Next-generation electric fracturing system improves efficiency, ESG performance
Hydraulic fracturing has experienced rapid transformation over the last several years. The market of the early 2000s and 2010s is a distant memory. In today’s energy economy, operators are seeking to increase value while reducing cost and non-productive time (NPT). Traditional oil and gas energy sources are competing against other investment opportunities and investors are asking energy companies to focus more on returns, cash flow and capital discipline. This focus on financial performance starts at the wellhead, where energy producers look at the cost of a barrel of oil and focus on levers that allow them to reduce the cost of production. This pressure is pushed down through the supply chain, including service companies, suppliers and original equipment manufacturers (OEMs). An ongoing change in the industry is underway to ensure greater better returns.
ESG CHALLENGES
This pressure is not just on the economics of producing a barrel of oil but also on how it is produced. Over the past few years, one of the significant changes in investor philosophy has been an increased focus on environmental, social and governance (ESG). This increased focus has forced all aspects of the supply chain to examine their product portfolio and quantify their performance. As described by the U.S. Environmental Protection Agency (EPA), the Greenhouse Gas (GHG) Protocol asks companies to examine Scope 1 (direct) emissions, Scope 2 (upstream activities), and Scope 3 (downstream activities). Reporting agencies and large institutional investors have adopted this scope methodology to quantify the performance of companies and their products.
These new challenges have forced E&Ps to evaluate all aspects of manufacturing their wells—drilling, completion, stimulation, intervention and production. In other words, they are looking at the cost of producing a barrel of oil equivalent and emissions, which comprises all the services required to create and produce a well. Two of the most significant activities in creating an unconventional well are drilling and fracturing. Fracturing is the single most energy-intensive function in oil and gas, making it a considerable target from a financial and ESG perspective.
Technology is being developed and deployed across the fracturing industry to tackle these challenges. This includes the application of various prime mover technologies, such as new engines, electrical systems, and even turbines adopted from the aerospace industry. Other areas in focus are the fracturing pumps, which are being engineered to be more economical and efficient. Alongside, the improvement in mechanical performance, digitalization, and ESG reporting play a greater role in quantifying equipment and service company performance. These improvements are driving greater reliability and uptime. The industry’s focus on improving fracturing operations is necessary to keep unconventional wells desirable and competitive in the emerging energy landscape.
CLEAN POWER SOURCE
This frac evolution, which has accelerated since 2019, has had one significant advantage: natural gas. Most emerging technologies in prime movers focus on leveraging natural gas as a fuel source. When considering the value of natural gas as a fuel source, a comparison can be made with the most common fuel for highly mobile industrial equipment, diesel. Over the last 20 years, natural gas as an energy source has not exceeded the price of diesel, Fig 1. In recent years, that gap has separated further.
This focus on natural gas, a fuel source, has a secondary value: emissions. Natural gas is a cleaner burning fuel that produces less CO2 and NOx when used versus diesel. This reduction in emissions is a significant step forward in reducing the ESG impact of creating and producing a well. As mentioned earlier, fracturing is the most energy-intensive function in completing a well. Combining cleaner burning fuel with increased energy efficiency and elimination of flaring, an E&P could reduce emissions associated with fracturing by up to 74%. These gains can be even more significant if the electrical grid supplies fracturing energy.
When considering Scope 2 and 3 emissions, one area often not considered is the availability of natural gas near the point of consumption. Unlike diesel, which requires significant logistics and processing to become a usable fuel, natural gas can be consumed close to the point of origin with minimal or no processing, Fig. 2. This fuel, known in the industry as wellhead gas, is highly desirable by E&Ps. This desire is partly driven by the pipeline’s limited takeaway capacity in many shale plays. As shale wells age, the gas/oil ratio increases, meaning that natural gas will become more prevalent in the shale plays as they age, making the ability to consume it locally a strategic advantage for the industry.
The evolution of fracturing technologies is encouraging to the industry, driving better performance and delivering greater value to the E&Ps. This advancement requires significant investment from the service companies that own and operate the frac equipment. These technologies have various benefits that a service provider can leverage to increase their financial performance and ESG profile. E&Ps have responded by awarding these new technologies longer contracts as well as a pricing premium over traditional fracturing equipment.
ELECTRIFICATION
Electrification is one of the areas of increased focus as an ideal solution to deliver on multiple phases of a company’s need to deliver cleaner, more efficient, and reliable solutions. As economics continue to play a more significant role in fracturing, OEMs and service companies will need to deliver better solutions. Electrification is a key technology that allows for increased efficiency and delivers current and future needs. The use of electricity is more than just converting a fuel source to a cheaper and cleaner solution. It is a new toolbox in which physics can be harnessed to leverage a new family of technologies.
