Federal field laboratories improving production efficiency, minimizing environmental impacts
In an effort to further characterize shale plays, and the risks and rewards inherent in their development, the U.S. Department of Energy’s (DOE’s) National Energy Technology Laboratory (NETL) has established a group of field laboratories in shale plays across the U.S. Among the first of DOE’s field laboratories is the Marcellus Shale Energy and Environment Laboratory (MSEEL), which began operations in 2014. The specific goal of MSEEL is to provide a long-term field site to develop and validate new knowledge and technology, to improve recovery efficiency and minimize environmental implications of unconventional resource development.
The laboratory, funded by DOE’s Office of Fossil Energy, is in Morgantown, W.Va. (Fig. 1), and run by a consortium of West Virginia University (WVU) and Ohio State University (OSU), with NETL project management and technical oversight. The original research program focused on a dedicated field site and laboratory at the Northeast Natural Energy (NNE) production site in the center of the Marcellus shale’s unconventional production region in north-central West Virginia.

Projects, such as MSEEL, are the cornerstone of the DOE’s Unconventional Oil and Gas Program. These field-scale demonstration projects are paramount in maintaining energy security and the competitiveness of the U.S. independent oil and gas industry. For NNE, the learnings from MSEEL not only increased reserves at the Morgantown Industrial Park (MIP) well site by 20%, but when compared to older wells, they also allowed for their incorporation into normal workflow and operational plans going forward. The results for several different project objectives have now been incorporated into NNE’s best practices.
Research performed at the MSEEL MIP site included:
- Development of integrated data acquisition and modeling approaches for reservoir-scale simulations, based on geophysical data, image logs and lithology.
- Scrutinizing petrophysical, reservoir and production data to establish the effectiveness of geologic versus geometric-based fracture stage design. Evaluating innovative stage spacing and cluster density practices to optimize recovery efficiency.
- Data-driven integration of geophysical, fluid flow, and mechanical properties logs, and microseismic and core data to better characterize subsurface rock properties, faults, and fracture systems, to improve understanding of the extent of the stimulated reservoir volume in unconventional reservoirs.
- Matching reservoir lithology and fracture-fluid types to understand the long-term interaction of fluids and gases with reservoir rock.
- Integrated geochemical and microbiological studies to advance the state of knowledge on in situ reservoir conditions, and the effects of fluid/rock interactions over time.
The initial project plan provided for collection of samples and data, and the testing and demonstration of advanced technologies. The project’s phased approach and access to multiple Marcellus wells has allowed for the flexibility to identify and incorporate new, cost-effective technology and science focused on increasing recovery efficiency, and reducing environmental and societal impacts.
A dedicated scientific observation well was used to collect detailed subsurface data, including log data and 147 sidewall cores. The science well also was instrumented, with a downhole seismic array, and used to monitor stimulation events in two new production wells, Fig. 2. NNE began drilling the two production wells (MIP 3H and 5H) in late June 2015.
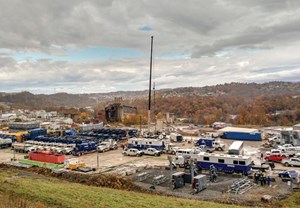
The 3H well was used to obtain 111 ft of 4-in. whole core through the entire Marcellus formation, as well as more than 50 1.5-in. sidewall cores, which are used by researchers to conduct geochemical, microbiological and geomechanical investigations. This same well was logged extensively and instrumented with fiber optic cable for distributed acoustic and temperature measurements throughout the full lateral length.
Several advanced technology logs were acquired and interpreted in the vertical and horizontal sections of the 3H wellbore (Fig. 3), to understand reservoir characterization, which was then used to steer the well in the preferred target and optimize the completion design. The horizontal test well was divided into five sections to investigate different completion design scenarios. A fiber optic cable, permanently installed externally on the casing, and microseismic monitoring were used to evaluate and gain insight to the overall performance of the completion designs.

The MSEEL Team investigated the effectiveness of an enhanced, engineered completion design, compared to the standard geometric method. The engineered design methodology minimized the effect of lateral heterogeneity on fracture initiation by leveraging lateral measurements acquired along the horizontal wellbore. These measurements were used to predict breakdown pressure, which in turn was used to place perforation clusters in rock with similar mechanical properties, thereby improving the probability of stimulating all clusters within a given treatment stage. This methodology enhanced the overall effectiveness of the completion design, it is believed, by increasing the percentage of perforation clusters along the lateral contributing to production.
IMPACT
Demonstration and confirmation of state-of-the-art techniques and technologies have reduced the risk to NNE, and other operators in the Marcellus region, through maximizing efficiency and resource recovery. The project also was able to redefine public perception of the process by allowing an unbiased view of the true environmental impact of the drilling and stimulation processes.
With respect to environmentally prudent development, NNE has learned that silica exposure can be controlled by using a box-type sand delivery system vs. the standard truck-and-trailer system. Researchers also learned that a natural gas hybrid rig does not reduce emissions as much as previously believed, nor does it provide significant cost-savings. Thus, NNE continues using the traditional diesel-engine rig systems for the time being.
