Improving efficiency is driving a new generation of frac plugs
When multi-stage hydraulic fracturing shifted from vertical wells to horizontal wells, and as horizontal wells became longer with tighter stage spacing to access more reservoir, stimulation operations became more time-consuming and complex. This brought with it a higher risk of issues.
The need for continuous improvement in plugs arose, due to increasing setting depths; challenges, such as pre-setting during installation; long run-in times; and the ability to quickly remove the plugs after stimulation to allow the well to go on production sooner. Completion equipment providers responded, continually evolving the design and material composition of frac plugs to overcome these challenges, which stemmed from advancements in horizontal multi-stage hydraulic fracturing.
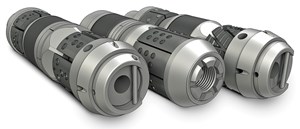
In December 2018, Packers Plus launched its TREX Lightning Frac Plugs (Fig. 1), designed specially to overcome operators’ challenges and provide increased efficiency with reduced operational risk, to get the most out of every well. The full lineup includes the Lightning Frac Plug and LightningPLUS Composite Plug, which both enable quick mill-out times, and the LightningBOLT Dissolvable Plug, to fully eliminate mill-out.
FRAC PLUG DESIGN
Over the years, the length of frac plugs has decreased significantly. Part of this has been achieved by creating a simpler plug with fewer parts, which has led to increased reliability and reduced mill-out times from having less material.
Material changes also have been a major shift in frac plug design. Early plugs were composed of various metals, which led to long mill-out times and large debris that often did not flow back. Current frac plugs are typically composed of all composite material. The all-composite material and designs are improved continuously, and today accommodate approximately 90% of the oil field’s requirements. There is still a need for metal designs in high-pressure and/or high-temperature (HPHT) environments.
FRAC PLUG INSTALLATION
Plug-and-perf is an inherently slow method for completing wells, by virtue of tripping in and out of the well with tools for every stage, then pumping the stimulation treatment. In vertical wells and later in single stage count horizontal wells, this operational time was not significant; however, as extended-reach laterals become more commonplace and stage counts reach into the hundreds, a typical run-in rate of 200 to 300 ft/min can make for an onerous and expensive completion operation.
If frac plug design can be improved to enable quicker run-in rates, operators can realize significant cost-savings with reduced fluid use and reduced pump time. The short length of the Lightning and LightningPLUS plugs enables fast pump-down, with typical operations averaging 450 to 550 ft/min., with line speeds as high as 1,000 ft/min.
Frac plugs that pre-set while being run-in-hole are another issue that can occur during installation. At best, this will result in added operational time and cost, as well as the added expense of retrieval equipment to remove the pre-set plug before resuming operations. A plug that has pre-set also may impact future operations of the well, as run-in-hole (RIH) speeds may be reduced significantly to limit the chance of another pre-set until a permanent solution is found.
Some makeshift wellsite solutions are sometimes implemented to prevent frac plugs from pre-setting on older-style or less-reliable plugs, but our firm has taken additional design measures to mitigate this issue. The LightningPLUS composite plug includes multiple, engineered anti-preset features built into the plugs, as well as the wireline adapter kit (WLAK). When combined, the anti-pre-set features in the plug and the WLAK prevent the tool from pre-stroking during pickup, and pre-setting during installation, before the plug reaches its planned depth.
FRAC PLUG MILL-OUT
Decades ago, in the early days of multi-stage fracturing of vertical wells, frac plugs were made from heavy material and outfitted with cast iron slips. These early plugs took longer to mill out, compared to today’s plugs, as well as having larger and heavier debris left over after milling. Yet, it was less of an issue in vertical wells, where typically only one or two plugs were deployed in a well. Debris from mill cuttings was also less of an issue, because the plug debris just fell to the bottom of the well and did not inhibit current or future operations.
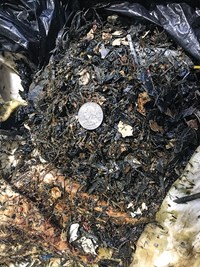
To reduce mill-out times and mitigate stimulation operational issues due to debris, composite frac plugs were developed for multi-stage, horizontal wells. Composite materials (Fig. 2) are lighter, which facilitate faster pump-down times and result in finer mill-out cuttings for manageable debris. Mill-out times for both the Lightning and LightningPLUS plugs are some of the best in the industry, with an average of less than 7 min. for a 5.5-in. plug with 1,500 lb of weight-on-bit (WOB), with motor on bottom.
