Developing an F22, umbilical-compatible scale inhibitor for West Africa
A novel scale management program was needed in a field offshore Angola after barite and calcite scales were detected in separate flowlines, as well as calcite in the hydrocyclones on the FPSO vessel. Due to changes in the Angolan environmental regulatory framework, an environmentally improved solution was required to effectively treat the scale.
The presence of F22 low-alloy steel (which contained a significantly lower value of chromium than that found in 316L stainless steel) within the well completion represented a further challenge. The required scale inhibitor not only had to be effective, but it also had to be benign to the materials of construction and compatible with the process fluids. Adding further complication, the solution had to be suitable for application via umbilical. If an inappropriate product is sent through an umbilical, the potential results can lead to significant downtime and add exceptional costs to remediate. Therefore, comprehensive umbilical compatibility testing would need to be performed on any proposed application.
ChampionX, a global leader in chemistry solutions and highly engineered equipment and technologies, was tasked by the operator with conducting development test work to select the optimal chemical solution that would meet all the required specifications, Fig. 1.
FIG. 1. An innovative scale management program was needed in a field offshore Angola that was compatible with low-alloy steel, could be safely applied via umbilical, and met Angolan environmental restrictions.
Customized, synergistic blending. Initially, several scale inhibitor chemistries were examined by dynamic scale loop (DSL) testing; however, none achieved the required scale inhibition performance needed for this particular set of challenges on their own. It was then decided that the next step would be to evaluate blends of scale inhibitors to assess whether a synergy between two different chemistries could offer improved inhibition performance while still having low corrosivity toward F22 metallurgy, being fit for application via umbilical, and meeting the Angolan environmental guidelines.
The chemistries selected for testing were known to have lower corrosivity toward metals. One used a polymer which had previously been applied successfully with F22 alloy and another used a polymer widely deployed in the North Sea in cases where low corrosivity is required along with strict environmental properties.
Since many traditional scale inhibitors are known to be corrosive against low-alloy steels, several additive chemistries were incorporated to further reduce the corrosivity of the blend. These final blends were successful in meeting the scale inhibition performance target and were found to offer good compatibility with F22 alloy under application conditions.
Since the product would be applied through an umbilical, sufficient concentration of dispersants and surfactants were added to make stable formulations. Each candidate chemistry was tested for thermal stability, high-pressure viscosity, cold stress, hydrate resistance and particle count to understand the feasibility of application via umbilical. Furthermore, the candidate chemistries to be tested were compatible with the Angolan guidelines on environmental acceptability.
EXPERIMENTAL METHODS
Upon successful selection of the scale inhibitors to be used, a comprehensive testing program was carried out. These tests included:
- Static thermal stability: formulations are screened for thermal stability at field-appropriate temperatures.
- F22 alloy corrosivity: neat corrosivity toward F22 alloy is assessed at field-appropriate temperatures.
- Brine compatibility: formulations are injected at a range of concentrations into field-representative brine, which is then aged at the required temperature for 24 hours (hr) and assessed for signs of precipitation or haze.
- Dynamic scale loop: Determines the minimum concentration of chemistry required to effectively inhibit scale formation.
- Viscosity: Formulations are subjected to viscosity determination across a range of temperatures to ensure the final product could be successfully used in the field.
- The water compositions used for testing were specified by the operator and closely represented the produced water composition of the field. This water composition (Brine 1) was the base case, and a second brine (Brine 2), representing a stressed condition with increased barium and sulphate concentrations, was also tested, ensuring the chosen product would be suitable, should field conditions change. Both brines presented a harsh barium sulphate and calcium carbonate scaling condition, presenting a challenging environment for effective scale inhibitor performance.
Materials compatibility testing. Materials compatibility testing is done to determine if the selected scale inhibitor is likely to pose a threat to the integrity of the materials of construction. To understand the corrosivity trends, each individual component of the selected chemistries was first evaluated for materials compatibility in a three-day static test at 120°C. To expedite screening of different additives in the formulations, each candidate formulation was then screened under the same conditions. Based on the test results over three days, different formulations were ranked and final corrosivity tests with the top candidates were conducted for 28 days.
