NEW BIT DESIGNS
Competition and proprietary software enable advances in this year’s bit designs
As new downhole tool designs enter the market, they are often accompanied by ancillary, application-specific services that improve their effectiveness.
Mark Tran, Engineering Editor.
PDC bit design has evolved dramatically from its primitive origins in the early 1970s. Along with the concurrent development of man-made diamond, which resulted in the mass production of Polycrystalline Diamond Compact (PDC) and Thermally Stable Polycrystalline Diamond (TSP or “diamond grit”), the fixed-cutter PDC bit has become the preferred choice 35 years after its first field deployment. PDC bit evolution can be attributed to vast improvement in cutter composition, geometry and distribution. According to one bit salesman who has been around long enough to know, “The industry saw fixed cutters pass roller cones in total market share last year, and PDCs continue to push ahead in share of worldwide operations and in feet drilled.”
Besides showcasing the new bit designs for this year, this article also focuses on recent developments in bit-design patent battles, proprietary bit-design software and the innovative solutions spawned by those designs, as seen through the release of drilling optimization suites offered by the major bit manufacturers.
MODERN PDC BIT DESIGN
Fundamental PDC bit design involves optimal cutter placement to achieve the desired attack angles into a rock formation, Fig. 1. Cutter exposure, which is the distance between bit blade top and tip of the cutter, must be maximized due to its hydraulic effects. Back-rake angle dictates cutter aggressiveness. In soft rock, small back-rake angles increase depth of cut and maximize ROP. In harder formations, increasing the back-rake angles minimizes wear. Increasing this angle prolongs the life of the cutter, but decreases ROP. To balance the two objectives of bit wear and fast ROP, bit designers must acknowledge the importance of optimal distribution of cutters along the bit blade.
 |
Fig. 1. PDC cutter orientation4 showing that effective backrake angle depends on DOC and cutting face/chamfer geometry.
|
|
Along the blade of each PDC bit, these backrake angles are distributed to balance the net forces acting on the cutters. Designers place less aggressive cutters near the bit’s center while progressively increasing aggressiveness toward the gage region. Ideally, designers prefer smaller side-rake angles near the center of the bit and progressively larger angles near the bit gage. Modern bit design principles seek to optimize these angles and require proprietary wear-modeling software to simulate its effects on different rock formations. Cutter geometry/orientation design involves calculating effective backrake angles which account for different effective included angles at each incremental depth of cut.
In the end, the ultimate goal for a bit designer is to achieve bit stability, which depends on cutting structure placement and orientation, as outlined above, along with other features such as blade profile, geometry, count and spiraling. Besides cutter geometry and orientation, designers must also focus on cutter composition. PDC cutters comprise a working component called a diamond table, composed of diamond grit wafers, and a structural component called a substrate. Just as cutter geometry design requires balancing of cutter effectiveness and wear, the designer must balance cutter durability with its thermal resistance.
Thermal stability of diamond grit is greatly enhanced after catalyst removal, after which the diamond grit becomes TSP. The catalyst-removal process is termed “acid leaching.” However, leaching weakens the cutters’ impact strength. An ideal design calls for optimal catalyst removal only from key regions of a cutter’s diamond table during leaching to enhance its thermal stability while maintaining its impact strength.
PENDING PATENT CASES
Three patent infringement cases pending in US District Court for the Eastern District of Texas in Tyler attest to the current competitiveness of the major bit manufacturers in gaining leverage on modern bit design techniques. In the first suit,1 ReedHycalog UK, Ltd., and Grant Prideco, Inc., alleged that Baker Hughes Oilfield Operations, Inc., Halliburton Energy Services, Inc., and US Synthetic Corp. infringed on four patents relating to PDC cutter leaching. In its answer and counterclaim, defendant Baker Hughes alleged that some of plaintiff ReedHycalog’s drillbits infringed four patents relating to PDC cutter orientation, depth-of-cut feature and distribution along the blade, resulting in a total of eight patents-in-suit in that case. One year later, US Synthetic filed a declaratory judgment case,2 asking the court to declare that it had not infringed the claims of the patents-in-suit arising from the first lawsuit and that the patents-in-suit are invalid and unenforceable.
