Closing the loop on water treatment
As operations continue to grow in scale and speed, water providers are making strides to optimize and standardize produced water treatment methods. Many methods are commonly used and no longer regarded as emerging technologies. Operators and service providers approach each program with technology selectively adopted to meet water quality objectives for frac chemistry and formation compatibility. Automation technology used during water treatment is emerging as a new opportunity to improve frac water consistency and treatment economics. This integration of treatment and technology with pit management, transfer and disinfection improves efficiency and simplifies job management for operators.
Satisfying water demands of up to 1.0 MMbbl per well can strain water sourcing systems and logistics, Fig. 1. The practice of sourcing produced water to supplement freshwater demands contributes to reductions in operating costs and disposal well load. Several key developments in the last few years have played a role in an industry-wide increase in the percentage usage of produced water to supplement freshwater consumption:
- Infrastructure. The industry transition to a well-factory mode and layout promoted development of infrastructure and management practices to cost-effectively move produced water from well to well.
- Slickwater practices. Complex gel chemistry has high sensitivity to impurities in the frac fluid. Slickwater fluids systems have a less temperamental chemistry. And, in particular, standard practices and formulations are now in place to allow confident usage of high-salinity waters.
- Treatment technology development. Systems and practices for conditioning produced water for reuse have continued to evolve, combined with improved completion chemical technologies to develop better and more tolerant frac chemistries. Field operators and completions engineers have developed more confidence in applying these solutions.
- Completions and disposal density fluid volumes per wells have never been higher. These factors, combined, put unprecedented demands on freshwater suppliers, and can put unprecedented loads on disposal formations, as well. These factors have diminished the availability of reliable, cost-effective sourcing and disposal options, and created a stronger incentive toward reuse.

Economic benefits from each of these factors are resulting in more recycle and reuse treatment activity than ever before. There has always been some incentive for reuse by operators, with strong motivation from corporate social-ethical responsibility and environmental drivers. These economic and reliability benefits have combined to tip the scales toward an industry-wide change to much heavier reuse activity in major plays.
Regardless of whether an operator fracs with fresh water, a blend of fresh with produced water, or even 100% produced water, all frac water requires some kind of conditioning or treatment. Treatment attention is typically applied during three main points in the frac cycle:
- Water plant for recycling produced water for oil recovery and water inventory, away from frac locations.
- Pit management of stored water.
- Disinfection treatment immediately prior to frac use.
FRAC WATER DISINFECTION
Working in reverse from the frac location, we find one of the most important phases of treatment immediately prior to the frac, which is disinfection. Water used during frac operations will be injected downhole, where microbes are at much higher concentrations and already adapted to the high-salinity formation. If deleterious microbes thrive in the reservoir, production can be harmed via plugging from biomass growth, fouling, corrosion (from acid formation), and formation of toxic gases like hydrogen sulfide (H2S). Primary treatment options for managing fresh and blended waters to mitigate risks related to microbial growth include:
- Conventional biocides
- Oxidizing biocides from totes and/or field-generators.
Conventional biocides typically include a liquid biocide like glutaraldehyde or a quaternary amine (e.g. “Glut/Quat”), which is added to kill microbes. The primary advantage is the simplicity, and the ease, of incorporating into the frac chemical blender already on location. Some challenges with this approach are that biocides may be ineffective, costly, and a potential environmental liability.
It can be difficult to monitor and determine the correct dosing of conventional biocides. These chemicals can take up to 12 to 24 hr for complete microbial kill, even when the correct dose is used. However, performance of conventional biocides is limited by conditions downhole, where it is diluted by formation water and degraded by elevated temperatures and pressures. To counter this effect, the standard practice is to overdose, as permitted by an operator’s completions budget.
Oxidizing biocides have the advantage of being relatively environmentally benign, low-cost, and have rapid reaction times. They also have the appeal of allowing for ready field measurement and on-location monitoring and adjustment. Analytical methods can vary, depending on the oxidizer, but in general, residual concentration of the oxidizer (or a certain elevated ORP) can be measured within moments of the addition. The microbes and other contaminants will quickly consume the oxidizer. Therefore, if residual oxidizer is detected, then sufficient dosing to assure good bacterial kill has been met. Further proof of disinfection can be done via ATP measurement, which measures the concentration of this viability indicator in a water sample, as well as other microbe detection tests.
Numerous oxidizers are used for various reasons, each with its advantages and disadvantages. All contribute to microbial control, when applied correctly. Commonly used oxidizers are in the list below.
Chlorine dioxide (ClO2) is a field-generated chemical, made from chlorite and acid, and often with bleach as well, which improves the efficiency of the chemical reaction. It is a common baseline oxidizer, and when applied safely and correctly, it is an effective disinfectant. It does require field generation systems to contain its harsh chemistry, and it is a powerful oxidizing gas. There are many service providers for application. This technology has been adopted by numerous operators.