Metal coupons were visually inspected, pre-weighed and then mounted on a tree assembly before being fully submerged in bottles of the test chemistries. The bottles were capped and sealed, and samples were placed in ovens for testing. After three and 28 days, the coupons were removed from the oven, cooled, cleaned, visually inspected, weighed and photographed. The general corrosion rate was estimated, based on the weight loss of individual coupons following the equation as shown below.
Where W = Weight loss (mg)
D = Metal density of coupon (g/cm3)
A = Area of coupon (cm2)
T = Period of exposer (hr)
Post-test coupons were further inspected for localized corrosion. Two coupons were used for screening purposes (3-day test) and three coupons were used for the final round of testing (28-day test). Localized corrosion assessment using vertical scanning interferometry (VSI) of the final recommended product was also conducted for the specific assets. A Bruker optical three-dimensional surface profilometer NPFlex-LA was used for characterizing metal coupon surface features. The surface-scanning technique based on VSI provides non-contact, quantitative measurements with a micron resolution in the vertical axis.
The NPFlex-LA determines the size and shape of the surface features over the whole scan area. Interferometry scans the entire coupon surface and quantitatively reports regions or features that deviate from the average surface baseline of the coupon. Not all surface features should be identified as a “pit” or “pitting corrosion,” as very minor changes in the surface structure may be labeled as a deviation from the average surface plane. These features may include inclusion complexes in the metal, grain structure lines, or imperfections, due to the surface finish technique. The scanning process identifies the topography of the surface, and post-scanning filtration of the data set allows for differentiation of scanning noise versus well defined, localized corrosion or pitting corrosion.
A description of surface features via these parameters is intended to give a more quantitative representation of the overall surface quality after exposing the coupon with different chemistry. However, for this project, no specific criteria were set, so all features greater than 10 microns in depth on the post-test coupons were captured and processed accordingly. Notably, one of the scale inhibitors intrinsically showed low corrosivity, so emphasis was given to consider, including this specific scale component in the final formulation.
Brine compatibility testing. For brine compatibility testing, the scale inhibitors and brines were mixed at varying concentrations, including 0 ppm, 1,000 ppm, and 1%, 10%, 25%, 50%, 75% and 90% chemical in brine. The solutions were then shaken and placed into an oven, to be heated to 110°C for the evaluation period. They were observed at 0, 2, 4 and 24 hr for precipitation, changes in clarity or phase separation.
While an area of incompatibility was seen, initially comprising haze formation immediately after mixing at 10% and increasing to form precipitation between 1% and 75% after 24 hr, one of the proprietary scale inhibitor blends was fully compatible at the lower concentrations recommended for application. This was over the time periods that the chemical was likely to be present at application concentration.
Dynamic compatibility testing. Dynamic compatibility testing aims to replicate the application of scale inhibitor from neat chemical to the laboratory-determined minimum inhibitor concentration (MIC), which would determine the ideal application concentration, Fig. 2. This testing was performed by injecting the scale inhibitors into the brine at the application concentration. The samples were then heated to field temperatures, and the injection point was observed for any haze, precipitation, or gel formation. No precipitation or haze formation was seen at any point during or after injection, indicating full compatibility with the brine at the tested temperature.
FIG. 2. Dynamic compatibility testing in brine at 90°C (mid-injection).
Static jar testing. Static jar testing assesses scale inhibitor performance as crystal growth modifiers against barium sulphate and is an industry-standard method. For static jar testing, powder jars were prepared with anion brine. The candidate scale inhibitors were then dosed into these jars at the appropriate volume for the required concentrations. In addition, a blank sample of anion brine with no scale inhibitor present and a control jar were prepared with sulphate-free brine to replace the anion solution.
Another set of jars was dosed with cation brine. The jars were sealed and placed into a pre-heated oven. After one hour, the cations were mixed with the anions and placed back into the oven. Samples were taken after 2, 4 and 24 hr and were injected into a plastic test tube containing quenching solution to inhibit further scale precipitation. A cap was placed on the test tube and the solution was mixed. Each sample was analyzed for barium within 48 hr.