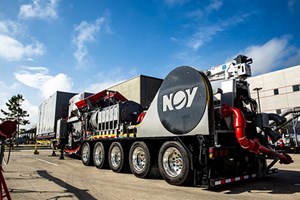
Next-generation e-fracturing. NOV developed the Ideal electric fracturing (eFrac) fleet to simplify the electrification process, reduce greenhouse gas emissions and lower the total cost of ownership for E&Ps, Fig. 3. This 5,000-hp platform combines intelligent electrical architecture and simplified drivetrains to increase power density and flexibility, streamline rig-up logistics, and minimize carbon emissions and sound while maintaining the redundancy that efficient fracturing operations require.
Power density. One of the distinct advantages of electrification is the power density it can deliver. Fracturing will always be a mobile function as the technology will have to travel to the location of the oil and gas resources. The power density opportunity for improvement of reciprocating engines is limited for the frac application. For most practical applications, the mobile requirement limits them to 3,000 brake horsepower (BHP), with many at 2,500 BHP. Utilizing reciprocating engines with natural gas as a fuel source can result in a 30-40% increase in size for an equivalent horsepower. As a result, regardless of fuel source, these engines are not expected to grow beyond the horsepower capabilities of today due to the mobile requirement of fracturing.
The Ideal system replaces reciprocating engines and transmissions with a direct-drive electric motor. Using the greater power density of electric motors enabled NOV to develop a 5,000-hp frac pump trailer that is road-legal and has a smaller footprint than conventional diesel-powered fracturing fleets, lowering emissions, sound pressures, and disruption to communities. With minimal parts, the electric motor provides longer maintenance cycles for service companies, reducing not only costs but also NPT.
Pump technologies. Power density is more than just fewer pieces of equipment to move to the location; it can provide significant advantages when considering the frac pump’s maintenance costs. Frac pumps are the single largest maintenance item on a frac fleet and the most substantial opportunity outside of prime movers to positively impact the cost of operating a fracturing fleet.
Like prime movers, frac pumps are improving and evolving. The latest advancements in frac pumps are focused on higher horsepower applications. These advancements focus on the lifetime economics and performance of a pump. New pump technologies, such as advanced power frames, allow for larger rod loads, lower RPMs, and fewer cycles. Improved lubrication systems and bearings enable pumps to be rated for continuous duty.
NOV conducted a case study examining more than 5,000 hours of operation. The study found that using Ideal’s 5,000-hp continuous-duty pumps resulted in between a 37% to 44% reduction in pump maintenance costs associated with valves and seats. Additionally, there was a 21% reduction in fluid end replacement costs. These performance gains are expected to continue to grow as these higher horsepower pump technologies continue to mature.
Blenders and backside equipment. The benefit of electrification is not limited to the high horsepower pumps. NOV’s Ideal solutions bring the value of electrification to backside fracturing operations through greater flexibility, feedback, and control. The complexity of mechanical equipment can be simplified through electrification, which can lead to high reliability, often one of the largest challenges with backside equipment. This challenge can become greater with the desire to move more personnel away from the equipment and operate it remotely. The Ideal electric equipment leverages the feedback provided by electrical processes to enhance the controllability of backside equipment.
Power flexibility. One distinct advantage eFrac has over other available technologies is that it can use this natural gas phenomenon and other power generation technologies, such as renewables, nuclear, and other forms of electrical power, either wholly or in part. Decoupling the consumer (electric motors) from primary conversion (fuel to electricity) makes the technology agnostic and, in this case, advantageous to use the most cost-effective and cleanest fuel sources available.
This flexibility to utilize multiple energy sources becomes increasingly important when considering emerging markets, where natural gas infrastructure may be limited or is considered a more valuable commodity.
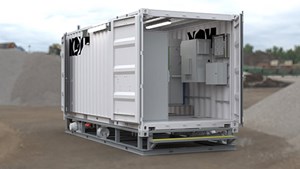
Power pods. Transitions to new technologies can be a challenge; NOV’s Ideal Power Pod enables scalable eFrac deployments alongside conventional diesel-powered frac units, Fig. 4. By providing up to 15,000 hp per pod, the modular power distribution system can eliminate the need for up to eight traditional units, saving about 800 gallons of diesel per hour. Additionally, when used with a conventional dual-fuel fleet, the Power Pod system allows for optimal natural gas consumption across the entire fleet, leading to further reductions in diesel consumption and emissions. Technologies such as the Power Pod can enable service companies to take meaningful steps to integrate eFrac into their product offerings through hybrid fleets and expand their knowledge and capabilities at a lower cost.