Peracetic acid (PAA) is an alternative to ClO2 that has comparable efficacy as a biocide, and it is heavily used in the food and agricultural industry for disinfection. PAA does not require field generation in a complex field generator, nor the managing of an array of harsh-chemical feedstocks. Instead, it is delivered and applied from simple totes and chemical feed systems. There are numerous providers of PAA application, and this technology’s adoption by operators appears to growing.
Sodium hypochlorite, or bleach, is a common household disinfectant that is also experiencing a growth cycle. It can be applied from simple totes, and numerous providers are using field-based electrolytic generator systems. The field-generation systems are having growing success and allow simpler chemical logistics, but they do rely on high-amperage field generation systems. There are numerous providers of hypchlorite-based solutions, either from simple totes or from field generators, and this technology appears to continue to grow in adoption.
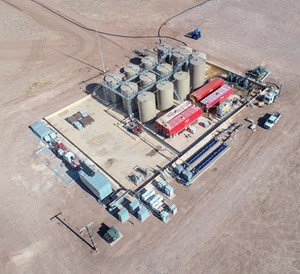
Ozone is a powerful oxidizing gas with a particularly short life as a chemical, but it is powerful at killing microbes. It is a field-generated system, using air as the only feedstock, but it does require considerable power and notable initial capital expense. However, the system operates at relatively low cost, once the capital is invested. There have been few providers of ozone treatment in the industry, and while ozone does have efficacy as a disinfectant, the technology appears to continue to be one of limited market adoption in the industry.
Hydrogen peroxide (H2O2) is used more as a bulk oxidizer, such as at a recycling plant, to aid in water clarification, more than as a direct disinfectant. As a biocide, it is nominally published to be around 1/100th to 1/1,000th the potency of PAA, and so it is rarely used as a direct biocide.
PIT AND STORED WATER MANAGEMENT
Any water that has been treated, and will not be immediately used, will require proper storage to maintain water quality. Typically, the treated water is stored in a pit or an above-ground storage tank (AST). Storage length can be days, up to months. Water stored for a short number of days requires very little maintenance. During longer storage periods, pit management becomes important, with aeration being the most common method of treatment, Fig. 2. Preservation biocides also may be used, but in general are not as common as utilizing a set of aeration diffuser bubblers or other similar types of technology.
Dissolving oxygen into the base of the pit, where most of the undesirable bacterial activity occurs, will carry water from the bottom of the pit and roll over its contents at a relatively minimum power cost to do so. This water movement draws up and exposes the lowest dissolved oxygen content water to mitigate SRBs, and also promotes consistent water quality composition across the entire pit.
PRODUCED WATER TREATMENT PLANTS
Multiple treatment technologies are often employed in a manner designed to meet operator specifications. Figure 3 shows typical recycle and reuse options.
H2S strip and burn. This step is less common, but effective on sour wells where H2S concentrations are excessive. The method consists of an H2S stripping gas stream, sent to a flare for the purpose of air-stripping H2S from the water, and elimination via flare.
Water clarification and pre-treatment. In general, most recycling plants operate utilizing the following basic steps:
- Initial coarse separation of oils and easily removed solids—typically at the operator’s tank battery (Fig. 4), such as the upright tanks at an SWD. For this reason, plants are often strategically located at or near an SWD.
- A chemical additive reaction step. Historically, pH adjustment with caustic soda was the more common approach, initiating reactions to precipitate certain impurities out of solution for easy settling. More recently, oxidation is more commonly used by many providers, where the water is treated with a low-cost bulk oxidizer such as H2O2, bleach or ozone. This oxidizes undesirable iron ions and other compounds into an insoluble form for removal.
- The chemically dosed water then goes through a clarification step that will either be a settling- based step, where the setting of insoluble compounds is induced via chemical additives in conjunction with internal weirs and plates, or it is removal by flotation by micro-bubbles and chemical additives, wherein the compounds stick to the surface of the induced bubbles and rise to the surface, to be collected in weirs for removal. Floatation has seen increased use by the industry, by producing a lower volume of solid wastes, combined with a simpler process to remove and collect floating versus sunken solids.