Earlier this summer, Reed Hycalog UK, Ltd., ReedHycalog, L.P., and Grant Prideco, Inc., filed another patent infringement case3 against three other bit manufacturers, United Diamond Drilling Services Inc., Varel International Ind., L.P., and Ulterra Drilling Technologies, L.P., alleging that Varel and Ulterra infringed four of the patents concerning the leaching of PDC cutters, while alleging that United Diamond infringed twelve patents, four of which were the same patents-in-suit in last year’s lawsuit.1 United Diamond, Varel and Ulterra were customers of US Synthetic, a defendant in the first lawsuit, who supplied the alledgedly infringing leached cutters used in their drillbits.
Recently, the district court in Tyler issued two memorandum opinions construing the claim terms of the patents-in-suit concerning acid leaching and cutter orientation/placement; it concluded that those terms, as construed, were not ambiguous and were amenable to interpretation, thus partially paving the way for a lay jury’s determination of whether those patent claims were infringed. Jury selection in ReedHycalog UK, Ltd. v. Baker Hughes Oilfield Operations, Inc. has been set for June 2, 2008, with a trial date set for June 9, 2008. Trial has not been set for the remaining two cases when this article went into press. Despite the pending patent infringement cases, this year’s offering of new bits and the associated product-support technology have increased compared to last year.
NEW TECHNOLOGY OVERVIEW
The following companies have specific new technology, released in the last year or so.
Security DBS. Direction by Design software is part of the Drilling by Design service platform from Security DBS Drill Bits. It provides advanced bit evaluation and design engineering to optimize directional performance for the specific drilling system used. With directional wells increasingly using PDC bits and rotary steerable systems, bit design is more focused on directional aspects of bit performance, including steerability, bit walk and bit-face control. Accurately evaluating these bit directional behaviors requires in-depth understanding of both the steering mechanism used and the bit/formation interaction.
Where previous design models represented bit motion by axial penetration rate, rotational speed and lateral penetration rate or side cutting, a sophisticated new model developed by Security DBS Drill Bits reveals new insight into steerability design by also incorporating the effects of specific steering mechanisms of various directional drilling systems, such as conventional motors, push-the-bit and point-the-bit systems.
The new interactive model meshes specific bit design features and formation characteristics in three dimensions, and simultaneously uses bit rotation, axial penetration, tilting motion and formation properties to simulate the bit-formation interaction. In terms of design, for a specific bit under given drilling conditions, it determines the effects of bit geometry parameters on steerability and walk rate, and predicts side force and walk force, Fig. 2.
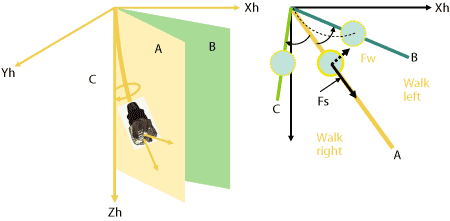 |
Fig. 2. Security DBS’s software calculates the walk rate, walk force and walk direction caused by bit tilting motion.
|
|
In addition, bit torque variance during directional drilling is calculated to account for different bit behaviors during kick-off, build and hold drilling modes. In the field, the software also provides a classification of bit and gage types according to steerability for use in selecting a bit with precisely the desired steerability and walk rate. Used in conjunction with the process of Design at the Customer Interface (Datci), the advanced software provides a powerful means to optimize bit design and system performance.
A new design platform developed for the QuadPack Plus line of premium roller cone bits incorporates the latest advances in fluid flow optimization to overcome turbulent flow problems that inhibit cuttings removal and lift, compromising ROP, bit life and hole quality. The new approach to hydraulics design works to eliminate problems associated with recirculation of flow and cuttings by capitalizing on the way a roller cone bit works.
Working with a university flow lab and using Computational Fluid Dynamics software to determine the optimal fluid flow regime for cuttings removal, Security DBS incorporated these new insights into a patent pending, engineered hydraulics design platform that addresses flow dynamics in terms of fundamental bit design. By optimizing arm geometry to create directed flow channels, fluid flow can be engineered to more effectively remove newly generated cuttings from under the cutting structure and efficiently sweep them up the annulus, contributing to higher ROP and longer bit life, Fig. 3. Introduction of engineered hydraulics design in this line of bits enables Security DBS to optimize hydraulic performance and drilling fluid efficiency to further enhance performance and longevity of its cone line, Fig. 4.