Digitalization. The E&Ps and service companies strive to bring more uptime and reliability to the frac market while also seeking to manage workforce costs and compliance with rules and regulations. This aim forces the equipment to become more reliable, predictable and intelligent. The answer to this challenge, in part, is digitalization.
As mechanical systems can be made to be intelligent through the addition of sensors and telematics to inform control systems, electrical systems have these capabilities embedded in them as part of the architecture. This entrenched digital control and feedback make electrical systems well-suited for automation and remote operation. As a result, Ideal is one of the industry’s first and most advanced remote-controlled eFrac fleet, with fully automated processes, intelligent machine monitoring, and analytics.
Whereas mechanical systems rely very heavily on calculated or inferred values, an electrical system can report a significant amount of data that can provide much more information. For example, an electric motor with a variable frequency drive versus a hydraulic motor with a proportional valve—at a high level, both perform a similar function. With the hydraulic system it can only report on a few parameters, such as pressure and calculated flow and additional sensors, such as flow, temperature, and oil cleanliness, can be added to create a more comprehensive system, but at additional cost and complexity which is often left behind in our industry as cost and complexity are seen as negatives. With Ideal’s electrical system, the drive will generate an accurate speed reference torque level, amperage, voltage, drive temperature and system status. The increased visibility allows for greater equipment insight and, as a result, better automation with fewer total pieces of hardware.
This feedback is not just limited to controllability. It can also be leveraged to make more intelligent equipment that can pinpoint the areas of concern and report to maintenance personnel to perform an activity before a critical failure. A great example is in looking at variables over time. By measuring and reporting actual work being done by the equipment, such as amps from a drive, an algorithm can be developed to monitor and compare it against a previously known value and, as a result, report a deviation.
This is the first step in creating a comprehensive equipment health program, which leads to increased asset utilization and reduced NPT. This can be done with a simple code addition; no additional hardware must be purchased or maintained. In short, going to electric makes the transition to intelligent equipment seamless.
ADDITIONAL CHALLENGES
Electrification is different than what the fracturing market has historically seen, and it does take some other levers to make it successful for everyone including:
Contractual. One of the major challenges is where the power is coming from. Several companies have entered the power generation frac market through a service model, but it adds complexity to the contract side of frac. This complexity requires that all parties see a benefit to adopting the technology. Electrification is unique in that it can offer benefits to all parties; however, it will likely be a more complex contractual process as more organizations are brought into the negotiation process.
Service personnel. As OEMs bring this technology to their customers, they must be willing to support it. Service companies may have little or no expertise on staff to facilitate a transition. Depending on the service companies, they may rely on suppliers to play a more pivotal role in the service of the equipment for a more extended period, if not perpetual.
Training. A service company may need to lean on outside organizations or suppliers to provide more significant training. Equipment manufacturers must provide expertise to guide service companies in safely and efficiently using the equipment. As companies evaluate solutions, they should consider not only the equipment but also the training capabilities of the supplier.
Collaboration. As in any transition, there is a learning curve. As technology evolves, typically, the complexity does as well. Therefore, collaboration and open communication are essential for a successful outcome. This can come as a challenge to suppliers and customers alike. By understanding where we are as an industry, our capabilities and limitations, we can build successful cooperative relationships that fuel healthy and lasting collaboration.
CONCLUSION
Change is here in the fracturing market and promises to deliver better performance across the metrics important to investors, operators and service companies. However, not all fracturing options are created equal, and the answer for what makes sense may vary by organization.
Technologies such as the Ideal eFrac fleet are essential for unconventional oil and gas to usher in the next generation of performance while delivering responsible, cost-effective fracturing operations. The transition to electric fracturing starts the long and profitable journey for our industry and, most importantly, delivers on what shareholders, customers, and communities demand.
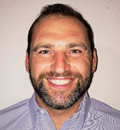
- Regional Report: Which future for Marcellus and Utica shales? (November 2024)
- Industry at a Glance (November 2024)
- What's new in exploration: Happy days ahead, maybe (November 2024)
- First Oil: U.S. upstream industry relieved by Trump’s win (November 2024)
- The ESG perspective: Living in interesting times (November 2024)
- Oil and gas in the capitals: Trump election boosts prospects for domestic oil industry (November 2024)