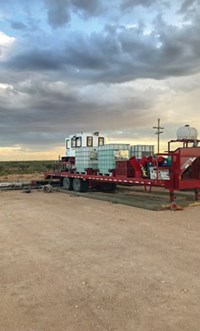
The data required to determine potential treatment options do not always direct operators to one discrete treatment over the other. The outcome of a bench test performed in October 2018 in the Permian (Table 1) indicated a combination of treatments was likely the best solution. In this case, the operator was transferring produced water into a storage pit. The test water scenarios included raw produced water; water after a few hours of exposure to bubbled air to simulate aeration; a sample with H2O2 as a bulk oxidizer for pit-water quality improvement; and a sample treated with peracetic acid. Results indicated in this particular water, that aeration, alone, was not enough to elevate the ORP to positive, but the addition of either chemical did elevate the ORP. None of the treatments materially improved the turbidity of the water. Improving turbidity in this case would either require more settling time, clarification chemicals, or other separation equipment. Ultimately, the prescribed treatment was a combination of pit aeration for maintenance and PAA, which demonstrated effectiveness as a primary disinfectant
In most cases, water after this level of treatment is now “frac ready” quality water. Some operators require an additional polishing step, such as a walnut shell filter, to remove any remaining oils and fine solids. While not necessary for immediate frac reuse, this is often performed for pit management purposes.
LESS COMMON CLARIFICATION, TREATMENT PRACTICES
Biological treatment plant. This option is popular in the Mid-continent region, where water is passed through an SWD tank system, and then through large pits that are heavily aerated to encourage benign microbial growth. These aeration systems are similar to municipal wastewater treatment plants, with retention times of three to four weeks. They have relatively low operating costs and produce good-quality water that is unlikely to sour. However, these systems frequently require seven-to-eight-figure capital investments, and usually are part of much-larger fixed infrastructure systems, and medium-to-long-term field completions and operations programs.
Electrocoagulation. Produced water is pumped across electrically charged iron or aluminum plates that release metal ions into the water to act as coagulants. Often this is accompanied by pH adjustment, and similar processing as described above. This practice has become less common, as slickwater fluids have become more prominent.
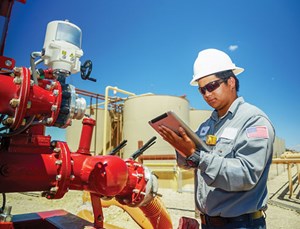
Membrane filtration. Barium and sulfate are both very large ions, so nanofiltration can be used to reduce water hardness. While the operation is straightforward, it creates an additional hard water reject stream of 10% or more of the total flowrate. This process is typically used at locations that have convenient or low-cost disposal wells that can accept the rejected water without harming their injection formation. Membranes can be sensitive to other contaminants in the water, requiring some care and maintenance. There are also some recycling facilities that may use membrane filtration as a final polishing step, such as nanofiltration or even reverse osmosis.
REAL-TIME MONITORING, CONTROL AND AUTOMATION
Automation technology continues to further the efficiency of each of mode of treatment. Oxidative biocides, for example, may require chemical dosing trailers (Fig. 5) just prior to the frac, to inject oxidative biocides. Some systems are automated, to test for biocidal activity on-the-fly and self-adjust the dosing rate to maximize efficacy. Comprehensive solutions like AquaView have been used in multiple basins to give remote and timely visibility of source water supplies, and improve accuracy in determining treatment parameters, Fig. 6.
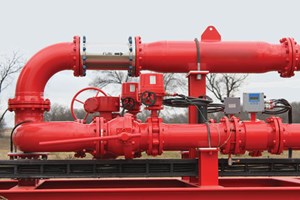
An Automated Proportioning System (APS) can blend fresh and produced water to a specific blend percentage or conductivity, Fig. 7. The ability to verify blended water quality on-the-fly is a function of sensors and actuators built into the proportioning system. Nearby automated pumps and manifolds support this process by automatically responding to pressure changes and stopping or diverting water to storage assets as needed. Depending on the blend ratio, extent of disinfectant demand, and overall initial water quality, this combination of automation and treatment can improve operational efficiency and safety at substantially reduced cost and effort. Other options include various chemical dosing and high-rate settling trains, ranging from simple AST’s for settling oxidizer dosed produced water, to engineered equipment, such as higher-rate bubble floatation rigs, to enhanced filtration equipment.
There are numerous approaches to treating and recycling water in the oil field, with no single approach always being the right answer. Much of the industry has adopted a cost-effective, more readily controllable solution with oxidizing biocides during water transfer operations. The most common in use today is ClO2 , with the increasing use of PAA and bleach expected to continue into 2019. Aeration of produced water and treated produced water, as well as treatment of some fresh water, has also become an industry standard approach to mitigate H2S formation and the souring and fouling of treated and raw waters. Innovation continues to be a game changer for the treatments themselves and automation technology helps to advance more complex treatment processes.
- Regional Report: Which future for Marcellus and Utica shales? (November 2024)
- Sustainability: Meeting new drilling demands with smarter power management (November 2024)
- Sustainability: The relationship between upstream operations and blue hydrogen production (November 2024)
- Shale technology: Using expandable casing patches to reinforce well integrity (November 2024)
- Novel approach of recovering energy from high-pressure multiphase streams (November 2024)
- Drilling advances: Is it always only about people? (November 2024)