Technology from Europe:
Italy
The King Kong Project: A challenging subsea tieback in the Gulf of Mexico F. Paone, W. Dooley and D. Beesley, Agip Petroleum Co.
The King Kong gas field is located in 3,900-ft water in Green Canyon Blocks 472, 473 and 516, in the US Gulf of Mexico, 150 mi south of New Orleans, Louisiana. The development project comprises three subsea wells, each tied back to a central subsea manifold. From the manifold, two flowlines extend 16 miles to Agip Petroleum’s Allegheny mini tension leg platform (TLP), which is primarily an oil treating facility. The project required design of new equipment using the most advanced technologies – both subsea and topsides. Some interesting features of the development related to:
- Weight and space availability: To control payload added to the TLP, particular attention was given to topsides equipment – e.g., use of special lighter and smaller valves, special paint for fireproofing, location of new skids and TLP reballasting to balance the TLP center of gravity – and also to the subsea system, e.g., risers with non-continuous buoyancy and cold processing to reduce size of topside dehydration equipment, reduced riser size and lighter umbilical materials.
- Methanol: Due to the small space available, use of a glycol recovery system was not possible. The methanol required for hydrate inhibition created some issues to be solved, including: contamination of the Allegheny crude, storage tank material and stress corrosion cracking of the titanium stress joints in the steel catenary riser (SCR).
- Gas metering: Due to the fact that three wells were commingled through two flowlines to the TLP, subsea multiphase meters were installed downstream of each well for production monitoring.
- Flaring: Due to the large volume of gas to be flared on this small platform and need to avoid increasing flare boom length and weight, a special, low-radiation flare tip was installed.
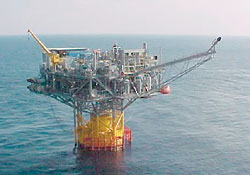 |
Agip Petroleum’s Allegheny TLP receives and processes gas from three subsea King Kong-Yosemite field gas wells through two 16-mi-long flowlines.
|
|
As noted, the King Kong-Yosemite field (KKY) comprises three gas-condensate wells tied together and back to Agip’s Allegheny TLP, by dual 8-in. flowlines/risers, two 5-in. infield flowlines and a system of umbilicals. The Allegheny facility comprises a two-level deck, mounted on a single-column mini TLP (TLP/Seastar), which is tethered to the ocean floor by three pairs of rigid, tubular tendons, supported by three pontoons arranged symmetrically around the hull. The facility is located in Green Canyon Block 254 (see accompanying figure). Allegheny is a mini TLP, constrained in terms of space and weight. It was mainly an oil-treating facility, designed for 27,500 bopd, 50 MMscfd gas and 10,000 bwpd. After King Kong, gas handling capacity was increased to 200 MMscfd.
For the weight/space concern, and because Allegheny is a small and very tight floating facility in which weight control was one of the keys, a major effort was made to control structural integrity of the TLP by evaluating and monitoring weight distribution, and the center of gravity (CG) location. Total weight and lateral CG were determined and designed to be within the TLP’s structural limits. Lighter components were selected, e.g., almost 80% of the process valves installed topside for King Kong were compact and light. This reduced the associated weight, compared to conventional components, by 30%.
To reduce riser payload, non-continuous buoyancy was installed through the King Kong risers, using a syntactic polyurethane inside medium-density polyethylene shells. Each riser utilizes 271 separate modules, giving a total buoyancy of 53,000 lb. Polyurethane and polyethylene are also good insulating materials. Due to the cold processing to be used for the King Kong wells, pipe insulation was required.
The problem of reducing payload also was related to the King Kong umbilical. In this case, it was decided to use thermoplastic materials (rather than metallic) for the hydraulic hoses. This reduced weight in the seawater, but caused failure of the two high-collapse-resistant hydraulic hoses during the factory acceptance test. Also, four of eight electrical conductors failed due to splice failures at the connector assemblies. It was decided to fabricate a supplemental umbilical to be installed in April 2003.
For the additional gas processing, King Kong wells have wellhead pressures of 6,500 psi (450 bar) and gas arrives at very cold temperatures (40°F, 4.5°C). So to achieve maximum allowable sales gas water content without expanding the existing dehydration system which treated only 50 MMscfd, the King Kong addition adopted the cold-processing methodology. The gas arrives topside at 35 – 40°F; this temperature is maintained constant through proper insulation of incoming flowlines. At this low temperature, the separation of liquids from gas is almost complete, and gas goes straight to sales.
For the methanol issue, since the gas temperature drops from 112 – 120°F at reservoir conditions, to 35 – 40°F in the flowline, saturated vapor condenses to free water in the 16 mi of flowline. And limited space/weight availability prohibits use of glycol. The only solution appeared to be methanol use. However, the required methanol injection created carryover with the condensate and into the sales crude. To solve this problem, a new piece of equipment was added, the water-wash system. This additional stage allows the methanol to be completely captured by added, treated seawater.
Two 400-bbl methanol tanks were installed on the TLP, but a fire protection barrier was required on the tanks for safety. And to reduce the additional weight impact, rather than any kind of mechanical shield or fire barrier, a special fireproofing paint was used, Chartek 4. In a fire, this paint expands to form a low-density, carbonaceous char to act as an insulating blanket.
Special consideration was also given to protecting the titanium alloy stress joints on the King Kong risers. Since solutions above 95% methanol can create problems due to permeation into the crystal lattice of the stress joint material, methanol injected into the King Kong wells is a strictly controlled mixture of 95% methanol and 5% water.
Gas metering. Since the King Kong field production is commingled at the subsea manifold, proper production allocation is necessary. Because of the subsea commingling, the project selected use of subsea wet gas meters from Solarton ISA. One meter was installed in each of the well jumpers downstream of the subsea tree, so each well’s flowrates could be measured continuously. This is the first application of such flowmeters subsea in the Gulf.
The ISA DualStream II flowmeter measures gas flowrate and total liquid flowrate, although it is not able to directly measure individual flowrate of water/ methanol and condensate. This is accomplished with post processing by a computer program. By knowing continuous injection flowrate of methanol for each well, the PVT routine supplies flowrates of gas, condensate and water.
Gas flaring. The Allegheny existing relief system was designed to treat about 50 MMscfd gas. The King Kong addition required increased capacity up to 200 MMscfd. The main concern about that was replacement of the existing flare tip. This tip was designed to handle up to 50 MMscfd but, over 25 MMscfd, heat radiation to the TLP was close to the tolerance limit. To maintain the required tolerance limit with a much higher flaring rate, a special, low-radiation tip was installed. The new tip is a high-pressure, variable orifice, sonic tip, compared to the existing one. This high-efficiency tip uses the energy of a high-pressure gas to entrain and mix air into the flare gas prior to ignition. With this tip, flare turndown (ability to efficiently/smokelessly flare a wide gas-rate range) is 12 times higher.
King Kong was a fast-track project, requiring 16 months from sanction to first oil. The project break-even point was reached after less than 12-months’ production.
This summary report was prepared from the paper “King Kong project: A challenging subsea tieback of a gas field to an existing mini TLP in the Gulf of Mexico,” Copyright OMC 2003, presented by the authors at the Offshore Mediterranean Conference and Exhibition, Ravenna, Italy, March 26 – 28, 2003. 
|