Even with lightweight composite plugs in a well, extended-reach laterals have made it challenging to get enough weight on plugs in the farthest depths of the well for an effective milling operation. To this end, dissolvable plugs are becoming more prevalent in completion programs, especially in the toe stages of a well, and the LightningBOLT dissolvable plug enhances confidence in this strategy with predictable and reliable dissolution rates.
FRAC PLUG TESTING
Evolving in tandem with frac plug engineering and design has been frac plug testing. Early tests were employed, simply to test the ruggedness of a plug, such as tying a plug to the back of a truck and dragging it around a parking lot before a pressure test to gauge its durability. Other common tests included the drop test and break force test, which can provide a good indication on the amount of force a plug is capable of withstanding when running into a sand bridge or from fluid being pumped and passed before it pre-sets. However, these tests omit the element of actual fluid moving past the plug.
With oil and gas producers drilling longer laterals and constantly pushing the envelope for pump rate and line speeds, it’s important to effectively and confidently pump a plug for more than 20,000 ft of wellbore, and still be able to boast the specs and rating advertised on a plug.
There are a lot of considerations that go into how to effectively simulate pumping a plug downhole and to test for a plug’s effectiveness, both during and after stimulation—flow loop testing is the method standardized at our firm to test our TREX Lightning Frac Plugs. This test method enables testing of the plugs, in combination with fluid, a WLAK and setting tool, as well as the ability to simulate different field environments.
For example, the plugs can be tested in different casing weights to verify performance with changes due to fluid mechanics and flow regimes that vary with the amount of bypass area. The amount of time that fluid flows past a plug can be changed to simulate the longer pump-down times encountered in extended laterals. Pump speed also can be increased to test how the plug responds at various speeds and even identify the exact point at which a plug will pre-set, due to fluid flow.
The one drawback of flow loop testing is that it cannot actively replicate how the plug will react with direct correlation to actively being pumped and moving down a lateral. However, there are several tests that can be performed in tandem, which can demonstrate a plug’s capability. When you combine some of these tests together and look at each result as a piece of the puzzle, a full picture of a plug’s capabilities becomes clear.
FRAC PLUGS IN THE FIELD
An operator working in the Bakken shale was looking to streamline its completion operations by utilizing zipper fracs on a well pad. In short, a zipper frac increases the efficiency of completion operations—especially in a completion operation like plug-and-perf—by alternating operations between two wells to limit the amount of downtime.
For example, while a frac crew is stimulating a stage on one well, a wireline crew is running a plug downhole on a second well. Once the frac plug is on depth and the perforations are shot, the wireline crew and the frac crew will switch wells to perform their tasks. This back-and-forth work between the wireline crew and the frac crew limits non-productive time (NPT), as both services are continuously operating instead of waiting for the other to finish.
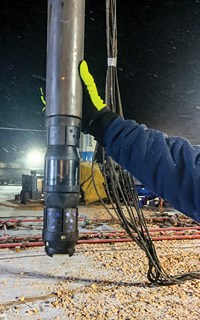
In addition to improving efficiency with zipper frac operations, the operator was looking to optimize initial flowback and mill-out times—a main benefit of fully composite plugs, such as the LightningPLUS Composite Plug, Fig. 3. A completely composite plug typically has a short overall length; quick mill-out times, due to the nature of the composite material; light cuttings that aid in flowback and clean up of the plugs, especially when compared to a heavier material, such as an older cast iron design; and, importantly, they provide an economic solution. When pad drilling and completing multiple high-stage-count wells, economics play a big determining factor when choosing from the variety of plugs on the market.
Another option utilized by the operator to further optimize its operations was using a dissolvable ball on the composite frac plugs. The dissolvable ball will improve operations in two ways. First, during flowback operations, the balls will quickly degrade and prevent any restrictions in the wellbore. Second, a dissolvable ball can prevent issues during mill-out operations. For example, while a plug is being milled out, it’s typical for the nose section below the bottom slips to get pushed down the well to the next plug. This nose section of plug can land on the isolation ball of the next plug and create a ball bearing effect, which causes the nose section to spin and move, increasing mill-out times and mill-out costs. A dissolvable ball will degrade enough to prevent this ball bearing effect and help expedite mill-out operations.