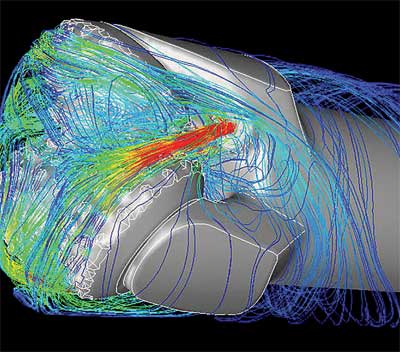 |
Fig. 3. Security DBS’ Fluent image.
|
|
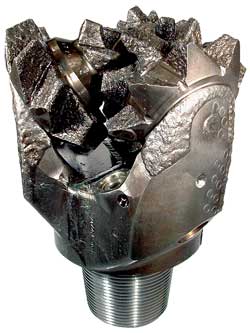 |
Fig. 4. Security DBS QuadPack Plus Engineered Hydraulics tooth bit.
|
|
The XR reamer provides concentric and simultaneous hole enlargement with activation/deactivation systems, where tool reliability, durability and hole quality are important. The XR reamer is the only tool that can be deactivated after enlarging for drilling ahead the original pilot hole size, and allows full-flow circulation while tripping out. The reamer minimizes BHA vibration, macro-doglegs at formation transition interfaces and the tendency to initiate “whirl.” Currently the only tool capable of enlargement to 50% over the pilot hole or drift diameter, the XR reamer is already proven in high-angle extended reach applications where it minimized downhole vibration, resulting in reliable performance even in these extra challenging environments, Fig. 5. Recent technological advancements in the XR reamer include self-body stabilization, auto-blocking cutter arms, and proprietary activation-deactivation systems.
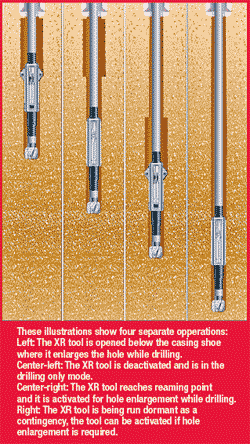 |
Fig. 5. Halliburton XR 1200 Reamer operation modes.
|
|
SPARTA. Using SPARTA well planning software to analyze formation properties and precisely define the application according to customer input, Application Design and Evaluation (ADE) service specialists then match bit designs to applications using powerful 3D IBITS software. This program allows designers to model cutting structures, evaluate the forces acting on them, and evaluate and optimize the bit for specific applications. To determine optimum drilling parameters and bit usage, Security DBS’s drilling optimization software applies a proprietary bit model to the specific downhole environment, as well as maintaining a record of performance for post-run evaluation.
This system helps provide the most efficient drilling mechanics based on sophisticated rock strength analysis, Fig. 6. Parameters such as ROP, WOB, RPM and bit dull condition are displayed in the final output plot. Security DBS is in the process of enhancing the software’s capabilities to capture formation data in real time from LWD tools, and then feed that back into the model to update the formation information and drilling model based on that real time data. Typically, the LWD data is located 50-to-100 ft behind the bit.
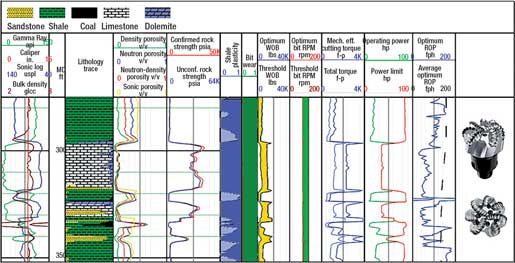 |
Fig. 6. Halliburton’s SPARTA tools provide an accurate predictor of rock strength and geology from well logs. Optimized drilling parameters are also provided on this plot.
|
|
IBitS (Interactive Bit Solutions) is a patented software tool that is used by Security DBS’ engineers who work closely with customers to optimize bit selection, or design a new bit, for specific applications. This software can be used to design a bit in minutes on a laptop in 3D, allowing the engineer to work in the customer’s office or rig site. The software’s tools include Force Balancing, Energy Balanced technology, Transitional Drilling Model and Diamond Distribution among others.
