Streamlining liquid mud plants: Sustainability from the ground up
The oil and gas industry plays a key role in providing the affordable and reliable energy essential for economic growth, employment, education, eradication of poverty and global health. However, the industry must couple its actions around climate change and water conservation to the need for supporting a growing global population’s demand for energy.
Significant progress is expected from research and development (R&D) expenditures made with these specific goals in mind, but impactful gains can be made quickly if sustainability concepts are applied directly to ongoing operations.
There are clear and measurable improvements to be made across the drilling and production value chain. Routine field activities and facilities that have been taken for granted for decades can be effective drivers of positive environmental change.
THE 3R’S
As an example, the time-tested liquid mud plant (LMP), always there to support drilling and completion operations, is the perfect candidate for a “3R” overhaul.
Reduce. The widespread use of non-aqueous fluids (NAF) has engendered numerous fluid recovery techniques. Some of these can be accomplished with mobile units at the rig site, but the LMP remains the centerpiece of fluid recovery, solids separation and preparation of “new” mud systems for the next wells in line.
To accomplish this, the typical LMP comprises multiple mixing tanks and fluid storage options. A large, busy stockpoint may have thousands of bbl of various fluids stored in purpose-built tanks. A well-run LMP must operate on two critical principles: 1) reduce disposal volumes; and 2) reduce dilution requirements.
Reuse. One of the chief benefits of NAF systems is their longevity. With proper conditioning and reconditioning, a NAF may be shipped in and out of the LMP to dozens of wells. Density adjustments can be simplified by blending with differing properties. The blended systems can be processed to meet most operator specifications. The industry’s paradigm shift to large-scale shale drilling also plays a part in how efficiently drilling fluids can be reused. If the well is destined for a shale frac job, the operator often relaxes the LGS percentage specification, because near-wellbore formation damage is no longer a critical factor. The high rates of penetration delivered by an NAF help reduce drilling days, and the availability of rig-ready feedstock at the LMP makes it easy to move to the next well in the batch with no downtime.
Likewise, water recovered from water-based fluid (WBF) can be used as wash water or added to many types of drilling fluid (water phase for NAF, base fluid for WBF), or it can be used to formulate some completion fluids. Thoughtful reuse helps reduce overall consumption of fluid components. Reducing consumption means fewer orders to suppliers, less material transported over the road or sea, less dependency on storage tanks that require lighting, maintenance and fluid agitation, and a smaller environmental footprint reaching from the point of sale to the original manufacturer. These positive changes may seem small and incremental at best, but the scope of drilling operations worldwide guarantees that the cumulative effect is significant and measurable.
Repurpose. A spent fluid system is not repurposed easily. Disposal seems necessary at the end of the fluid life cycle. Wash water from tank cleaning is a good example, as are WBFs that are no longer in spec for sensitive wellbores and will not hold up well in storage. However, a well-equipped LMP can help transform these “waste” fluids into the key components in other pumping and circulation activities, where a sizable volume of fluid is necessary, and fluid quality is less critical. These crossover applications extend the usefulness of the fluid and help reduce disposal volumes in the long run.
Optimizing LMPs for the 3Rs. Lean operations naturally foster greater efficiencies, often well beyond the original objectives. Consistency, standardization and continuous improvement are the subsets of an efficient plant. What may start out as a sensible cost-saving effort in fluid management—such as blending fluids to achieve density targets—can also deliver repeatable gains in sustainability.
To make these gains, Halliburton recently launched an LMP assessment initiative that encompasses multiple facilities around the globe, each with its own unique set of conditions. A five-stage process is applied to each candidate LMP, beginning with the selection criteria and ending with measurable results, Fig. 1.