With the right frac plugs selected and operations chosen to optimize the completion program, the stimulation commenced. Each well in the zipper frac was 60 stages. The frac plugs were run as deep as 20,905 ft, TD, at speeds over 950 ft/min. in the vertical and over 450 ft/min. in the horizonal. All 120 plugs were run successfully between the two wells without issue or delay. Mill-out times were as low as 3 min. per plug, with an average mill-out time of 6.5 min.
Another operator working in the Permian basin out of Midland, Texas, put the anti-pre-set feature of the LightningPLUS composite plug to the test by running three of the plugs in the heel of a long-string well, with a TD of approximately 14,500 ft and 67 stages. All three LightningPLUS composite plugs were run successfully to their planned depth, with an average run-in speed of approximately 340 ft/min. After the stimulation was complete, the three plugs were milled out in an average time of 7.67 min., with favorably sized cuttings circulated to surface, due to the lightweight nature of the composite materials.
An offshore operator working on the Gulf of Mexico shelf opted to run the LightningBOLT dissolvable plug after another frac plug was unable to hold pressure. As a result, these dissolvable plugs were used to complete the last six stimulation zones, starting at more than 17,000 ft, and to perform the Bureau of Safety and Environmental Enforcement (BSEE) casing integrity test requirement.
Prior to the plugs being run, Packers Plus provided its ePLUS® Retina well monitoring service on the well. This innovative real-time monitoring system verifies surface and downhole events, without interfering in concurrent operations, using an array of sensors to collect and analyze signals from the wellhead to distinguish various operations.
Successful zonal isolation was detected for each LightningBOLT dissolvable plug, and the stimulation treatment was delivered successfully. Following stimulation, a LightningBOLT plug was run as the lower barrier for a BSEE 30-minute casing integrity test and was verified through qualified third-party testing.
FRAC PLUGS OF THE FUTURE
A year after launch, Packers Plus TREX Lightning Frac Plugs have been run in wells across North America. Following the evolution of frac plugs, this suite of frac plugs incorporates design enhancements, such as anti-pre-stroke and anti-pre-set measures, and the growing popularity of dissolvable alloys and degradable elastomer elements, to improve operational efficiency with faster run-in times and reduced or eliminated mill-out times.
While dissolvable plugs can eliminate mill-out times altogether, composite frac plugs still make up the majority of the market. Milling out 50 to 75 composite plugs in a wellbore is quicker than milling out cast iron plugs, and the smaller debris is easier to handle.
But dissolvable technology is catching up.
Dissolvable materials are becoming more and more common, especially as operators drill longer and longer laterals. The reason for the move to dissolvable plugs on extended-reach lateral wells is due to a lack of effectiveness and capability of milling at the toe. Yes, milling procedures and the capability of coiled tubing milling operations is improving, to meet the challenging operations presented in a modern wellbore design; however, the extra cost paid for dissolvable plugs can be less than the cost of milling operations at the toe stages, especially if there are operational issues.
This has led to the increasing deployment of a hybrid wellbore design. More and more operators are running dissolvable plugs at the toe of the well and then transitioning to more traditional composite plugs for the remainder of the well. Going forward, if the market price for dissolvable plugs continues to decrease, more and more of each lateral will be completed, using dissolvable plugs. Not only will this eliminate mill-out, it also will reduce the time that coiled tubing and/or workover rigs spend in the well; reduce the amount of debris left in the wellbore; save on both fluid and chemical costs; and ultimately lead to faster turnover times, helping the well get on production and generate revenue quicker.
These advancements have been important in helping oil and gas producers save time and money. They could be setting the stage for the next generation of frac plugs, which will drive further improvements in completion efficiency, and equipment reliability and repeatability.
- What's new in exploration: Happy days ahead, maybe (November 2024)
- Shale technology: Using expandable casing patches to reinforce well integrity (November 2024)
- What's new in production: Banking crisis (October 2024)
- To frac, or not to frac, that is the question (September 2024)
- U.S. drilling decreases on shale consolidation, technical advancements following record production (September 2024)
- Frac sand’s incredible journey (July 2024)