The ADE transmits the design directly to the manufacturing center for quick prototyping and delivery on a priority basis. Guy Lefort, Global Product Champion at Security DBS says, “We have engineers working with operators all over the world, at their oilfields. They send design files electronically back to Houston where the PDC is built and then shipped back. There is joint ownership in the design.”
Smith International. IDEAS, the Integrated Dynamic Engineering Analysis System, is Smith Bit’s proprietary bit design and simulation software suite. The software’s bit designs are developed using a highly sophisticated, proprietary simulation process to accurately model the total drilling system, all the way from where each individual cutter contacts the formation, through each component in the BHA, all the way up to the surface drive mechanism. The certification process verifies the performance capabilities of each bit design through a dynamic simulation and modeling methodology, which takes into account not just the lithology at the rock/cutter interface, but also the drillstring, the drive system, the BHA and the total system’s influence on bit behavior.
Depending on the service provider, the physical characteristics of a rotary steerable system and the basic geometry of the RSS tool can vary greatly depending on the technology used in the system design. Previously, the perception was that each type of rotary steerable system or steerable motor BHA required its own individual bit design and each bit required highly specialized directional features. With the software, that perception has changed.
Because of the truly dynamic nature of the simulation software’s model and the holistic approach of incorporating all system elements into the analysis, PDC bits can be now certified as being dynamically stable across a range of demanding directional applications. Additionally, with the modeling software, all the different types of rotary steerable systems can be accurately modeled individually.
When Rotary Steerable Systems (RSS) were first introduced more than ten years ago, the process for designing and selecting directional PDC bits became increasingly complex. PDC bits that previously performed well with steerable motors often did not work as well with an RSS. Sometimes a bit that performed acceptably with a rotary steerable system in one application did not work well when run with a different rotary steerable system in another application. Improving bit design in directional applications had become more complex, and bit performance was more difficult to predict.
To receive Certified Directional status, bits are tested in the virtual application using the software’s analysis process and are then declared capable of meeting the performance objectives of the particular directional application, Fig. 7. The simulation model allows engineers to design bits that are dynamically stable within their target application. Figure 8 shows the bottomhole pattern of the bit on the left with significant vibration, while the bit optimized by the software on the right has a smooth bottomhole pattern.
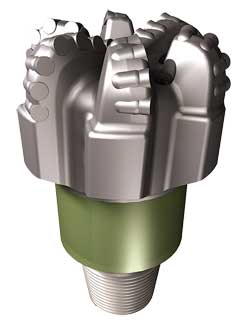 |
Fig. 7. Smith’s MDi616 is IDEAS certified for directional applications.
|
|
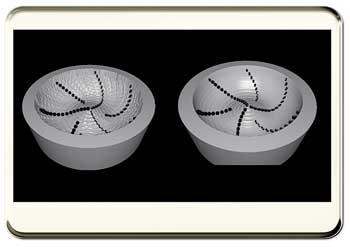 |
Fig. 8. Bottom hole scraping pattern from IDEAS simulation suite.
|
|
Smith’s iDRILL engineers use simulation suites to model the entire drillstring to optimize the performance of the operator’s complete drilling system while minimizing vibration and its adverse effect on the costly components of their BHA. Figure 9 shows the final product of the group’s Finite Element Analysis (FEA) on a particular BHA run indicating troublesome sources of axial, torsional and lateral vibration. In its second year of service, the powerful virtualization tool offers operators the ability to analyze and mitigate vibration and stick-slip.
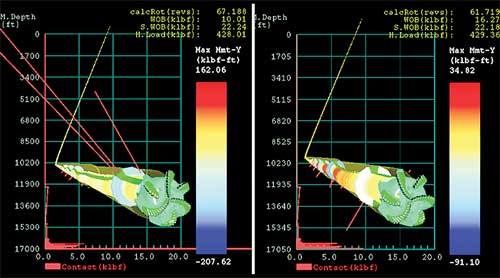 |
Fig. 9. Smith’s iDRILL’s BHA analysis using FEA.
|
|
Additionally, the service includes BHA design for ERD wells and the ability to improve ROP in very hard formations. In summarizing the benefits of the service, Mark Frenzel, iDRILL/DBOS On-Time Manager, stated that, “Once the final recommendations are made, all parties involved are brought together so that the best drilling system and all of its individual components (which are often a mix of different vendors’ equipment that has been carefully matched and balanced) can be reviewed and highlighted to understand the best surface parameters for the run.”