CANDIDATE SELECTION
In this assessment, the top candidates among LMPs are sited in various locations around the world, Fig. 2. Selection is based on operations and capabilities, rather than proximity to major industry centers. In fact, some plants are very remote or operate near residential areas, and this can heighten the importance of a positive impact on local communities and sustainability. The essential traits include the following:
- Large volume of NAF throughput / return due to the intrinsic reusability of these systems
- Strong demand for high-value base oil systems
- Frequent handling of high-value brines in certain locations.
This does not exclude conventional diesel-based NAFs as good candidates for reuse and blending operations, even though the cost per barrel (bbl) is low by comparison to the “designer” fluids used in deep water and other complex wellbores. Likewise, WBFs need consideration when it comes to reuse and repurposing. Although these fluids are certainly not as durable as NAFs, the LMP optimization plan includes looking for ways to “3R” all fluids to the extent possible.
Data capture. Given the variability among LMPs and their respective capabilities, settling on an “always applicable” data set is possible only for certain metrics that provide insights into possible replacement materials and/or alternative packaging that can reduce the environmental footprint. Another part of the analysis focuses on the use of solids removal technologies to significantly improve fluid reusability, and this is compared to the costs and inventory management issues raised by dilution/disposal options. The knock-on effects can ripple through the supply chain and have an overall result of less waste, less energy consumption and less risk to sustainability. These outcomes translate to fewer emissions, which is part of the company’s commitment to establishing viable ESG targets.
Implementation. Halliburton deploys a small team of subject matter experts to evaluate each LMP. This group includes operations managers, equipment champions and information technology specialists, among others. New workflows and purpose-built spreadsheets help the team organize data extracted from various sources. No two LMPs have identical conditions, and the types and extent of improvements can vary. However, it’s a strong and essential first step to what becomes habitual environmental conservation.
Results. Halliburton can facilitate the 3Rs at its LMPs, at the rigsite and throughout the network of manufacture, packaging, transportation and final disposal. Following the 3R strategy, Halliburton has decreased purchases which helped reduce inventory by over 34,000 bbl and helped prevent some of the emissions typically associated with the manufacture, transfer and mixing of new fluids and their components.
The innovative equipment used to make this happen cannot be overlooked:
- High-performance centrifuges are configured in parallel to process an average 60,000 bbl per month at major LMPs.
- Advanced solids separation units can be installed anywhere to produce a low-solids pre-mix mud for blending, and the dried solids can be used as material for treating non-critical fluids, 3.
- High-efficiency mixing devices ensure that NAF systems are rig-ready when they leave the LMP, which helps eliminate rig time spent on conditioning the fluid and results in lower, less-costly energy consumption.
FINAL THOUGHTS
While the industry is making significant R&D investments to drive environmental performance, technology development takes time, and many innovations will require significant capital to scale. Instead of waiting, much can be done now to drive immediate impact.
Ensuring our progress in sustainability can begin with a hard look at some of the most mundane operations. Instead of dealing with acres of tanks filled with “hurry up and wait” fluids, LMP managers are now proactively cleaning, blending and reusing all possible feedstock. This helps ensure an ample supply during periods of high activity and helps minimize the negative impact of excess inventory during a downturn. They are tracking reductions and calculating environmental gains throughout the fluid life cycle and following up with continuous improvement steps wherever appropriate.
To date, this 3R process has been implemented successfully at ten LMPs around the world. The goal is to evaluate and optimize six to eight facilities each year, going forward. This is a “ground up” movement that incorporates personnel on the front line and allows them to be the faces of industry’s commitment to greater environmental responsibility. In any case, it’s a great place to start!
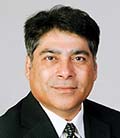
- Regional report: Guyana-Suriname: Rapid expansion of production continues (July 2024)
- Annular safety valves advance flexibility, reliability and safety in completion operations (July 2024)
- Well decommissioning: Simple solutions to complex problems (June 2024)
- Rethinking sand management for optimized production (June 2024)
- Can an offshore drilling rig run on green methanol? (May 2024)
- Custom-made blueprint for optimizing late-life assets (April 2024)