Executive viewpoint
The oil and gas industry may have been slow to realize the potential of IoT and digitalization, but with the market downturn slowly fading into the rearview mirror, companies are quickly catching up. Digital adoption is now paving the way for optimization across the supply chain, enabling producers and their suppliers to unlock value in ways that have previously not been possible.
Despite the positive momentum, the industry still has a long way to go on its digital transformation journey. Widespread tech conservatism, an aversion to data-sharing, and concerns related to cybersecurity continue to hamper the process. However, times are changing, as it has become clear that the benefits of embracing disruptive technologies—such as artificial intelligence (AI), digital twins, and additive manufacturing (AM)—greatly outweigh the perceived risks.
Additive manufacturing. As a company on the forefront of facilitating the oil and gas industry’s transformation, we at Siemens have seen first-hand the tangible benefits that can be captured through digital adoption—both in our customers’ operations and our own.
In 2012, for example, we identified the field of AM as a disruptive technology and began rapidly developing a process to apply 3D printing techniques to commercially produce critical gas turbine components. The goal was to increase the availability of spare parts to end-users and enhance key product attributes of turbines, such as emissions and fuel flexibility.
One key aspect that enabled us to undertake this project was digitalization—specifically, the digital twin from Siemens’ PLM software portfolio which, among other things, allowed us to design and simulate a complex part that used to be made up of 13 individual parts and 18 welds. In 2017, we installed the first 3D-printed burners in a commercial gas turbine run by our business partners E.ON in Germany. Last summer, after extended operation and testing, they passed their major inspection with flying colors. The result has been improved gas turbine reliability and performance, as well as a substantial reduction in component lead time.
Condition monitoring. Another salient example that illustrates how digitalization is advancing the industry can be seen in the North Sea. In 2018, Siemens supplied an advanced lithium-ion battery storage solution called BlueVault to the West Mira semisubmersible drilling rig. It is the world’s first modern drilling rig to operate a low-emissions, diesel-electric hybrid power plant.
A key feature that made this application of energy storage possible was the battery solution’s advanced condition-monitoring system, which monitors the voltage and temperature of individual battery cells. Each battery module contains roughly 100 monitoring points, which means that for the MW-hr battery system used on West Mira, there are upwards of 15,000 points where data are being collected. This provides system operators with a high degree of transparency regarding the performance of the battery system. It also enables the use of advanced digital tools, such as machine learning and AI, to analyze data, identify anomalies and predict potential problems before they occur.
It is this same real-time condition monitoring approach that has enabled us to create tailored, prescriptive maintenance plans for our customer’s rotating equipment assets—a program we call FlexLTP (or Flexible Long-Term Program). All of it is made possible by connectivity, IoT, and digitalization.
Taking calculated risks. The positive results from both the AM and energy storage use cases (among many others) confirms what I believe is critical to the future of the oil and gas industry. As companies, we need to think forward and take calculated risks, in order to address the challenges we face—from high capital and operating costs, to rising emissions.
If we better understand the “why”—preparing for tomorrow’s business environment, while simultaneously addressing these challenges, it becomes clear how disruptive digital technologies will continue to make a difference. Embarking on the digital journey, however, takes dedicated leadership, along with a realization that no one acts alone. Stakeholders must come together to address pain points, like cybersecurity, if they are to advance the industry further along the digitalization S-curve.
Developing and adopting disruptive technologies also requires a certain affinity for risk. When we started with the additive manufacturing project, it was not obvious where the effort would lead, but it paid off. Today, we print burners 90% faster than with conventional methods. We also know that AM is more sustainable, as it uses up to two-thirds less material. Combined with an improved design, this doesn’t just lead to better performance, a longer lifespan, and numerous customer benefits—it also addresses, however small, the global challenges we face.
The road ahead. Oil and gas production does not happen in a vacuum, but rather against the backdrop of megatrends enveloping the globe. Chief among these include a burgeoning population in which 1 billion people lack access to power and dire need to reduce carbon emissions.
Digitalization is playing, and will continue to play, a key role in addressing these challenges by fundamentally changing contracting/business models and bringing customers and service providers closer together through strategic partnerships. It is only through a common effort that the industry will be able to achieve full-scale digital transformation and drive toward a more sustainable future.
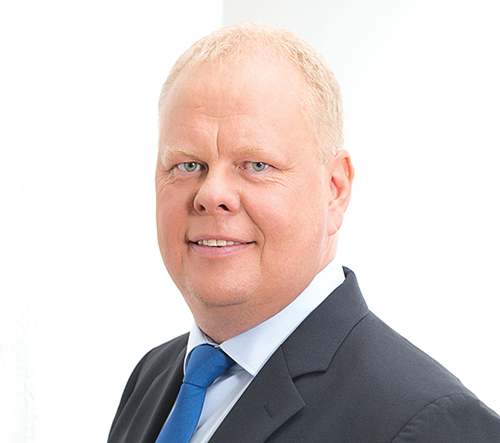
- Aramco's upstream digital transformation helps illuminate the path toward excellence (June 2024)
- Adopting a holistic approach to cybersecurity (March 2024)
- Embracing automation: Oil and gas operators leverage new operational efficiencies (May 2024)
- The five A’s on the road to completions automation (May 2024)
- Digital’s influence on drilling and production keeps growing (March 2024)
- Taming the red zone with automation (April 2024)