DBOS On-Time. Smith recently announced the release of its real-time drilling optimization service, DBOS On-Time, at the October 18, 2007, Houston Wellsite Information Transfer Standard Markup Language (WITSML) conference. The company chose the WITSML forum for the service’s debut announcement because WITSML, a reliable defined standard for transferring drilling information data in XML format, is the data platform upon which its drilling optimization software operates. WITSML also enables efficient data transfer through the use of the internet. Thus, the source logs can be processed on a remote server which, in turn, can send recommendations back to the rig or the operator’s office via the internet.
Similar to Security DBS’s SPARTA, Smith’s traditional DBOS (Drillbit Optimization System) optimization software performs formation analysis, bit selection, bit design, hydraulic requirements and drillability trend analysis based on offset well data, e.g., gamma ray, sonic, caliper, bulk density, neutron porosity, composite mud logs, etc. However, the new real time optimization service also correlates bit depth with offset well data to give the driller a real-time map of bit position along with real-time look-ahead recommendations on ROP, WOB and ROT, Fig. 10.
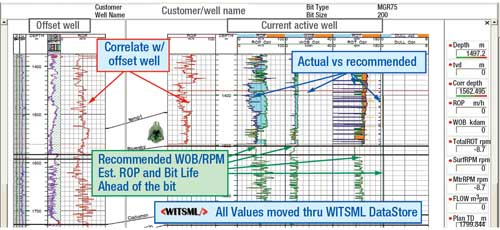 |
Fig. 10. Smith’s new DBOS-OnTime drilling optimization service.
|
|
The real time drilling optimization software also computes a bit dull condition curve as well as an MSE curve. The software’s screen displays a blue curve shading, at each of the recommended parameters columns, when those parameters are not achieved and orange shading when they have been exceeded, thus giving the driller a noticeable visual cue to change parameters.
The software has been field tested through pilot projects that have confirmed its effectiveness. The results of those tests show that poor compliance with recommended parameters resulted in premature dulling of the bit; in contrast, parameter compliance resulted in bit dulling within the software’s optimized prediction. Running alongside this software is another optional module, YieldPoint Real-time Hydraulics, which computes hole-cleaning status, Equivalent Circulating Densities (ECD) at each casing interval and ECD at the openhole section. Smith’s real-time hydraulics optimization software enables the operator to simulate corrective actions by changing factors such as flowrate, mudweight and ROP. Regimes of annular flow for various regions of the borehole are displayed to aid in identifying areas of insufficient cuttings transport.
Hughes Christensen. The company enhanced its design of steel tooth cutting structures for the GX and MXL product lines. FastMax is a proprietary bit with more rows and more teeth compared with the standard Hughes Christensen steel-tooth product line. There are nine rows instead of seven; all of the inner rows have novel pyramid-shaped teeth with proprietary Endura II hardfacing. These powerful pyramids enable a higher-contact load with longer wear life and less balling tendencies for faster drilling, Fig. 11. FastMax bits include STL hardfacing to strengthen the legs and shirttails of steel tooth and TCI bits.
Nova Scotia � Gateway to the North Atlantic. This special supplement highlights this key province in Eastern Canada. The supplement covers unique opportunities for operators and equipment/service providers to communicate planned growth for local projects in Nova Scotia, as well as their international capabilities.
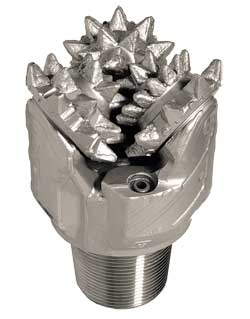 |
Fig. 11. Hughes Christensen FastMax bit with pyramid shaped teeth and Endura II hardfacing.
|
|
In addition to its new Diamond Volume Management (DVM) series of PDC bits (Fig. 12), the company also offers its proprietary “D” Technology bits, which are a proven solution for the ever-increasing complexity of directional applications and operators’ tougher performance objectives. In motor steerable applications, low-interval ROP is a result of motor stalling and toolface control problems. In rotary steerable systems, overly aggressive bits cause higher torsional vibrations, or stick-slip, resulting in reduced drilling efficiencies and overall lower ROPs.