MSEEL also provided confirmation of a two-fold benefit utilizing synthetic drilling mud. First, it is much cleaner and more environmentally friendly to dispose of than traditional mud, and second, it provided significant improvements in drilling performance metrics. This type of mud is now used in every well that NNE drills. For lessons learned related to resource recovery efficiency, it was proven through fiber optics and production logging that increased 100-mesh sand concentrations do not degrade the reservoir performance when compared to larger sand proppant. NNE now uses a much higher percentage of 100-mesh sand as part of its standard frac design.
The MSEEL project also provided an opportunity to learn that fewer perforations are needed per stage than had been used previously. By using fewer and smaller holes, NNE was able to increase the flowrate across these holes, which allows for a more powerful and efficient frac, delivering sand more effectively into the formation. Coupled with this, NNE learned that upgrading the casing string and frac stack, to be able to withstand higher pressures, provides more certainty and lowers the risk that every perforation cluster is stimulated effectively. Finally, NNE and WVU have shown that engineered completion stages do provide improved well performance.
SPECIFIC ACCOMPLISHMENTS
Fracturing. WVU has developed a software system, “FIBPRO,” to analyze fiber-optic distributed acoustic sensing (DAS), distributed temperature sensing (DTS), and microseismic data collected during hydraulic fracture stimulation of the MIP 3H well. Analyses using FIBPRO show that the distribution of deformation and cross-flow between stages demonstrates the differences in completion efficiency among stages and clusters. These differences affect production efficiency and have resulted in a better understanding of the geologic/geomechanical controls on completion and, ultimately, on production of the well.
WVU also has developed an integrated geomechanical and discrete natural fracture (DFN) model to investigate the complexity of hydraulic fracture geometry. Reservoir simulation and history matching of the well production data confirmed the subsurface production response to the hydraulic fractures. Well spacing sensitivity research was done to reveal the optimum distance that the wells need to be spaced, to maximize recovery and the number of wells per section.
Numerical modeling was conducted to simulate stimulation stages 1 through 3 of the 3H well, using measured injection data. Comparison of slurry volumes, slurry rates, and proppant mass estimated by the model, and of measured data, show good correlation. This modeling will continue for other stages, to incorporate microseismic and production spinner test data, to better model fracture geometries.
Geochemistry. New microorganisms have been recognized in the deep biosphere represented by the Marcellus shale. Understanding these organisms could reduce downhole well damage and precipitation of radium (Ra) in surface facilities.
To better analyze the biogeochemical characteristics of the Marcellus shale, and to investigate geological controls on microbial distribution, diversity and function, WVU and OSU researchers have developed a method to maximize recovery and reproducibility of lipid biomarkers. Utilizing metagenomics, OSU has been able to show that the Marcellus has a distinct taxonomic signature.
Environmental. Continuous monitoring of flowback and produced waters for nearly a year shows that total dissolved solids (TDS) have leveled off, and there has been little change in ionic composition. Radionuclides in the drill cuttings have been consistently below WV Department of Protection levels for landfill disposal, and well below U.S. Department of Transportation levels for classification as a low-level radioactive waste. Findings from the analysis of MSEEL drill cuttings aided W. Va. legislators in establishing new statewide waste disposal criteria. These criteria are based on EPA’s toxicity characteristic leaching procedure (TCLP). The TLCP has not been exceeded for either organic or inorganic constituents in the MSEEL drill cuttings.
Direct-reading aerosol sampling was conducted throughout all stages of well development, except pad preparation. Sampling locations included the drill pad, itself, as well as locations at 1-km and 2-km distances. Background samples also were taken as references. EPA-regulated PM2.5 (particles less than 2.5 micrometers in diameter, capable of reaching the lung airspaces in a human) emissions were not detectable from background at 1 km, downwind, during highest emissions periods (hydraulic fracturing) on the well pad. Air emissions monitoring during drilling and completion operations indicates that a significant part of air emissions was from truck traffic and other mobile sources, not from emissions due to pad operations.
MOVING FORWARD
Data gleaned from three years’ worth of research from the first two MSEEL wells will guide more extensive testing at a second, new wellsite near Core, W.Va. The new research site is about 8 mi northwest of the initial Morgantown Industrial Park site, in western Monongalia County, W.Va. The second site is geared toward cost-effectively improving gas recovery from horizontal drilling and hydraulic fracturing in the region. Because gas production at the original MSEEL site was seasonally controlled to meet Morgantown’s gas demand, MSEEL Phase 2 provides an opportunity to investigate well response in an unconstrained production environment. Moreover, Phase 2 provides an opportunity to compare up to six wells.
The previous and pending efforts advance hydraulic fracture stimulation techniques that were pioneered by NETL researchers years ago. A key objective of the upcoming field test is to demonstrate more cost-effective techniques for the development of advanced completion strategies that can be applied to other areas of the Marcellus shale play, to improve resource recovery efficiency.
