullet when it comes to preventing corrosion; however, continual research and development of innovative and improved solutions, using highly motivated and competent teams combined with collaboration between equipment manufacturers and industry bodies, places Oceaneering at the forefront of corrosion management and detection, helping customers to enhance reliability and reduce risk.
The good news is that if all these elements are in place, effective management and mitigation of external corrosion can be attainable after all.
- Advancing offshore decarbonization through electrification of FPSOs (March 2024)
- Subsea technology- Corrosion monitoring: From failure to success (February 2024)
- Driving MPD adoption with performance-enhancing technologies (January 2024)
- Digital transformation: A breakthrough year for digitalization in the offshore sector (January 2024)
- Offshore technology: Platform design: Is the next generation of offshore platforms changing offshore energy? (December 2023)
- 2024: A policy crossroads for American offshore energy (December 2023)