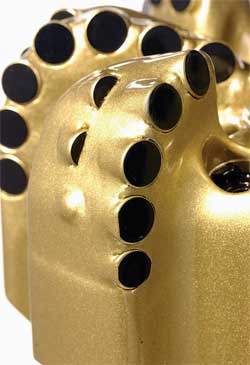 |
Fig. 12. Hughes Christensen DVM series PDC bit.
|
|
Varel International. This company offers its comprehensive program of enhanced diamond protection for roller cone bits. Due to higher drilling rig costs and increased extended reach applications, more diamonds are being used to improve roller cone bit life. Enhanced diamond-protection packages are available on all TCI and steel tooth bits.
Diamond protection is when, during the manufacturing process, polycrystalline diamond capped inserts are inserted in the gage, back row and/or along the leading edge of the shirttails to provide added protection to the bit in abrasive formations. Diamond protection enhances bit life and lowers drilling costs for roller cone products run on motor, directional and rotary steerable applications, particularly those drilling through abrasive formations such as siltstone, sandstone, granite and limestone.
The company’s diamond program options include: enhanced back row protection (increases gage holding in abrasive applications); enhanced gage row protection (maximizes gage holding in abrasive and directional applications); and enhanced shirt-tail protection-provides maximum seal protection and wear resistance in the most extreme drilling environments, Fig. 13.
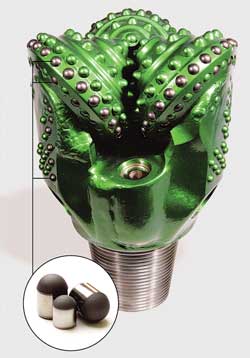 |
Fig. 13. Varel International’s 8.75-in CH67D1DMRS.
|
|
As an added-value to customers, the company can retrofit most of its existing roller cone inventory with backrow and shirttail protection. This ability provides quicker response and faster delivery times to customers needing diamond enhanced options.
The company’s proprietary simulation software, called SPOT, a French acronym that translates into “Simulation for the Optimization of Drillbits,” is used to examine different cutting structures for a given area to design drillbits. Several different designs can be viewed simultaneously, enabling engineers to compare designs. The software was developed by Crystal Profor, a French-based PDC company that Varel purchased in 2000, shortly after the company was sold by Varel president and CEO Jim Nixon. Recent enhancements to the software involved improvements in the code efficiency and data sourcing.
The software uses laboratory and field data, with the lab data containing full-bit and single-cutter test data, Fig. 14. Use of Varel’s software is valuable to customers using RSS systems, since the software can predict a bit’s directional behavior to match the operator’s needs in terms of the bit’s directional signature.
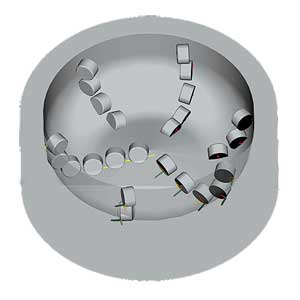 |
Fig. 14. Image of bottom-hole pattern simulation from Varel’s SPOT program.
|
|
Ulterra Drilling Technologies. Ulterra’s MD Directional PDC drillbits are engineered to address the drilling requirements of motor and rotary steerable directional systems, Fig. 15. Ulterra’s engineers have developed specific product attributes that are deployed on MD products to address bit applications regardless of the directional system.
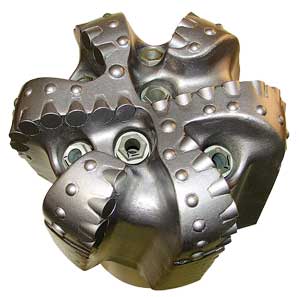 |
Fig. 15. Ulterra Drilling Technologies’ MD1666BE.
|
|
These products have a unique bit profile, cutting structure, and gage configuration to address the challenges associated with directional drilling in demanding applications. The LSE bit profile optimizes lateral stability and drilling efficiency; a dynamic cutter layout provides high ROP, both axially and laterally, while reducing drilling vibrations. Torsional load limiters optimize ROP while controlling torsional vibrations, while the directional gage optimizes lateral efficiency and stability. These attributes are combined, based on the intended application to create a directionally friendly PDC drillbit with predictable reactive torque and reduced stick-slip, without sacrificing drilling efficiency and ROP. The company designs its MD products with the latest in 3D-solid modeling, CAD/CAM capabilities and proprietary design software to ensure accurate art to part processes.