DAS/DTS is too costly to be used on all wells. Therefore, aided by advanced numerical modeling developed by WVU, the project team will calibrate results from a large array of less-expensive, new tools at the Core site to more cost-prohibitive techniques used in the Morgantown Industrial Park wells, to demonstrate new, lower-cost alternative imaging to currently used seismic or more costly fiber optics (FO) approaches. Instrumenting multiple wells at the Phase 2 site (Boggess pad) with FO distributed temperature and acoustic systems (DTS/DAS) would allow for construction of a publicly available, multi-well unconventional fractured reservoir simulation model.
Concurrently, the goal is to utilize both seismic and FO to validate the new, cost-effective technologies (including logging-while-drilling techniques) that could result in their adaptation to the industry’s operational workflow, resulting in the design of better wells at much lower cost. If MSEEL Phase 2 can prove that these technologies work and lead to improved well results, lessons learned from the project can lead to more efficient and effective resource recovery in the region and possibly throughout other U.S. shale plays, thereby improving the nation’s energy security and industrial competitiveness.
The MIP wells operated by NNE were monitored before, during and after stimulation activities, to investigate any potential environmental impacts associated with oil and natural gas operations. Lessons learned, such as the use of green drilling fluids, which were shown to eliminate the need for drill cuttings to be disposed of as a hazardous waste, have become the standard for NNE drilling operations. They will be employed in future MSEEL phases.
In addition, monitoring of produced fluids and natural gas will continue at the Core site (Fig. 4), to confirm earlier findings of no adverse environmental impacts resulting from gas development operations, and the potential for fluid recycling or beneficial reuse.
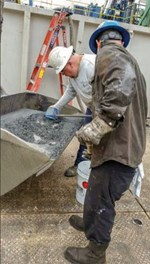
According to Tim Carr, MSEEL Principal Investigator, Marshall Miller Professor of Geology and Department Chair at West Virginia University, top holes have been spudded, and drilling was set to begin at the Core site on the new wells in April. The wells will include one logged and cored vertical well, and up to six horizontal wells, with one fully instrumented, including fiber optic wiring and sensors to provide almost real-time information during fracturing and through production.
One well also will employ some 12,000 lb. of acoustic proppant, whose particles implode, creating a source for micro-seismic information gathering to directly map the extent of the stimulated reservoir volume. Surface 3D seismic also will be integrated into the study. One of the largest challenges in the wake of the MIP work is improving efficiency. Important questions, according to Carr, include: 1) Can we lower costs; 2) Can we increase production; and, 3) Can we reduce the time to project completion?
To get at these questions, NNE will use the latest in downhole logging and monitoring to again set a new standard for the best practices of the industry. The goals of the up-and-coming project will be to truly define what the fracture network looks like. This will be done by using very sensitive fiber optics that can give determination of true frac dimensions and geometries. This will then be used to maximize reservoir contact while at the same time reduce the overall usage of sand and water.
Modeling at multiple scales from nanopore to reservoir-scale by WVU at the original MSEEL site has advanced understanding of the frac response and affected rock volume. The approaches and capabilities to handle and process big data sets (~ 10 terabytes) from a single well helped optimize spacing between laterals, stage length and cluster design. While the technologies used in MSEEL enabled NNE to design better wells, they are cost-prohibitive to use in a development scenario.
However, several technologies have been developed since MSEEL began that, when coupled with advanced modeling, could allow for acquisition of the same type of information much more cost-effectively. That is the critical focus of the MSEEL project’s next phase. If Phase 2 can prove that these technologies work and lead to improved well results, lessons learned from the project can lead to more efficient and effective resource recovery in the region and possibly throughout other U.S. shale plays. WO
DISCLAIMER
"This report was prepared as an account of work sponsored by an agency of the United States Government. Neither the United States Government, nor any agency thereof, nor any of their employees, makes any warranty, express or implied, or assumes any legal liability or responsibility for the accuracy, completeness or usefulness of any information, apparatus, product or process disclosed, or represents that its use would not infringe privately owned rights. Reference herein to any specific commercial product, process or service by trade name, trademark, manufacturer, or otherwise, does not necessarily constitute or imply its endorsement, recommendation or favoring by the United States Government or any agency thereof. The views and opinions of authors expressed herein do not necessarily state or reflect those of the United States Government or any agency thereof."
ACKNOWLEDGMENT
KeyLogic Systems, Inc.’s, contributions to this work were funded by the National Energy Technology Laboratory, under the Mission Execution and Strategic Analysis contract (DE-FE0025912) for support services.
- Electric actuation in the Permian basin (July 2024)
- Drilling advances and where they’re headed (July 2024)
- ESP challenges in an EOR project after breakthrough: An analysis of continuous improvement for ESP designs towards the reduction of OPEX (June 2024)
- Explaining sand erosion in oil and gas production (June 2024)
- Rethinking sand management for optimized production (June 2024)
- Leveraging artificial lift to optimize production (June 2024)