A chemistry is considered to effectively inhibit scale if, at the desired concentration, the percentage inhibition is greater than 80%. The scale inhibition efficiency was calculated as:
Where:
CB = cation concentration in the blank
Ci = cation concentration in the test (inhibited) samples
CO = cation concentration in the control
Figure 3 shows the results conducted using the static jar test method, which measured efficacy against barium sulphate scale formation. The results indicate that over a 24-hr test period, 5 ppm was sufficient to prevent scale for both scale inhibitors (SI-B and SI-D) being tested using Brine 1.
FIG. 3. SI-B and SI-D under static conditions, 90°C, 24 hr, Brine 1.
For Brine 2, with increased barium and sulphate concentration, the minimum inhibitor concentration (MIC) for SI-B increased to 10 ppm after two hr, 15 ppm after four hr and 20 ppm after 24 hr. For SI-D, the MIC increased to 15 ppm at two and four hr and 20 ppm after 24 hr, indicating comparable performance, Fig. 4.
FIG. 4. SI-D under static conditions, 90°C, 24 hr, Brine 2.
Dynamic scale loop performance testing.
In line with standard DSL testing protocol, freshly prepared brines were filtered through a 0.45µm membrane under vacuum. Both brines then passed into separate heating coils within the oven. At a T-junction, the brines mixed and passed into the scaling coil. The differential pressure is measured across the coil and will increase, once scale formation and adhesion to the coil wall cause a blockage. If the formation of scale within the coil rises 1psi above the baseline, the result is a “fail.”
DSL testing assesses scale inhibitor performance as nucleation inhibitors against both barium sulphate and calcium carbonate. The method was selected to confirm which of the scale inhibitor blends would show equal, or superior, performance over multiple test methods. DSL testing was carried out on several scale inhibitors, Fig. 5.
FIG. 5. DSL testing using Brine 1, 1000psi, 110°C, 6.8 pH.
The blank time, i.e., the time taken for scale formation to cause a differential pressure rise of one psi above the baseline for Brine 1 was recorded as around 12 min. This results in a chemical hold time of 36 min. (3x the blank). The results show SI-D was the highest-performing scale inhibitor, with an MIC of 15 ppm, followed by SI-C and SI-B, both with an MIC of 30 ppm. The polymer SI-A had an MIC of 20-30 ppm.
For Brine 2, the blank time was recorded at about 8 min. with a chemical hold time of 24 min. (3x the blank). Again, the results show that SI-D was the best-performing chemical with an MIC of 15 ppm, followed by SI-B with an MIC of 20 ppm.
CONCLUSION
All testing performed by ChampionX detailed the process whereby different additives were evaluated with scale inhibitors to develop a formulation that provided an acceptable general, as well as localized, corrosion rate against F22 low-alloy steel. The final candidate formulation, SI-D, was compatible with the brine at the concentrations and time periods likely to be experienced in the field and was subsequently effective against a mixed barium sulphate and calcium carbonate scaling regime.
Several conventional and widely applied scale inhibitor formulations were evaluated against the brine chemistry provided and were found to have higher MICs than the proprietary blend of the same scale inhibitors tested via DSL. There, the lowest MIC was determined to be 15 ppm, versus 20-30 ppm for the scale inhibitors evaluated on their own. The results of DSL testing suggest a degree of synergistic effect was seen.
However, static jar testing indicated a similar level of performance between the different test chemistries against a purely barium sulphate scaling regime, indicating the synergistic effect may not be applicable to all scale types. Further laboratory testing to quantify the synergistic effect, or otherwise, of the scale inhibitor blend against a range of conditions and scales is ongoing.
ACKNOWLEDGEMENT
This article contains elements of SPE paper 209495-MS that was presented at the SPE International Oilfield Scale Conference and Exhibition, held May 25-26, 2022, Aberdeen, Scotland.
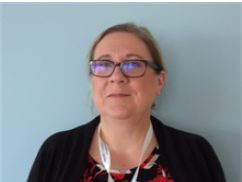




- Regional report: Guyana-Suriname: Rapid expansion of production continues (July 2024)
- Annular safety valves advance flexibility, reliability and safety in completion operations (July 2024)
- Well decommissioning: Simple solutions to complex problems (June 2024)
- Rethinking sand management for optimized production (June 2024)
- Can an offshore drilling rig run on green methanol? (May 2024)
- Custom-made blueprint for optimizing late-life assets (April 2024)