Increasing recovery by reducing oil in water with production chemicals
Africa remains one of the most consistent oil-producing regions in the world, with proven crude oil reserves of 125.3 Bbbl in 2021.1 Nigeria is one of the continent’s largest oil producers and according to the African Energy Chamber,2 has the potential to become a leading exporter to Europe, as the energy security crisis continues.
To meet anticipated local, regional and international requirements, maximizing production from existing discoveries in offshore Nigeria’s deepwater environment is paramount. With increasing volumes of produced or effluent water created during oil and gas operations, it is imperative to limit or prevent emulsifications, which can impact output efficiency and proactively control the formation of sulphate and carbonate scales to maintain flow assurance and the integrity of the production system.
Excessive water production. As wells mature and more hydrocarbons are extracted from the reservoir, the water table in the reservoir rises. More water is then produced, increasing the potential for scale deposition. This produced water often contains residual quantities of oil and, in many cases, solid particles. While any oil left in the water can potentially waste the time and money spent bringing it to the surface, separating even small amounts of oil from water over a period can lead to increased revenue.
An alternative option is to reuse the water. However, when produced water is used to supply a waterflood or steam flood program, it must be clean. Oil and solids can quickly foul expensive water-softening resin beads. Dirty water also can lead to costly maintenance programs for injection wells. Therefore, for both opportunities, many types of equipment are used to separate as much oil from water as possible. A bespoke chemical program is considered the most viable and efficient method to improve the efficiency of equipment and reduce the cost of the overall operation.
ChampionX, a global leader in chemistry solutions and highly engineered equipment and technologies, was contracted by a major independent operator in Nigeria to test and develop a customized water clarifier solution to treat the produced water outlet of their first-stage separator.
Produced water treatments. Before operators in Nigeria can decide the best plan of action to support production optimization, strict water discharge criteria must be met with varying government requirements across the region. Several conventional methods are available to treat the produced water, as well as overcome problems, such as production and waste management. These include gas flotation equipment, whereby tiny gas bubbles attach themselves to solid and liquid contaminants and cause them to float to the surface for easy removal.
Another common practice is the use of corrugated plate interceptors (CPIs). When oily water passes between the plates, free oil particles rise until they collect and coalesce on the underside. This amalgamated oil then travels upstream along the plate until it reaches the water surface, where it is skimmed off and collected. The use of hydrocyclone technology was the preferred choice of the operator in the project with ChampionX, Fig. 1.
Here, produced water from the separators is introduced indirectly through a rectangular port in a conically shaped chamber. As the water rotates rapidly around the chamber, and moves downward, the decreasing diameter causes high centrifugal acceleration of the water to the outside wall, pushing lighter oil droplets to the center of the cone. The oil rises to the top and flows out, and the water then exits the bottom of the cone.
Thorough testing and analysis. The operator had been experiencing issues with extremely high oil-in-water (OIW) content in the produced water from their first-stage separator. This averaged approximately 3,500 ppm going to the produced water surge drum (PWSD). As the hydrocyclone was out of service during the plant trial, the off-spec produced water was being sent to the slop tank to stabilize for a minimum of 48 hours (hr) before it could be disposed.
Often, even after several days of “polishing” in the slop tank, the water quality did not meet the government’s discharge regulation limit of 40 ppm and had to remain in the slop tank until it met specification. The produced water also presented problems for production and waste management. An incumbent’s water clarifier had been applied, but it did not decrease the OIW content.
To address the problems associated with persistent effluent quality, ChampionX was contracted by the operator to perform a series of on-site static bottle tests to evaluate the efficiency of its water clarifier products and put forward the most efficient chemical treatment solution. Bottle testing is used most widely for water clarification testing, Fig. 2. Clear, calibrated 6-oz. prescription bottles were used, which conveniently hold 100 ml of produced water. The tested treatment dosages ranged from 50 ppm to 500 ppm.
After the water clarifiers were applied, the samples were agitated and then observed visually to assess the clarity of the water for benchmarking purposes. This is commonly done by looking through the bottle at a printed surface, such as a paint pen. The bottles are graded after each agitation on a scale of one to ten, with one being the worst. At the end of the evaluation, the results showed that water clarifier CLAR16029A performed the best of all the chemistries tested to achieve the specification required.
Water clarifier field trial. Over one month, the product was injected at the produced water outlet of the first-stage separator at a startup dosage rate of 7 ppm. By the end of the field trial, this rate was gradually optimized to 15 ppm. As both the hydrocyclone and the produced water degasser were bypassed, the produced water was stabilized in the slop tank, and in less than 24 hr, the OIW met the regulatory requirement of less than 40 ppm. This compares to more than 48 hr with the previous chemical application. The results of the application on the customer facility are shown in Fig. 3.
Improving efficiency and oil recovery. During the field trial, oil recovery from the produced water at the PWSD increased from 1.29% before the introduction of CLAR16029A to approximately 83% after the water clarifier treatment was started. The operator authorized the chemical program immediately, and the product continues to be used. After the hydrocyclone equipment was repaired and re-commissioned, the practice of sending the produced water to the slop tank for stabilization to meet the regulatory limit of 40 ppm was discontinued.
The results clearly demonstrate that an effective water clarification program can be used to increase OIW recovery, improve the efficiency of water treating equipment and reduce the cost of the overall operation. Most importantly, it can be used to ensure regulatory compliance to discharge requirements and therefore, optimize waste management practices and improve the environmental sustainability of oil and gas operations.
REFERENCES
- https://africa.businessinsider.com/local/markets/10-african-countries-with-the-largest-crude-oil-production-output-in-2021/qbj8bj3
- https://energychamber.org/how-nigeria-can-become-a-leading-oil-and-gas-supplier-to-the-european-market/
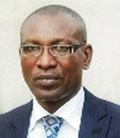
- Executive viewpoint: Advancing offshore crane safety through collaboration (March 2025)
- First Oil: Deepwater Development conference highlights renewed interest in that sector (March 2025)
- What's new in exploration: Gulf of what? Mar del Norte ~1519? Gulf of North America? (March 2025)
- Decarbonizing Scope 3 emissions: The responsible approach to energy travel (February 2025)
- World Oil’s Deepwater Development Conference approaches with great momentum (February 2025)
- Advancing MPD operations with integrated riser joint technology (January 2025)