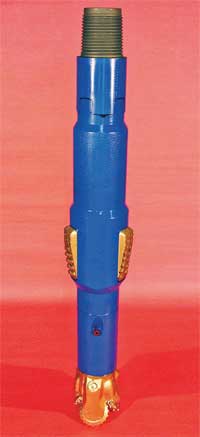 |
Fig. 16. TriMax Industries’ RKS design EWD.
|
|
Tri-Max Industries. The implementation of a concentric hole opener to simultaneously drill and underream has provided many benefits to the operator including better directional control and improved ROP. In the past, the use of EWD tools for underreaming operations in deep oil and gas wells has been challenging. Enlarging while drilling of hard abrasive formations has rarely been considered due to the risk and cost. Tri-Max Industries’ RKS design EWD tool was developed to meet these obstacles, Fig. 18. The EWD is mechanical, or weight activated, concentric hole opener. The advantages of a balanced cutting structure seen in concentric hole openers coupled with a solid steel support for the cutter blocks was made apparent early in the tool’s testing. This design incorporated a longer cutter block with nearly double the amount of PDC inserts. The design also featured a longer stabilization gauge to enhance cutting stability and further eliminate vibration issues. The concentric reamer cuts less formation; the ROP is controlled by the bit which does most of the work and is easier to stabilize. Tri-Max’s Industries’ design is the latest in a long history of EWD tools designed to meet special drilling requirements.
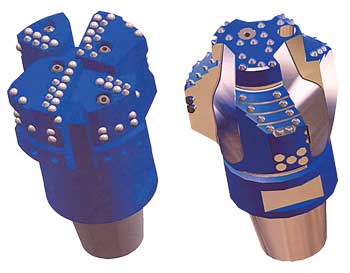 |
Fig. 17. Early prototypes of PID bit Particle Drilling Technologies.
|
|
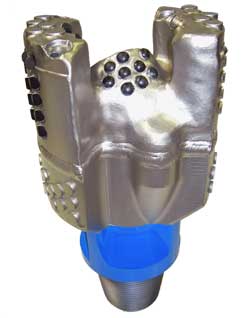 |
Fig. 18. Current commercial field trial version of PID bit.
|
|
Particle Drilling Technologies. This company has made significant progress since last year’s report of their Particle Impact Drilling (PID) bit. As readers might recall, the PID bit fires particles at the formation at a rate of four million impacts per minute, which yields contact stress many times higher than the rock’s unconfined compressive strength. To date, this bit has undergone 12 tests in which downhole conditions are simulated at over 5,000 ft in depth. At the TerraTek Drilling & Completions Laboratory in Salt lake City, Utah, PDTI observed PID bit ROP, through 30 kpsi UNC rock, increase from three to six times from that of a conventional bit. Figures 17 and 18 illustrate design changes through the PID bit’s evolution.
LITERATURE CITED
1 ReedHycalog UK, Ltd. v. Baker Hughes Oilfield Operations, Inc. Civil Action No. 6:06-cv-222-LED, (E.D. Tex. May 12, 2006). 2 US Synthetic v. ReedHycalog UK, Ltd., Civil Action No. 6:07-CV-269-LED (E.D. Tex. June 11, 2007). 3 ReedHycalog UK, Ltd. v. United Diamond Drilling Services, Inc., Civil Action No. 6:07-CV-251-LED (E.D. Tex. June 4, 2007). 4 The district court’s interpretation of an illustration from a patent-in-suit (U.S. Patent No. 6,460,631) in ReedHycalog UK, Ltd. v. Baker Hughes Oilfield Operations, Inc. Civil Action No. 6:06-cv-222-LED, Memorandum Opinion, Dkt. No. 245 at 63 (E.D. Tex. May 12, 2006).
|